By Max Luedtke
As resources become harder to access over time, we need to go further and dig deeper to find them. At the same time, governments, investors and the global community want miners to operate more sustainably, with less impact on the environment and the global climate.
That’s helping push more mining underground, as well as forcing the industry to look for alternatives to the diesel that’s powered it for decades, while maintaining efficiency and productivity.
I discussed some of these challenges at a panel discussion organized by Business Sweden at IMARC 2023, covering topics including international co-operation, innovation, and the move to electrify operations, as we strive to make mining more sustainable, safer and more productive.
These industry discussions signal a time of change and of opportunity. To make the most of it, we need to rethink the way we plan mines, push innovation, and work together as an industry in real partnerships. All fine words, but let’s look at how it’s all actually going to work in the real world.
Planning for a sustainable future
To meet sustainability targets and stay productive, it’s clear we can’t design our future mines in the same way.
Electrification will mean more parts of the operation placing demand on a common source of power. That’s going to require careful and integrated mine and infrastructure planning, particularly if we are going to tap the potential of renewables.
What will be the mix of grid power and renewables? Will the mine design allow trucks to take advantage of regenerative braking? Will we be able to schedule production around energy availability?
To truly integrate operations, we need intelligent control systems. As well as well as orchestrating power, having a distributed control system, like ABB’s Ability ™ System 800xA ®, which also covers processes, operations, safety and maintenance - helps streamline decision making and troubleshooting, improving uptime and efficiency and helping make operations both safer and more efficient.
At ABB we’ve long said the greenest power of all is the energy you don’t have to use. The more efficient our operations, the greener they’ll be. And electrification is about much more than just haul trucks, so a holistic approach also helps us get more sustainable faster. Processes suitable for electrification and automation can be converted sooner, meaning faster gains across the mine which add up over time.
For example, integrating automation control with a ventilation on demand system like ABB Ability ™ Ventilation Optimizer can reduce ventilation power consumption by up to 50% thereby only ventilating areas that require it, rather than the whole mine - the sort of efficiencies that are only going to become more important as mines get deeper and hotter.
All the while, we can be working on the big-ticket items like those haul trucks, which are likely to go through an evolution, from trolley systems to trolley-battery hybrid, to full battery.
In Australia, developments that make it easier to relocate the overhead trolley infrastructure mean that we’re probably going to see electric haul trucks operating in this market sooner than some may think. Not only are they greener, but they’re also very productive, able to climb grades at twice the speed compared with trucks running on diesel and demanding less in ongoing maintenance and service.
Defining industry standards and working together
A crucial factor in getting both electrification and integration working is going to be partnerships across the industry, including everyone from mine owners, operators to OEM manufacturers and technology providers like ABB. If we want to change the industry, all parties need to have a say in how the technology and solutions develop.
ABB is already working in this deep partnership model in Australia, joining with ASX-listed diversified mining services group Perenti on a study for the full electrification of IGO’s Cosmos nickel project in Western Australia. The broad-ranging study brings together Perenti’s technical and services expertise, ABB’s eMine™ electrification and automation framework, and IGO’s desire to help move the industry forward by working with partners to help get solutions to make mining more sustainable to market more quickly.
Covering factors including mine design, fleet selection, power distribution, safety, cost modelling and more, the study is a key part of IGO's ambitious decarbonisation plans.
Sharing expertise in this way will be vital if mining innovation in fields like electrification and automation is going to accelerate. Interoperability is one area ripe for progress. The advantages are easily seen in areas like the interface between chargers and batteries and vehicles, for example, where common standards make life easier for everyone. Right across operations, standardising where it makes sense also allows us all to get economies of scale and solutions operators can more easily adopt and rely on. They make it easier to get the integration that’s going to make the mine of the future possible.
Sharing expertise has also helped the likes of Boliden and LKAB experts in forging innovation partnerships, both with mining OEMs, as well as with industrial groups outside mining that have solutions that can be ruggedised and adapted. And that helps bring innovation to market faster, a vital advantage if you are a smaller player in an industry with some very big global operators.
Working in partnership with LKAB and Boliden, ABB recently announced an industry-first test of an autonomous robot that scans walls and places explosive charges without the need for human guidance. Tested at the Boliden Garpenberg underground zinc operation, the ABB Robot Charger removes the need for human workers to handle explosives at the unsupported rock face, significantly lifting safety.
It typifies the kind of innovation miners are going to need as operations get deeper, but also the co-operation and partnerships that are going to drive the industry forward. ABB is now looking for more partners to help us drive the next stage of the Robot Charger’s development.
