Powerful tools such as computer-aided-engineering (CAE) and computational fluid dynamics (CFD) make it possible to rapidly perform virtual prototyping. However, the complexity of these tools limits their use to skilled users. A key driver of innovation is to democratize technology; with this in mind, ABB has introduced three semi-automated platforms designed to make numerical modeling quick, easy and reliable. The new tools reduce prototyping costs and enable dozens of design variation tests in a reasonable time frame.
Boguslaw Samul, Andrzej Kobierski, Janusz Duc ABB Corporate Research Kraków, Poland, boguslaw.samul@pl.abb.com, andrzej.kobierski@pl.abb.com, janusz.duc@pl.abb.com; Jaydeep Deshpande ABB Power Grids, Dry Transformers Raleigh, NC, United States, jaydeep.deshpande@us.abb.com; Jan Westerlund ABB Motors and Generators Technology Helsinki, Finland, jan.westerlund@fi.abb.com; Dietrich Bonmann ABB Power Grids, Power Transformers Bad Honnef, Germany, dietrich.bonmann@de.abb.com
One of the key questions concerning electrical devices that are under development is the extent to which they will reduce costs both in terms of production and operation. On the one hand, there is a drive to reduce devices’ weight, size and complexity; on the other, the devices must be robust, affordable and efficient. How can design engineers zero in on the best possible balance of factors for a given application in the least possible development time?
The answer to this question is complex because, for instance, reducing the size of an electrical device is limited by factors such as electrical distances (insulation properties) and its thermal management. But testing devices to ascertain their electrical and thermal properties is usually expensive and time consuming.
Nevertheless, there are powerful tools that can help device designers visualize, quantify and accurately predict a growing number of a device’s characteristics during the development stage. For instance, computer-aided-engineering (CAE) tools, such as the finite element method (FEM) and computational fluid dynamics (CFD), can significantly reduce costs and testing times, as they enable creation of a virtual prototype of a device and analysis of dozens of its arrangements in a relatively short time →1. State-of-the-art simulation software, together with the growing computational capabilities of high-performance computers (HPC), enables virtual testing of complete devices with a level of accuracy that is within only a few percentage points of actual tests.
