Mastering the flow and use of electricity, and applying digital data to the task, is as vital on the racetrack as it is for the electricity grid.
The ideal way to win races in the fully electric ABB FIA Formula E Championship, says Vincent Gaillardot of the Renault e.dams team, is to complete the last lap with “the car crossing the finish line as the last kilowatt-hour of energy is drained from the battery.”
It’s all about managing energy, in other words.
Gaillardot is the project leader of the Renault team, whose cars are driven by Sébastien Buemi and Nico Prost, and he knows from experience that the same basic principle applies to all types of motorsports. Assuring that a Formula E car powered entirely by electricity will operate at peak capability but also make it to the checkered flag is a complex balancing act. So is providing a stable power supply for thousands of consumers from a remote generation source, as ABB does in China and India, one of the many power management challenges ABB technology is able to successfully meet.
“We can’t complete an entire race driving all-out,” Gaillardot says, “so we try to reduce the power demand and focus on being efficient.” A successful strategy, as Renault e.dams has won the team championship in each of Formula E’s previous three seasons.
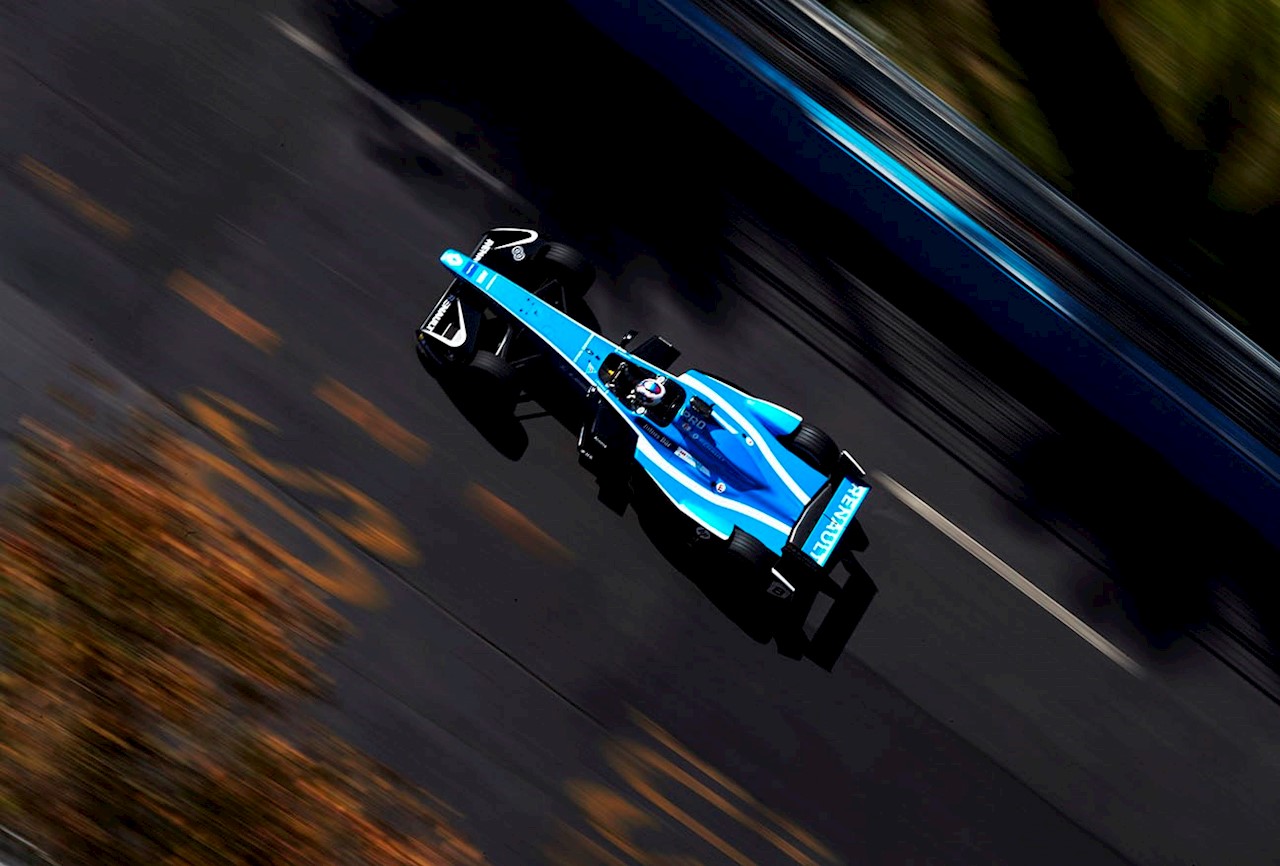
The importance of power management is one of the things that makes ABB’s partnership with Formula E such a natural alliance – and an opportunity that promises to broaden each partner’s expertise and experience. After all, mastering the flow and consumption of electricity, and harnessing digital technology to the task, is at the heart of ABB’s business. And those skills are a crucial part of the art and science of Formula E.
