Swedish cold-rolled steel is in high demand by the global automotive industry, which prompted ABB’s customer, SSAB, to increase the production capacity at its rolling mill in Borlänge, Sweden. The company was faced with a challenge since the upgrade required a new power supply — and time was of the essence. ABB has delivered three eHouses to address these challenges. The flexible electrical houses were ready to supply low voltage to the line the instant they were delivered on site.
Text and photos: Jakob Svärd
In order to meet increased demand, SSAB in Borlänge is currently expanding its continuous annealing line at the rolling mill in Borlänge. The line is expected to be completed in 2020.
The path to a more sustainable transport sector does not begin where one might think. One place it starts is in Malmberget, outside of Kiruna. Deep inside the dark mine there, mining company LKAB mines iron ore, which is subsequently shipped via electric rail to SSAB’s production facility in Luleå to be transformed into steel. The unprocessed steel is then transported, also via electric rail, to the SSAB rolling mill in Borlänge to be processed and transformed into high-quality steel products. Docol is one such product. It is the result of Swedish steel innovation and has become popular among vehicle manufacturers constantly on the lookout for ways to produce lighter, stronger and more eco-friendly vehicles.
Work on expanding the production line started at the beginning of 2017, and SSAB was already in need of a new power supply by the following summer for the various phases to stay on schedule. Therefore, SSAB purchased three eHouses equipped with fire alarms and ventilation, a Resibloc dry-type transformer and MNS 3.0 low-voltage switchgear from ABB, as well as UniGear medium-voltage switchgear placed in a separate switchgear room.
By selecting and investing in an eHouse solution — a flexible walk-in enclosure that is designed to be installed in very limited spaces — the company was able to save both time and money compared to designing a completely new switchgear room. It provided reduced site resources, reduced installation and commissioning time on site, and a predictable delivery. “With the eHouse solution, we have an optimal solution in terms of future infrastructure in the production line,” says Jennica Simesgården, electrical power project manager at SSAB.
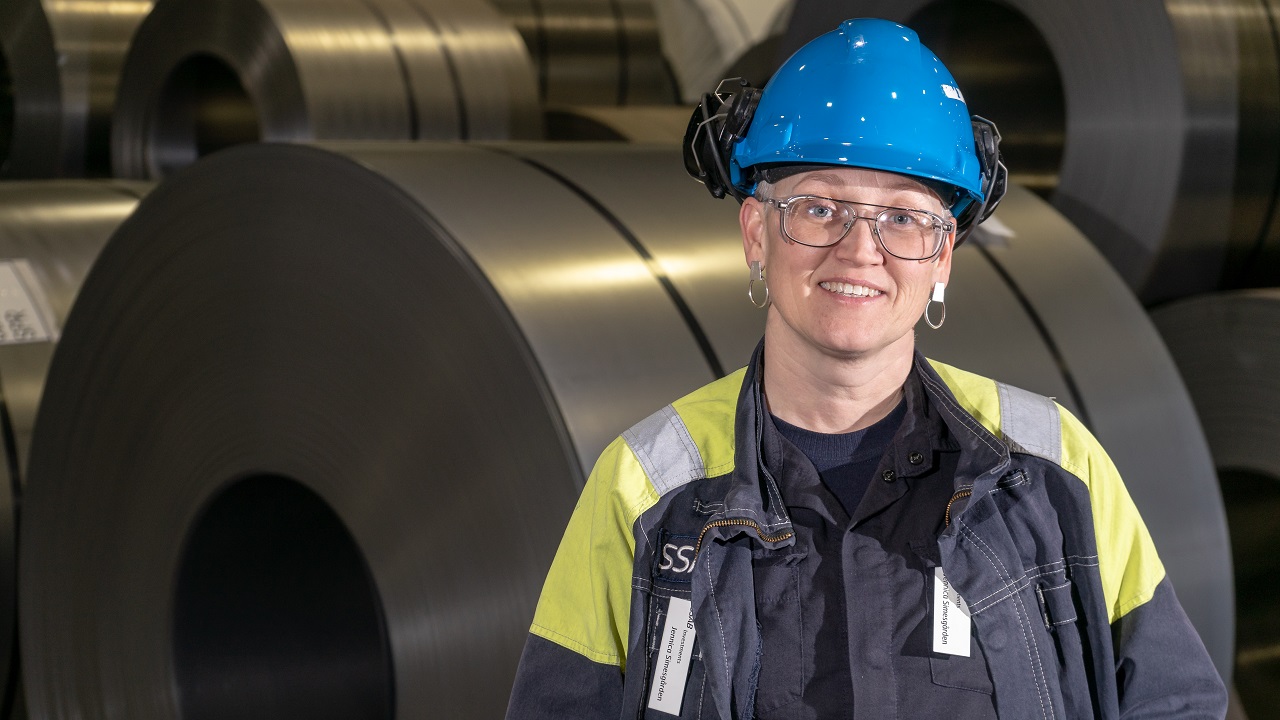
In this type of vulnerable position, it is important to be able to rely on your partner to deliver a quick, flexible and well-functioning solution, which SSAB was able to do in this case. “Our cooperation has gone really well, so I have been able to rest assured,” she says.
