Sweden’s ForSea is the largest high-frequency RoPax ferry line in the world utilizing electric power to gain major emissions reductions and other environmental and operational benefits. Henrik Fald Hansen, Senior Chief Engineer on the Tycho Brahe and Christian Andersson, Senior Chief Engineer on the Aurora, describe the core business considerations behind the switch to battery propulsion, excellent collaboration with technical solution provider ABB Marine & Ports, and how the ships have been making a big splash in the market.
The Tycho Brahe and Aurora, originally built in 1991 and 1992, respectively, are a familiar sight on the four-kilometer-wide Øresund Channel separating Denmark and Sweden, serving as a ‘floating bridge’ between Helsingør and Helsinborg. Each perform close to 46 trips daily carrying more than seven million passengers and 1.9 million vehicles every year. “The ships sail mainly manually and no trip is the same in the heavily trafficked waterway, in fair weather and foul,” says Fald Hansen.
Relying on the technology expertise of ABB Marine & Ports, the two sister ships underwent a comprehensive rebuild and conversion from marine diesel to electric power four years ago. The scope of the work included the installation of 4,160 kWh battery packs, ABB’s award-winning Onboard DC Grid™ power distribution system, as well as energy storage control systems and a state-of-the-art shore-side charging solution. The vessels were officially inaugurated in November 2018.
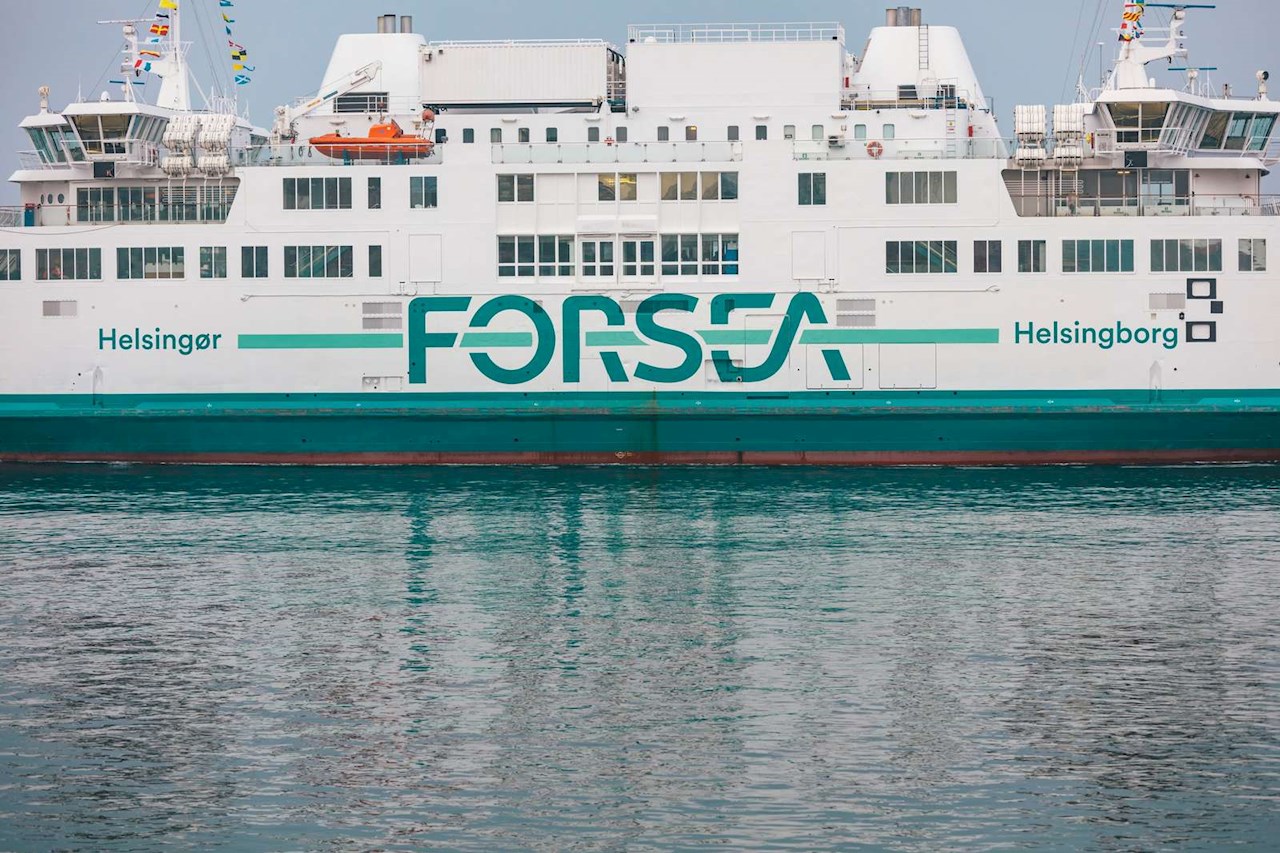
Main motivators driving electrification
Fald Hansen explains that back in 2015 when ForSea first considered electrifying the ferries, the main economic driver behind their investment decision was to find savings at a time of soaring fuel prices. At same time, the company wanted to promote green values, reducing emissions above and beyond national climate goals.
