Durch Kombination von fortschrittlichen 3D-Druckverfahren mit neuen intelligenten Werkstoffen entstehen an führenden Hochschulen und Laboren analoge autonome Objekte, die sich mit der Zeit verändern, ohne dass dafür ein computergestützter Antrieb erforderlich ist. Das branchenübergreifende Potenzial dieser Technologie ist immens.
Wie wäre es, wenn sich künstlich erschaffene, komplex geformte Objekte wie lebende Organismen verhalten könnten, indem sie auf äussere Reize reagieren und sich ihrer Umgebung anpassen? Und was wäre, wenn diese Objekte wieder in ihren ursprünglichen Zustand zurückkehren könnten, sobald der Reiz wegfällt oder ein anderer aktiviert wird? Durch Veränderung einer grundlegenden Eigenschaft wie der Form könnten ohne elektromechanische und computergestützte Steuerungen Strukturen geschaffen werden, die sich selbst zusammenfügen, anpassen oder sogar reparieren. Die Auswirkungen für die Gesellschaft und Wirtschaft wären revolutionär. Auch wenn es danach klingt, ist dieser Gedanke längst nicht mehr Science-Fiction. Weltweit sind Forscher an führenden Forschungsinstituten dabei, fortschrittliche 3D-Druckverfahren mit neuen intelligenten Werkstoffen zu kombinieren, um 4D-gedruckte Objekte zu erschaffen, die sich genau so verhalten.
Im Zeitalter der vierten industriellen Revolution werden Branchen, die sich solche Möglichkeiten zu Nutze machen, wirtschaftlich zweifellos im Vorteil sein. Vor diesem Hintergrund investieren Institutionen und Unternehmen in neue, bahnbrechende Technologien, von denen der 4D-Druck besonderes Potenzial bietet.
Durch Kombination von 3D-Druckverfahren mit intelligenten Werkstoffen, mathematischer Modellierung und Algorithmen das maschinellen Lernens erschaffen Forscher dreidimensionale Objekte, die sich auf bestimmte externe Reize hin mit der Zeit verändern. Dadurch wird der 3D-Druck um eine vierte Dimension ergänzt und eine bisher nie dagewesene strukturelle Autonomie erreicht. So könnten analoge autonome Produkte oder Komponenten entwickelt werden, die in der Lage sind, sich zu verändern, ohne dass dafür ein computergestützter Antrieb erforderlich ist. 4D-gedruckte Komponenten, die ihre Gestalt verändern oder sich ohne Motoren, Drähte oder aktive Energiequellen bewegen, würden sich auf ähnliche Weise verhalten wie biologische Organismen – autonom. Die zukünftigen Anwendungsmöglichkeiten für solche Strukturen im Bauwesen, im Transportwesen, in der Textilindustrie, im Gesundheitswesen und in der Luft- und Raumfahrt sind immens.

3D-Druck: Grundlagen
Die additive Fertigung, wie der in den 1980er Jahren erfundene 3D-Druck auch genannt wird, unterscheidet sich von traditionellen Fertigungsverfahren, bei denen Teile gegossen, geformt oder gefräst werden. Hier wird das zu fertigende Objekt durch schichtweises Auftragen von Material in programmierter Form aufgebaut. Auch wenn er noch nicht überall gängige Praxis ist, findet der 3D-Druck z. B. in der Robotik, der Biomedizin sowie der Luft- und Raumfahrttechnik breite Anwendung, da er die Herstellung einzigartiger, massgeschneiderter 3D-Strukturen ermöglicht.
Heutzutage werden zunehmend mathematische Modellierungsverfahren und Algorithmen des maschinellen Lernens genutzt, um die Konstruktion und Materialentwicklung zu unterstützen und den Druckvorgang zu steuern. Im Jahr 2019 nutzte das niederländische Unternehmen MX3D den 3D-Druck, um den Arm eines ABB-Roboters strukturmechanisch anzupassen und zu optimieren. Dank eines speziellen 3D-Druckverfahrens (Wire Arc Additive Manufacturing, WAAM) konnten die komplexen organischen Geometrien aufrecht gedruckt werden.
