Genom att införa ett ABB Ability™ digitalt system för spårning av malmbilarnas last har gruvbolaget Boliden ökat säkerheten, effektiviteten och lönsamheten vid sitt anrikningsverk i Bolidenområdet. Med hjälp av RFID-taggar i malmbilarna och vid de olika destinationerna längs vägen har man numera full kontroll över varje last.
Text: Christina Liljestrand Foto: Patrick Degerman
För nästan hundra år sedan hittades guld utanför Skellefteå i norra Västerbotten som blev startskottet till gruvjätten Bolidens verksamhet. I det lilla samhället med samma namn är anrikningsverket med sin lave i dag ett landmärke och det första steget i den komplicerade processen att utvinna koppar, zink, bly, silver och guld ur malmen. Varje år kommer ungefär 30 000 malmbilar hit för att sortera eller anrika sin last för vidare bearbetning.
Anrikningen i Boliden är emellertid mer komplicerad än i många andra gruvor:
– De flesta andra tar sin malm från ett och samma ställe, medan vi får last från fyra olika närbelägna gruvor, berättar Daniel Holmgren, som är tekniker på Boliden och har varit med och drivit projektet med digital lastspårning från början.
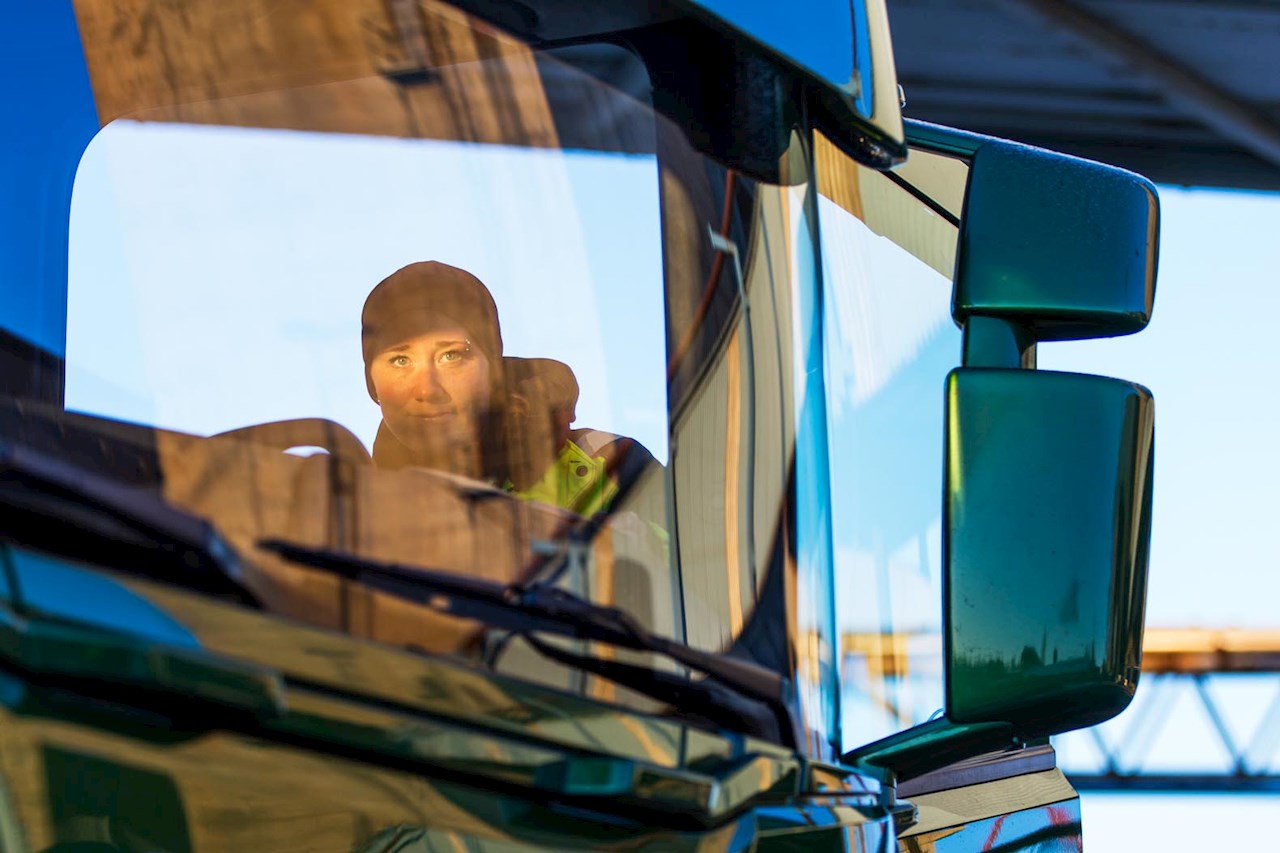
Det är stor skillnad på de olika malmtyperna och vissa får absolut inte blandas. Anrikningsanläggningens två linjer bearbetar därför bara en malmtyp i taget. Därför är det av största vikt att hålla reda på vilken last som tippas var.
Utanför kontorsbyggnaden ligger grindarna som leder in till verkets område. Genom dem styr lastbilsföraren Frida Ågren in sitt 72 ton tunga fordon. När hon för en dryg timme sedan passerade ut från Kristinebergsgruvan nio mil bort registrerade en sensor hennes lastbil och en order för lastspårning skapades direkt i Bolidens styrsystem. Alla gruvor i Bolidenområdet har försetts med RFID-läsare och alla lastbilar som transporterar malm från gruvan till anrikningsverket har försetts med unika RFID-taggar.
