Vinay Kariwala ABB Ability™ Innovation Centre, Bangalore, India, vinay.kariwala@in.abb.com; Chakravarthy Suhas, Daniele Angelosante Former ABB employees
Air pollution regulations are becoming tighter in many countries, with regulatory focus on continuously validated measurements of emissions. Many countries now require 24/7 monitoring of NOx, carbon monoxide, carbon dioxide, sulfur oxides, hydrochloric acid and hydrogen fluoride. Often, dust, mercury and dioxins must also be monitored. Not surprisingly, these tougher regulations bring with them increased compliance overheads for operators: In Europe, for example, measurements must be validated every hour. Three hours without measurements invalidates an entire monitoring day and annual monitoring downtime may not exceed 11 days (97.5 percent availability).
ABB Ability™ digital services for gas analyzers
Unfortunately, just as regulations are becoming stricter, in-house analytics expertise is becoming rarer. This diminishing pool of knowledge can lead to delays in troubleshooting emission-gas analyzer issues and, thus, endanger emission compliance. A robust approach to maintenance helps counteract this risk.
Until now, ABB gas analyzers have very often been subject to a preventive maintenance strategy in which periodical inspections and service interventions are performed to reduce breakdowns and enhance equipment life →01. This approach guarantees availability and removes the burden of knowledge from customer-supported personnel.
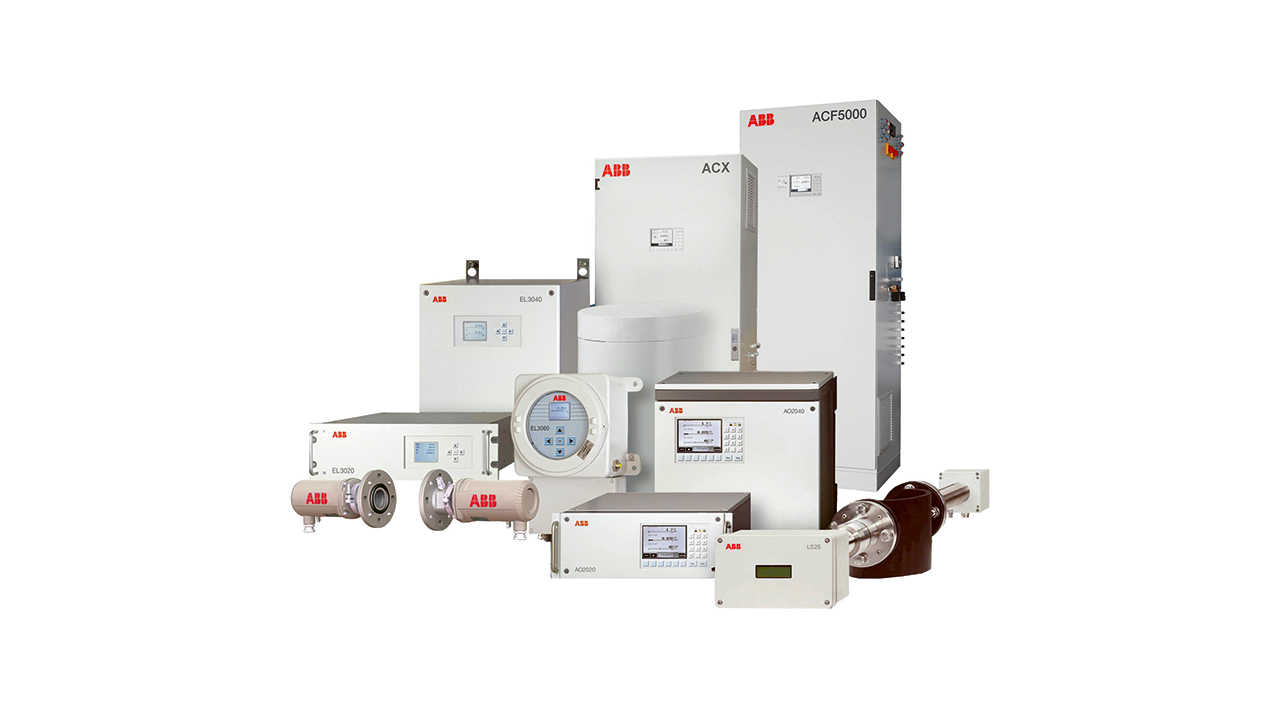
Now, digital services for gas analyzers can help strengthen the benefits of preventive maintenance as well as aid the shift from preventive to predictive maintenance. This ABB Ability™ offering consists of:
• ABB Ability™ Remote Assistance for measurement devices
• ABB Ability™ Condition Monitoring for measurement devices
ABB Ability™ Remote Assistance for measurement devices
ABB Ability™ Remote Assistance for measurement devices is a service aimed at improving the customer experience during technical support. The service enables an authorized ABB service engineer to log in to an on-site industrial-grade gateway – after the customer has requested intervention from the call center – and connect with the device under investigation to collect all the data required for troubleshooting the problem. Instead of an engineer having the customer step through the device diagnostics over the phone, the engineer can perform the troubleshooting. The customer receives, via mail or phone, a clear overview of progress and a solution or a solution recommendation.