Mithilfe intelligenter Algorithmen wurden die optimale Druckstrategie und die Orientierung des Werkzeugwegs für jedes geometrische Merkmal bestimmt. Hier konnten durch generative Gestaltung Zeit und Kosten gespart werden, indem die Produktivität erhöht und der Materialabfall reduziert wurde – wichtige Aspekte für die massgeschneiderte Roboterherstellung.
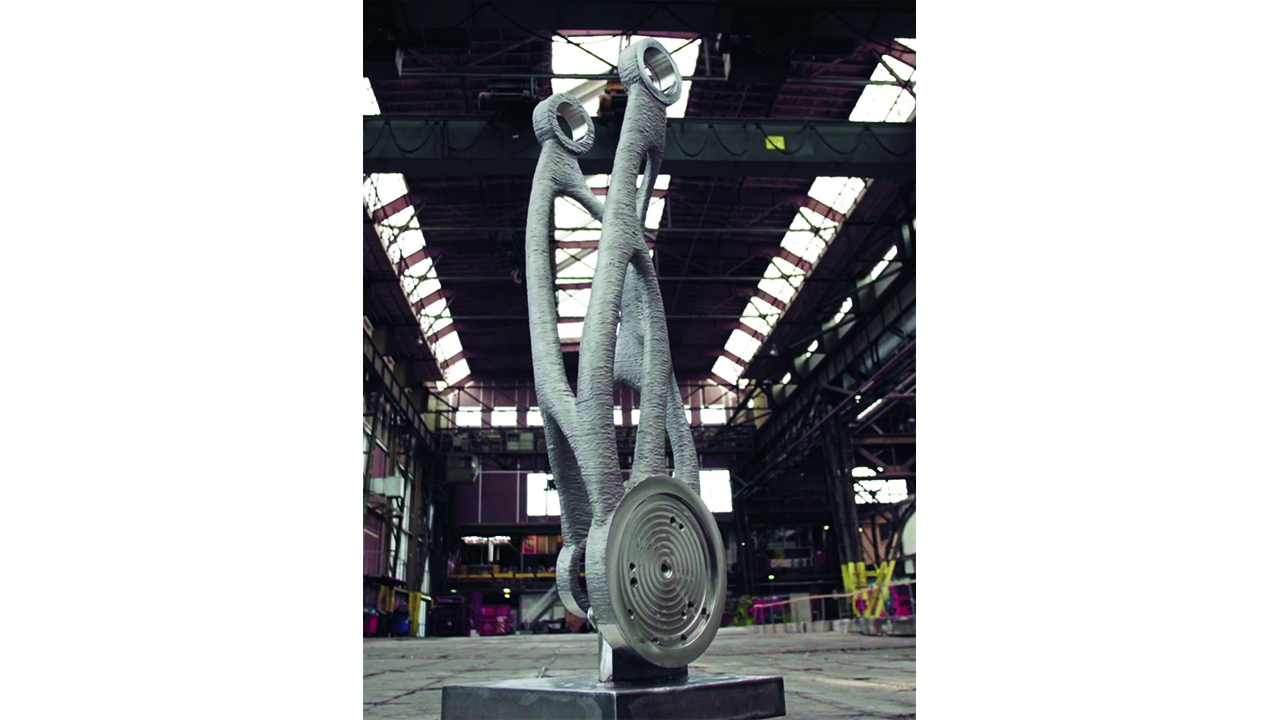
Auf dem Weg zum 4D-Druck
Die Entwicklung intelligenter Werkstoffe – Materialien mit funktionalen oder reaktiven Komponenten, deren Verhalten so berechnet ist, dass sie auf bestimmte externe Reize reagieren – und die Verfügbarkeit von 3D-Druckverfahren legten die Grundlagen für den 4D-Druck.
Der Begriff 4D-Druck wurde vom Architekten und Informatiker Skylar Tibbits im Jahr 2013 geprägt. Während sich viele Labore mit dieser Kombination befassten, gründeten Tibbits und seine Kollegen am Massachusetts Institute of Technology (MIT) im Jahr 2014 das Self-Assembly Lab. Im Mittelpunkt von Tibbits‘ Vision stehen drei grundlegende Funktionalitäten von 4D-gedruckten Objekten: Selbstmontage, Selbstanpassung und Selbstreparatur.
