Die von ABB in Lenzburg produzierten Leistungshalbleiter und die daraus gefertigten Produkte zum Einsatz in leistungselektronischen Anwendungen durchlaufen gesamthaft hunderte Produktionsschritte; vom Einstoss der blanken Wafer bis zum fertigen Halbleitermodul. Ein Produktionsschritt im BiMOS-Backend-Bereich – einer der beiden hier gefertigten Leistungshalbleiter-Typen – war dabei sehr arbeitsintensiv und erwies sich bei hoher Auslastung immer wieder als Flaschenhals.
Auftakt 2013
«Im Jahr 2013 begannen wir zu analysieren, wie die Effizienz dieses Prozessschrittes erhöht werden könnte», erinnert sich David Hajas zurück, Program Manager für die BiMOS-Backend-Automatisierung. «Dabei stellten wir fest, dass viele nicht wertschöpfende Prozesse, wie etwa das Bereitstellen, das Be- und Entladen sowie der Transport der Materialien, einen beträchtlichen Teil des Arbeitsaufwandes ausmachen.»
Von der Idee zur digitalen Fabrik
Eine Lösung für automatisierte Zuführarbeiten von Material, die industrieweit zunehmend eingesetzt wird: fahrerlose Transportfahrzeuge, sogenannte «Automated Guided Vehicle» (AGV). «AGV sind prinzipiell fahrende Roboter, die so programmiert und automatisiert werden können, dass sie als Zulieferer für stationäre Roboter und Anlagen dienen», erklärt Hajas. «An der Stelle kam die Idee auf, die uns dann wirklich Richtung digitale Fabrik bringen sollte: Wenn dieser Bereich automatisiert werden kann, liesse sich das nicht im ganzen Backend-Bereich der BiMOS-Fertigung umsetzen?» ABB-intern konnte den ABB Geschäftsbereich Steuerungstechnologien in Dättwil mit dem Manufacturing Execution System (MES) die übergeordnete Steuerung realisieren. «Doch es gab keinen Generalunternehmer, der diese Gesamtlösung für uns umsetzen konnte», betont Hajas.
Über 50 Roboter
So entschied ABB Semiconductors, diese Rolle selbst zu übernehmen. Doch allein die erste Etappe des Genesis-Programms umfasst über 100 Projekte und Teilprojekte. 55 Roboter – davon 40 von ABB – und rund 30 neue Sonderanlagen sowie 100 bestehende Betriebsmittel sind in das Leitsystem zu integrieren. Eine der grössten Herausforderungen: Die Automatisierung in einer bestehenden Fertigungsstätte zu realisieren, ohne deren Betrieb übermässig einzuschränken.
Wertvoller Erfahrungsgewinn mit Pilotanlage
Mangels Erfahrung mit grossen Automatisierungsprojekten baute das neu geformte Team von ABB Semiconductors ab 2015 deswegen eine Demonstrationsanlage mit insgesamt sechs ABB-Robotern, AGVs sowie verschiedenen automatisierten Sonderanlagen auf. Mit ihr sollte die technische Machbarkeit in kleinem Stil dargelegt und weitere Konzepte aus den Erkenntnissen entwickelt werden. «Die Erfahrungen, die wir mit dieser Pilotinstallation und der Zusammenarbeit mit den einzelnen Partnern gesammelt haben, waren essenziell, um das Gesamtprojekt dann wirklich umsetzen zu können», erklärt Hajas.
Kontinuierlicher Datenaustausch mit dem MES von ABB
Das koordinierende Genesis-Team in Lenzburg ist bestrebt, möglichst viele Komponenten aus dem eigenen Konzern einzusetzen. «Daraus entsteht insgesamt eine wirklich digitale Fabrik», so Hajas. Sämtliche Anlagen und Roboter tauschen ständig Informationen mit dem übergeordneten ABB MES aus. Das Ergebnis: In einer Roboterzelle können viele verschiedene Produkte gleichzeitig bearbeitet werden.
Roboter rüsten Anlage selbst um
Die Roboter rüsten dabei die Anlagen selbst um. Die Umrüstprozesse und nicht-wertschöpfende Transportprozesse werden damit also vollständig automatisiert. Damit wird eine hoch agile Produktion geschaffen, die sich selbständig anpasst – je nachdem, was gerade produziert werden soll. Für den Materialtransport zwischen den Zellen sorgen AGVs, ebenfalls auf Anweisungen des MES hin. Im Kontrollraum kann eine Person eine komplette Fertigung überwachen und steuern. Die dafür notwendigen Daten werden durch die vertikale Integration dem MES geliefert.
Wichtige Schnittstellendefinition
«Die wichtigsten Aufgaben des Genesis-Teams bestanden im Erstellen des Gesamtkonzepts, der Spezifikation von Anlagen und Schnittstellen sowie im Schnittstellenmanagement zwischen den Anlagen. Die einwandfreie Kommunikation und Interaktion zwischen ihnen macht Industrie 4.0 wirklich aus», so Hajas.
