Ingo Mauritz ABB Process Automation Minden, Germany ingo.mauritz@de.abb.com
Since its introduction more than 40 years ago, the DCS has made enormous contributions to the safe, efficient and reliable operation of hundreds of thousands of industrial facilities. From the beginning, ABB has been a leader in the DCSs that drive large and critical operations in a wide range of settings, such as utilities, water, process industries, oil and chemicals, food and beverage, pharmaceuticals, marine and data centers. Today, safety, efficiency and reliability remain foundational requirements, but current practitioners require greater and more agile innovation to respond to the increasingly demanding and dynamic landscape of process industries. How should ABB DCSs evolve over the next 40 years to accommodate these requirements →01?
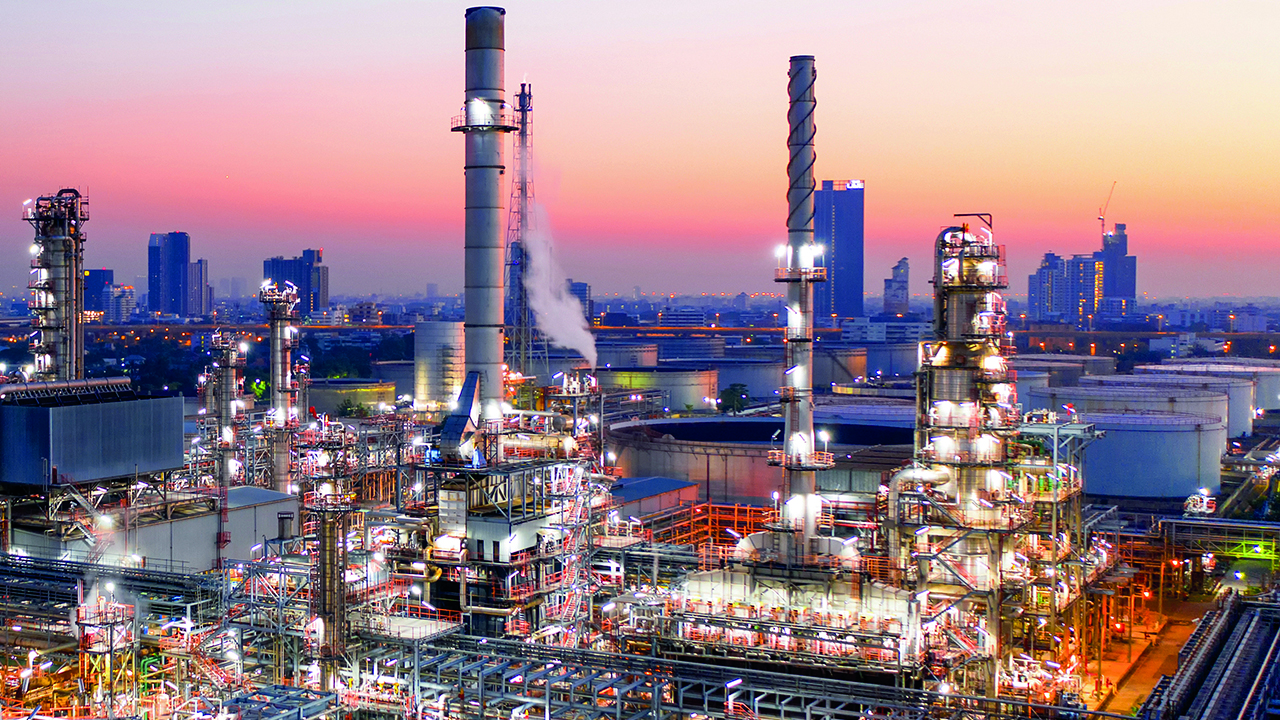
Future-proof, flexible architecture
ABB envisions that demands on future process automation systems will be reconciled through a process automation architecture that effectively enforces a differentiation between a robust evergreen core – where reliable, deterministic response is prioritized – and an extended, digitally enabled environment that performs tasks that are less time-critical while facilitating faster innovation and continuous performance improvements. Such an extended automation environment will enable secure connectivity with additional Industrial Internet of Things (IIoT) initiatives and allow for greater collaboration among people, systems and equipment →02.
