Sönke Kock ABB Motion Ladenburg, Germany
Electrically driven powertrains are critical components in industry and it is essential that they can run continuously. With ABB Ability™ Condition Monitoring for powertrains, ABB is now helping customers increase the uptime of their entire powertrain. ABB Review interviewed ABB’s Sönke Kock to find out more.
AR ABB Review (AR): Sönke, first of all, what is your role in ABB?
SK Sönke Kock (SK): I am ABB’s Digital Leader for the Global Business Line Drives. Digital innovation is an important topic in Drives.
AR Let’s start at the beginning, shall we: What are electrical powertrains and why are they important?
SK Throughout industry, infrastructure and buildings there is a need to drive conveyor belts, operate pumps, turn mixers, move or process material, rotate fans, or any one of a thousand other tasks. These tasks are accomplished by electrical powertrains – that is, the connection of a number of drives, motors, bearings and couplings, gears and pumps, in different configurations. These powertrains are critical components for industrial operations, but also for our everyday life. Imagine an elevator not running, the water pressure dropping or the factory conveyor stopping. To avoid these inconveniences, outages, or potentially dangerous situations, it is very desirable to keep a close eye on the condition of the electrical and mechanical equipment.
AR And that is what is done at the moment?
SK Not quite. Traditionally, powertrain monitoring has come at a cost that made it prohibitive to use for anything but the most critical applications. That’s because putting in a comprehensive monitoring system requires a sophisticated installation that is sometimes more expensive than the powertrain components themselves! Furthermore, the monitoring equipment and software must be installed and maintained by external specialists. I think you can see the dollars mount up in front of your eyes! For that reason, the industry often reverted to annual or bi-annual vibration measurements as a service, avoiding fixed monitoring equipment installations. This makes condition monitoring much more economical, but now there is a long period between measurements where things can still go wrong. And there is a safety risk, as the maintenance personnel must come close to the rotating machinery.
AR So how is ABB solving this conundrum?
SK With the service ABB Ability Condition Monitoring for powertrains →1.
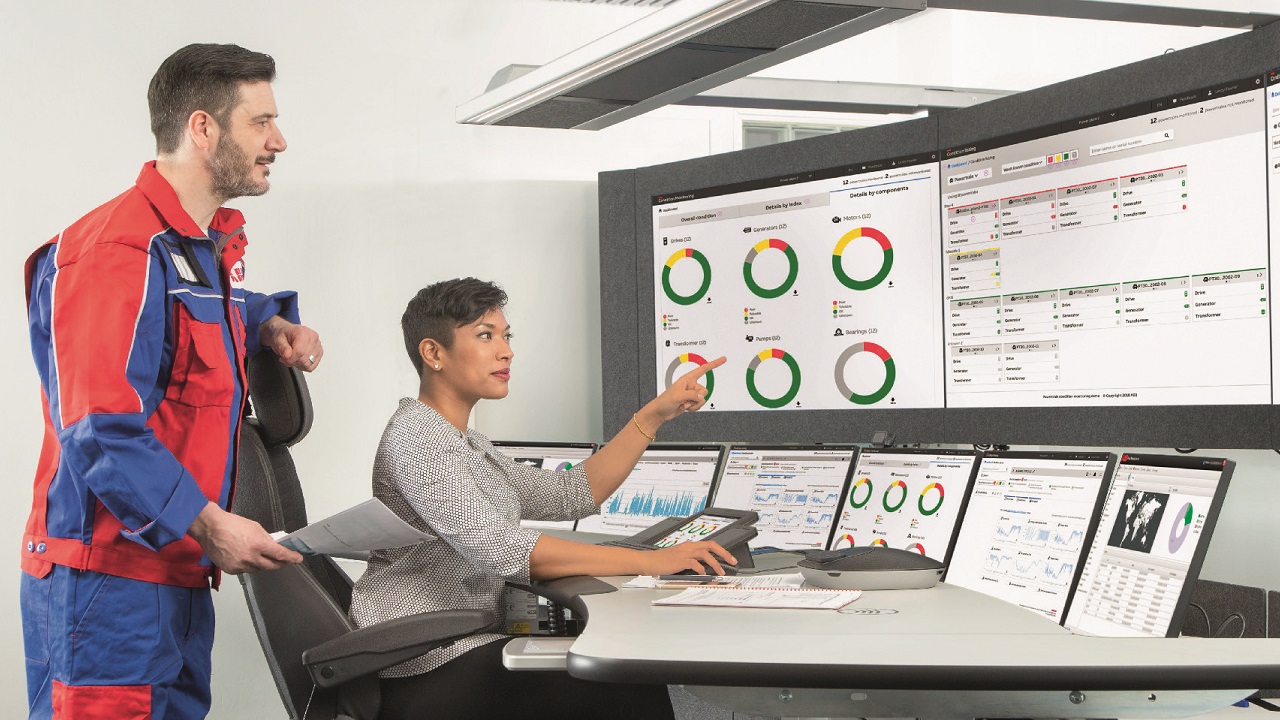
AR And how does that work?