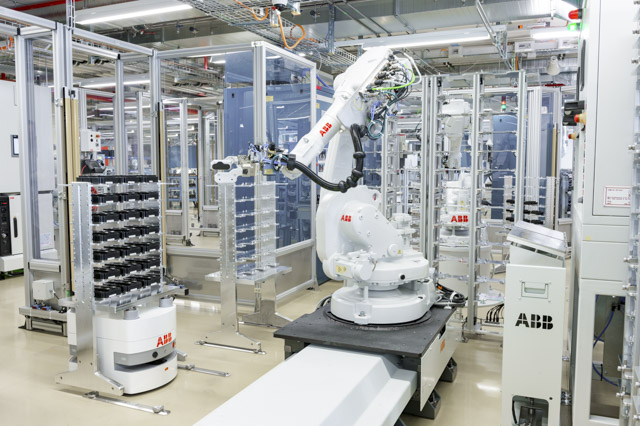
Erste Teilinbetriebnahme im November 2018
Im November 2018 wurde die erste Roboterzelle für das Testen von manchen Leistungshalbleiter-Modulen in Betrieb genommen. Die weiteren Zellen für das komplette Testing mit insgesamt zwanzig ABB-Robotern – darunter ein YuMi – sollen in den nächsten Monaten produktiv werden, bis Ende 2019 auch jene für die so genannte Substratfertigung, die am Anfang des BiMOS-Backend-Prozesses steht. Dann wird die erste Phase von Genesis abgeschlossen sein.
Danach wird ABB Semiconductors eine automatisierte Fertigung von einer Komplexität aufweisen, die ihresgleichen sucht. Und damit auch als Leuchtturmprojekt und Vorzeigefabrik dienen, die aufzeigt, was sich mit den Robotern und Ability-Lösungen von ABB realisieren lässt.
«Die Fabrik des Jahres 2018» – Auszeichnung für die Standortsicherung
Schon jetzt hat ABB Semiconductors im renommierten Industriewettbewerb «Die Fabrik des Jahres 2018» den Preis in der Kategorie «Standortsicherung durch Digitalisierung» gewonnen. Dies nicht für «Genesis» allein, sondern für die gesamte Digitalisierungsstrategie des Standorts.
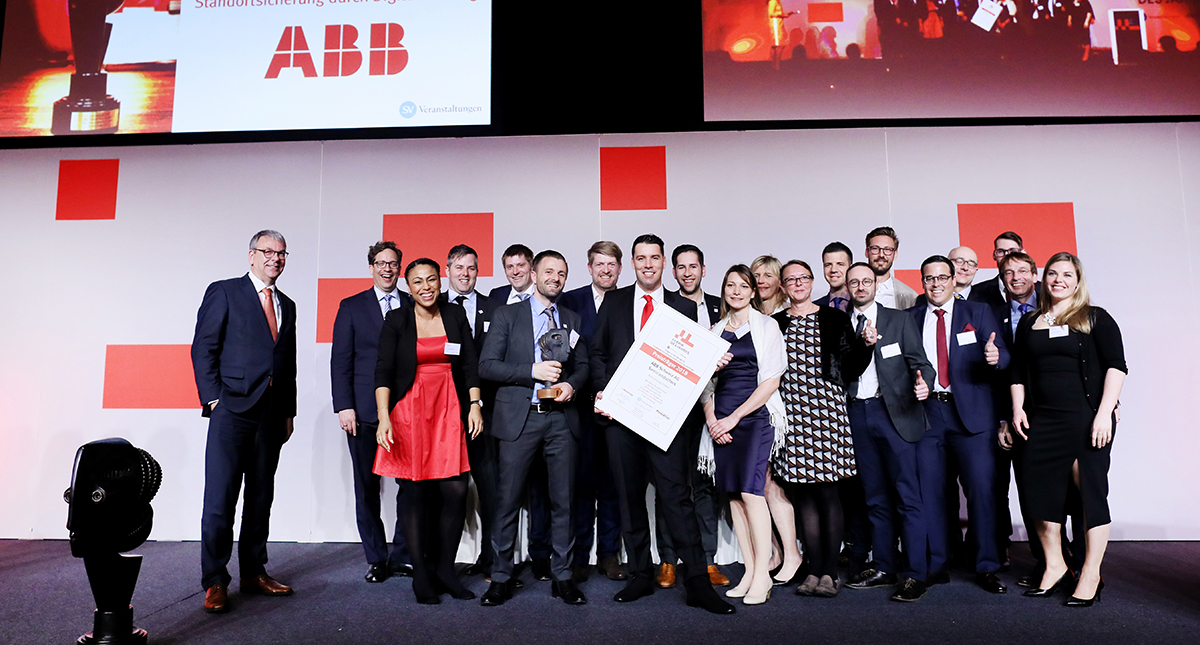
Über ABB Semiconductors:
Die Produktionsstätte für Leistungshalbleiter wurde 1981 in Lenzburg eröffnet. Es ist das globale Produktionszentrum des ABB-Konzerns. Ab 2008 ist ABB Semiconductors in Lenzburg umfassend erweitert und erneuert worden. In Lenzburg werden zwei verschiedene Leistungshalbleitertypen gefertigt: stromgesteuerte BiPolar-Halbleiter sowie spannungsgesteuerte BiMOS-Leistungshalbleiter. Bei beiden wird der Frontend-Prozess der Produktion der Leistungshalbleiter selbst vom Backend-Prozess unterschieden, in dem diese Halbleiter in Module eingesetzt und getestet werden. Mit «Genesis» wird der Backend-Prozess der BiMOS-Fertigung automatisiert.