Selbstmontage: Wären Strukturen in der Lage, sich autonom, d. h. ohne menschliches Zutun oder die Hilfe eines elektromechanischen Systems, zu einer bestimmten Zeit und an einem bestimmten Ort selbst zusammenzufügen bzw. zu entfalten, könnte dies den Bau von Strukturen oder sogar Gebäuden an schwer erreichbaren oder gefährlichen Orten erleichtern. Antennen, die sich selbstständig im Weltall errichten, wären ebenso möglich wie winzige Objekte, die sich im menschlichen Körper zu medizinischen Zwecken selbst zusammenfügen.
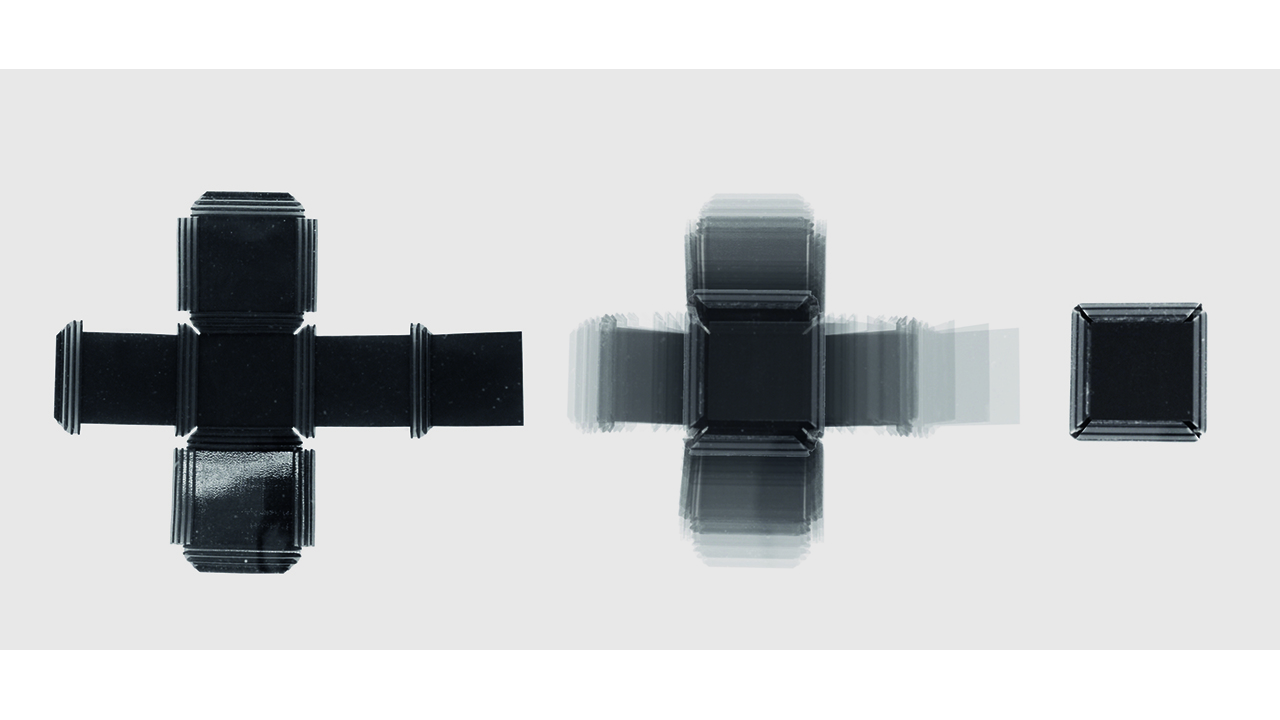
Selbstanpassung: Durch 4D-Druck lassen sich Sensorik- und Aktorikfunktionen in einer gedruckten Struktur kombinieren, wodurch elektromechanische Systeme überflüssig werden. Die daraus resultierende Reduzierung der Komponenten, Montagezeit, sowie des Material- und Energieeinsatzes führen wiederum zu Kosteneinsparungen. Eine mögliche Anwendung sind Baustoffe, die sich autonom an Witterungsbedingungen anpassen.
Selbstreparatur: Aus der Fähigkeit zur Selbstmontage folgt die Fähigkeit zur Demontage. Dies wiederum öffnet die Tür zum Konzept der Selbstheilung. Man stelle sich z. B. undichte Wasserleitungen in einem Krisengebiet vor, die sich ohne Erkennungs- und Lokalisierungssysteme oder menschlichen Eingriff selbst reparieren können – oder medizinisch implantiertes intelligentes Gewebe, das in der Lage ist, sich selbst zu heilen, ohne dass invasive Eingriffe notwendig sind.
