Der Bericht „Flexing for the Future, a 2035 Global Powertrain Forecast Report” – in Auftrag gegeben von ABB und erarbeitet von den Automotive-Intelligence-Experten bei Ultima Media – stellt heraus: Automobilhersteller müssen einen flexibleren und kollaborativen Ansatz für ihre Fertigungs- und Logistikinfrastruktur wählen, wenn sie ihre Profitabilität und Qualität auch im kommenden Jahrzehnt aufrechterhalten wollen.
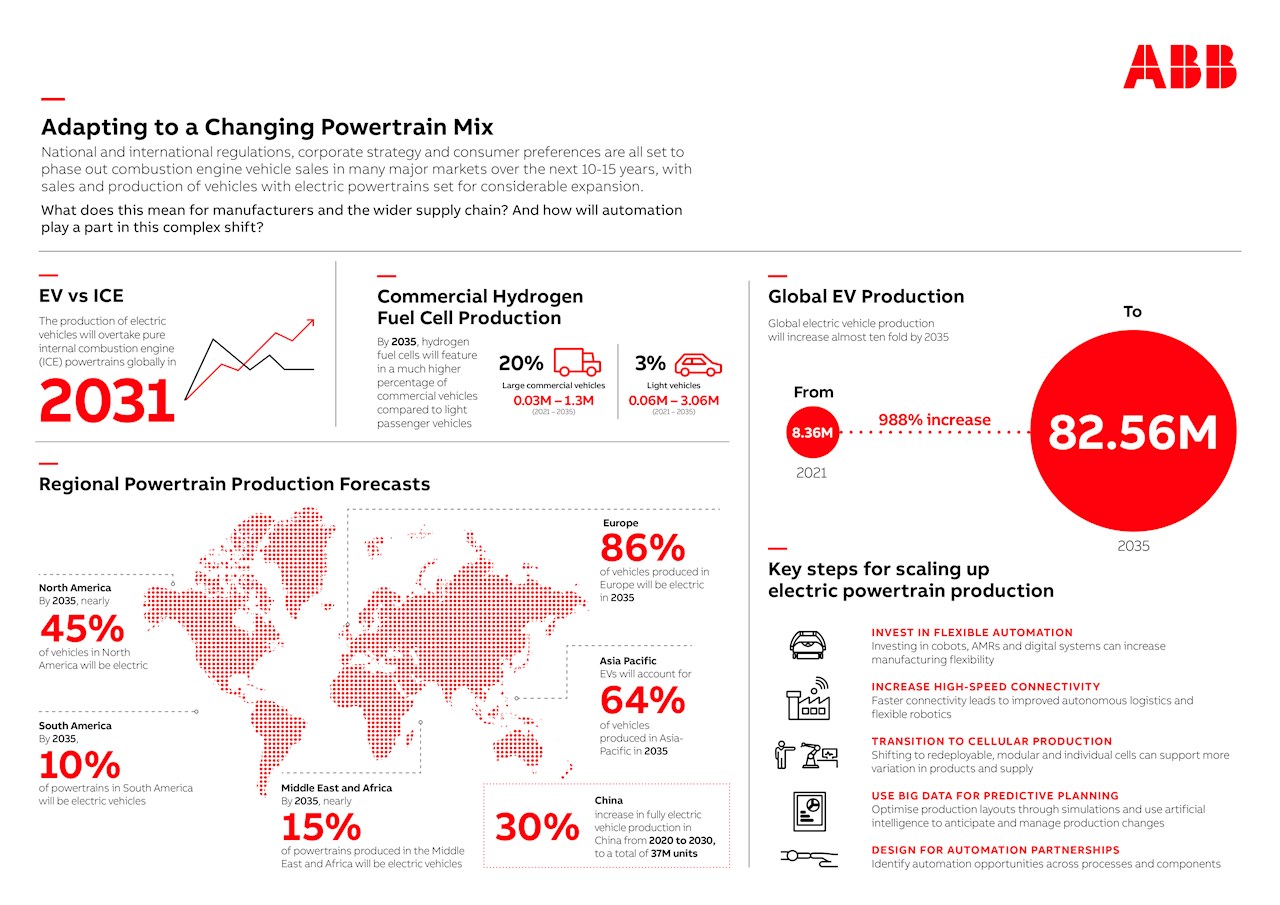
Auf die ehrgeizigen Ziele zur Eindämmung des Klimawandels, die vielen regionalen Unterschiede bei den Regularien und ein verändertes Kaufverhalten reagieren derzeit viele Hersteller: Sie entwickeln Plattformen und Produktionsanlagen, die einen komplexen Antriebsstrangmix – von Benzin und Diesel bis hin zu Hybrid- und Elektroantrieben – sowie neue Technologien wie Wasserstoff-Brennstoffzellen unterstützen.