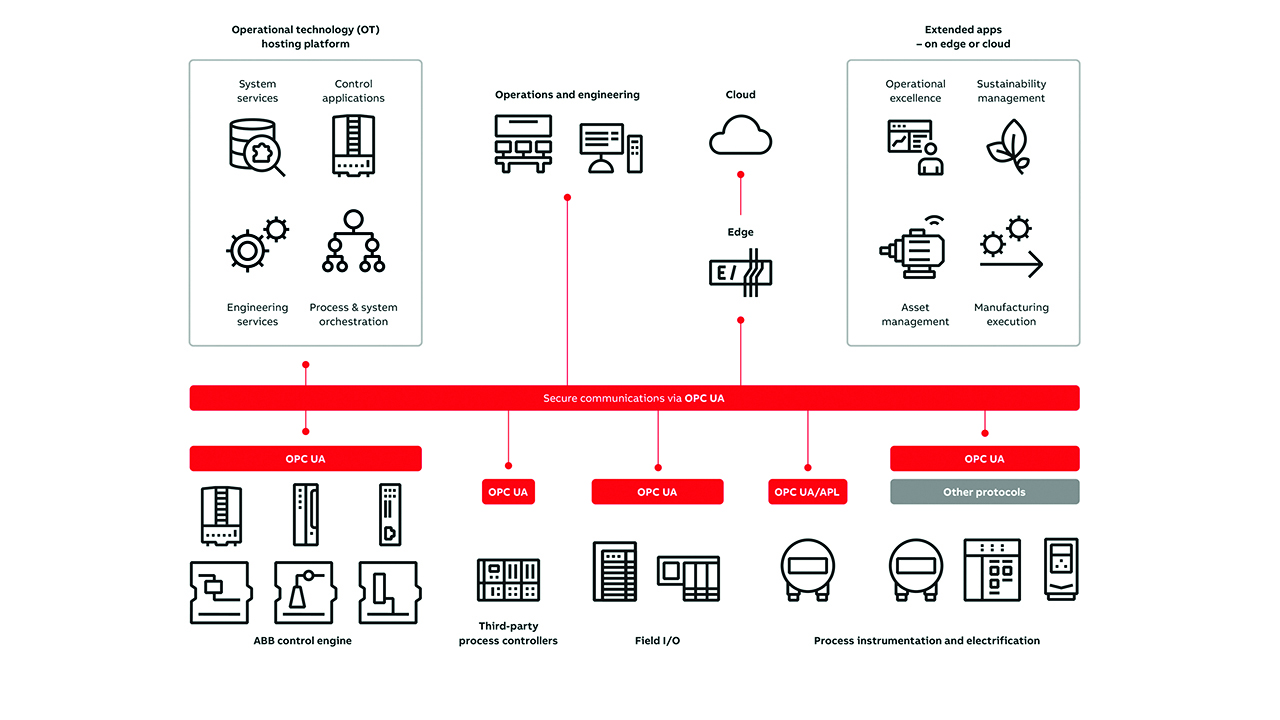
Consistent with the Open Process Automation Forum’s vision of independent software modules with defined communication interfaces, future process automation core and extended environments will be virtual, modular domains with cyber secure interfaces based on industry-standard OPC UA information models and communications [1]. These containerized modules will be automatically orchestrated in accordance with the performance and security expectations placed on them. This strategy moves enforcement of authentication and authorization from the network perimeter toward a zero-trust approach at the core, where components will be required to digitally prove their identity and originality, as well as their authorization for specific tasks, in order to properly deal with the evolving threat landscape [2].
