By Mario Macri, Head of ABB Australia's Smart Power and Smart Buildings Divisions.
The robots have arrived: automation is a reality and an enormous opportunity for manufacturing. Mario Macri, Country Digital Lead, Australia, for ABB, argues that many manufacturers in the food and beverage industry are yet to embrace the full potential of this powerful technology.
Behind automation is AI – Artificial Intelligence. The starting point for bringing AI into manufacturing is data. Data is king – you can’t have AI without data, and you need to digitalise your assets to get that data.
Simply put, AI for manufacturing is a combination of sensors monitoring every aspect of a process, collecting enormous amounts of data (the more the better), and crunching it with human-programmed algorithms. These algorithms can detect everything from a motor drawing too much power to a variation in the colour of a batch of cereal on the production line.
AI is already making manufacturing safer, smarter and more efficient – and the future of this technology holds exponential potential.
At ABB we talk about it in terms of ‘know more, do more, do better, together’. You’re getting data, you’re making decisions based on that data, you’re optimising using AI and you’re on the journey towards autonomy, when it all comes together seamlessly.
Manufacturers need to embrace the Internet of Things (IoT) to start on this journey. That means low-cost sensors and processors embedded in every part of your line, all connected and pumping data into the cloud. Humans simply cannot take in all that data, which is where the algorithms of AI come into play — it turns data into intelligent insights, and insights into action.
The gains from AI technology are especially exciting for food and beverage (F&B) manufacturing, as they will move us ever closer to an autonomous production line, vastly improving efficiencies and sustainability, and removing humans from repetitive production lines, where they can sometimes even be in potentially high-risk situations. Food safety is also bolstered by the consistency of automation, mitigating risks of food recalls which cost food and beverage manufacturers many millions of dollars per year in lost revenue.
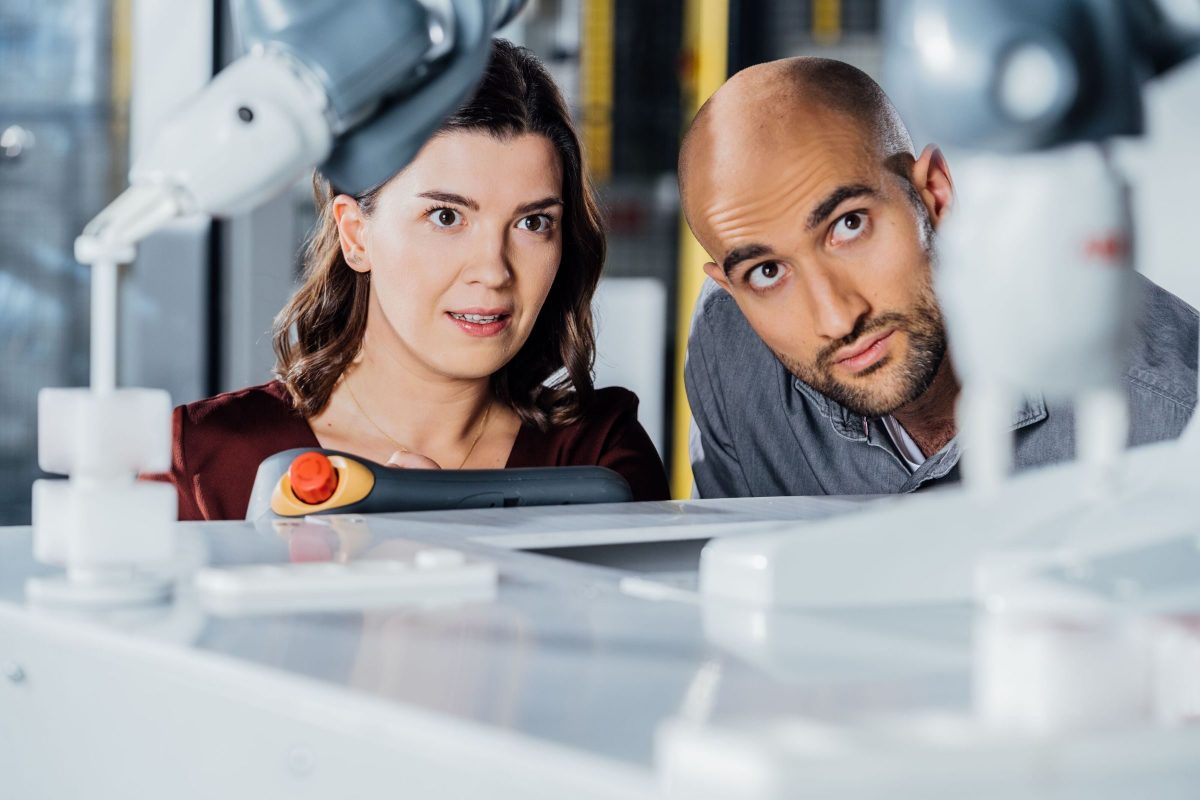
We have barely scratched the surface of what the partnership between human and machine intelligence can offer F&B manufacturing, but it’s critical to work out how to deploy it well.