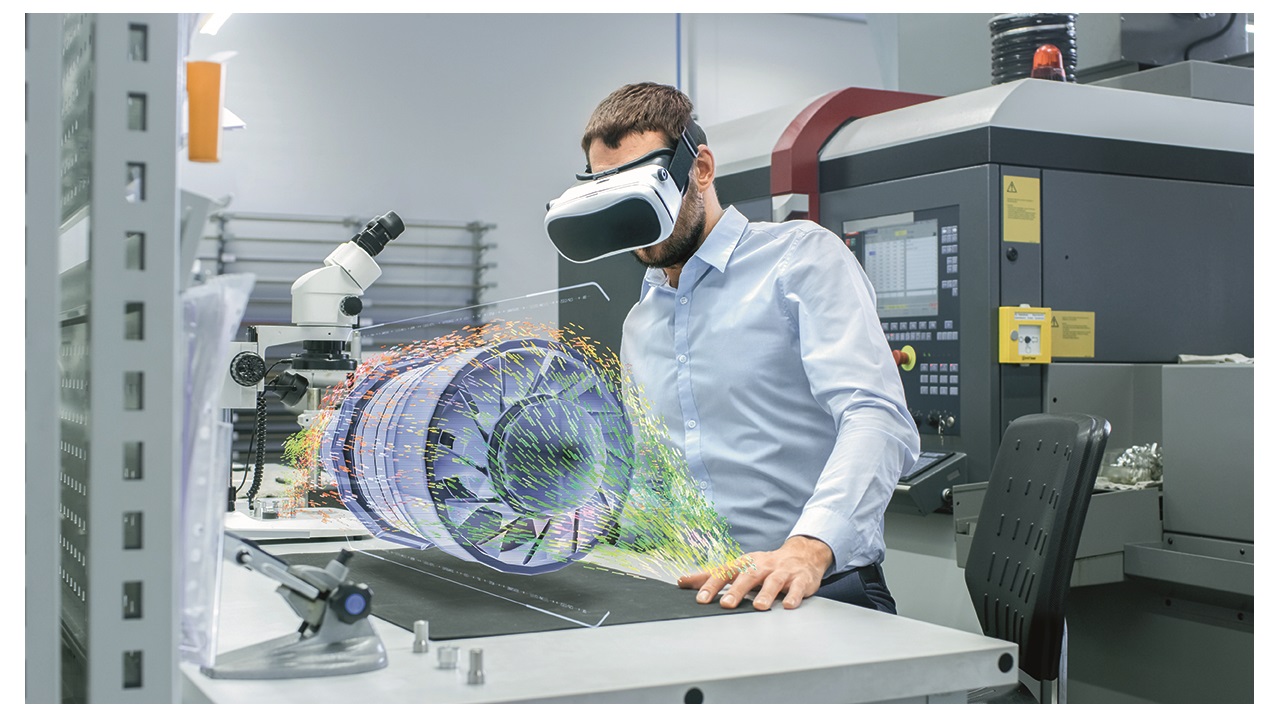
Three hurdles
This is not to say, however, that an era of flawless virtual product testing has arrived. Design engineers still face three significant hurdles: the cost of software, the cost of high-performance computers and an often insufficient familiarity with proper simulation model preparation and solver setups. But here again, solutions are at hand: Expensive commercial software can sometimes be replaced with open-source code, local HPC’s can be replaced by cloud solutions, and model preparation and solver setups can in some cases be performed by dedicated software with built-in templates and settings that do not require changes by the user. In this evolving landscape engineers can now get a user-friendly interface with a clear set of options and receive results in the form of a report. This approach, which is sometimes referred to as “simulation democratization,” makes it possible for just about any engineer to use such an interface, rather than just a handful of numerical calculation specialists.
How is ABB driving the trend toward affordable simulation tools that provide increasing value for its customers? Here’s a look at three semi-automated tools developed at ABB for use in product development.
StudyTrafo
Verification of design and optimization of magnetic shielding are very important aspects of transformer production because of the need to reduce the stray losses generated in metallic parts exposed to magnetic fields. The preparation of associated numerical models requires deep knowledge of simulation software, skills in 3D modelling and experience in evaluating the results – skills that are generally relevant only to daily users of simulation packages, but not always to electrical designers. In view of this, ABB has developed StudyTrafo, a semi-automated tool dedicated to the prediction of hot spots for simulation experts as well as for occasional users. StudyTrafo’s interface makes the generation of simulation models easy to follow and very fast.
The concept of the interface is to generate simulation models based on the input data of the mechanical dimensions of transformer components – in other words, core and yoke clamps, windings, tank and shielding →2. Simulation models are generated in commercial software dedicated to electromagnetic and thermal calculations using built-in 3D primitives as blocks, cylinders, etc. and geometric operations.
