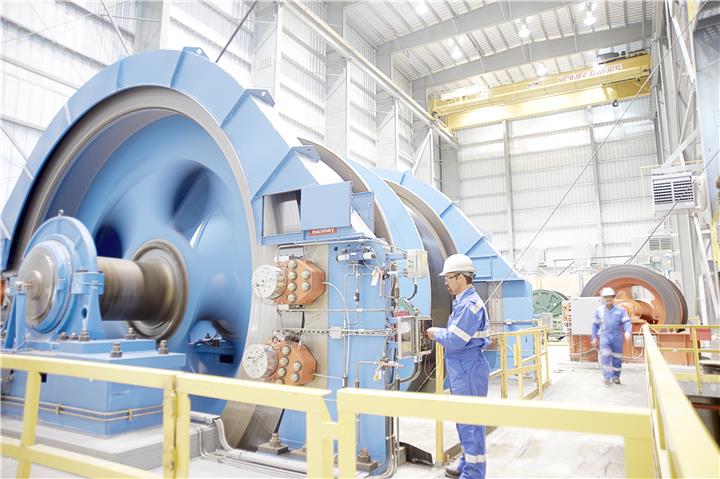
The company is applying the might of its innovative global development team to achieve Safety Integrity Level (SIL) ratings for the three key functional safety systems that protect its widely-used mine hoists.
Following the growing requirements by regulators around the world for SIL ratings in mining equipment, ABB decided to go one step further.
"We're the first in the world to develop a complete SIL 3 compliant mine hoist safety system, I believe," ABB Australia process automation head of division Stuart Cowie explains.
He said other mine hoist manufacturers had developed applications with safety-rated controllers which had been assessed as compliant with existing local regulations. But ABB's development is going one step further by achieving SIL product certification of the entire safety system prior to installation. ABB's new offering will then only need to be configured for the application, thus making it more attractive to clients as they will know beforehand that the equipment and systems are already certified and verified to be compliant.
"I believe we're the first to take this on," he said.
ABB is developing three functional safety systems for its mine hoists - the Hoist Monitor, Hoist Protector and Hoist Brake System - to SIL3, a high level safety rating.
"Then essentially you'll have a complete hoist safety system - from the detection of a failure to the actuation of the safety brakes - that is SIL certified," Cowie said.
"What it means is that you'll have reliable and redundant fail-safe protection systems, so if anything fails, a back up process will prevent calamity."
ABB is developing all three systems to meet the criteria set by the International Electrotechnical Commission standard IEC 62061.
"It is very topical in the sense that when mines go to upgrade their mine hoists, regulators are saying that in any upgrade you have to consider a safety system," Cowie said.
"ABB is really making a name for being at the forefront of new technology and our team has been integral to design at our centre of excellence for mine hoisting in Sweden."
ABB staff from Australia and Canada are working with the centre in Sweden to "reimagine and redevelop" the mine hoist Brake System, Hoist Monitor and Hoist Protector.
The developments are being assessed for certification by the government-owned SP Technical Research Institute of Sweden.
Australia-based senior applications engineer Alonso Morey is part of the development team for the Hoist Monitor and has spent time in Sweden helping to review the design, documentation and software coding.
"ABB is changing what has been done in the past regarding the way safety of mine hoists is treated," he said. "ABB have re-imagined and redeveloped what we're doing to the standards that are in place."
He said ABB first conducted an extremely comprehensive review of possible risks and hazards to all types of hoists in different environments, including rope miscoiling, overspeed, underwinding, broken drive chains and shaft obstruction.
"ABB then discriminated which potential hazards could be mitigated normally with mechanical hazard control, which could be mitigated with electrical controls and what could be done to achieve a certified SIL rating, according to each potential hazard," Morey said.
He said the Hoist Monitor was already in the testing phase and was closest to achieving SIL3 certification, which is expected to occur before the end of this year.
The extensive testing processes for the software modules alone include review, simulation and testing, black box testing, white box (structure) testing and further analysis and thorough documentation.
The Hoist Monitor provides speed distance protection for a mine hoist to ensure it runs within safe limits set by the control system. If the control system fails, the Hoist Monitor disconnects the control system's command to move the machine (motor torque) and have the brakes applied to stop the hoist safely and predictably. The unit also provides protection for additional pulley related protections, e.g. bad coiling, clutch monitoring (drum hoists), worn friction inserts, rope slip (friction hoists).
The Hoist Monitor is being designed as a compact, relatively inexpensive solution that can be retrofitted to most mine hoists to achieve greater functional safety.
Once the Hoist Monitor is certified, it will feed into the development of the Hoist Protector, a more advanced system with additional controls, tailored for installation during a complete hoist system upgrade. The Hoist Protector will offer a complete solution for mine hoist safety, including all of the Hoist Monitor protections, shaft and underground level protections, e.g. gate monitoring, emergency stop push buttons. It will also provide a complete integration with the Brake System and variable speed drive's "Safe-torque Off" feature.
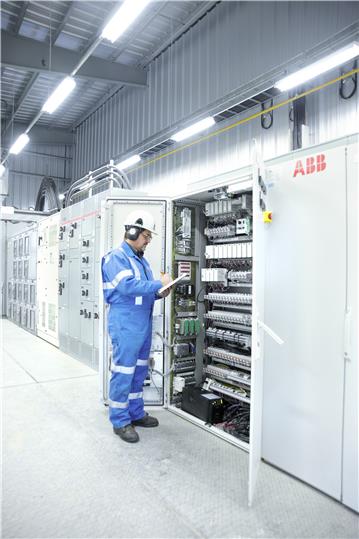
ABB has already created a site-specific Hoist Protector-style design for an Australian mine that pioneers the concept of the new system.
"We have worked with ABB Sweden on a project-specific solution for a mine in New South Wales that takes into account most of the protections the Hoist Protector will deliver " Morey said.
"The engineering and site experience with this project will feed into the development of the Hoist Protector, continuing the close collaboration between ABB Australia and Sweden."
Morey said ABB's third mine hoist system seeking SIL certification, the Brake System, was being developed in two parts.
The mechanical and hydraulic systems had already been designed and tested in Sweden; meanwhile ABB in Canada is developing the controller and electrical elements for the 2-4 channel SIL Brake System.
Certification could occur as early as 2017 and ABB hopes to have the more complex Hoist Protector system SIL rated in 2018.
Morey said different elements of functional safety within the three systems could have different SIL ratings but ABB was aiming for the highest standards it believed possible.
ABB is following the IEC 62061 standard for the development of these systems, which could potentially be merged with the parallel ISO 13849 to create a new international standard IEC ISO 17305.
However Morey said any future change to the international standards would not greatly impact ABB's developments.
New South Wales guidelines already include SIL requirements for mine hoists. Other states use a Risk assessment based procedure to determine the required SIL of each safety function.
* This is a version of an article originally published in Australia's Mining Monthly magazine