SK The availability of low-cost, IoT-based – that’s the Internet of Things – wireless sensors and data transmission allows for permanent monitoring at a fraction of the cost of traditional condition monitoring systems. ABB Ability Condition Monitoring for powertrains is a cloud service that makes this data permanently available online at minimal installation cost. The solution is based on ABB Ability, which is ABB’s unified, cross-industry, digital offering that extends from the device in the field to the edge and all the way to the cloud. ABB Ability enables fast global service, proactive maintenance and a host of other benefits. This means the customer has better insight into their assets, thus enabling a safe, reliable and efficient operation that takes uptime and productivity to new heights.
AR What is contained in the condition monitoring solution?
SK The condition monitoring service currently covers drives, motors, bearings and pumps →2. Condition Monitoring for drives, for instance, is a service that provides real-time information about events in the connected frequency converters. Monitored parameters include the availability of the drives, environmental conditions and faults. With this service, possible problems can be detected early and necessary maintenance measures can be initiated.
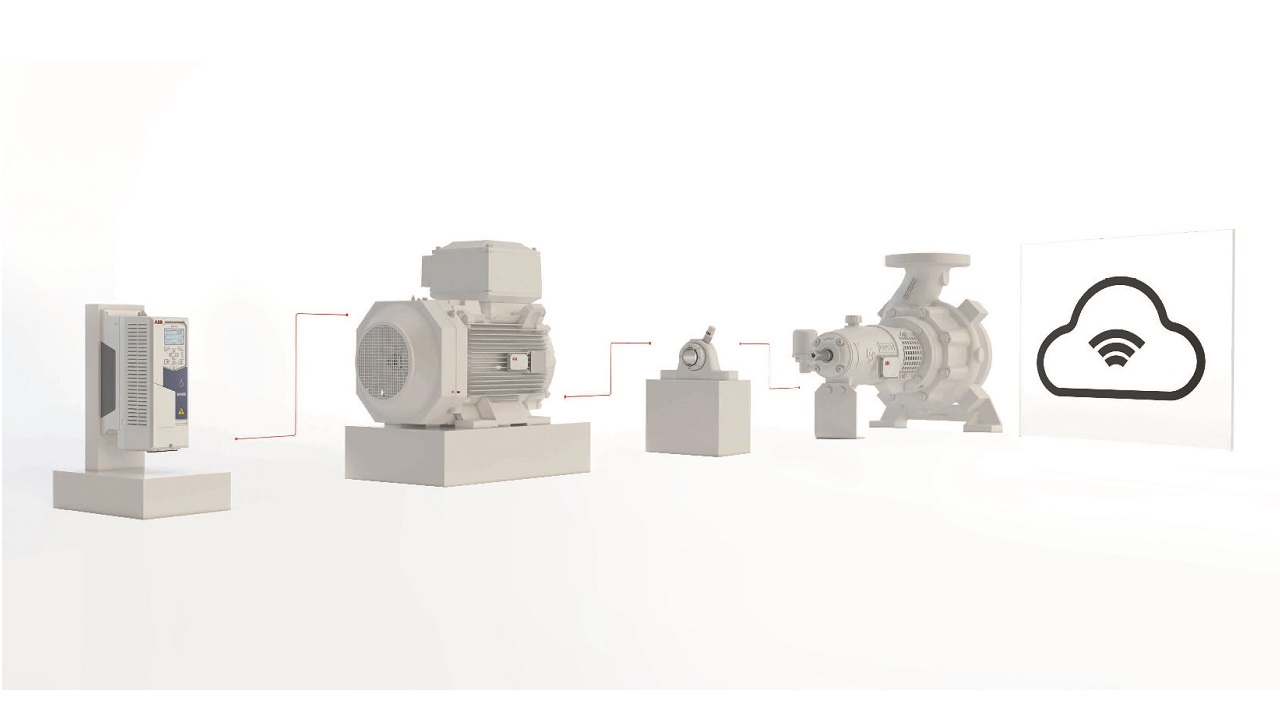
AR And I believe smart sensors play a role too?