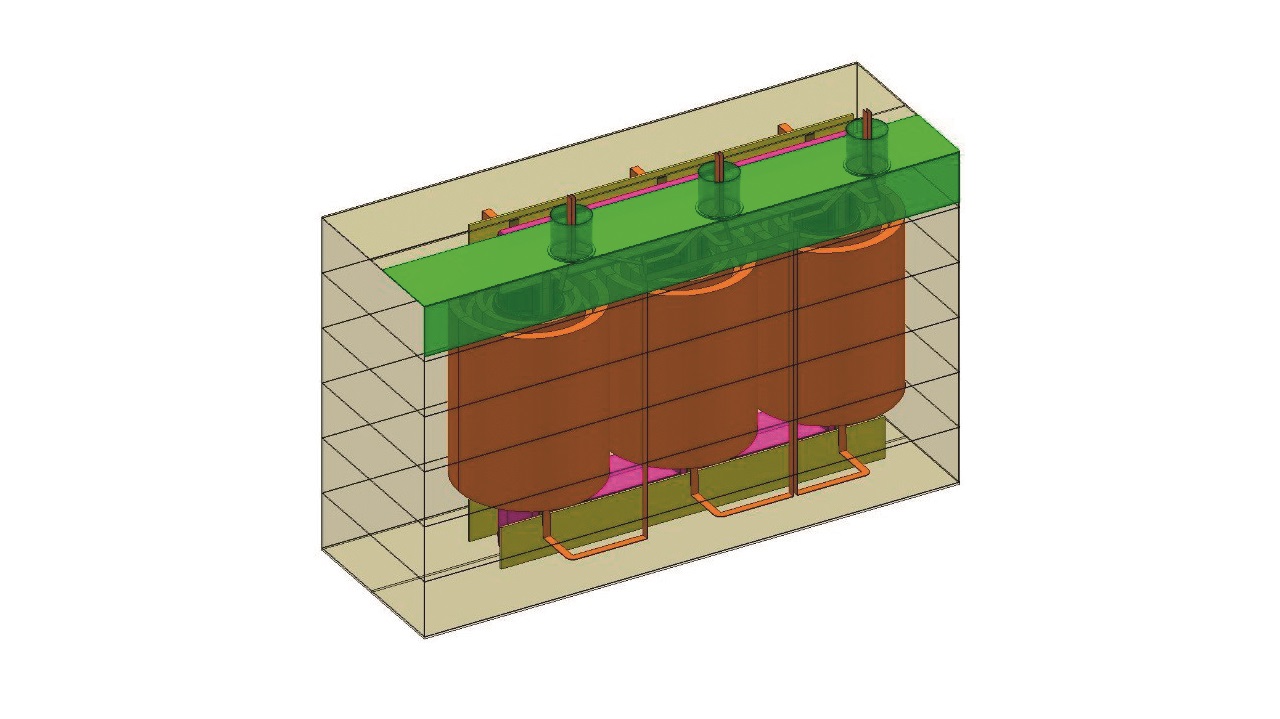
Additionally, boundary conditions and simulation settings are automatically assigned to generated models. All the parameters are statistically fitted based on dozens of tested units and small, medium and large power transformers produced around the world by ABB. A material library dedicated to such calculations was developed by ABB scientists using laboratory measurements.
StudyTrafo is written in C# and input data can be entered manually by users or imported directly from a design system →4. The latter option allows instantaneous creation of simulation models. As a result, simulation time is relatively short, allowing engineers to provide a complete optimization of a transformer design within one day. Final results are presented in the form of a table showing the distribution of losses and maximum temperature values.
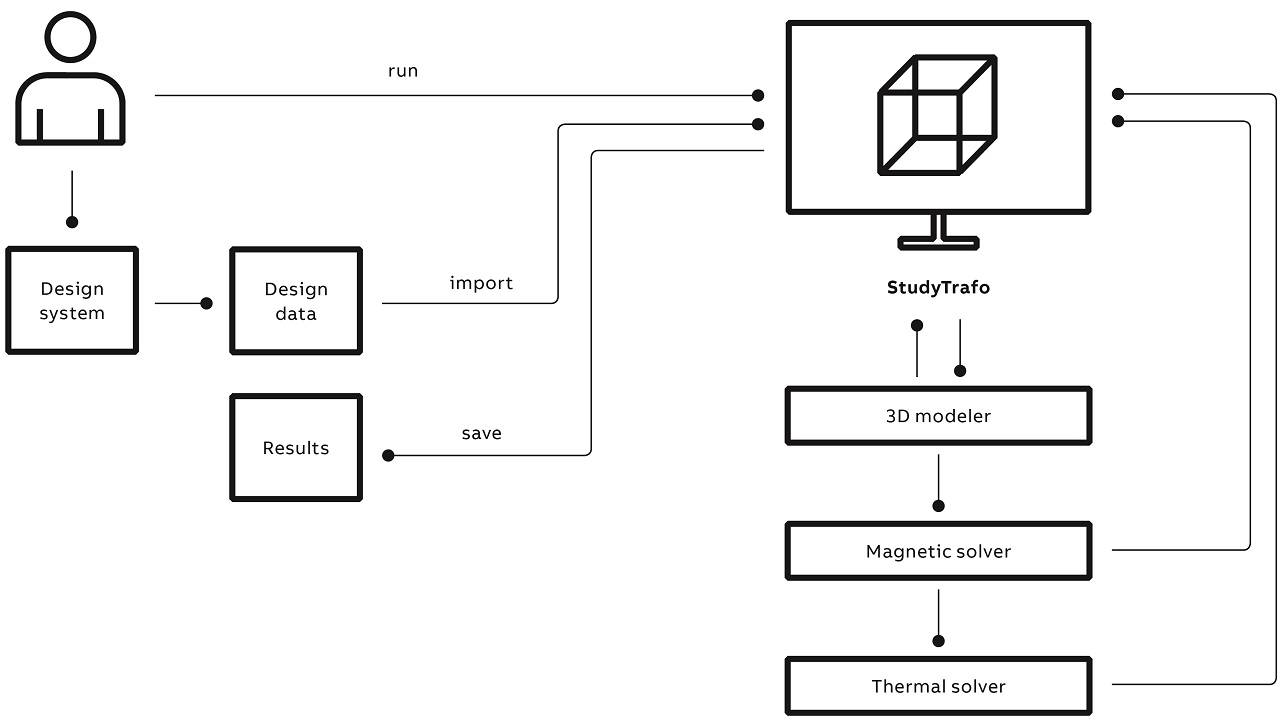
The methodology is practical and inexpensive. Compared to other tools and analytical methods available for stray loss calculations, the standard deviation between measured and calculated structural losses has been decreased by a factor of two. Furthermore, the benefit of applying computer simulations is not limited to cost and time savings for a single transformer unit, but also results in a better understanding of the physical processes occurring during operation. Such an approach offers multiple benefits in terms of the opportunity to run simulation tests of different solutions. This results in improved designs with lower stray losses and greater efficiency.
CFD for MCCU