I tell customers: ‘Start at your most critical process and your biggest pain point – and keep it simple!’ The digitalisation journey is not a linear project, it’s a change journey of an organisation and the culture of a company and you will try things that may not necessarily deliver immediate results, although that’s how you will learn.
Have a vision and commit that all upgrades will support your digitalisation/IoT journey. Use those rare CAPEX or OPEX opportunities to replace a component with a digitally enabled one. Once you are collecting data, you can start to ask questions of it. How can I apply condition monitoring or energy-efficiency algorithms or other artificial machine learning algorithms to help me improve this process? Start small in critical areas, and stay focused.
Energy efficiency and maintenance are a great starting spot. I like to use a conveyor belt as an example – hundreds of motors in a food conveyor-belt system moving goods around. Do all those motors have variable speed drives or sensors that talk to each other, why is that one drawing more power than the other?
What can the power distribution system with meters, circuit-breakers, power-conditioning and the like supplying my critical assets tell me about how and where I use power, or whether I am running the equipment in a way that affects its longevity? You collect all these little insights from one conveyor belt or sub-system and apply that on a grander scale and all of a sudden, you see where you can gain energy efficiencies.
AI and learning algorithms revolutionises maintenance. Rather than time-based preventive or run-to-failure maintenance, sensors collect data which algorithms interpret to produce predictive analytics. AI gives us the capability to operate with condition-based or predictive maintenance, which improves uptime and savings two ways: avoiding unexpected shutdowns and planned shutdowns for maintenance that isn’t needed yet.
Another key area for AI in F&B manufacturing is improving production – I get a better product outcome, I can tweak things on the run. We’ve had monitoring and then acting on simple things such as vat temperature or key batching parameters for a long time – that’s pretty primitive compared to what AI can do. It’s so much more nuanced: Quality checks on batch or process equipment using AI enabled real-time monitoring means anomalies are identified as soon as they occur, and changes made immediately rather than at the end of a cycle, vastly reducing waste, and saving money.
There are multiple ways for F&B manufacturers to use AI and harness the huge datasets collected from their automated systems, analysing historical data and ingredient parameters. With the support of the right control system, the possibilities become endless: Brands can create best-quality flavour profiles and even refine individual steps in the production process such as fermentation or pasteurisation.
As to physical robots, AI-driven robotics are advancing intelligent automation, and the latest trend is training them alongside humans. ABB has partnered with Covariant, a Silicon Valley startup, to trial picking robots that work side-by-side with human counterparts. Covariant’s software combines 3D cameras and reinforcement learning, so robots can learn new tasks independently.
You can immediately see the potential here for packaging lines, where we know robots can work faster, with more precision and no breaks. There have traditionally been challenges for robots being able to cope with things like shape variance or not being able to ‘see’ transparent items, such as water bottles, which some robots will just ignore. The vision system on the Covariant robots – a combination of sophisticated AI and cameras – allows the robot to combine footage from the camera with past learned experience. This allows for much more sophisticated trial-and-error responses, which ultimately result in incredible accuracy that can work at scale.
Think about the potential to apply AI robotics at, say, a meat-processing plant. I can already see a time where an AI-enabled robot could train alongside an experienced meat worker and learn to make the right movements to process a carcass. Look at what robots have done in other manufacturing industries, such as welding robots in automotive plants.
In a similar way to additive manufacturing, AI supports the entrepreneurial spirit of manufacturers. R&D used to be the domain of people with a lot of money, who could prototype endlessly. These technologies let people try new things and bring products to market faster and more efficiently, learning so much more than we could have ever imagined. They unlock creativity and allow ideas to be tried out in a lower cost, easier way.
The feedback loop is getting shorter and shorter, so AI helps you correct things and get efficiencies of scale faster, so you can do more with the same number of people, and do it better. This technology helps you to make better decisions, faster.
Australian industry needs to embrace these new technologies or we risk becoming laggards in the sectors that are essential to our sovereign security. The conditions are particularly ripe for value-add niche manufacturing – which I see as the sweet spot for us in Australia. It’s really exciting.
This article was originally published in AU Manufacturing.