Take, for instance, the flow of vital data during the race. The amount of charge left in the race car’s battery is monitored constantly, and that information is displayed for the driver. The data is used to formulate race strategy in real time. That includes make-or-break decisions like when a pit stop should be scheduled, or determining how aggressive the driver can be in defending his position or passing competitors.
And under Formula E rules, a considerable amount of operating data must be continually provided to racing officials, including brake pressure and motor speed, as well as the battery’s voltage, current and temperature. In essence, a Formula E race is an exercise in monitoring and operating a mobile power grid.
Harnessing the power of ABB Ability
The remote monitoring and control of power management and operating conditions is a key strength of ABB Ability™, the company’s integrated digital platform. ABB Ability coordinates data collection, provides analysis and can remotely control ABB equipment to manage complex systems. For microgrid energy systems in remote locations, for instance, ABB Ability can allow the control room to be far away in a more convenient setting.
Even the delivery of electricity requires a high level of management, an area where ABB excels as well. High Voltage Direct Current (HVDC) links, a technology pioneered by the company more than 60 years ago and continues to develop, deliver the maximum amount of power, with minimal losses, over thousands of kilometers. The ABB Ability™ MACH control system acts as the brain of a HVDC link, providing essential monitoring, control and protection functionality that ensures reliable and efficient power supply – the role of the driver in a Formula E car.
Ensuring reliability of the equipment is also a critical task for racing teams that compete in season-long competitions like the ABB FIA Formula E series. Motors, gearboxes, batteries and electronic systems must be continually assessed to make sure that maintenance is performed or replacements made before a failure occurs.
Reliable equipment is of course vital for other forms of transportation, such as seagoing vessels. ABB Ability™ Collaborative Operation Centers around the world can monitor seagoing vessels, similar to how a Formula E racing car is constantly monitored during a race. When a critical alarm is triggered onboard a vessel, the lights in the ABB Ability Collaborative Operations Center turn red and engineers immediately start to resolve the issue. The monitoring can also reduce downtime by forecasting when electrical equipment will need to be replaced and scheduling the work to minimize the layover time in port.