Diese große Bandbreite bringt eine steigende Komplexität mit sich, die nicht nur die Prozesse innerhalb der Produktionswerke betrifft, sondern sich durch die gesamte globale Logistik und Lieferketten zieht. Da der Antriebsstrang herkömmlicher Verbrenner wenig mit dem von Elektrofahrzeugen gemein hat, kann die schiere Vielfalt der Komponenten und Verfahren, die es abzudecken gilt, schnell unüberschaubar werden. Hinzu kommt: Marktgegebenheiten, staatliche Anreize, Gesetzgebungen und sogar die zugrundeliegende Technologie können sich rasant ändern. Hersteller müssen daher versuchen, ihre Fertigungsanlagen noch flexibler zu gestalten, wenn sie diese Unwägbarkeiten auffangen wollen.
Dabei geht aus dem heute veröffentlichten Bericht hervor, dass Digitalisierung und Automatisierung die großen Zugpferde darstellen, um diesen hohen Grad an Flexibilität zu erreichen.
„Durch die Umgestaltung der traditionellen Produktionsarchitektur mit ihren langen Fertigungsstraßen hin zu modularen Zellen erhalten Hersteller die Möglichkeit, diese einzelnen Zellen zu modifizieren oder gar zu ersetzen, ohne dass es zu kostspieligen Produktionsausfällen kommt“, betont Jörg Reger, Managing Director Automotive bei ABB Robotics. „Solch reibungslose Anpassungen erlauben es den OEMs, zunächst im kleinen Umfang zu starten und entscheidende Bereiche des Fertigungsprozesses durch Hinzufügen oder Umstellen von Zellen zu erweitern, sobald sich die Anforderungen ändern. Mit diesem hohen Grad an Prozessflexibilität bieten wir die Möglichkeit, die steigende Komplexität nicht nur zu bewältigen, sondern sie in eine Chance zu verwandeln.“
Eine weitere Schlüsselmaßnahme hin zu flexibleren Prozessen ist die Umstellung auf eine autonomere Logistik und Materialhandhabung in den Werken, so der Bericht. OEMs setzen hier zunehmend auf autonome mobile Roboter (AMR), um Materialien flexibel zu transportieren.
Hinzu kommt: Mithilfe eines digitalen Zwillings („Digital Twin“) der Anlage lassen sich Änderungen vorab testen und optimieren. Ist das Design der Zelle im virtuellen Raum perfektioniert, kann sie schnell als vollständig validierte Einheit überall auf der Welt implementiert werden. Die zellenbasierte Fertigung ermöglicht es zudem, Roboter mittels eines sogenannten „Lift-and-Shift“-Verfahrens in Bereiche mit hoher Nachfrage zu verlagern. Auf diese Weise lässt sich die Lebensdauer einer Anlage über ihren ursprünglichen Zweck hinaus verlängern.
Entscheidend für den Erfolg solcher Maßnahmen ist jedoch eine engere Zusammenarbeit zwischen dem Hersteller und seinem Automatisierungspartner. Der Bericht verweist auf die Tatsache, dass das Fachwissen vieler Automobilhersteller und -zulieferer in der Regel auf bestimmte Produkttechnologien und Fertigungsprozesse konzentriert ist. Der beste Weg, um schnell Lösungen zu entwickeln, ist daher die Zusammenarbeit mit einem geeigneten externen Partner. Kombinieren Zulieferer ihr Prozess-Know-how mit der Automatisierungsexpertise eines externen Unternehmens, können gemeinsam Automatisierungslösungen entwickelt werden, deren Produkte nicht nur für den reinen Fertigungsprozess, sondern eben auch für die Automatisierung konzipiert sind.
Das kann dazu führen, dass die Automatisierung in weitere Bereiche des Produktionsprozesses vordringt. Dazu zählen der zunehmende Einsatz von Robotern in der Endmontage sowie innovative Technologien wie PixelPaint von ABB, die arbeitsintensive Prozesse, welche die Produktion verlangsamen, überflüssig machen.
Wie der Bericht jedoch ebenso herausstellt, geht es bei der flexiblen Automatisierung nicht nur um die Anschaffung von Robotern, sondern um eine völlig neue Sichtweise darauf, wie sich die Produktionsleistung in einem unsicheren und sich schnell verändernden Umfeld maximieren lässt.
Der Bericht steht hier als Download zur Verfügung.