Sich verändernde intelligente Strukturen
Ein erfolgreicher 4D-Druck erfordert ein geeignetes 3D-Druckverfahren, intelligente Werkstoffe, einen externen Reiz (z. B. Temperatur, Feuchte, Magnetfeld usw.), einen wohldefinierten Mechanismus der Interaktion zwischen dem Reiz und dem Werkstoff (z. B. Formänderung durch Wasseraufnahme) und die Anwendung mathematischer Modellierungsverfahren zur Bestimmung der Materialverteilung und Funktionalität sowie zur späteren Vorhersage und Programmierung der Bewegung. Auf diese Weise wird die gewünschte Veränderung in Form, Eigenschaft oder Funktion erreicht.
Um die gewünschte Formänderung und Struktur zu erreichen, müssen die intelligenten Werkstoffe in der Lage sein, sich nach dem Druck zu biegen, falten, verdrehen oder kräuseln. So kann z. B. durch Selbstfaltung aus einer flächigen Struktur eine kubische Form oder durch Verbiegung bzw. Kräuselung aus einer zweidimensionalen Form beim Eintauchen in Wasser eine dreidimensionale Blume entstehen. Oder ein eindimensionaler Drahtstrang könnte sich selbst zu einem dreidimensionalen Drahtrahmen falten.
Reversible Formänderung
Heute sind komplexe sogenannte Formgedächtniswerkstoffe (Shape Memory Materials, SMMs) in der Lage, sich einen bestimmten Zustand zu „merken“. Um diesen Formgedächtniseffekt (Shape Memory Effect, SME) zu nutzen, sind mindestens zwei Programmierschritte erforderlich: Zunächst wird ein bestimmter Reiz aktiviert, woraufhin das 3D-gedruckte Objekt von seiner ursprünglichen Form in einen temporären Zustand übergeht. Diesen behält das Objekt bei, bis ein zweiter Reiz dafür sorgt, dass das Objekt in seine ursprüngliche Form zurückkehrt. Nachdem sie einmal verändert wurde, kann die Struktur – durch Programmierung oder ohne Programmierung – den temporären Zustand immer wieder herstellen. Es ist also ein reversibler Prozess.
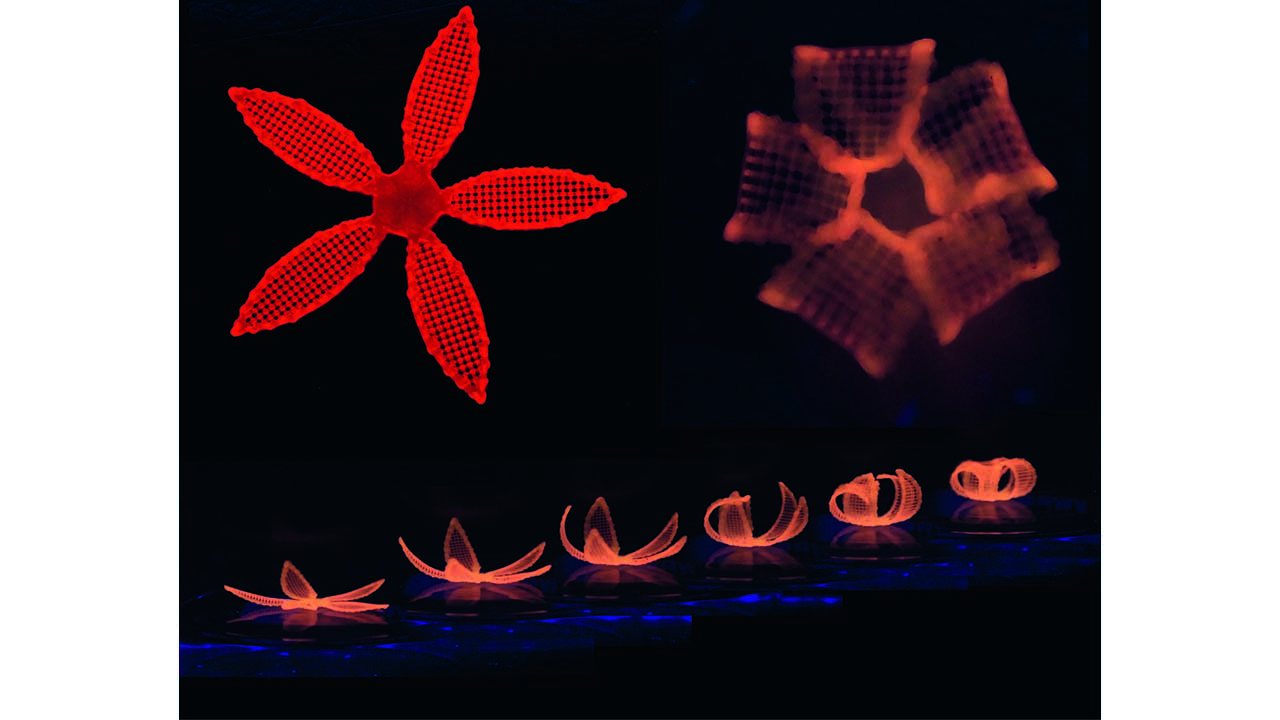