Because process controller and application software will exist as containerized functional entities independent of hardware, they will be flexibly deployable and dynamically available across purpose-built and industrial PC controllers, edge devices, on-premise servers and cloud platforms.
The orchestration environment will automate load balancing among hardware resources and simplify control application allocation. Advanced applications will run adjacent to the control core and be easily modified without impacting operations by virtue of their containerization. Additionally, new functionalities will be tested and validated, via digital twin simulations online, prior to deployment.
Resilience will be assured by adjustable availability approaches designed to meet application needs, allowing users to optimize system availability with a cost-effective hardware footprint.
Orchestration automated, complexity hidden
The need for orchestration and management of modular, containerized control engines and applications represents a significant change for users of future process automation systems. IT departments might be accustomed to such tasks, but operation engineers are focused on running their processes, rather than managing the tools that control them. Hence, the need exists for automation of these activities.
Technology adoption with continuity
The future process automation system will be designed to enable current users to take advantage of new technology and solutions with minimal disruption to their existing setup. Protection of users’ intellectual property and their investment in applications means they can retain their infrastructure while adopting new technology at their pace and as needs dictate.
New portability approaches and a layer of technology independence between software and hardware will ease inter-platform application transfer and minimize hardware life cycle concerns, providing a lower-cost, lower-risk method for the graceful evolution of current systems, keeping future automation evergreen.
An architecture built to adapt
Strengthening the control system core also entails moving noncritical functionality that may be updated more frequently onto an outward-facing platform. ABB’s edge software is designed to provide this functionality, serving as a data-diode for secure core protection and providing a comprehensive application framework for monitoring and optimization. If edge capabilities are critical to core control functionality, the software can also be deployed as part of the core. The new process automation system environment delivers this flexibility.