SK Yes, we can equip motors with the ABB Ability Smart Sensor, which converts traditional motors into smart, wirelessly connected devices →3. The smart sensor is attached to, say, low-voltage motors for remote monitoring via an app to the Internet portal. This arrangement creates predictive insights that can increase availability while reducing energy consumption.
03a The Smart Sensor converts traditional motors into smart, wirelessly connected devices and enables an early warning of potential problems. Here it is seen on a mounted bearing. 03b Fitting and removal of the Smart Sensor is uncomplicated.
03 The ABB Ability Smart Sensor.
AR Are the smart sensors used elsewhere?
SK Yes, in mounted bearings, for instance, to supply status information. Bearings are critical components in the overall system and can be leading indicators of problems, so it is well worth keeping a close watch on them. Analysis of data from smart sensors is also used in pumps to monitor pump temperature, cavitation and bearing condition to prevent clogging or pump malfunction.
AR What other advantages does ABB Ability Condition Monitoring for powertrains give the customer?
SK One very valuable aspect is that the digital powertrain offers users a low-cost introduction to digital monitoring. The low entry threshold lets customers try it and see – and usually they are won over. Other benefits are fast commissioning and installation, as motors, bearings and pumps do not need to be cabled separately. This is a big plus as, if you do get problems during commissioning or operation, the cabling is often the culprit. Ease of use and integration, manufacturer independence, scalability and flexibility are further advantages.
AR Can this solution lead to more comprehensive monitoring?
SK Yes, unlike previous solutions that provided only point data on the state of individual components, there can now be permanent monitoring of all of the components. This comprehensive monitoring delivers benefits such as lower cost, higher uptime and more efficient operation.
AR If it is so comprehensive, does that mean the customer has to install a full-scale monitoring system from the outset?
SK No, not at all! Our solution scales. Any individual component of a powertrain – motor, bearing or pump – can be outfitted with measuring equipment and included in the monitoring system. And then other components can be simply added – just like clickable building blocks! The data is collected in a mobile, easily configurable and scalable cloud-based system that is available through apps and Web portals →4. This all means that a finished solution can be used for only a part of the powertrain – for example, just the motor – or for the entire driveline. Because setup is quick and flexible, the customer can try out various configurations and invest in the condition monitoring solution that best fits their needs.