At SSAB, the eHouse solution was mounted on beams high above the production floor. Products were delivered and commissioned in the summer 2018. The gains offered by the flexible power supply are clear to the time-honored steel manufacturer.
Jennica concluded, “The solution reduces our need for resources since we do not need as many for a project. This will be especially important in a future where fewer people need to do even more in the industry.”
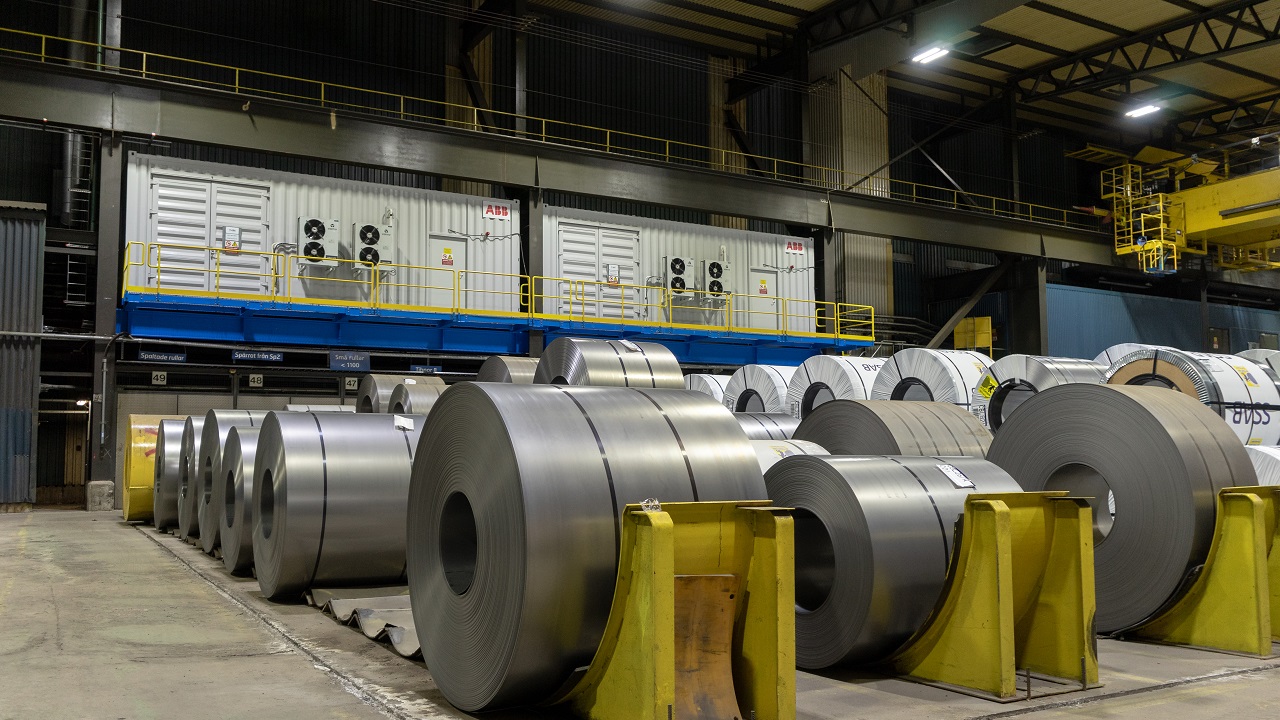