Die meisten für den 4D-Druck untersuchten SMMs basieren auf Hydrogelen oder flüssigkristallinen Elastomeren sowie verschiedenen Kombinationen dieser Stoffe. Diese hydrophilen Polymere können grosse Mengen Wasser aufnehmen, ohne sich aufzulösen, wobei synthetische Varianten aufgrund ihrer langen Lebensdauer und Gelfestigkeit bevorzugt werden. Flüssigkristalline Elastomere sind Polymernetzwerke, die eine vollständig reversible Formänderung mit grosser Amplitude durchlaufen können. Sie verbinden die Elastizität von Elastomeren mit der Fähigkeit zur Selbstorganisation und somit der Programmierbarkeit von Flüssigkristallen. Aufgrund dieser Eigenschaften sind diese Werkstoffe besonders im Bereich der Biomedizin, z. B. für künstliches Muskelgewebe und winzige Soft-Roboter, vielversprechend.
Aktuelle Forschung und Entwicklung Zurzeit verzeichnen neben dem MIT noch weitere führende Forschungseinrichtungen wie das Wyss Research Institute for Biomedical Research der Harvard University, die Rutgers University, die Eidgenössische Technische Hochschule (ETH) in Zürich sowie das California Institute of Technology (CIT) phänomenale Fortschritte auf dem Gebiet des 4D-Drucks.
Unter der Leitung von Jennifer Lewis befassen sich Gruppen am Wyss Institute in Harvard mit der Möglichkeit, die Biologie mithilfe des 4D-Drucks nachzubilden. Dazu untersuchen die Forscher, wie Hydrogel seine Form und Gestalt unter der Einwirkung verschiedener chemischer Auslöser wie z. B. Wasser verändert. Als Tinte verwendet können mit dem Hydrogel Objekte gedruckt werden, die ihre Form ähnlich wie Blumen verändern. Viele Pflanzen verändern ihre Gewebemikrostrukturen und Zusammensetzungen in Abhängigkeit ihrer Umgebung. Um diesen organischen Prozess nachzubilden, entwickelte die Gruppe HydrogelVerbundstoffe mit Cellulosefibrillen, die auf ein kontrolliertes Aufquellen programmiert sind. Die daraus 3D-gedruckten blumenförmigen Objekte verändern ihre Form, wenn sie mit Wasser in Berührung kommen, und bilden so die Reaktion von Pflanzenorganen auf Feuchtigkeit, Temperatur oder andere Umwelteinflüsse nach.
