Mahesh J Vaze ABB Corporate Research, Process Automation, Bangalore, India, mahesh.vaze@in.abb.com; Subhashish Dasgupta ABB Corporate Research, Process Automation Bangalore, India, subhashish.dasgupta@in.abb.com
Multiphysics modeling is a globally sought-after methodology to simulate complex flow systems with high fidelity. This is possible due to the immense developmental strides that have been made in recent years with the ability of mathematical tools to capture complex flow patterns, heat transfer and gas dispersion. One important application that could benefit from multiphysics modeling is ventilation control of underground mines. With pollutant sources originating from diesel vehicle exhausts and blasting activity, mine ventilation control systems are hugely important for the health and safety of employees and for equipment safety →01. Air flow systems must deliver the quality and quantity of air when and where it is needed – a complex flow control process. Advanced strategies such as ventilation on demand (VOD) and optimization of ventilation, using algorithm control and digital twins, are already provided within ABB's state-of-the-art ventilation control for for the mining industry. However, ABB is ever ambitious to evaluate improvement potential and, if possible, take systems to the next level.
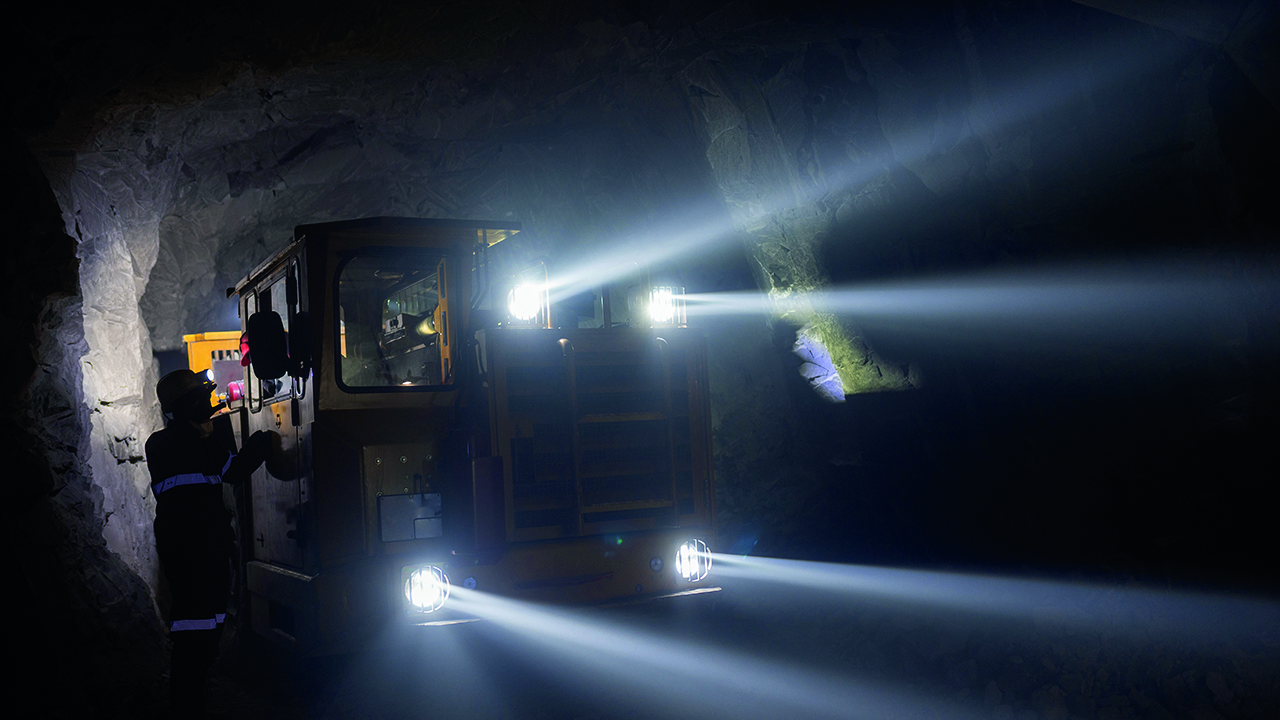
For this reason, ABB’s multiphysics experts investigated the possibility of leveraging multiphysics modeling, specifically computational fluid dynamics (CFD) modeling with species transport analysis to simulate gas dynamics within mines. The end goal is to improve ventilation control strategies so that customers will be able to reduce pollution levels better than ever, thereby ensuring the safety and health of personnel. Furthermore, because mine ventilation is an energy intensive process, both energy and financial savings could be increased.