Project execution and automation engineering transformed Project execution can be streamlined by decoupling hardware engineering and software development, as is accomplished, for instance, by ABB Adaptive Execution™. This tool allows project tasks to be performed in parallel by different teams, in different locations and even in virtualized cloud engineering environments →03. For example, engineers can perform virtual application testing and commissioning with a combination of virtualization, emulation and simulation technologies, all implemented in the cloud as a digital twin. The digital twin recreates process dynamics, probing performance against functional specifications. This virtual commissioning helps to identify potential issues, resulting in smoother and faster start-ups, and can proceed in parallel with other project tasks.
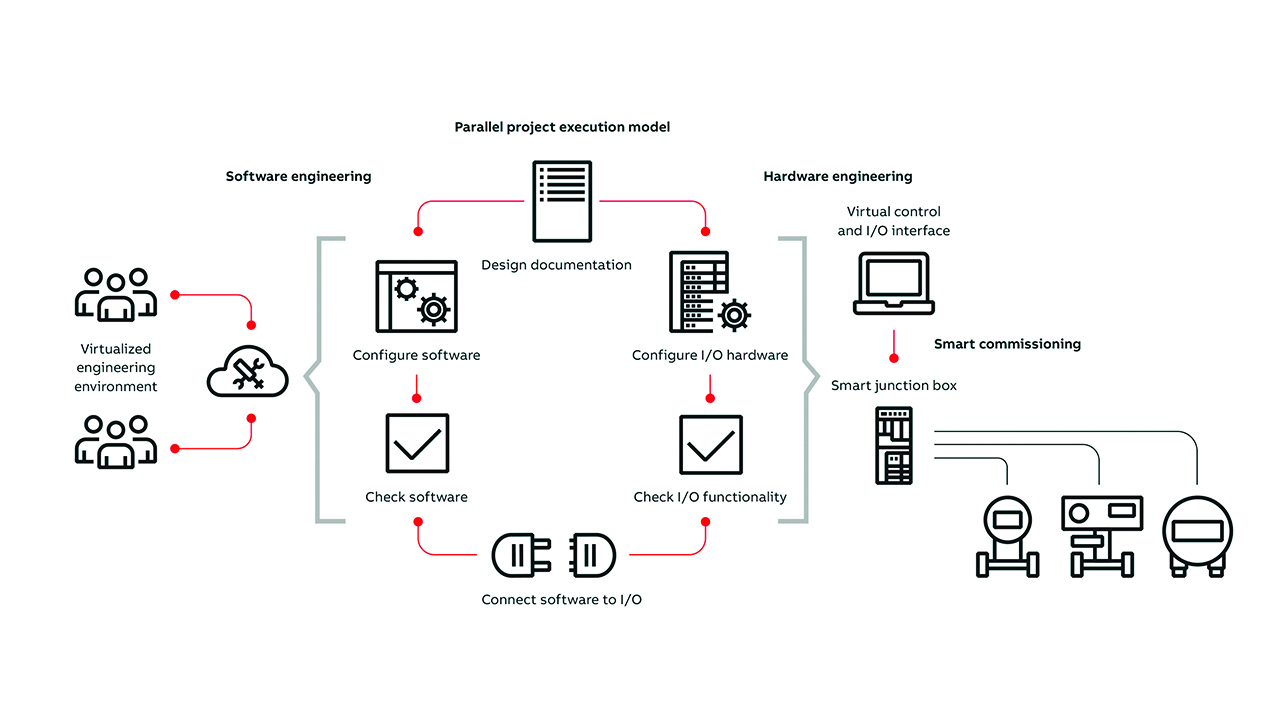
Libraries of modular, reusable code developed for particular types of processes or assets can further streamline project execution. Future process automation systems will use pre-made, pre-tested automation software modules that come complete with elements for control, visualization and associated services. Using well-defined communication interfaces for interaction with other modules will eliminate the need to develop “glue” logic to coordinate module behavior. Using pre-made modules also allows agile control strategy upgrades and process reconfiguration. Quality controls on pre-tested code will also help to ensure that the unit becomes operational quickly and without incident.
Overall process orchestration of the software modules will be facilitated by the automation system, elevating the control engineer’s tasks from programming control logic to configuring process-specific automation requirements. When designing a process unit for which a pre-tested module cannot be readily repurposed, automated engineering methods will shorten the distance between offline engineering tools and the direct development of code in the process automation system of the future.
A digital ecosystem that fuels the IIoT
Among the functions of the extended, digitally enabled environment envisioned in future process automation systems is secure, simplified integration with other essential elements on the edge, on-premise or in the cloud. Such integration will provide users with safe, secure, application-level access to core control OT data – as well as data from other IIoT devices, applications and business structures – without disturbing core control operations →04.
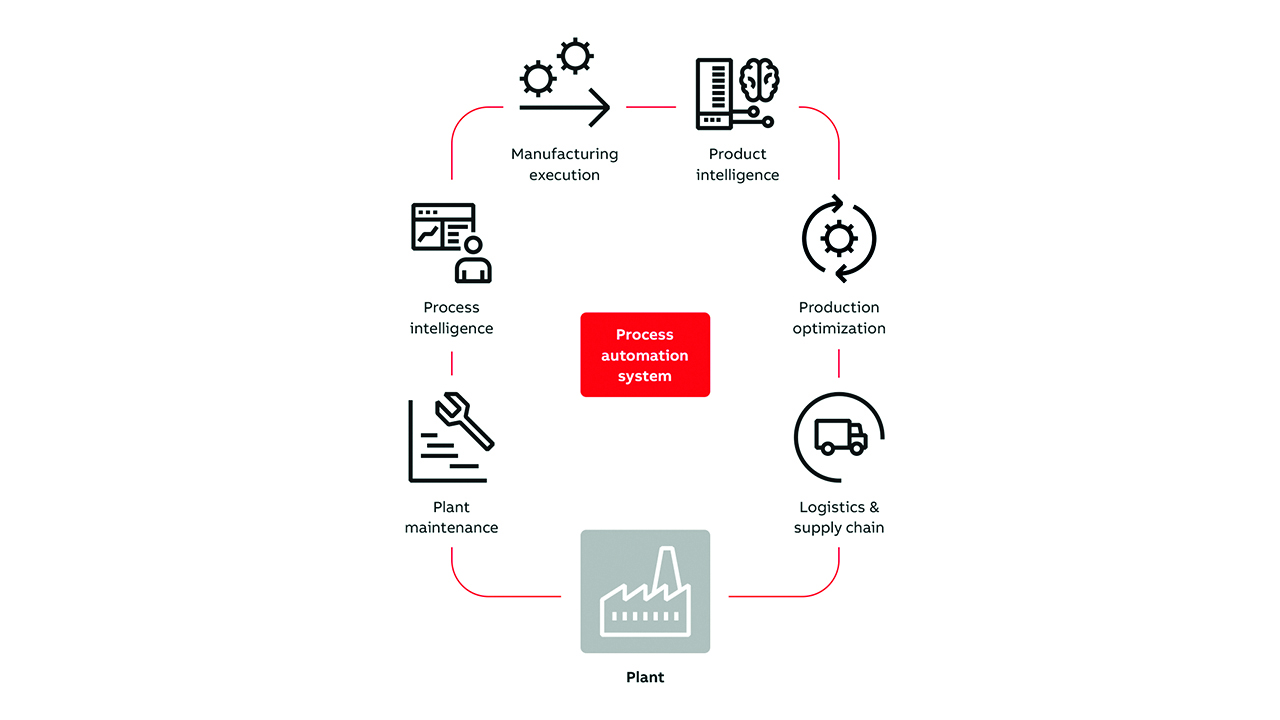