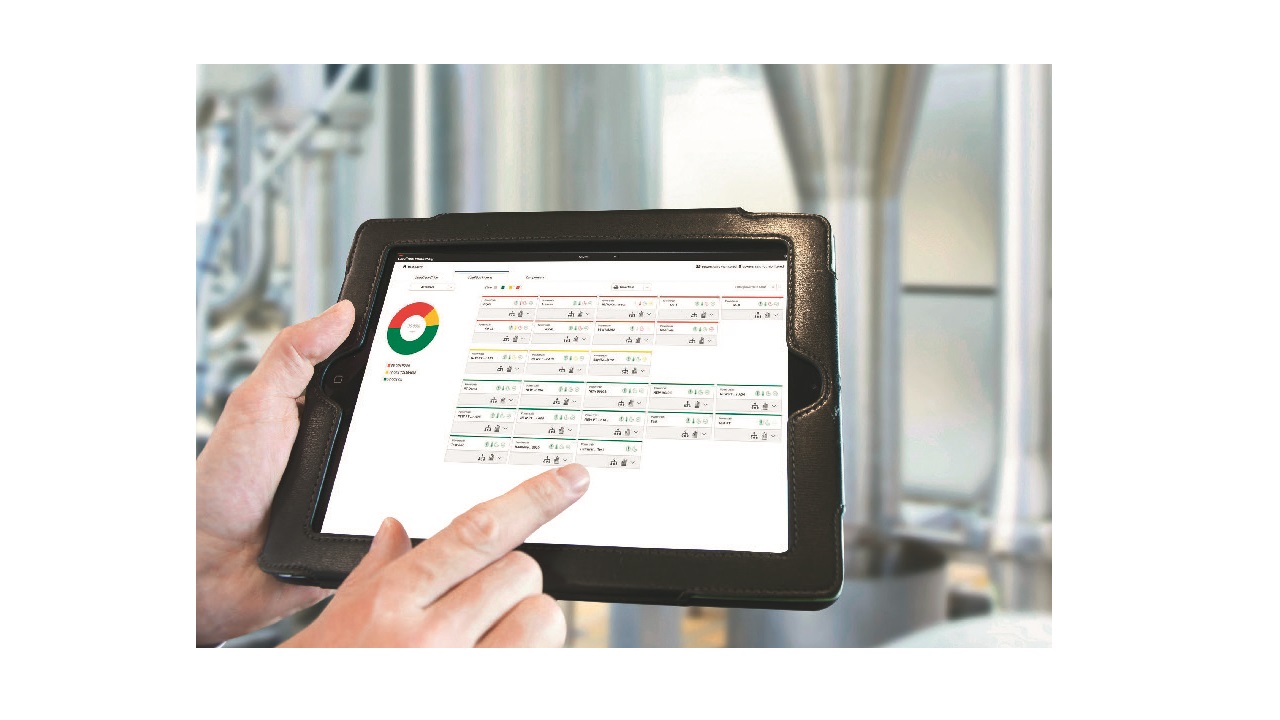
AR Are companies already using ABB Ability Condition Monitoring for powertrains?
SK Companies around the world are indeed already using it for optimized monitoring of their equipment. For example, the Swedish utility Uppsala Vatten och Avfall employs it to provide its operators with reports on real-time indicators for their pumping systems, such as reliability, usage, power consumption and load. Norway’s Glencore Nikkelverk uses it in a seawater pumping system that distributes cooling water around their plant. The integration of the ABB solution gives the mining company the opportunity to gather more information about the thermal condition of the drives and to compare the data with that of other monitoring solutions.
AR Are there other examples?
SK Yes. All around the world. The giant SSAB steel mill in Finland uses ABB Ability Remote Assistance, a service-ready offering that comes along with the ABB Ability Digital Powertrain offering, to increase the reliability of key drives in their coking plant. The remote monitoring system has already enabled faster fault detection in a variable-speed drive on site. Further afield, global agricultural company Olam International has installed the ABB Ability Smart Sensor for motors in several factories: a cocoa plant in Singapore, a dairy in Malaysia and a sugar factory in Indonesia.
The sensors allow remote monitoring of the motors and, thus, predictive maintenance →5. Downtimes have been significantly reduced and the life of the system has been extended. The customer is very happy and has told us that the ABB digital remote monitoring approach is much better than the previous method as shutdowns can be avoided and overall reliability increased.
