Za światowym sukcesem wódki Absolut stoi nie tylko kampania reklamowa, która została określona przez magazyn „Advertising Age” mianem „jednej z najlepszych kampanii XX wieku”, ale również dbałość o sposób, w jaki ta wódka jest produkowana.
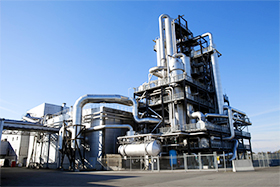
Specjalna zimowa odmiana pszenicy, dojrzewająca na urodzajnych polach południowej Szwecji oraz subtelny proces destylacji odgrywają ważną rolę w nadawaniu produktowi końcowemu charakterystycznej, delikatnej, zbożowej nuty. Proces destylacji wódki Absolut jest teraz sterowany przez system 800xA firmy ABB. Kilka kluczowych funkcji sterowania, takich jak dane opisujące tendencje rozwojowe, monitoring stanu posiadania oraz zarządzanie informacją Smart Client, pomagają utrzymać światową reputację produktu w zakresie smaku i jakości. Wytwarzanie wódki Absolut to skomplikowany i subtelny proces.
Utrzymanie właściwej temperatury fermentacji jest kluczowe dla zapewnienia wysokiej jakości, oczekiwanej od tej międzynarodowej marki. Aby zagwarantować sukces między innymi pod tym względem, firma Absolut niedawno rozwinęła środowisko operatora w gorzelni Nobbelov niedaleko Ahus na południu Szwecji o System 800xA.
Łatwe do przeanalizowania dane opisujące tendencje rozwojowe pozwalają operatorowi wykrywać i korygować odchylenia w czułym na zmiany procesie fermentacji. "Jeśli coś idzie źle i nie może być poprawione na czas, możemy stracić nie tylko całodniową produkcję, ale również jesteśmy zmuszeni wyrzucić to, co do tej pory wyprodukowaliśmy" - mówi Johnny Stahl. "Funkcja śledzenia tendencji rozwojowych w procesie wbudowana w System 800xA pozwala nam monitorować kluczowe wartości skuteczniej niż dotychczas. Dodatkowo, taka informacja jest również wizualizowana dużym ekranie. To pozwala naszemu wielokierunkowemu zespołowi obserwować co się dzieje oraz sugerować odpowiednie działania, szczególnie w sytuacjach krytycznych".
Zwiększona niezawodność i skuteczność procesu
Kilka innych funkcji Systemu 800xA pozwala firmie Absolut optymalizować działania operacyjne. Dla przykładu monitoring stanu posiadania sygnalizuje potrzebę konserwacji konkretnej instalacji i generuje raport diagnostyczny, który pomaga zespołowi serwisowemu zawczasu rozwiązać pojawiający się problem, zanim zakłóci on całą produkcję.
Zapis historii procesu ułatwia operatorom zwiększenie efektywności procesu poprzez wyświetlanie tego, jak energia została wykorzystana w danym okresie czasu. Obecnie gorzelnia firmy Absolut zużywa zaledwie nieco ponad jedną kilowatogodzinę energii na litr czystego alkoholu, dzięki czemu jest najbardziej efektywną energetycznie gorzelnią na świecie.
"Wykorzystując funkcję Smart Client mamy łatwy dostęp w biurowych komputerach do danych specyficznych dla procesu"Funkcja Smart Client poprawia przepływ informacji
Anders Andersson, projekt menedżer, z chęcią wymienia zalety funkcji Smart Client Systemu 800xA. To funkcja, która umożliwia dostęp do danych procesu systemu automatyki z każdego miejsca, w którym operator (lub inny autoryzowany pracownik) się znajduje i o każdej porze. Przed wdrożeniem Systemu 800xA było to możliwe wyłącznie poprzez zeskanowanie wielu różnych systemów, co pochłaniało sporo czasu i było podatne na błędy operatora. Obecnie Smart Client szybko identyfikuje tzw. wąskie gardła w systemie, dzięki czemu operator może zareagować szybko i skutecznie.
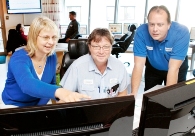
"Wykorzystując funkcję Smart Client mamy łatwy dostęp w komputerach w biurze do danych specyficznych dla procesu" - mówi Anders. "Naszym ostatecznym celem jest zintegrowanie naszych systemów biznesowych, wagowych i laboratoryjnych z Systemem 800xA. To postanowienie nie powinno być trudne do zrealizowania".
System przyjazny dla użytkownika, w którym operator jest na pierwszym miejscu
W krótkim czasie wszyscy uświadomili sobie, że System 800xA jest przyjazny dla operatora. "W początkowym etapie użytkownicy pracowali na symulatorze, dzięki czemu mogli przekazać ABB wartościową informację zwrotną" - powiedział inżynier automatyki Tony Knutsson. "Po dalszych pracach na miejscu instalacji i weryfikacji w ABB, nowy system został zainstalowany, a gorzelnia wznowiła działalność wykorzystując pełną zdolność produkcyjną w ciągu zaledwie pięciu dni".