The ABB Remote Assistance industrial-grade gateway has been designed to fulfill stringent cyber security requirements. Gateway usage policies are defined and enforced to prevent malicious access. Only authorized and trained ABB service personnel will be able to access the gateway and device data, and only with the customer’s consent. Gateway access can be through a 4G network or via Ethernet. Rigorous security measures, including firewall restrictions, are applied to these networks to ensure cyber security.
Together with ABB’s Dynamic QR Code assistance for analyzers – an ABB service product that provides comprehensive diagnostics and a real-time health check of an analytic system without any need for training or remote connectivity [1] – the ABB Ability™ Remote Assistance for measurement devices represents the first layer of digital service products provided for this type of product.
ABB Ability™ Condition Monitoring for measurement devices
A second digital service product that is designed to provide condition data is the ABB Ability™ Condition Monitoring for measurement devices. This service product is, as with the ABB Ability™ Remote Assistance for measurement devices, delivered via an industrial-grade gateway. The gateway is connected to the analyzers on-site and regularly monitors key tags that reflect their health. Retrieved data is stored in a database and processed to uncover early warning signs of degradation and its possible source. The data and findings are collected in health reports that can be accessed by ABB service engineers or the customer and can be sent via email to authorized personnel →02.
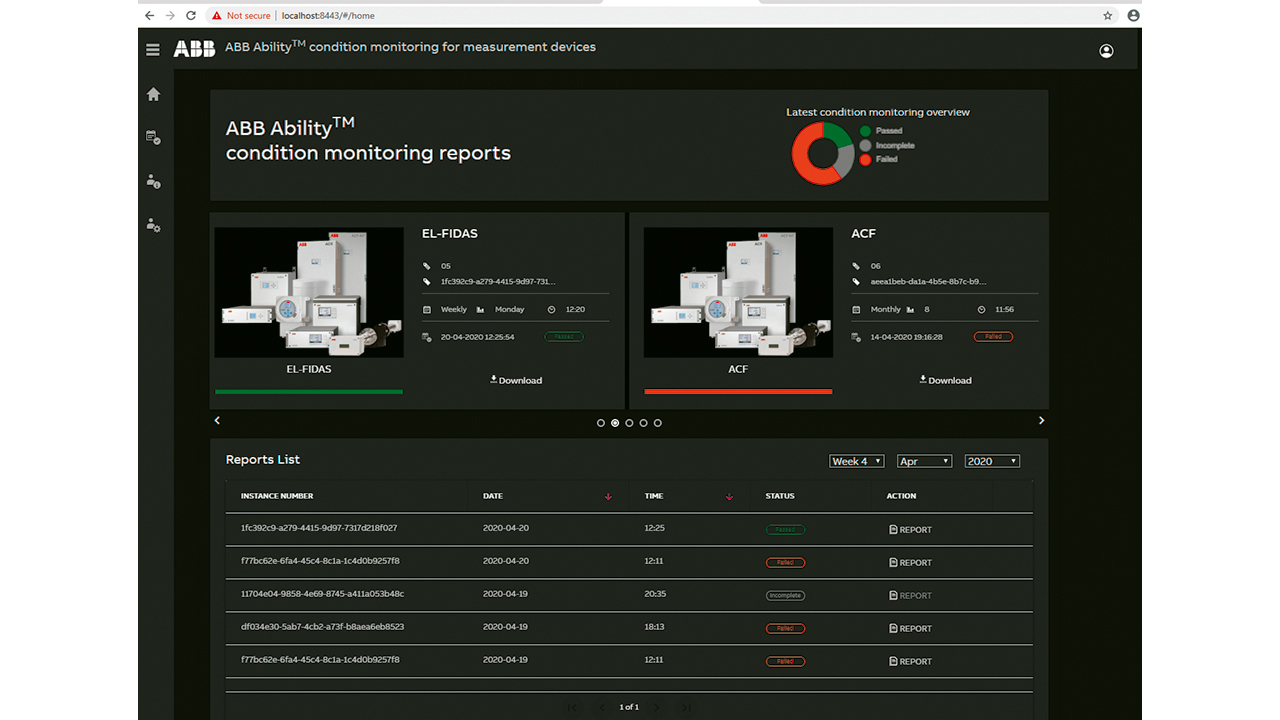
Health checks can be performed at scheduled intervals (daily, weekly, or monthly) to collect real-time measurements and diagnostics. ABB specialists evaluate these parameters against established performance benchmarks to provide service recommendations. Findings can lead to the specific maintenance activities necessary to avoid unexpected stoppages due to excessive deterioration of critical components. Problems can be resolved during a scheduled maintenance visit or plant shutdown before an actual failure happens.
Such pre-emptive intervention is crucial for gas analyzers that play a critical role in process control or environmental emission monitoring, as well as for analyzers in inaccessible locations – eg, in marine, offshore, or mining applications.
Ultimately, the goal of the ABB Ability™ Condition Monitoring for measurement devices is to avoid unplanned downtime and optimize the total cost of ownership.
Standalone solution