MCCU-CFD is a semi-automated tool dedicated to experimental CFD (computational fluid dynamic) simulations of electric motors →5. It was developed as a part of the MCCU (Multiphysics Cascaded Controlling Unit). The main idea behind the software is to control and automate several different physical phenomena commonly used by R&D engineers to study the operation of motors. This solution allows R&D design engineers to study how the alteration of the given dimensions or operational parameters of a motor influence the motor’s approximated performance.
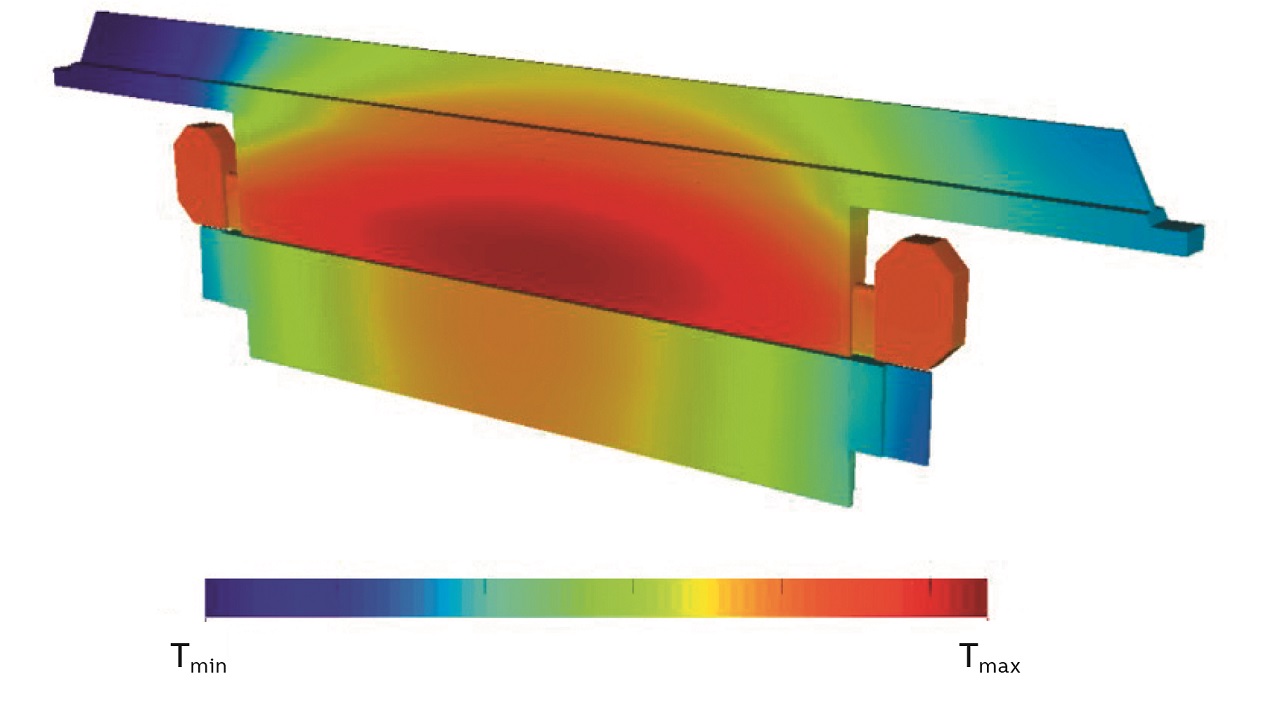
MCCU gathers multiple tools within a single interface, which can be accessed and used from a web page. The idea behind the tool is to allow R&D engineers to automate the process of preparing complete CFD simulations based on a predefined set of parameters.
The MCCU-CFD tool allows users to perform a CFD simulation of a motor with one click. The input for simulation is provided by ADEPT software – a comprehensive design environment for electric motors, and includes overall dimensions and motor operational parameters.
The tool generates a representative 3D model of a motor suitable for running an airflow or coupled thermal and airflow solution using open source utilities such as OpenFOAM →3. Once the scripts are finished with finite volume mesh generation of active parts and air domain they assure proper material property, heat source and boundary condition assignment for all motor components.
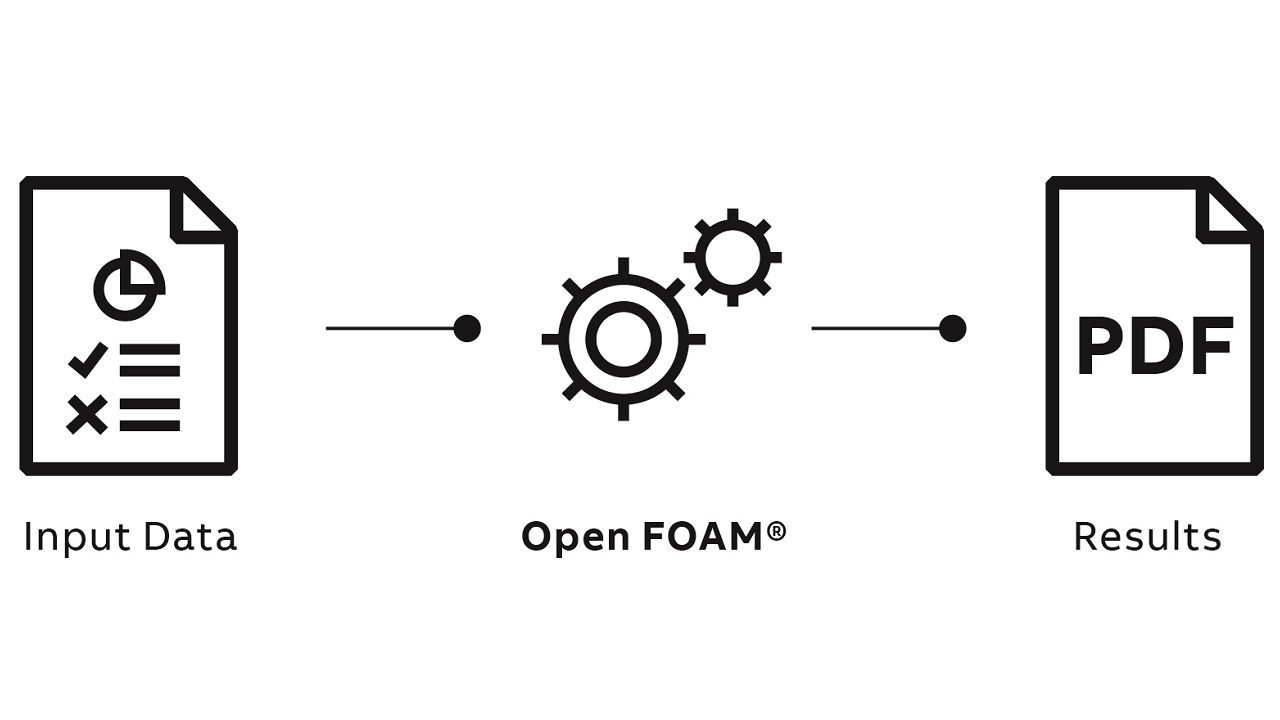
