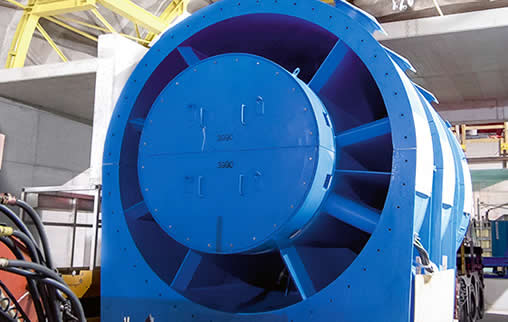
- Zewnętrzna średnica wentylatorów wynosi ok. 3,5 m. Biorąc pod uwagę również zainstalowaną maksymalną moc rzędu 15,6 MW, czyli mniej więcej tyle, co 25 samochodów wyścigowych Formuły 1 razem wziętych, jest to nie tylko największy, ale i najpotężniejszy tunelowy system wentylacji na świecie - mówi Alwin Larcher, który pełni funkcję dyrektora projektu ABB dla pakietu C AlpTransit Gotthard AG (ATG). W 2011 roku ABB otrzymała zamówienie na wentylację eksploatacyjną wspólnie z niemieckim TLT-Turbo GmbH. ABB była odpowiedzialna za całe elektryczne wyposażenie systemu, podczas gdy TLT jako kierownik konsorcjum odpowiadała m.in. za instalację gigantycznych wentylatorów.
Przez lata, ten duży projekt wymagał wysiłków na etapach planowania, budowy i instalacji. Na początku 2015 roku ABB i TLT stanęły przed ostatnim wyzwaniem: rozruchem technicznym (IBS). - W tunelu o bardzo dużych rozmiarach i przy skomplikowanych zależnościach między różnymi systemami, z pewnością nie było to rutynowe zadanie - podkreśla Larcher.
Zaczęło się już od testów medycznych w Szwajcarskim Instytucie ds. Zabezpieczeń przed Nieszczęśliwymi Wypadkami (SUVA), dotyczących sprawności fizycznej pracowników mających pracować w tunelu oraz wymaganych szkoleń z zakresu bezpieczeństwa. Było to konieczne do uzyskania pozwolenia na pracę w najdłuższym i najgłębiej biegnącym tunelu kolejowym na świecie. W niektórych miejscach tunel pokrywa 2300 metrów skały o temperaturze sięgającej 46° C. Jedno centrum wentylacyjne zlokalizowane jest w szybie w Sedrun, ok. 800 metrów w głębi góry i 800 metrów ponad poziomem drogi. Drugie w Faido, w budynku wejściowym obok długiego na 2,8 km tunelu dostępowego do zachodniego tunelu. Do wielofunkcyjnych stacji, w tym również do stacji awaryjnych, można się dostać jedynie poprzez północne i południowe wejścia w Erstfeld i Bodio oraz samochodem przez tunele dostępowe w Faido. Znajdują się one w odległości odpowiednio 20 i 17 km od północnego i południowego wejścia.
Rozruch techniczny
Rozruch techniczny obejmował nie tylko komponenty elektryczne wentylatorów w centrach wentylacyjnych, ale także integrację ich sterowania w głównym systemie sterowniczym tunelu. Podczas rozruchu przetestowano także m.in. system czujników składający się z ponad 80 czujników temperatury, wilgotności i prędkości wiatru, rozmieszczonych na całej długości obu tunelów. Również integracja systemu lokalizowania pożarów w czterech stacjach awaryjnych została rozplanowana przez ABB.
- Współgranie systemów w tunelu, od systemu ochrony pociągów po systemy kanalizacji, oświetlenia i wentylacji, jest kluczowe dla funkcjonowania tej konstrukcji stulecia - podkreśla Larcher.
Wyrazy uznania za pomyślne przeprowadzenie rozruchu wyraziła również AlpTransit Gotthard AG. - Po pomyślnym ukończeniu większości testów, przeprowadzanych od początku 2015 roku, chciałbym podziękować wszystkim zaangażowanym, za ich nieustanne wysiłki i pełną zrozumienia współpracę - dodaje Andreas Huber, starszy kierownik budowy wentylacji eksploatacyjnej / dźwigów w ATG.