The ABB Ability™ Condition Monitoring for measurement devices can work as a standalone on-premise solution without the need for external ABB intervention and the health check report can be analyzed by the customer’s maintenance personnel. At any time, customers can contact ABB to discuss maintenance strategies. This approach is ideal for self-maintainers where the customer maintenance personnel can leverage the data provided by the ABB Ability™ Condition Monitoring for measurement devices with the aid of in-house expert resources.
ABB Ability™ Condition Monitoring for measurement devices complements ABB Ability™ Remote Assistance for measurement devices for a complete ABB-connected remote service offering.
Business intelligence engine
At the heart of the ABB Ability™ Condition Monitoring for measurement devices is a business intelligence engine, which captures data from the analyzers, analyzes it and produces an indication of the analyzer’s health. This engine is in the form of a Web service, which makes it easy to accommodate equipment configuration changes. A cloud-based version of the service, available soon, will further increase flexibility.
The solution is conceived as a platform that provides basic services – such as a report generator, data analysis engine, etc. This architecture simplifies the addition of new analyzers. The data definitions and related analysis software for a specific analyzer type reside outside the plat-form – in the so-called verification definition files – which speeds the onboarding of new analyzers and simplifies software component maintenance.
Database confidentiality
Data is a critical part of the solution and an ABB custom-made database is used to store it. This database is kept loosely coupled with the rest of the software to ensure data confidentiality and controlled access. Analyzer data is stored in the database along with a timestamp for every data point to ensure the correct data set is retrieved for the creation of historical reports.
The solution features a fully-fledged user management system in compliance with ABB’s cyber security norms. Other critical elements of cyber security such as system hardening, data encryption and secure data transmission are also addressed. Important data points are encrypted and stored. The complete solution, along with the hardware, is tested by the Device Security Assurance Center, which is an advanced security lab within ABB.
More than gas analyzers
ABB Ability™ Remote Assistance for measurement devices and ABB Ability™ Condition Monitoring for measurement devices currently support ABB’s product line of continuous gas analyzers (CGAs). Support for other product lines, including gas chromatographs and spectrometers is currently under development. The two digital services will be extended to include ABB’s digital advanced service offering such as data analytics, and predictive maintenance.