Introducing ROMs: An implementable version of CFD models
CFD modeling with species transport analysis is a proven methodology used to simulate gas dispersion, as evident from research publications worldwide [1-2]. With the capability of providing a holistic view of the distribution of gases, eg, carbon dioxide and methane, as they vary with time, CFD models are by far the best means to provide insights into complex gas flow systems. Nevertheless, CFD modeling is time-consuming and challenging when it comes to platform integration. Consequently, ABB evaluated the feasibility of developing ROMs, which is a more simplified modeling process approach than CFD, in order to facilitate integration with control system platforms.
Not only does a ROM retain the essential features of a full-scale model and enable simulation of any given set of inputs to yield the output in an acceptable time, it offers further benefits:
• optimizes product design using several iterations in less time
• provides the opportunity to develop on-line physics-based digital twins
• allows low-or mid-level experts to use simulations.
And, because ROMs can be converted to front-end versions, in other words, to user-friendly and configurable versions, private and confidential data can be concealed from third party users. As a result of these advantages, ROMs can be used not only to lower computational resources and optimize design but can lower costs overall.
Building a ROM
As a first and essential procedural step to build a ROM, ABB developed an initial full-scale CFD model of the system. Numerous CFD simulations were performed on the same model setting, by varying input parameters and then recording the corresponding output results. Behind the scenes, a multi-dimensional curve fitting procedure, using machine-learning (ML) or neural-network (NN) algorithms, related the input parameters to the output results to yield the ROM. The ROM was then tested for accuracy and reliability, by using test cases, ie, comparing the model predictions for cases not simulated in the first step with predictions of the full-scale CFD model. These ROMs can be created and exported to other platforms in industry standard formats such as “.fmu” files.
02a Geometry of a tunnel. 02b Computational mesh. 02c CO₂ mass fraction over a tunnel. 02d CO₂ mass fraction over a plane.
02 The CFD modeling of vehicular pollution of an underground mine tunnel used for the simulations is shown.
Why develop a ROM for mine gas dynamics?
In this study, the primary source of mine pollution was considered to be vehicular exhaust. In this case, the ventilation duct forces fresh air through the mine tunnel in order to dilute the concentration of toxic gases such as CO₂, and to maintain the CO₂ level within the allowable legal limit. What if the CO₂ level could be realistically predicted under a given set of input parameters? Not only would such capability enable the efficacy of ventilation controls to be improved, it would, in turn, have a beneficial impact on the health and safety of employees as well as energy consumption.
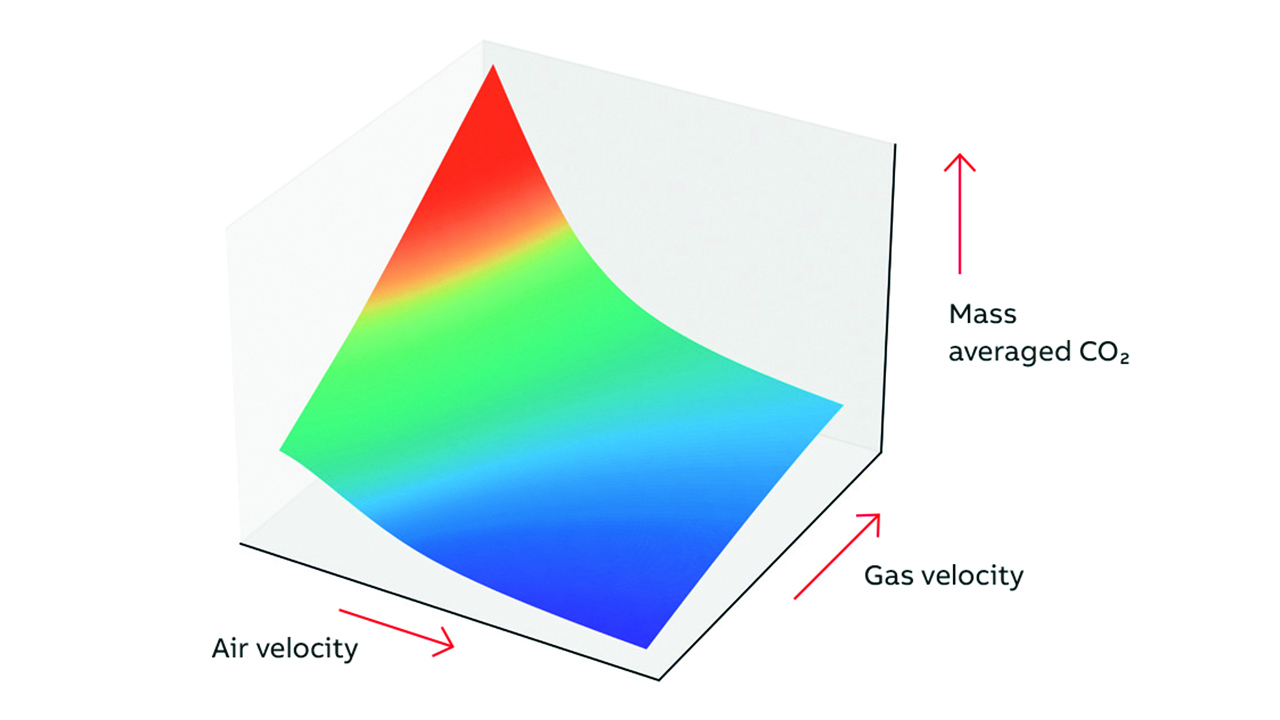
Testing the ROM: Does it work?