Now is the right time
Whether it's for electrification, autonomous systems or interoperability, the sooner we begin to engage with each other as an industry, the sooner we’ll see results. No one can completely overhaul the way mining is done by themselves. We have much to learn and the more we help each other, the faster we’ll have an industry that’s safer, more sustainable, and productive.
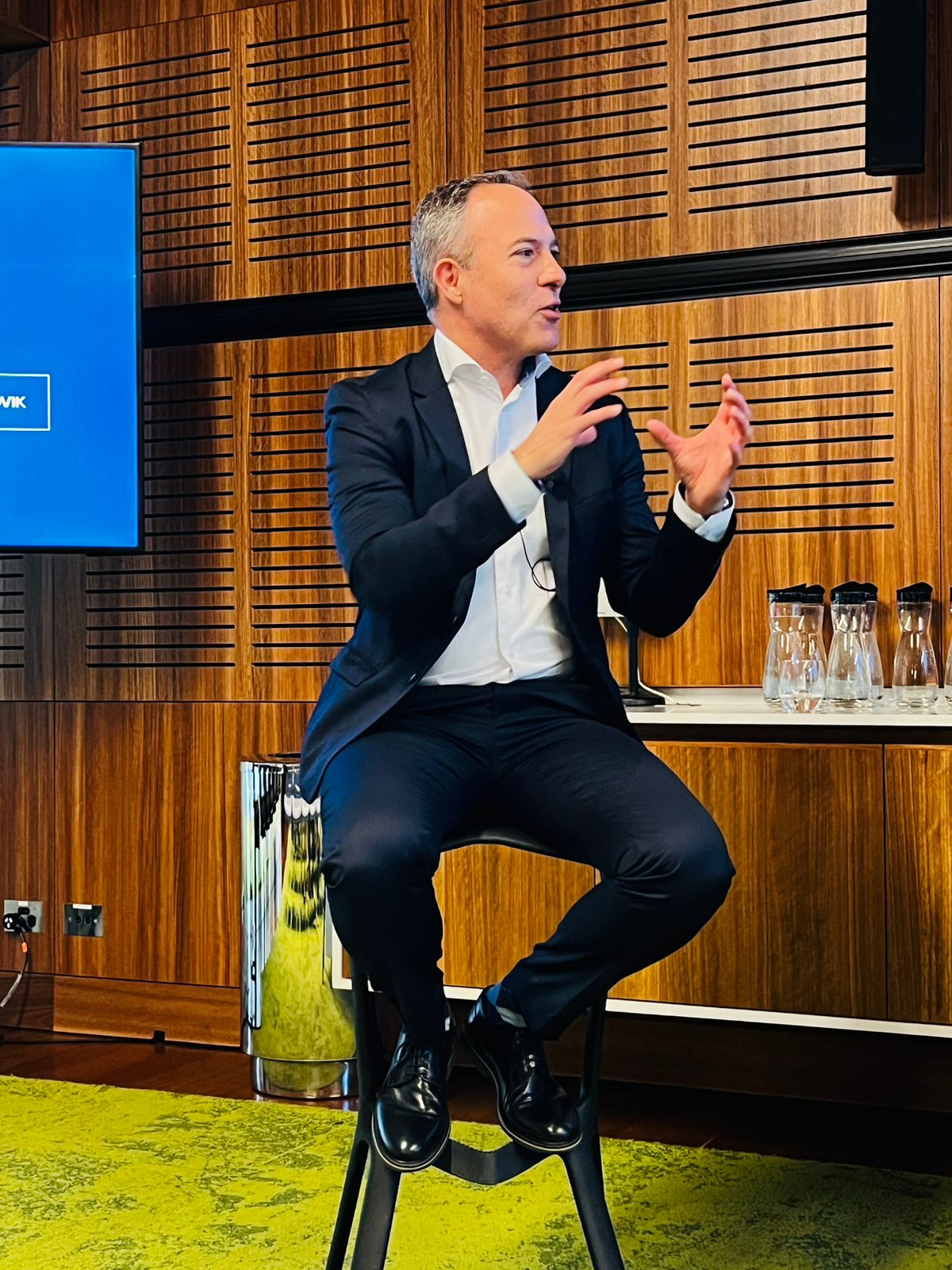
Pictured left, based in Switzerland, Max Luedtke is Vice President, Global Head of Mining, at ABB.
Pictured above with panel members Hans Wahlquist, Global Director Product Management, Epiroc, Simon Stone, Vice President Asia Pacific, Hexagon AB, and Wayne Scrivens, Vice President Au & NZ, Sandvik. Discussing How do Sweden's mining innovations foster international collaboration, distribute risks, and expedite implementation of new solutions" at IMARC 2023.