The digital ecosystem will be built on emerging edge and cloud technologies. These technologies change the automation landscape by providing a flexible and secure computing infrastructure, including servers, data storage, development environments, business intelligence services, artificial intelligence (AI) and data analytics for improving risk management, optimizing productivity and achieving sustainability targets.
Optimization with data analytics
Data is at the heart of optimization at a process, plant or enterprise level. The challenge resides in collecting and combining the data from different sources, contextualizing it, transforming it into knowledgeable insights and delivering it to the appropriate persons for timely action.
Here, flexible, edge-oriented solutions will predict issues and prescribe actions for better asset operations, superior predictive maintenance strategies and improved tuning of production processes.
Opening the door to new business models Digitalization will bring about a new range of business models and services because, with the digital ecosystem separated from the critical core, extended applications can follow a separate software purchase process, allowing a much quicker pace and opening the door to Software-as-a-Service (SaaS) or Platform-as-a-service (PaaS) business models. This evolution will shift spending from capital to operational budgets.
Changing roles and processes for a digital industrial workforce Along with the digital transformation of today’s DCS, the roles and duties of plant personnel are going through a transformation of their own. While the effect on future work processes is far-reaching, the duties of the control room operator are perhaps the most directly affected.
In future process automation systems, autonomous operations and industrial AI will revolutionize work, not necessarily by replacing humans, but by augmenting human cognitive capabilities to amplify their potential and assist decision making →05. Experts will be freed from mundane, repetitive tasks and can then focus on higher-value activities. Thus, people and autonomous systems will partner, with humans making the final decision.

In the field, sensor data collection and machine-learning algorithms will enhance operatives’ senses via augmented reality (AR) tools for more efficient maintenance and commissioning. For engineers, a host of innovations will remove the complexity associated with managing today’s integrated plant systems. These advances include self-configuring networks, evergreen operations, plug-and-produce insertion of new equipment modules and natively cyber secure components →06.