“We have worked for years on sustainability improvements, switching to low-sulphur marine diesel oil (MDO) and installing catalytic cleaning on all our vessels in 2006, which was always a red line for us as we sail in and out of city centres. The municipalities certainly encouraged us to become more climate-friendly, but it hasn’t been regulations driving us; we have led the way. We installed the catalytic converters voluntarily at very little cost as we were able to negotiate lower harbor taxes. As we are a very visible transport link in the Øresund region, with many people commuting every day to Denmark, the improvements boosted our positive perception among the public.”
We have worked for years on sustainability improvements.
Another important consideration was ensuring the local grid power provider would be able to supply energy and collaborate on the necessary infrastructure on shore. Only green renewable energy (with the highest classification) is used for charging the ships’ batteries.
Benefits for shipowner, passengers, local citizens, and sea life
Since the vessels began battery-powered operations, ForSea has achieved a CO2 reduction of over 37,000 tons, equal to total emissions by all four ferries on the route during one year of diesel operation. Following the Tycho Brahe upgrade (see below), in full electric mode both that vessel and the Aurora are expected to reduce CO2 by 65 percent compared to the base year of 2016, and very close to the 70 percent target set by the Danish Government, to be completed by 2030.
Tuna had disappeared from this area for the last 40 years, but they seem to be back since last year.
Electrical power substantially reduces noise and vibrations, benefiting passengers, local citizens and sea life. Recent studies indicate that fish stocks in the local area are rising, notably cod and tuna. “Tuna had disappeared from this area for the last 40 years, but they seem to be back since last year. Now there are even local operators doing tuna safaris. Historically the area around Gileleje was big in fishing so we hope we can contribute to a better future for local communities. Air pollution has also been reduced in Helsingborg after we started with electric operations,” says Andersson.
On the operational level, electric sailing has massively improved the onboard working environment. “While previously we were used to a lot of decibels, now the engine rooms are quiet and more pleasant versus the mechanical past. Where we had separators, which required a lot of protective gear to clean because of the dirt and cancer risk, now we only have filter units. Being a first mover and having all this data-driven high-tech equipment and the DC system is also really nice. It’s a different mindset and makes it much easier to recruit young men and women to work on our ships,” says Fald Hansen.
An additional unexpected benefit, according to one of the ship’s captains, was that replacing what would have been tonnes of marine diesel oil (MDO) in the bottom tanks with the addition of 200 tonnes of topside equipment has led to improved stability.
We hope we can contribute to a better future for local communities.
Shoreside innovation
The batteries onboard Tycho Brahe and Aurora are charged typically for a period of six to nine minutes on both sides of the channel, using four advanced charging robots mounted on mobile ‘sledges’. The robots pull into and connect to the vessels automatically using machine vision technology. Each approximately 20-minute one-way trip uses 20-25 percent of battery capacity, sailing at a speed of 10.5 knots to maintain schedule. Just Aurora has executed upwards of 50,000 connections, which no electric ferry in the world comes even close to. The success rate is more than 95 percent including weather-related issues and human-related faults/disconnections.