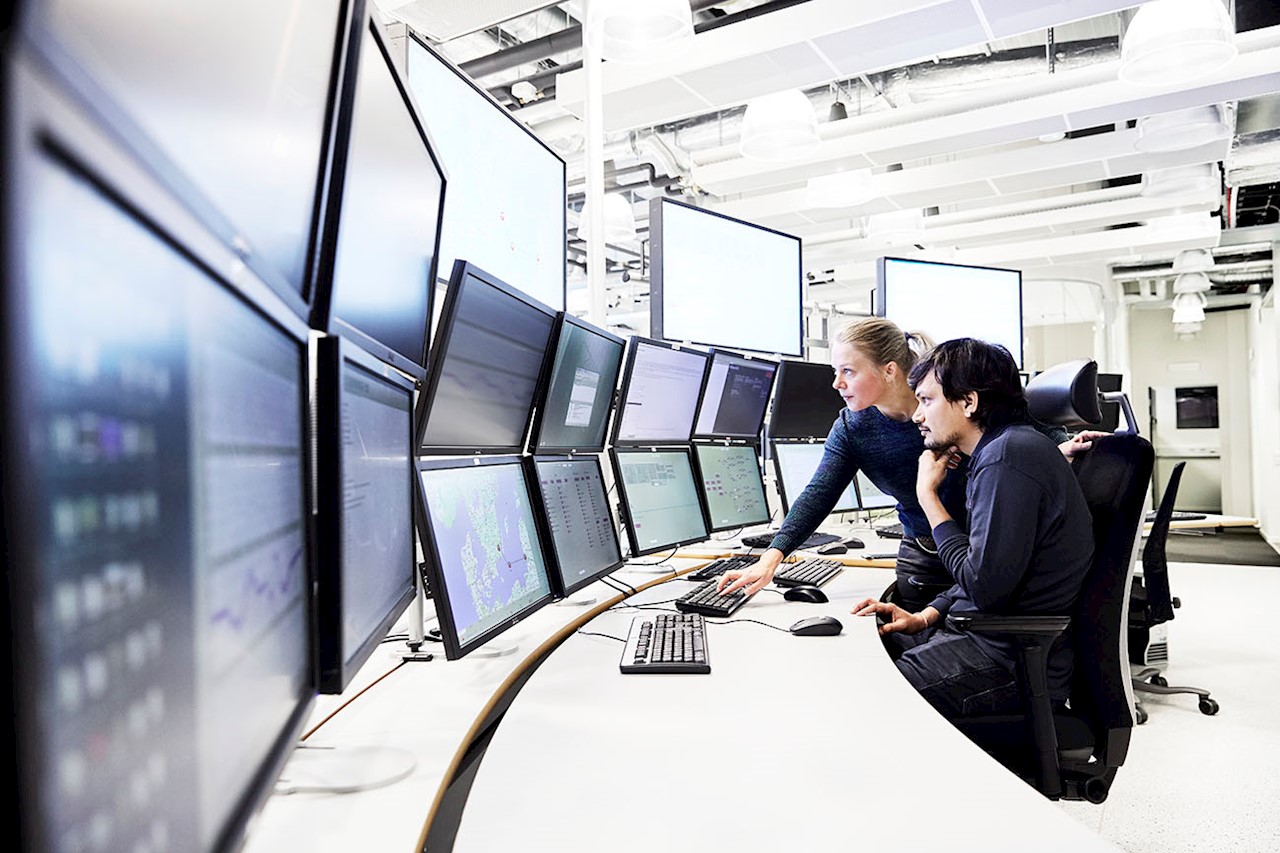
Equipment monitoring is yet another area where the synergies between ABB and Formula E might evolve into benefits for both. Among the features of ABB Ability™ is the Smart Sensor, a wireless device that can provide remote condition monitoring for electric motors by collecting data on vibration, temperature and other parameters. The Smart Sensor can relay information about the motor’s health, via a smartphone and over the internet, to a secure server.
The subtleties of strategy
For knowledgeable racing fans, seeing team strategy play out is one of the great delights of watching a Formula E event. In fact, Formula E race strategy is particularly challenging because many of the variables – like timing the pit stop, rationing battery energy, selecting the level of regenerative braking – are not transferrable from other types of auto racing.
For example, as Renault’s Gaillardot explains, Formula E cars produce more consistent lap times than racers do in Formula 1, where the cars get faster as gasoline is consumed and the cars become lighter.
In one of the unique facets of Formula E rules so far, instead of changing tires during a race, the driver must actually swap out the entire car. That’s a legacy of Formula E’s debut season in 2014, when batteries didn’t have sufficient capacity to last for an entire hour-long race.