A better view of things
To complement the service portfolio and improve the customer experience, ABB exploits appropriate new technology, for example, augmented reality (AR), which is used to visualize virtual data superimposed on the real world. ABB Ability™ Remote Insights for service, for example, is a collaborative application that improves interaction between remote experts and field personnel by enabling live instruction and guidance that can be overlaid on live video using AR.
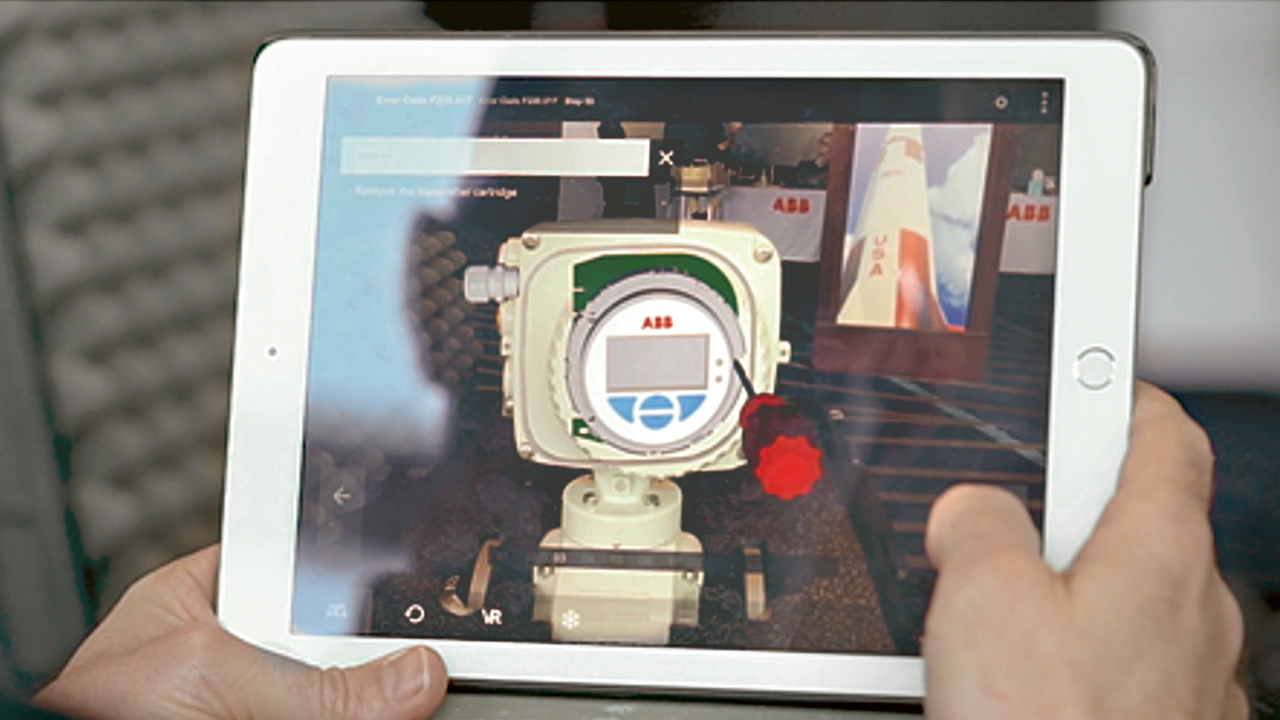
Troubleshooting of industrial devices is primarily based on experience and offline manuals. A drawback of the latter is that the engineer must continuously shift his vision between the manual and the device under investigation. Two AR-based approaches have been developed to remedy this situation: The first uses a 3-D computer-aided design (CAD) model of the device superimposed on the real device, along with step-wise instructions for troubleshooting. The second approach connects a remote expert with the local engineer’s AR device via a video call. Thus, the expert sees exactly what the service engineer sees and can guide the engineer remotely →03 – 04. The expert can annotate the service engineer’s view and can send artifacts, such as images and videos, to facilitate troubleshooting. This approach makes best use of the expert’s time and allows coverage of many more sites than would be the case were the expert to have to travel to each one.