Frida Ågrens första anhalt på anrikningsverket är en av bilvågarna. Här dokumenteras hennes ankomst, och hon får sedan med hjälp av ABB Ability™ System 800xA en automatisk anvisning vart lasten skall tippas av. Platsen avgörs beroende på hur anrikningsprocessen körs vid tillfället.
När Frida Ågren sedan kommer fram till tippningsfacket krävs det att hon inväntar bekräftande grönt ljus innan hon tippar – skulle hon tippa mot rött stannar systemet.
– Det är ju ingen av oss lastbilschaufförer som vill tippa fel! intygar Frida Ågren. Men innan styrsystemet infördes och man hade kört samma sträcka 16–18 gånger, kunde det inträffa att man trots meddelande på radion missade att tippfickan var ändrad. Med det nya lastspårningssystemet där allt samverkar och varje kritisk händelse registreras automatiskt är det inga frågetecken någonstans, och risken att tippa fel blir betydligt mindre.
Enklare arbete via monitorer
I kontrollrummet sitter driftoperatören Anders Sinclair och övervakar hela processen. Han planerar arbetet via monitorer och hans arbete har också underlättats betydligt sedan systemet infördes.
– Här ser jag alla bilar som är på väg till anrikningsverket, visar Anders Sinclair på skärmen. Det är möjligt att spåra och analysera varje lastbil och alla turer den gjort. Systemet ser till att lasten hamnar rätt, och skulle det ändå råka bli fel får vi genast veta det och allting stannar.Förut märktes det bara ifall grov, okrossad malm hade täppt till en passage.
Anders Sinclair visar hur han kan stänga av hela systemet och sedan återställa och köra igång det igen. Han minns särskilt en gång när flera faktorer resulterade i att tonvis med stenbumlingar åkte in i systemet som inte stoppades förrän lasten transporterats hela 200 meter på bandet:
– Fyra man fick vara ute i sju-åtta timmar innan vi hade fått ordning på det igen! I dag skulle det inte kunna hända.
Säkerheten för människor, utrustning och processer är av yttersta vikt. Sedan det nya systemet infördes behöver de anställda sällan rycka ut på omfattande reparationsjobb, vilket gör arbetet idag mindre riskabelt.
Samordning av befintlig och ny teknik
Styrsystemet är särskilt anpassat för Bolidens verksamhet genom att samordna både befintlig och ny teknik. Johan Granström är affärsutvecklare på ABB och han vill framför allt belysa värdet med att använda ny teknik för att bättre integrera värdekedjan.
– Styrkan med att integrera en större del av värdekedjan med befintliga system, är att få en tydligare överblick och därmed kunna reglera sin process för att få så högt utbyte som möjligt. Tillgång till mer data skapar förutsättningar för nya insikter och bättre beslut.
Image currently unavailable
Image currently unavailable
Image currently unavailable
Image currently unavailable
Image currently unavailable
Image currently unavailable
Image currently unavailable
Image currently unavailable
Image currently unavailable
Image currently unavailable
Image currently unavailable
Image currently unavailable
Image currently unavailable
Image currently unavailable
Image currently unavailable
Image currently unavailable
Image currently unavailable
Image currently unavailable
Daniel Holmgren, tekniker på Boliden. Malmbilen lastas vid gruvan. Vid utpassage registreras bilen med hjälp av en RFID-läsare och en ny order skapas i systemet. Malmbilen anländer till anrikningsverket och ställer sig på bilvåg. Ny RFID-läsare registrerar bilen och kopplar vikten till en befintlig order och malmtyp, samt vilken gruva lasten kommer från. I kontrollrummet sitter driftoperatören Anders Sinclair och övervakar hela processen. Torbjörn Viklund, processchef på Boliden. Gruvbolaget Boliden har i dag drygt 5 600 anställda i flertalet länder.
Torbjörn Viklund, processchef på Boliden, understryker att kontrollen över feltippningar ger nya möjligheter att generera rapporter beroende på malmtyp.
– Systemet ger tillgång till rapporter som möjliggör ekonomisk och kvalitetsmässig redovisning för varje malmtyp, var för sig. Vi genomför dessa redovisningar varje månad och år. Och om vi vill utveckla systemet ytterligare är allt förberett för det.
Så går det till i Bolidenområdets gruvor:
- Malmbilen lastas vid gruvan. Vid utpassage registreras bilen med hjälp av en RFID-läsare och en ny order skapas i systemet.
- Malmbilen anländer till anrikningsverket och ställer sig på bilvåg. Ny RFID-läsare registrerar bilen och kopplar vikten till en befintlig order och malmtyp, samt vilken gruva lasten kommer från. Föraren får sedan en automatisk anvisning vart lasten skall tippas av. Platsen avgörs beroende på hur anrikningsprocessen körs vid tillfället.
- När föraren anländer till sin tipplats får hen grönt trafikljus om det är rätt tippställe, rött om det råkat köras till fel plats.
- Systemet registrerar även om bilen har tippat.
- Rapporter kan sedan genereras ur systemet för att identifiera vart och hur mycket material som finns, samt hur mycket som eventuellt råkat tippa fel.
Boliden
Gruvbolaget Boliden har i dag drygt 5 600 anställda i flertalet länder. Boliden är i dag även den ledande aktören i Europa när det gäller produktion av koppar och nickel och globalt en av de största aktörerna för återvinning av elektronik och bly från batterier.