Once a model is complete, simulation is calculated on a server until it reaches a stable state. At the end of the simulation process, automated post-processing is carried out using software such as ParaView. MCCU-CFD collects simulation results in the form of pictures, plots, and tables and prepares a report that is then sent to the user.
DryFOAM
Dry-type transformer designs are highly sensitive to temperature changes. Their thermal performance is characteristically worse than that of liquid-filled transformers due to their cooling medium (air) and to the fact that they use natural convection for heat transfer. In order to achieve optimized design for dry-type transformers, it is therefore imperative to have reliable thermal calculation tools at the designer’s disposal.
These tools can range from simplified lumped mass systems to very intricate network models. Going beyond the limitations of averaged parameter models, computational fluid dynamics allows users to capture the effects of turbulence, radiation and buoyancy, as well as the effects of geometric features on dry-type transformers.
With the advent of cloud computing, the cost of computation is now lower than ever. Hence, for a numerical analysis system such as CFD, cost of computation is no longer a bottleneck. Historically, the cost of commercial licensing has been a prohibitive factor in terms of widespread adoption of available platforms. In this new landscape, Open FOAM rivals commercial software suits as an alternate open-source software suite. Use of OpenFOAM makes it possible to scale simulations broadly across computational cores and truly leverage high performance computing at an ultra-low cost →6. For a repeatable task such as the design of a transformer, an automated platform based on OpenFOAM provides a good solution for accurate thermal calculation.