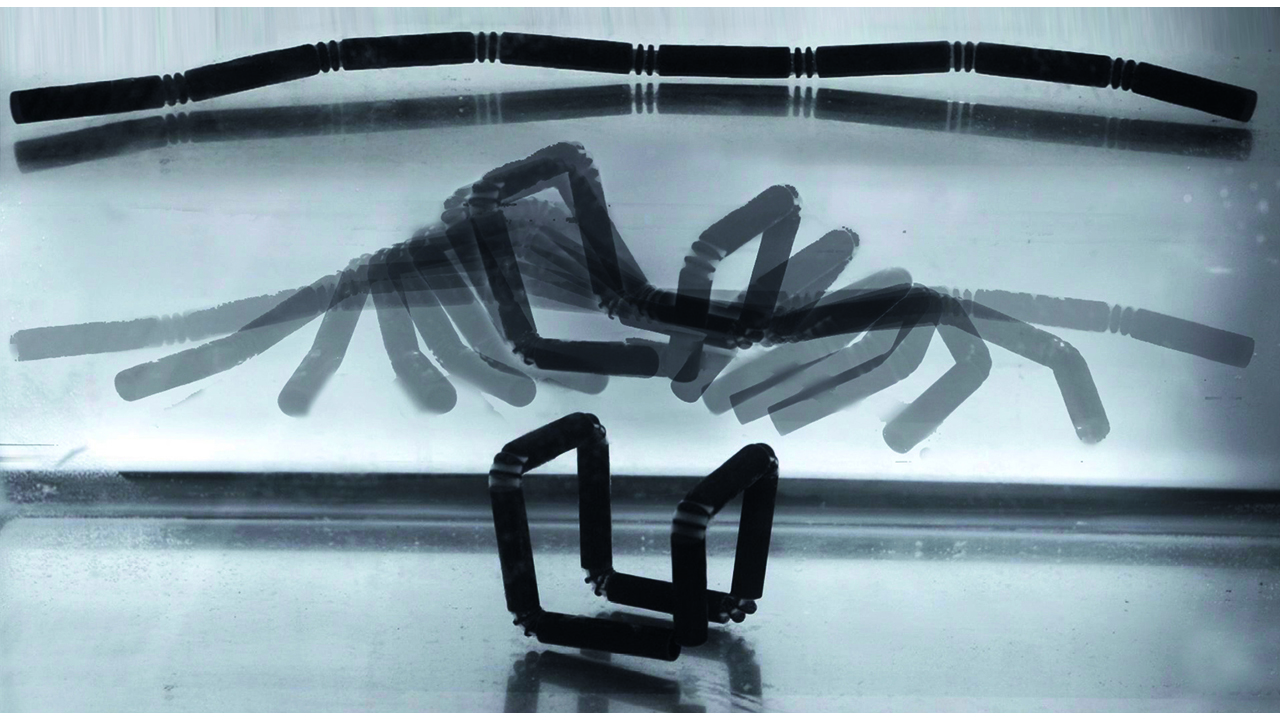
Andere Gruppen verwenden Hydrogele, die auf physikalische Auslöser, z. B. Temperatur, reagieren. An der Rutgers University haben Wissenschaftler mithilfe eines lithografiebasierten Verfahrens, der sogenannten Projection Micro-Stereolithography (PμSL), winzige dreidimensionale Objekte aus temperaturabhängigen, formverändernden Gelen gedruckt. Solche 4D-gedruckten Strukturen können z. B. zur Entwicklung von Dämpfungselementen für Soft-Roboter oder zur gezielten Medikamentenabgabe genutzt werden.
Im Jet Propulsion Laboratory der NASA am CIT befassen sich Forscher mit speziellen Metallgeweben, der sognannten „Weltraum-Panzerung“. Das wie ein Kettenhemd anmutende Gewebe besitzt vier bedeutende Eigenschaften: Es ist reflektiv, faltbar, zugfest und ermöglicht ein passives Wärmemanagement. Eine Seite des Gewebes reflektiert das Licht, während die andere Seite Licht absorbiert, womit es zur Temperaturbeeinflussung genutzt werden kann. Das Gewebe lässt sich auf verschiedene Weise falten und passt sich ohne negative Krafteinwirkungen verschiedenen Formen an. Die Fähigkeit, neue Funktionen in das Material hineinzuprogrammieren, eröffnet nahezu unendliche Möglichkeiten. So könnten diese Materialien eines Tages zum Bau grosser Antennen im Weltraum, zur Herstellung von Schutzanzügen für Astronauten oder als Schutzschild gegen Meteoriten genutzt werden.
