ABB's new approach to performing factory acceptance tests (FAT) remotely is smart and sustainable. Instead of long-distance flights, our customers were conveniently located in their home country of Sweden, yet actively taking part in the FAT in China
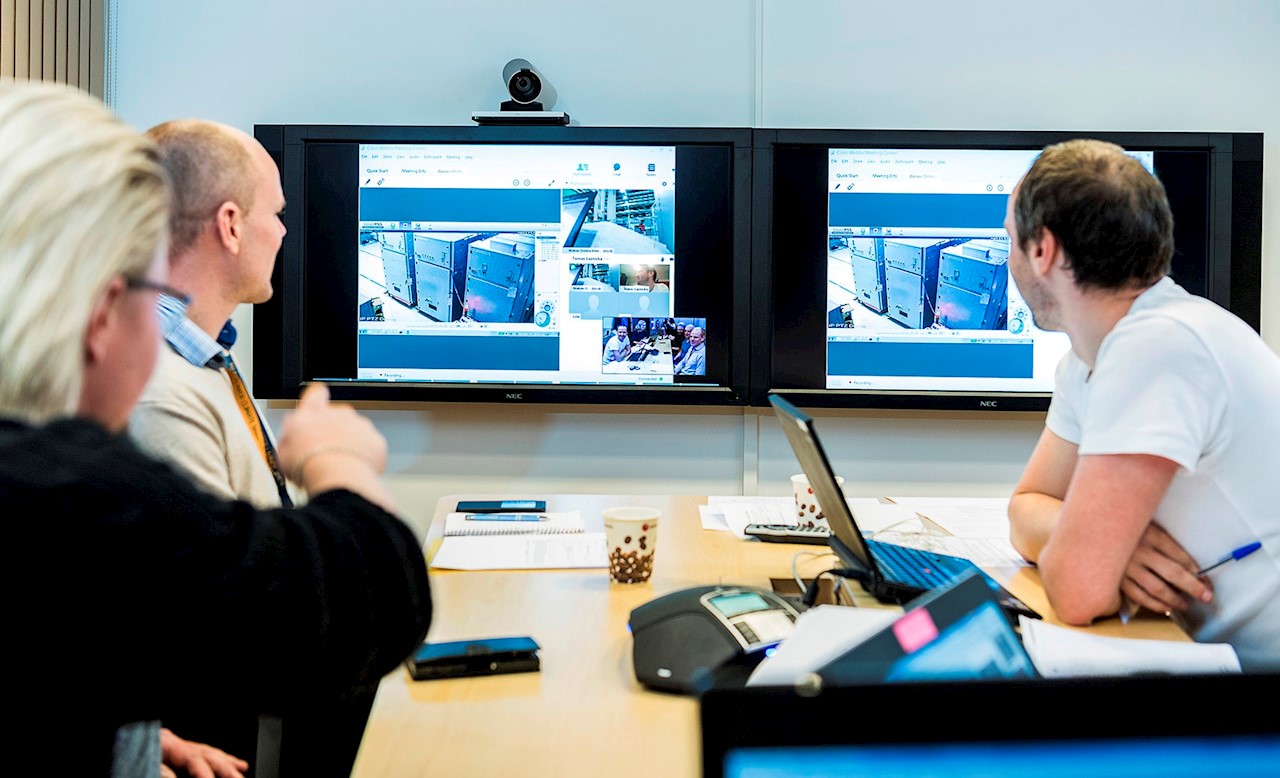
ABB has introduced an alternative approach to performing FATs (factory acceptance tests), known as Remote FAT. In the past the FAT has been an activity that had to take place in the factory, but today with the help of advanced information technologies, FATs can also be done remotely. A smart and sustainable alternative that significantly simplifies the activities and reduces associated costs.
In the village of Bäckefors, in the province of Dalsland in southwestern Sweden, Linjemontage has been contracted to rebuild one of Vattenfall’s transformer stations into a modern weather-proof indoor substation with the capacity to deal with increasing amounts of wind power. Three new medium-voltage switchgear from ABB’s UniGear product family will be installed in the substation.
"As per normal procedure, we and our customer Vattenfall, needed to ensure that each switchgear meets our specifications through a FAT before being shipped from the factory," says Jesper Höglund, project manager at Linjemontage.
For customized products and systems, a FAT is carried out before the products are shipped from the supplier's factory. During a visit to the factory, the customer verifies that the products ordered are manufactured according to their specifications, and observes the required testing of the product. Standard FATs tend to be associated with some cost, as participants need to travel to the factory where the product is manufactured. It might also involve obtaining visas, which is often a costly and cumbersome process.