Alwin Larcher, który ma na koncie duże projekty w całej Australii i na Bliskim Wschodzie, mówi że jako Szwajcar jest dumny, iż miał swój wkład w to przedsięwzięcie. Dla jego kolegi, Ralfa Roescha, głównego inżyniera odpowiedzialnego za system sterowania, który pracuje w ABB od 1994, była to również kwestia dużego zaangażowania emocjonalnego. - Jako stary budowniczy tunelów, włożyłem moje serce i duszę w ten projekt. Odłożyłem tymczasowo na bok moją pracę szefa działu, aby całkowicie poświęcić się temu zadaniu - mówi z uśmiechem.
Płuca dla całego tunelu
Było dużo do zrobienia, ponieważ ABB i TLT odpowiadały za obszerny pakiet w tym zamówieniu - począwszy od 24 wentylatorów strumieniowych we wlotach do obydwu tuneli w Erstfeld i Bodio, a skończywszy na ośmiu głównych wentylatorach wyciągowych i nawiewowych w centrach wentylacyjnych w Sedrun i Faido. Dwa centra wentylacyjne tworzą swego rodzaju "płuca" całego systemu i odpowiadają za wymianę powietrza wewnątrz tunelu. Wentylatory nawiewowe dostarczają z zewnątrz świeże powietrze - w Sedrun przez 800-metrowy pionowy szyb - którego dopływ jest regulowany poprzez system klap, a następnie powietrze rozprowadzane jest po tunelu. Wylatujące powietrze jest usuwane przez oddzielny szyb za pomocą wentylatorów osiowych z prędkością do 300 km/h (prędkość powietrza w wentylatorze).
Oprócz zwyczajnej wymiany powietrza, wentylatory muszą przede wszystkim dostarczyć wystarczającą ilość świeżego powietrza w razie pożaru, a jednocześnie usuwać dym przez długie szyby wydechowe, w szczególności po to, aby podróżni w nagłych przypadkach mogli opuścić pociągi i dostać się w bezpieczne miejsce. - "Mózg" systemu wentylacyjnego, czyli odpowiednie oprogramowanie, jest bardzo ważne, aby dokładnie dostosować wentylatory i klapy do różnych scenariuszy - mówi Roesch. Nadrzędny system sterowania reguluje pracę wentylatorów zakładając około 50 możliwych przypadków, łącznie z funkcjonowaniem na wypadek eksplozji.
Dużo wysiłku logistycznego
- Musieliśmy przeprowadzać nasze testy głównie w nocy z powodów związanych z bezpieczeństwem oraz z dużą prędkością zasysanego powietrza - tłumaczy Larcher. Logistyka i planowanie stanowiły wyzwanie, głównie z powodu koordynowania własnych prac prowadzonych pod ziemią z pracami wielu innych dostawców. - Pomimo szczegółowego planowania w biurze, kilkakrotnie musieliśmy szukać szybkich rozwiązań na placu budowy. Czasami wyglądało to zupełnie inaczej, niż się spodziewaliśmy - dodaje Larcher. Wyzwaniem była m.in. dostawa wagonami kolejowymi wentylatorów o średnicy wiatraka 2,8 m i ich instalacja w wąskich centrach wentylacyjnych.
Zobacz infografikę:
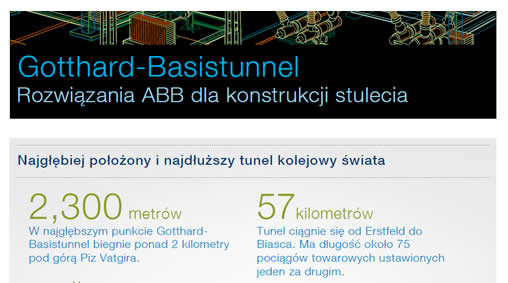