Swindon-based car parts manufacturing plant increases throughput time and improves working conditions through robot automation
BMW Group’s Swindon plant makes a high volume of parts for the iconic Mini. This creates over 200 tonnes of scrap steel each day to manage.
Previously, scrap steel bales weighing over 200kg were conveyed from the baling machine onto a rotational conveyor and dropped down a chute two metres into a scrap bin. Once full, the scrap bin was transported to the local metal recycling facility.
This process presented a few challenges. Firstly, it generated a lot of noise, posing a potential health risk for people in close proximity. Secondly, the lack of control over the two metre bale drop invariably resulted in a chaotic filling pattern and pile-ups which caused conveyor stoppages. Dropping the heavy bales also increased the risk of mechanical damage to the bins, which could result in downtime for repairs.
Lastly, it was a challenge to match the pace of the baling process with the distribution conveyor – any delays or faults in either stage could slow the entire process.
After conducting various trials to get a better understanding of whether the previous system could be retained with modifications to the process, BMW Group Swindon opted for a new concept utilising ABB’s IRB 8700 to help minimise the impact of the bale drop and ensure more effective filling of the bin. The largest ABB robot on the market, the IRB 8700 has a payload of up to 1000kg and a reach of up to 4.20m.
Close collaboration between BMW Group’s Press Engineering Department and ABB’s Robotics business in the UK resulted in a new robotic handling solution. The bales are still pushed along a mechanical bale chute but now first enter a bale separation unit where each bale is separated from the bale queue, enabling the robot to take one bale at a time. Armed with a servo-driven gripper, the IRB 8700 picks the bales and places them via a pre-defined pattern into the scrap bin.
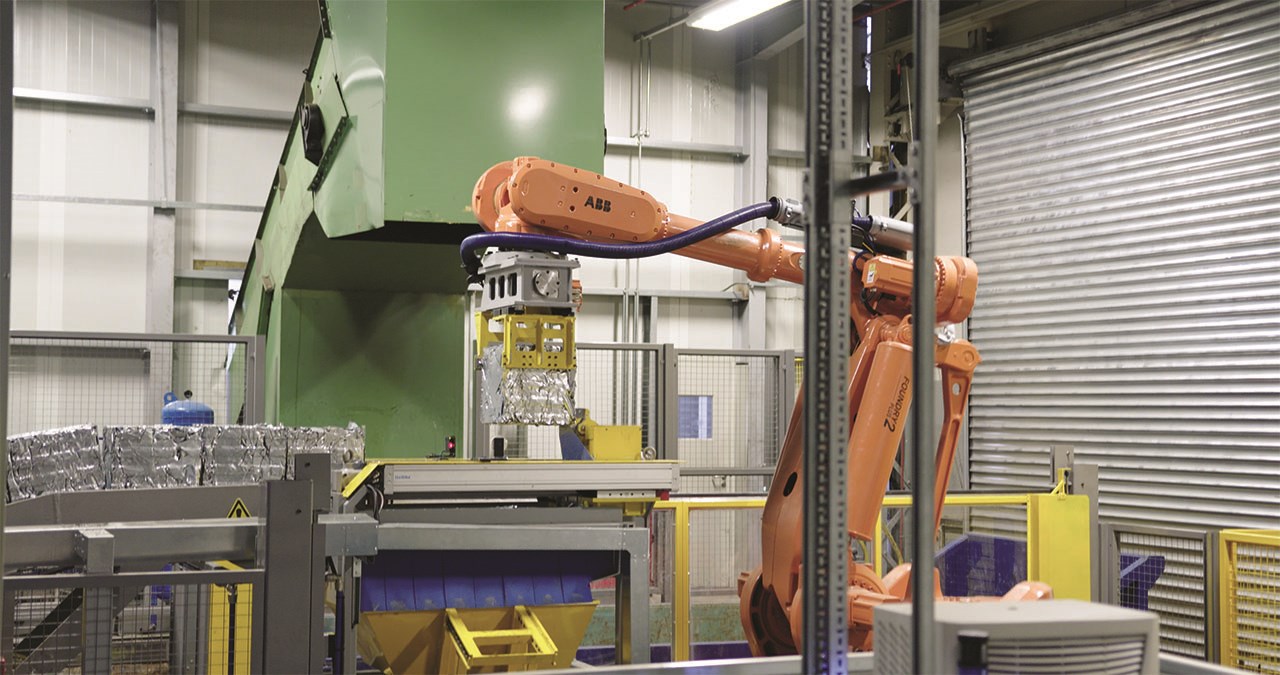
The advantage of the servo gripper is that it can be integrated as a seventh axis directly in to the robot controller. This eliminates the need for a separate control system, and is more efficient than a hydraulic system as well as maintenance friendly.
The increased speed of the robot system has resulted in an average reduction of five seconds cycle time for the bale stacking process. As previously, once the bin is filled it is collected by the HGV.
Furthermore, the speed of the IRB 8700 means that even with the introduction of an organised bin filling pattern, the processing time for bale stacking has been reduced by 16% to 25 seconds as opposed to 30 seconds.
The bale placing pattern means that the scrap metal bin reaches an optimum filling level of 60 bales over two levels. At a total of almost 13 tonnes, this remains within the maximum permitted load for transport on public roads. Optimising the available space also reduces the potential slippage of bales during bin pick up.
To ensure permanent and uninterrupted scrap disposal, the system consists of two bale stacking stations so that when one bin has been filled, the other can begin to be filled straight away.
The control over the process provided by the robot means that the drop is now only 50mm. This has significantly reduced the noise generated, leading to an improved working environment for employees as well as optimising the space available within the bins. In addition, the bales are not always a perfect cube and occasionally have shards of metal sticking out. Therefore, if the drop were any less there could be damage to the sides of the bins caused by knocks from displaced bales.
Pre-built and commissioned in a warehouse at BMW Group’s Swindon plant, the robot cell was installed over the four day production free period over an Easter holiday. Robert Low, Account Manager, ABB Robotics explains, “Downtime on the factory floor is very disruptive for our customers. The fact that we could pre-build and commission this solution weeks beforehand in a different location was a great advantage for BMW.”