To investigate the possibility of using ROMs to make predictions, CFD modeling of vehicular pollution within underground mine tunnels was performed. The geometry and the computational mesh of an underground mine is as shown with the boundary conditions or model inputs given →02a-b. Here, the ventilation air velocity at the ventilation duct outlet and the exhaust gases emitted by the vehicle are considered to be the primary input parameters. The volume rendering of CO₂ mass fraction →02c shows the ventilation air ejects of the toxic gases away from the dead-end of the tunnel. The interesting results in this case are the mass averaged value of CO₂ over the entire underground mine volume, and the face-averaged value (entry, exit and mid-plane) of CO₂ for each of the three planes →02d. The ROM establishes the relationship between the output and input parameters for the given geometry and discretization scheme.
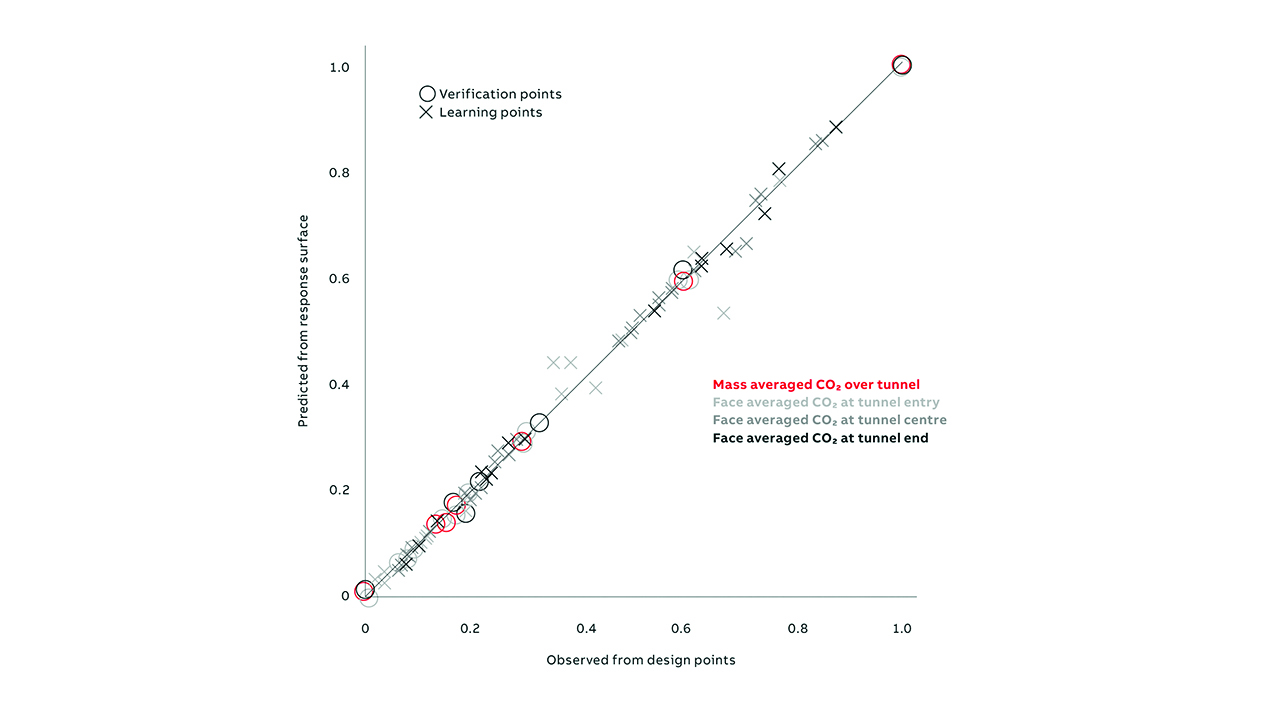
The design of experiments (DOE) for the ROM of gas dispersion within underground mine tunnel was established using the Optimal Space Filling Design (OSF) method. Initially, a few design points (DPs) or variations of input parameters are considered; these DPs are simulated using the CFD model. The input parameters are mapped to the output; this results in the generation of the ROM by means of the genetic algorithm method for solving constrained and unconstrained optimization problems. The output of the ROM is the response surface →03; this surface graphically depicts the relation of the primary output results; which in this case is the mass averaged carbon dioxide concentration within the tunnel volume and the input parameters, as well as the ventilation air and vehicle exhaust velocities. The accuracy and