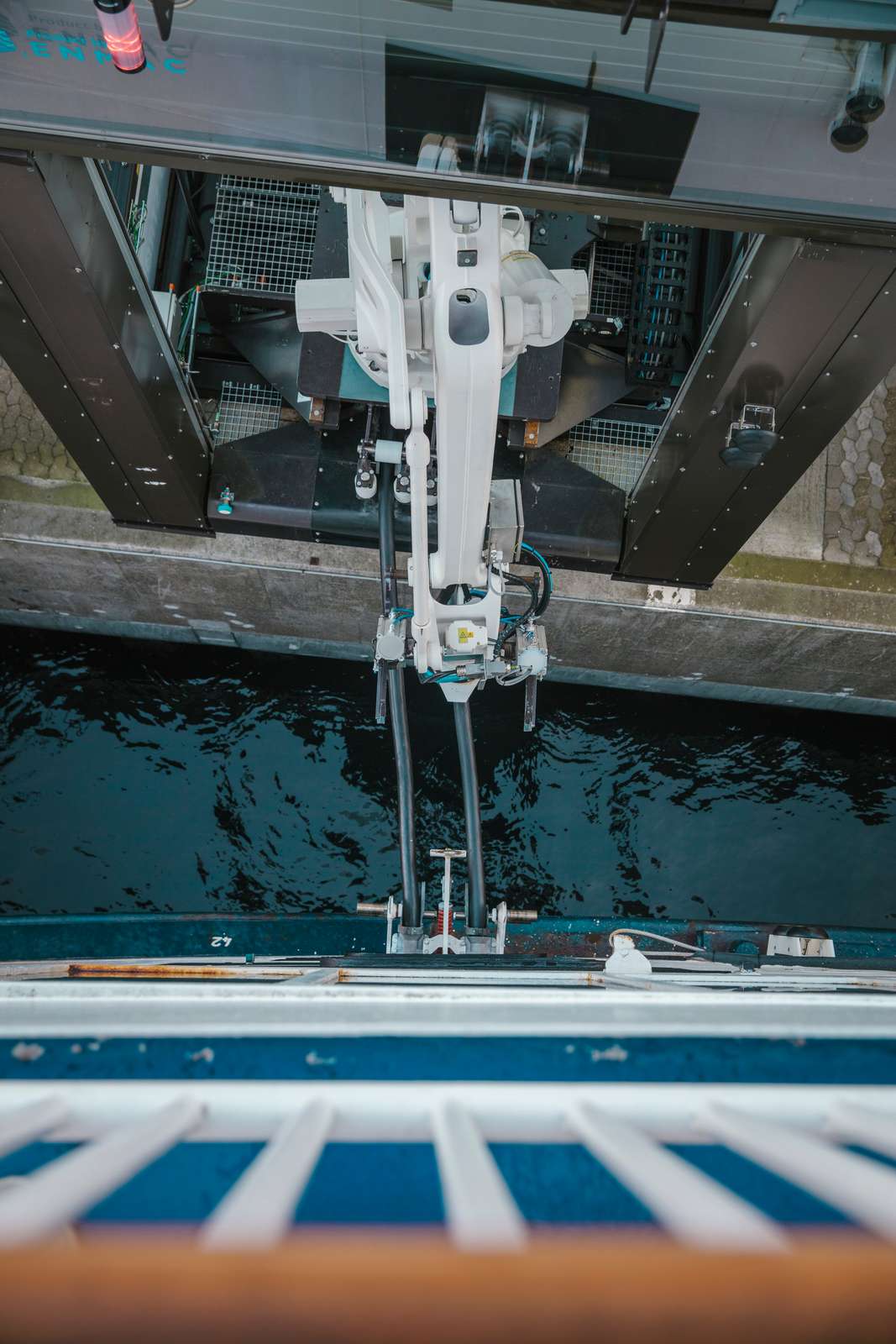
“It is ideal to charge the batteries to 83 percent of capacity. If something goes wrong with charging on one side, there is still enough energy to get back to the other side. For safety, the diesel motors will start automatically as soon as battery capacity falls below 30 percent,” adds Fald Hansen.