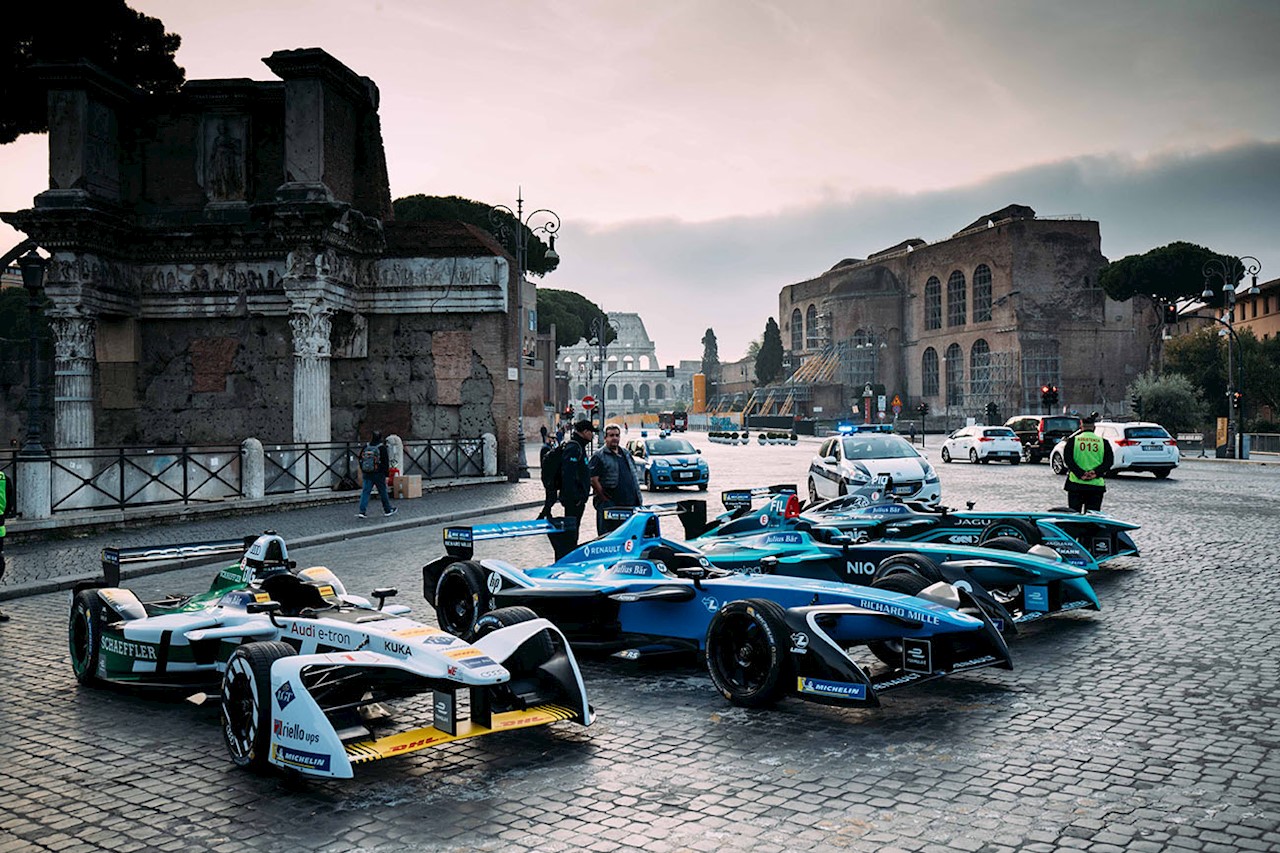
Beginning next season, higher-capacity batteries in a new generation of Formula E cars will be intended to work for the whole race – assuming the racing team can adequately manage the electricity usage. Teams will have to rethink that part of their race strategies.
Crucial decisions are made long before the race
Under the Formula E rules now in place, making the best use of the energy stored in the car’s battery pack is decisive in winning races. That’s why, in the weeks before a race, Formula E teams puzzle through the many competition variables in sophisticated simulator sessions.
In the simulator, the team can determine factors like whether it’s most efficient to maximize the output of the regenerative braking or to rely more on the mechanical brakes. The teams can calculate what the optimum motor speeds will be. And they can figure out whether on-board software or a driver’s manual controls will do the better job of conserving battery charge.
Sessions in the simulator can also help to gauge the optimum time to make the midrace car swap. A driver stuck behind a slower car may benefit from making his pit stop early, if the simulation shows that the time lost in the swap would have him re-entering the track clear of traffic. On the other hand, it may be a better strategy to delay the stop by a lap – assuming enough battery energy was conserved earlier – and rejoin with an extra lap’s worth of battery reserve and therefore the ability to be bolder about passing.
“To run at the front of the ABB FIA Formula E Championship races requires a driver to have the right amount of power exactly when he needs it,” says Rami-Johan Jokela, ABB’s Head of Digitalization.