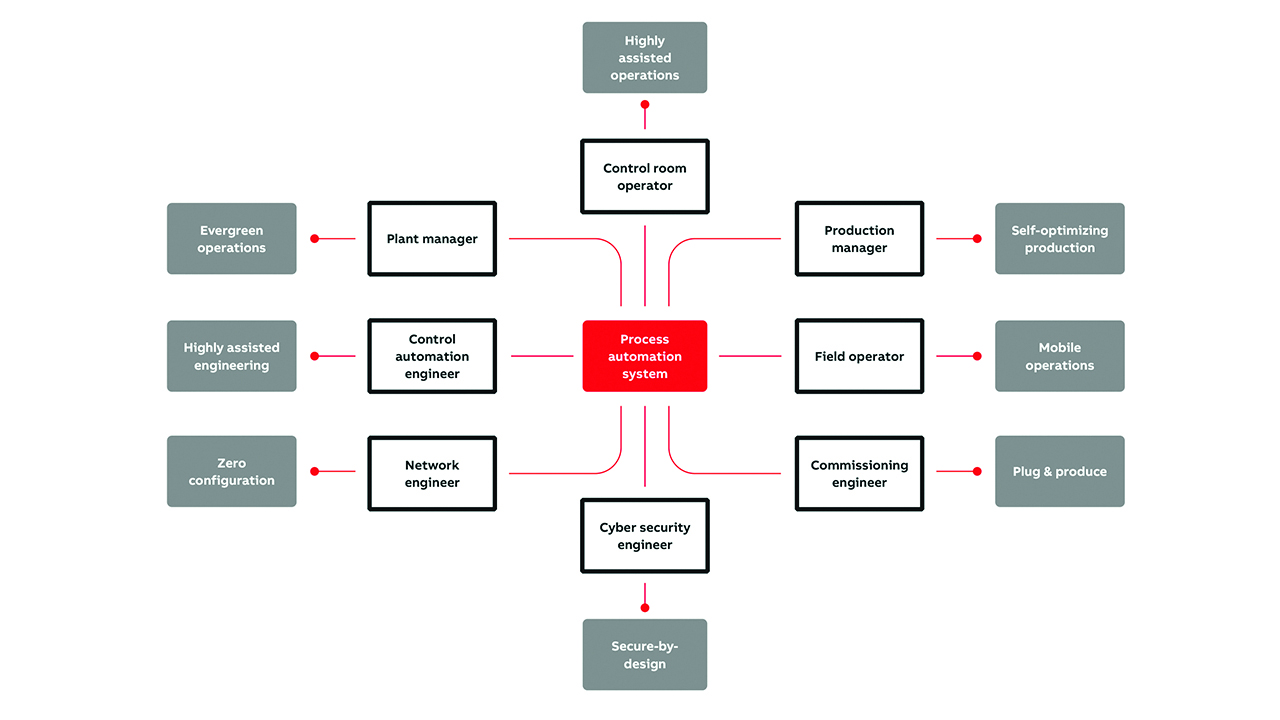
The journey ahead
The process automation system vision described in this article represents ABB’s guide to simplify and accelerate DCS innovation, with continuity, over the next few decades. ABB envisions that the process automation systems of the future will empower industries to compete in a fast-changing world by delivering adaptable, reliable, integrated, modular and secure automation solutions with flexible, simpler and faster project engineering execution and commissioning [2]. This vision will facilitate digital transformation and collaboration between people, systems and equipment through secure OT/IT integration for autonomous operations and sustainable performance, thereby ensuring the safety of people and the environment and the continued commercial success of the enterprises that embark on this journey.
References
[1] M. Kiener, “Buzzword demystifier: OPC UA,” ABB Review, 1/2023, pp. 80 – 81.
[2] ABB, “Envisioning future process automation systems: Enabling innovation while preserving continuity.” Available: https://new.abb.com/control-systems/control-systems/envisioning-the-future-of-process-automation-systems. [Accessed February 14, 2023.]
Photo fig. 01: ©Getty Gallery/stock.adobe.com