Tycho Brahe undergoes major upgrade
Due to various technical problems, it was decided in early 2021 to upgrade the Tycho Brahe with a new battery pack, increasing capacity by 50 percent from 4,160 kWh (4.16 MWh) to 6,400 kWh and doubling its lifetime from five to an expected 10 years. “Tycho Brahe was converted first so we learned many lessons from what was essentially a pilot project. Those learnings we brought forward to Aurora. The new system gained class approval from Lloyd’s Register (LR) in what was a truly collaborative endeavor. Class also learned a lot during the process,” says Sami Lehikoinen, Head of Marine Services at ABB Marine & Ports.
Housed on deck without wasting space inside the vessel, the battery pack is the largest with the highest capacity installed on any ferry worldwide. The complete energy storage solution comprises four ABB e-House containers, two housing the Corvus batteries and two housing electrical equipment, drives and cooling equipment. Although most heavy metal work was executed at Öresund DryDocks in Landskrona, a lot of follow-up work, including fastenings, was performed while the ferry was in operation to minimize disruption to ForSea’s high-frequency schedule.
The upgrade was a turnkey agreement with ABB. “That made their offering unique and was a big benefit. Having only one company to work with and one point of contact made it very easy for us,” says Fald Hansen. Tycho Brahe returned to full electrical sailing in October 2022.
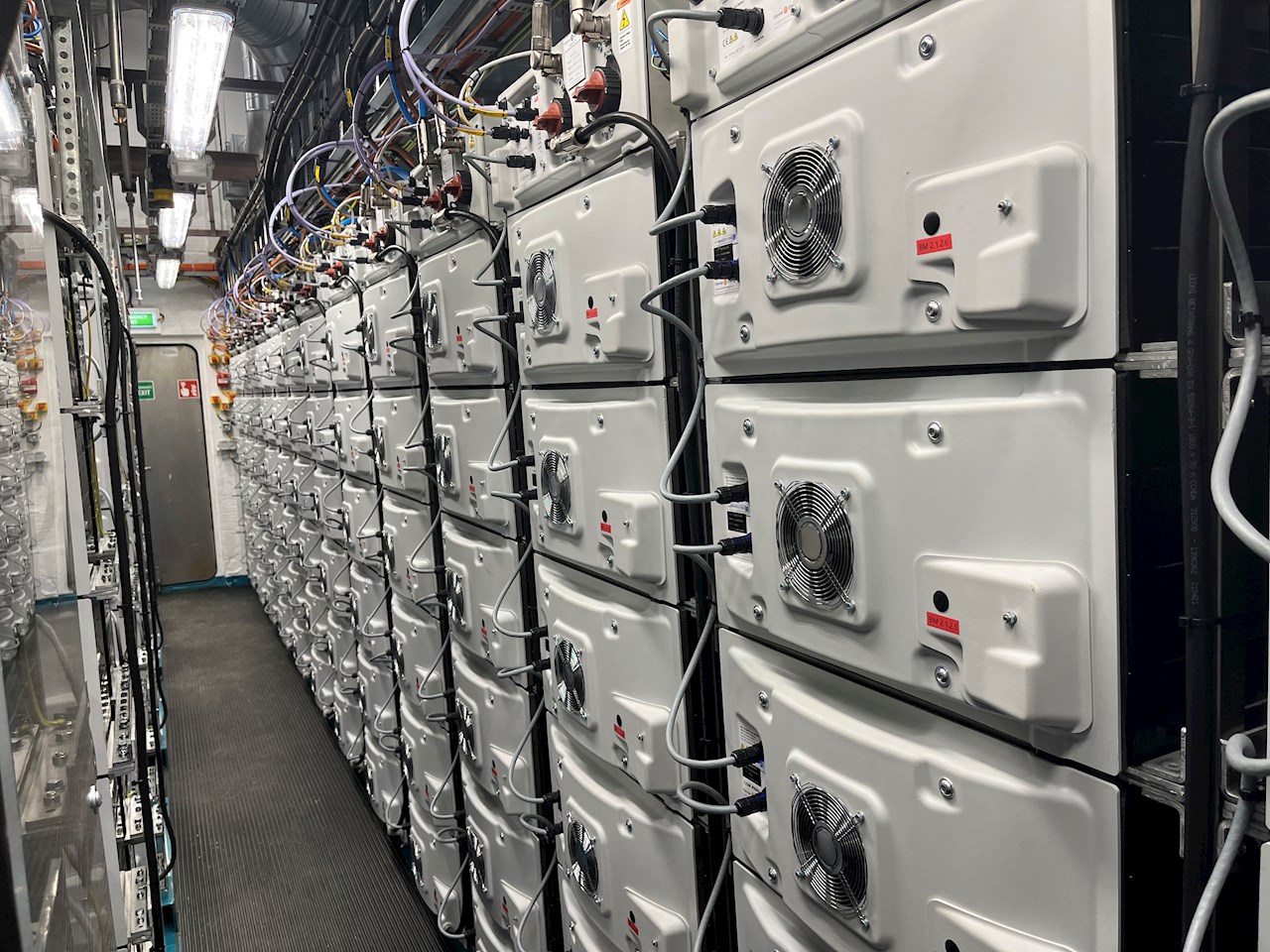
Collaboration is everything