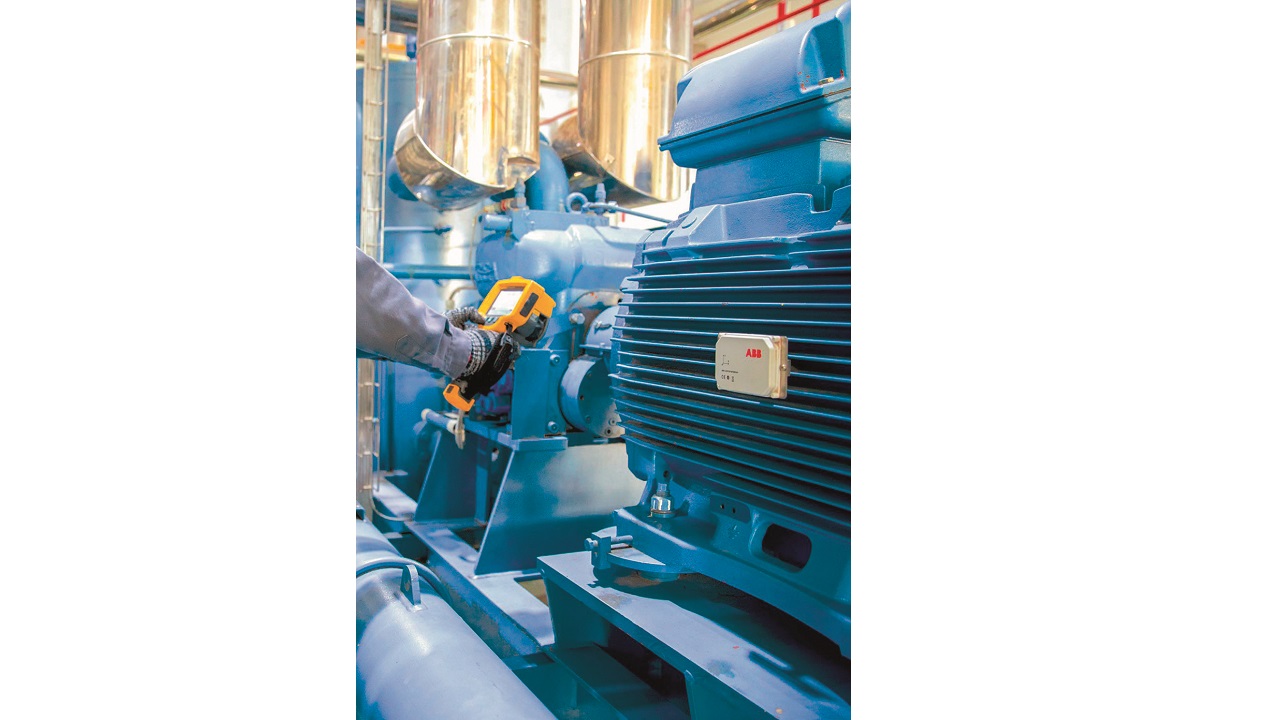
Another significant example is found in the world’s biggest free-fall simulator – Aero Gravity – in Italy. To meet the highest safety standards, Aero Gravity uses the cloud-based ABB Ability Condition Monitoring service for its drives. The service continuously collects data on key drive parameters and provides an overview through an indication system to identify areas that may need extra attention. Technicians can diagnose and analyze potential problems through an advanced set of online tools.
AR How about training personnel to use the system. Is it easy to operate?
SK A particular advantage of the powertrain analysis is the fact that all components report their status data in the dashboard of the user portal via an intuitive traffic light display. Green means that the component is OK; yellow indicates that the user should keep watching the component; and red indicates that there is a significant problem. Maintenance technicians and operators can thus maintain an overview of the powertrains. Of course, they then have easy access to any in-depth data they might need to review, such as vibrations, speeds, temperatures or power consumption.
AR Is there more to the digital powertrain than intelligent maintenance?
SK Absolutely. Imagine you are the manager of a major pump station. The total transparency of the operating point and the stress on all the components of your pumping systems allows you to select operating points for your different pumps that maximize their lifetime and minimize the energy consumption of your installation. So it is not only about predictive failures, it is also about intelligent and sustainable operation.
AR What are the next steps?
SK We launched the ABB Ability Digital Powertrain at the 2019 Hannover fair and have been busy with the work a major product launch entails. However, we already have expansions and enhancements in the pipeline. Maybe you’ll have me back in the near future to describe them!
AR Sönke, thank you for the interview.