An der ETH Zürich haben Kristina Shea und Tian Chen mithilfe eines Druckers vom Typ Stratasys Connex3 Objet500 Objekte aus Formgedächtnispolymeren, einem temperaturbeständigen, starren Kunststoff und einem elastomerartigen Material hergestellt. Die als flache 2D-Strukturen gedruckten Objekte entfalten sich in warmem Wasser zu tragfähigen 3D-Formen. Die Möglichkeit, die Tragfähigkeit mit der Zeit zu verändern, könnte besonders in den Bereichen Weltraumforschung, Architektur, Bauwesen und der Automobilindustrie interessant sein.
Herausforderungen und Einschränkungen
Trotz der Fortschritte auf dem Gebiet des 4D-Drucks gibt es noch bestimmte Herausforderungen und Einschränkungen zu bewältigen, bevor der 4D-Druck die Forschungslabore verlassen kann. Dazu gehören Aspekte wie physikalische Trägheit, Werkstoffe, Langlebigkeit, zusammenhängende Abhängigkeiten und Kosten. Zurzeit dauert es zwischen einigen Millisekunden und Sekunden, bis der Veränderungsprozess abgeschlossen ist, da grosse Moleküle bei der Neuanordnung bestimmte Distanzen zurücklegen müssen. Diese Zeitspanne kann je nach Anwendung angemessen, zu langsam oder zu schnell sein (für Baumaterialien wäre der Vorgang z. B. genau richtig).
Darüber hinaus setzen sich Werkstoffe, die auf äussere Reize reagieren, typischerweise aus einer begrenzten Auswahl von Polymeren zusammen, womit die möglichen Auslöser auf bestimmte Umgebungsbedingungen (z. B. Wärme, Druck, Chemikalien usw.) beschränkt sind. Um die Zuverlässigkeit und Langlebigkeit von intelligenten Werkstoffen zu verbessern, könnten Verbundstoffe eingesetzt werden, die metallische oder keramische Komponenten enthalten. Und da die strukturelle Veränderung und ihre Dauer von mehreren Faktoren abhängen, können unterschiedliche Umgebungsbedingungen zu unterschiedlichen Reaktionszeiten führen, was problematisch sein kann. Der 4D-Druck ist zurzeit zwar noch in kapitalkräftigen Nischen wie der Medizin, dem Militär und dem Luxusgüterbereich verankert, wird sich aber in Zukunft auch in Mainstream-Bereichen etablieren.
Die Zukunft ist 4D Auch wenn sich seine Nutzung momentan fast ausschliesslich auf die Forschung und Entwicklung beschränkt, ist zu erwarten, dass die vielversprechenden Vorteile dem 4D-Druck in den nächsten zehn Jahren erheblichen Antrieb verleihen werden. Das Gesundheitswesen, die Luft- und Raumfahrt sowie die Rüstungs- und Automobilindustrie beginnen bereits damit, die neuen Möglichkeiten zu nutzen.
Allerdings gibt es noch eine ganze Reihe von Produktdesignmöglichkeiten und zusätzlichen Funktionalitäten zu erforschen. So könnten z. B. Produkte mit integrierten 4D-gedruckten Verbindungen realisiert werden, die das Zerlegen vereinfachen und so die Wiederverwendung (bzw. das Recycling) von Komponenten fördern. Und wenn es darum geht, umfassendere Umweltanforderungen zu erfüllen, ist eine breitere Palette von geeigneten Werkstoffen und Verbundstoffen erforderlich. Ausserdem sollten weitere Anstrengungen unternommen werden, um die Stabilität von 4D-gedruckten Objekten zu verbessern und den 4D-Druckvorgang zu optimieren.
Trotz alledem sollten Unternehmen, die die Vorteile der digitalen Innovation für sich nutzen wollen, bedenken, welch beispielloses Potenzial der 4D-Druck – besonders als Mittel zur Entwicklung beweglicher autonomer Komponenten – bietet. Mit zunehmender Ausdehnung der vierten industriellen Revolution und fortschreitender Entwicklung intelligenter Werkstoffe gewinnen auch der 4D-Druck und die Robotik zunehmend an Dynamik, und ehe man sich versieht, können nicht nur massgeschneiderte Roboterarme zur Unterstützung industrieller Prozesse gedruckt werden, sondern Roboter könnten in der Lage sein, sich überall und jederzeit selbst zu optimieren, zu bauen und zu reparieren.•
Der Autor, Chau Hon Ho, arbeitet in den ABB Future Labs in Baden-Dättwil:
chau-hon.ho@ch.abb.com