Cooperating with ABB during the conversions and the upgrade was a “fantastic journey as a first-mover project," says Fald Hansen. “ABB supplied at a high level and we’ve met many skilled and inspiring people. The installation was very professional in terms of equipment, table works, drawings, cable markings, and all the other high-quality details. When we put the new system into operation it was really easy to use the electrical drawings to fix issues. We learned a lot with ABB from the start on how to operate with batteries, and also about collaborating with class societies. The risk assessment was excellent.”
Regarding the charging solution, Andersson says it is no secret there were some hiccups at the outset. “The main issue was with the charging tower connections. We started with a wireless link but that proved unstable and was replaced with a radio link. The scanner used to calculate movements of the vessels was first just 3D and it took a year to correct this using 3D laser machine vision instead. A particular challenge was coping with the angle of sun at certain times of day, which required extensive testing. Again, as a first mover we had to gradually learn the system’s DNA and how to maintain and improve it. It meant a lot of work for ABB and the crews understanding the issues and taking plenty of notes.”
“We learned from ForSea that they really appreciated our can-do attitude and that we were always there for them bringing our expertise to overcome challenges – large and small. Together we proved that, yes, this can be done. Many companies boast that they are planning these kinds of complex projects, but we actually did it,” says Lehikoinen.
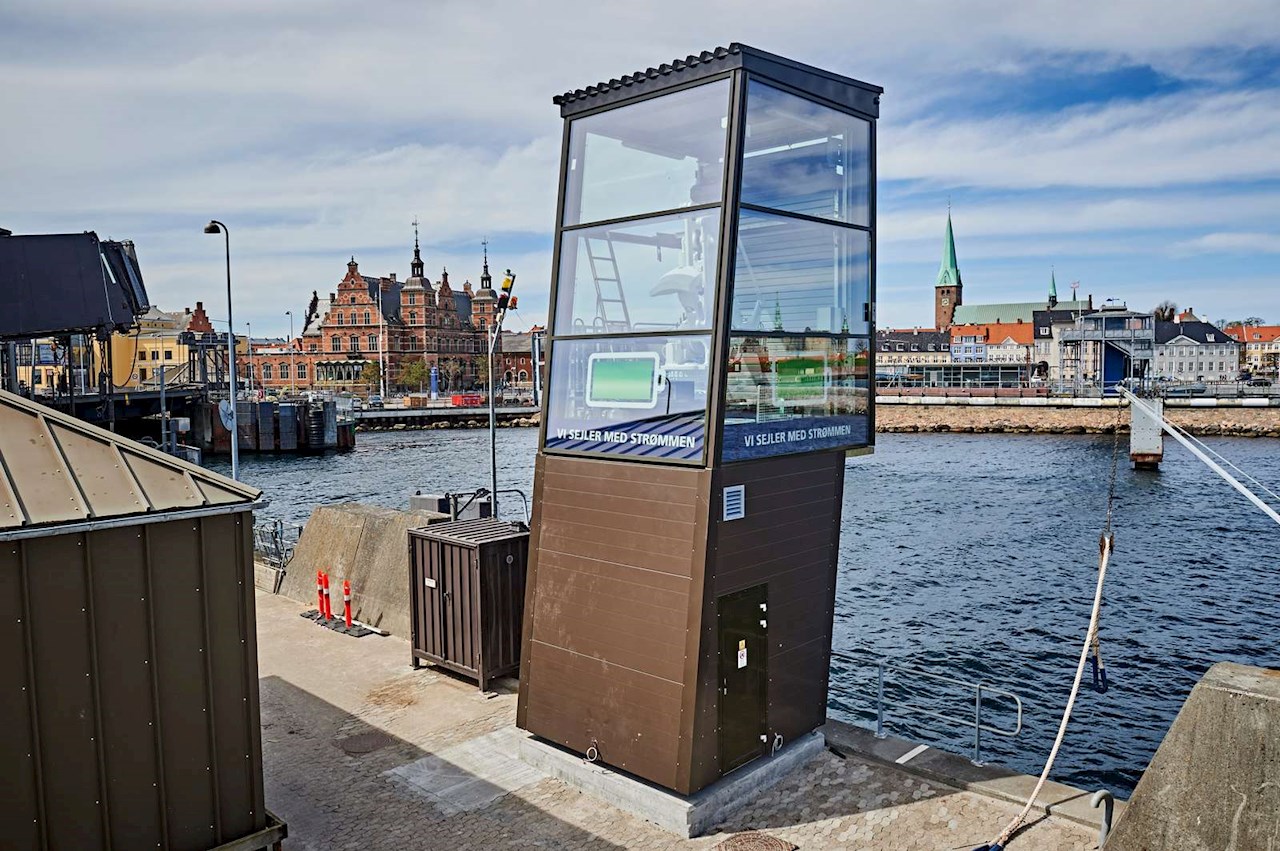
Positive feedback
Both Fald Hansen and Andersson stress the market reaction to electrification has been fantastic. “It’s been a great journey to be part of. We have had many US visitors from shipowners, ports and transport departments in New York, Washington and the West Coast, as well as delegations from Brussels, European countries, Singapore, Japan