Flexibility that saves time and money
In November 2017, a Remote FAT was carried out for the UniGear ZS3.2 switchgear to be delivered to the new substation. Five representatives from Linjemontage and Vattenfall, as well as ABB’s project managers, were conveniently located in ABB’s Västerås office in Sweden, yet they were able to actively participate in the FAT activities taking place 8,309 km away at ABB’s factory in Xiamen, China. Thanks to high-definition video conference and cameras, real-time voice communication and file sharing, the considerable geographical distance was virtually forgotten.
“We, as the customer, appreciated the possibility to perform the FAT remotely in this case. It’s a method with great benefits. Five people did not have to travel to the factory in China, saving us a lot of time and effort in making arrangements,” said Jesper Höglund, who sees great potential with Remote FATs. “In order for Remote FAT to work optimally, you need a high-speed connection and a well-structured program encompassing each step.”
“Here we have a group of people that had otherwise been taking long-haul flights to China. Through the Remote FAT, not only did we save a number of travel days and associated costs, we reduced the climate impact significantly,” said Tomas Laznicka, ABB’s project manager for the Bäckefors project.
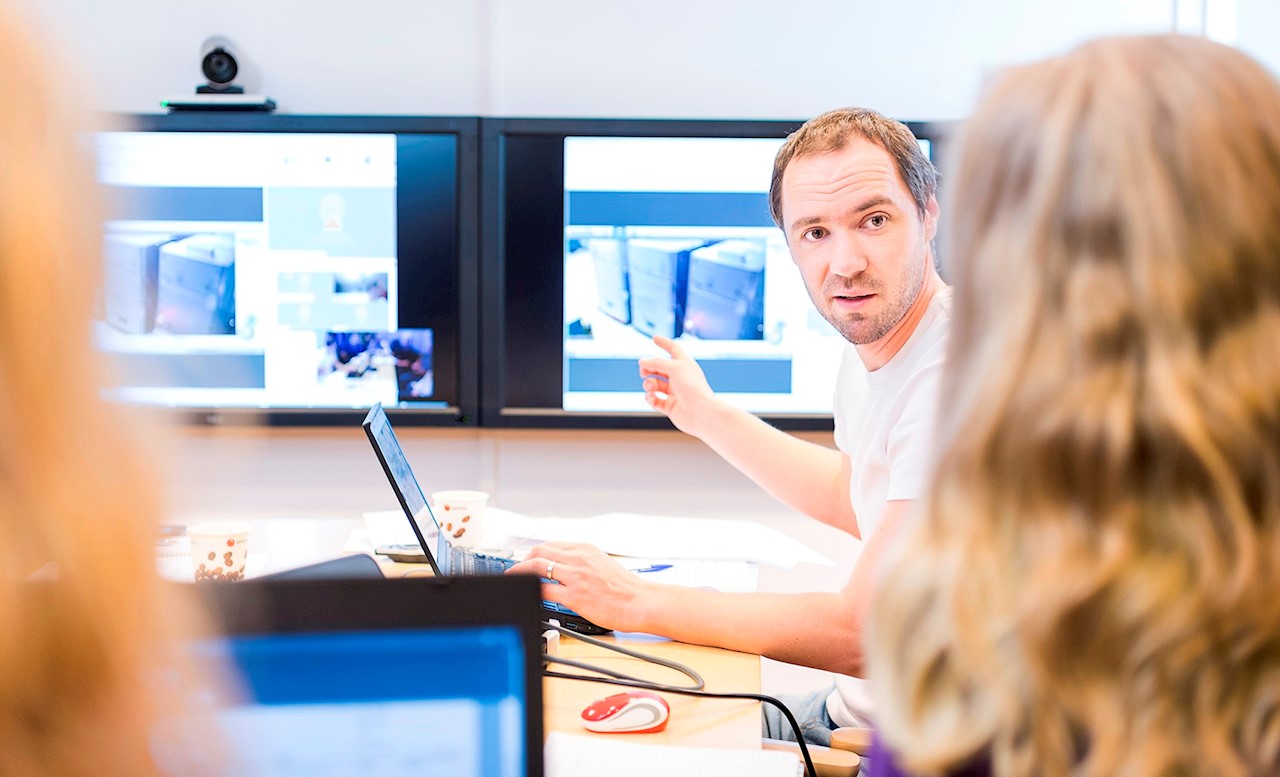
How is it done?
Remote FATs are based on an internet cloud service and with the help of computers, phones and touch screen tablets, the FAT is carried out using high-definition video, real-time voice communication and file sharing. There are several cameras in use, so the focus can be shifted to different components, using zoom-in or out functions, or by switching camera views. Using this application, data is easily monitored and stored, bringing easy traceability of records, and on top of voice communication, there is also a chat function available.