reliability of the ROM is verified using the goodness-of-fit procedure →04, which relates the predicted values from the response surface to the values from the design points obtained from the full-scale CFD model. With the ‘×’ symbols denoting the design points/learning points used to develop the ROM, and the circular symbols showing the additional verification or test points, it can be easily observed that all of the verification points follow the regression line, thereby ensuring the proper goodness-of-fit, required for validation →04. In this case, the Root Mean Square (RMS) error is only 1 × 10 –³, which is an acceptable error level.
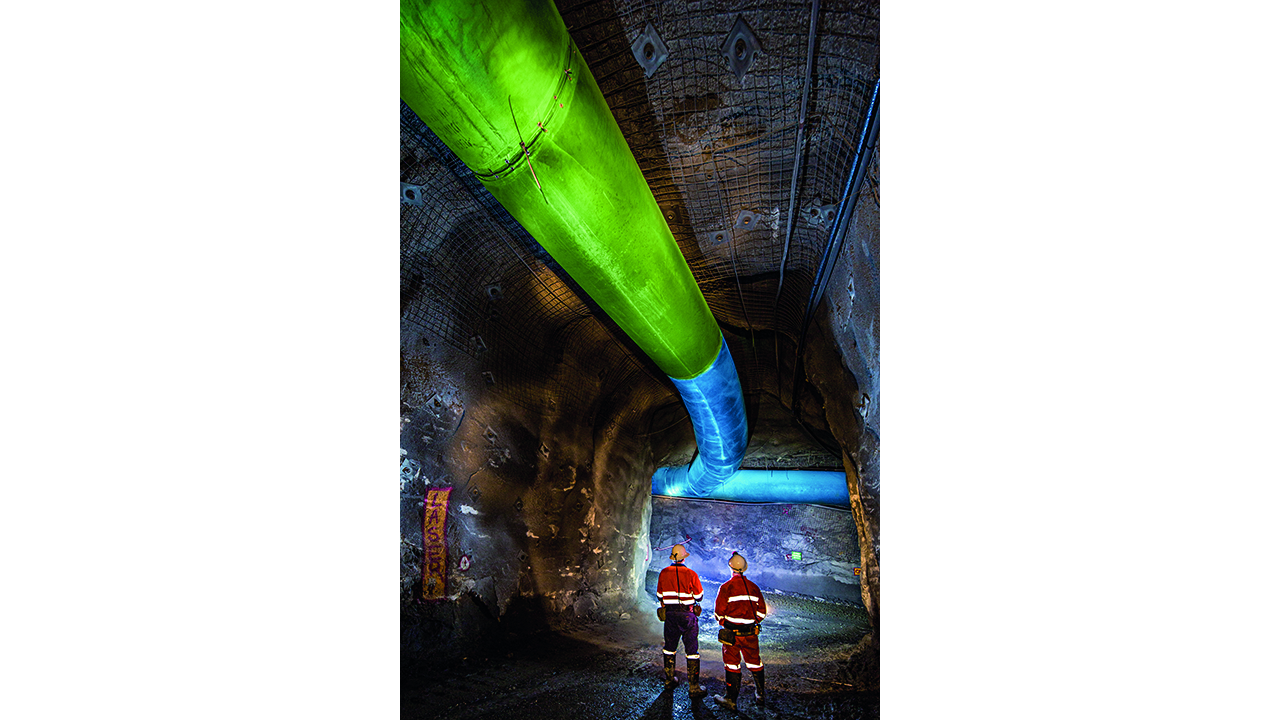
Platform integration is key
Based on these previously described experimental results, the response surface generated by the ROM, which relates exhaust gas concentration to the input parameters, can be an effective tool for the online control of mine pollution as long as the response surface can be integrated with ABB control platforms →05. This is the case since the ROM can be used to generate the “.dxrom” file, which can easily be accessed via Microsoft Excel →06 and in turn can be integrated into ABB’s currently available control platforms, such as VOD, and ABB Ability™ Ventilation Optimizer. Because three-dimensional high-end multiphysics calculations are the foundation of the ROM, leveraging the generated response surface would add a new dimension to the latest mine ventilation control technologies offered by ABB. Such a step would not only help customers to improve air quality, providing fresh air where and when it is needed, it would improve the health and safety of employees and coincidently save energy through optimization. This would translate to cost savings too.