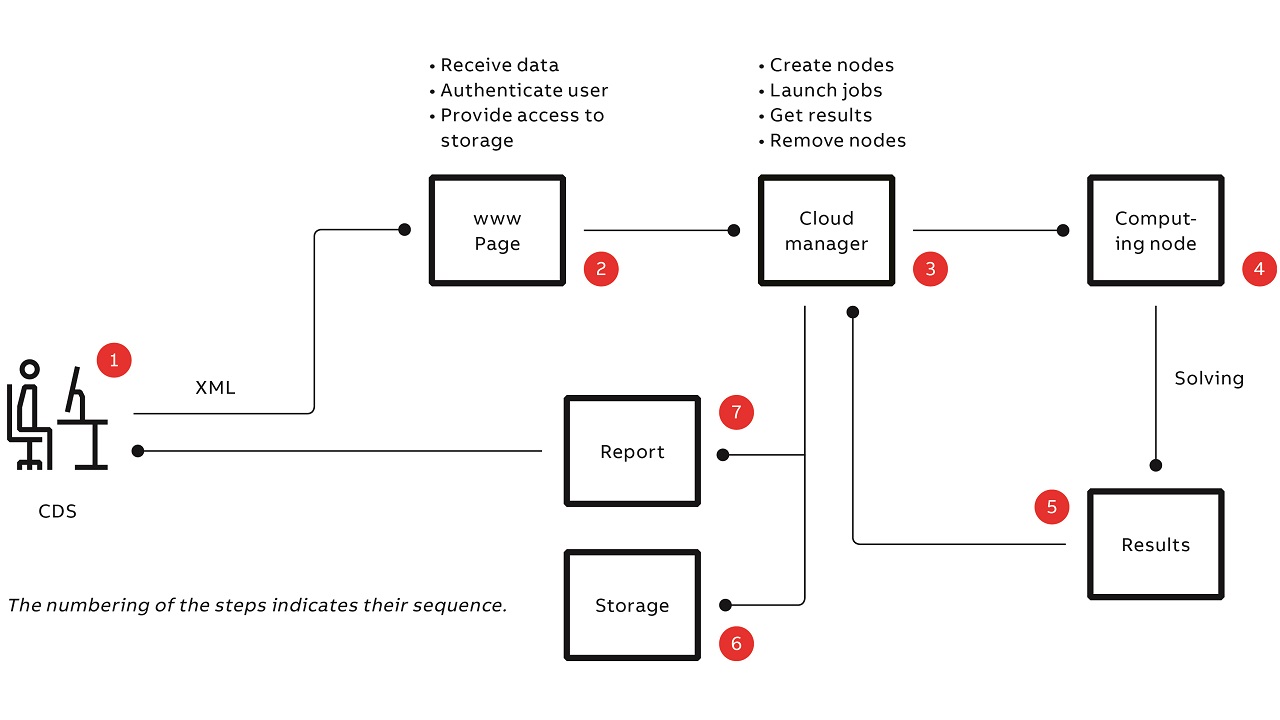
DryFOAM (Dry for dry transformer and FOAM for OpenFOAM) dates back to a 2016 workshop titled “Thermal Issues in Electrical Machines.” Experiences exchanged in the areas of open source computing, thermal management, simulation software development and novel cloud computing methods at the time resulted in a 2017 IT project.
The overarching idea of the project was to
a) provide a simple and reliable tool for fluid flow – thermal simulations of dry transformers,
b) use open source technologies to keep operational expenses at a minimum,
c) use cloud computing (Microsoft Azure) to reduce computational overheads and d) make it easy enough for use by every engineer in dry transformer factories regardless of their theoretical background in thermal-fluids.
DryFOAM starts with a single design input file, which is also used universally by ABB’s Common Design System (CDS) for transformer design. It automatically extracts geometrical parameters, such as winding, core and enclosure dimensions, loads (losses) and boundary conditions (environmental temperature). Octave (another open source system, analogous to Matlab commercial software) scripts then takes over to build a 2D axisymmetric representative model of a transformer including core, windings, cooling ducts, enclosure, ventilation openings and air domain around the device. Finite volume meshes are generated according to CFD method needs, ensuring quality of elements and boundary layer details for resolving near wall flow for natural and forced convection. Finally, DryFOAM’s workflow assigns heat sources, material properties, boundary conditions and solver settings. When the model is ready DryFOAM starts calculations and generates a report after the solver reaches a stable solution. One of DryFOAM’s key features is automated report generation. This facilitates communication of results in the most readable format for designers. Simulation complexity is abstracted in the process and designers are shown key information regarding core-coil thermal performance. Designers know not only the average winding temperatures, but also hot spot temperatures and locations. A report can then be downloaded or stored in the system.
From a deployment perspective, DryFOAM is fully containerized. It can therefore be used on a laptop, workstation or in the cloud. Cloud solutions appear to be particularly promising because a predefined DryFOAM Cloud User Interface ensures data security and enables fast and easy file input and uploads as well as report downloads and online/live presentation of solution stability parameters versus iteration.
At its current stage, DryFOAM software enables 2D calculations of two construction types, but plans call for more detailed 3D calculations that enable other types of transformers such as Resibloc and traction transformers. Even more importantly, the tool’s skeleton can be easily adapted to the simulation of other ABB products.