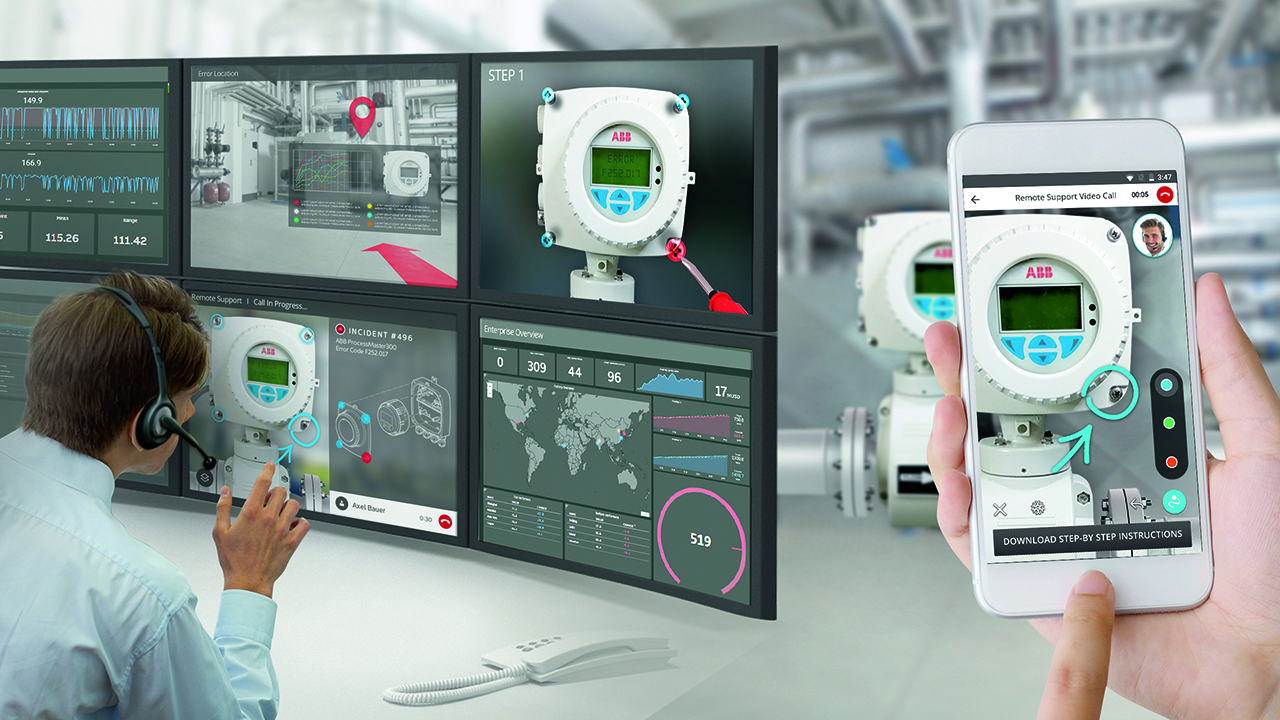
One application area in which AR is expected to offer major benefits is the repair of emission monitoring equipment on marine vessels. Currently, when a problem occurs, the onboard maintenance engineer must phone ABB service. If the problem cannot be rectified over the phone, then an ABB service technician would either be waiting at the next port or, in extremely urgent cases, be flown directly to the vessel. With the use of AR, the maintenance engineer can fix the issue with assistance from 3-D CAD models or the expert, who is connected to the engineer’s AR equipment as described above.
Expertise and technology
With emission regulations tightening, financial penalties for emission transgressions increasing and experienced in-house analytics experts becoming rarer, it is important that companies bring in the very best external expertise and technology to help them keep their gas analysis equipment in working order. ABB Ability™ Remote Assistance for measurement devices and ABB Ability™ Condition Monitoring for measurement devices are two new digital services for gas analyzers that provide exactly such expertise and technology. With these two products, regular periodical preventive inspection is enhanced and the way is opened to predictive, as well as simpler, maintenance. The products enable fast and incisive remote intervention by ABB experts, thus ensuring that the very best skills are employed in keeping emissions monitoring equipment in top order and providing peace of mind.
References
[1] D. Lincoln et al., “Dynamic QR Code speeds service response,” ABB Review, 1/2018, pp. 40 – 45.