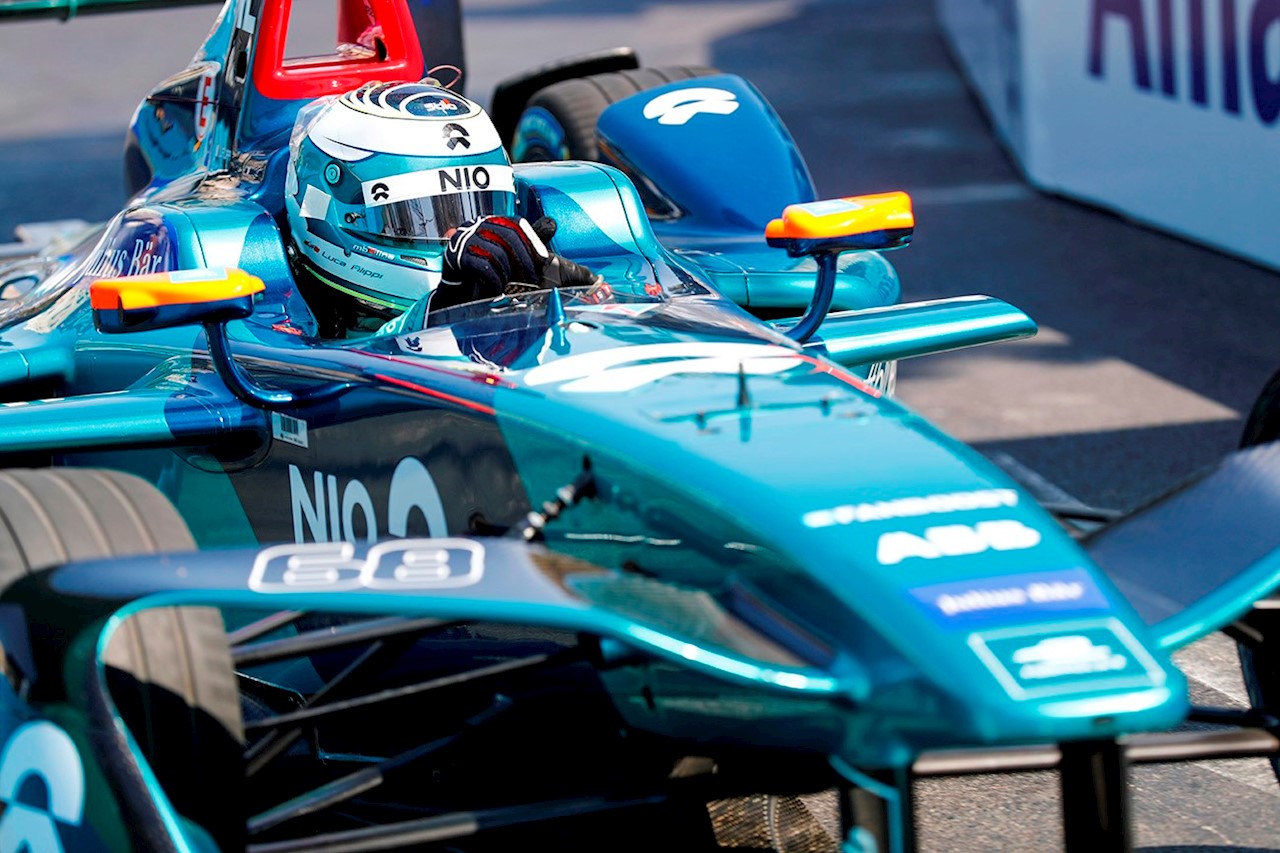
“That management challenge is exactly what ABB confronts day-in and day-out, whether it’s stabilizing an electricity grid, managing assembly plant robots, delivering electricity over long distances or coordinating seaport operations,’’ Jokela says. “That’s why the sport of Formula E, with its forward-looking goals of sustainability and relevance to our transportation future, is a perfect fit for ABB’s core competencies.”
That will matter at the season’s next race, the Rome E-Prix on April 14 – the way it matters at every Formula E contest.