and even South America. Christian and I have shown around 4,000 people around the ships – there is so much curiosity,” says Andersson. “We certainly hope more shipowners will take the same course, especially in shortsea shipping. Our message is: Go for it. The world needs it.”

Andersson says port operators are especially interested in how ForSea handled the charging solution, given that many are facing logistics challenges as alternative new fuels including batteries, hydrogen, ammonia and methanol become available. “There’s also interest in how the charging system could be adapted for cruise ships,” he adds.
Our message is: Go for it. The world needs it.
Passengers on side
Many customers want to go down to the engine room, youngsters especially, to see for themselves how it all works. They are also keen on the possibility of charging electric vehicles onboard. ForSea is currently working on a pilot project that should be finalized by June. “We are already plugging in refrigerated trucks and now working on installing eight car charging points on each ship for a trial period. The biggest challenge is cable management,” Andersson says.
The plan is also to upgrade the battery pack on the Aurora in 2024 and to convert the sister vessel Hamlet to battery-electric operations by 2025. “Our realistic ambition is to be one of the most sustainable ferry companies in the world and by the end of this decade we should be running all our ships with zero CO2 emissions."
Both chief engineers say being a first mover is no easy ride, but a very rewarding one. “It took a lot of hands-on effort. Henrik and I have put four years of our lives into this, and we’re very proud to have achieved it. We have tremendously enjoyed the outcome!”
In September 2023 ForSea Ferries was rebranded as Øresundslinjen.