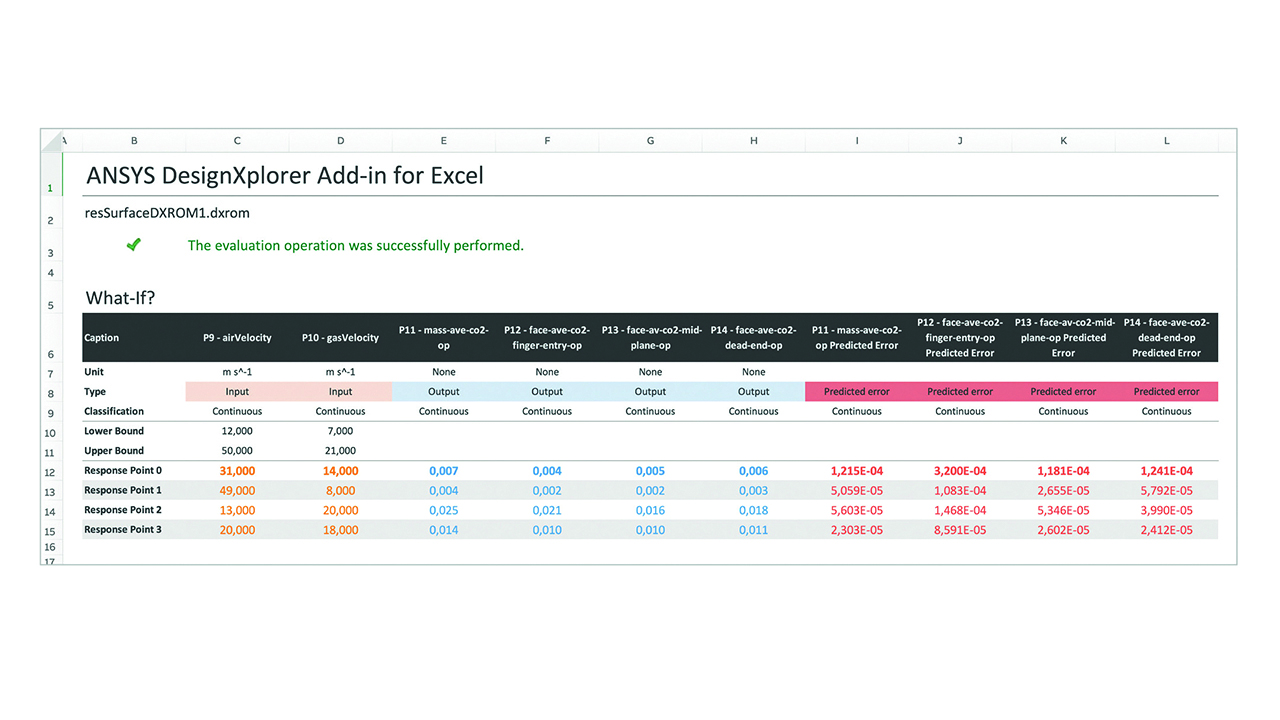
References
[1] J.C. Kurnia, “CFD simulation of methane dispersion and innovative methane management in underground mining faces”, Applied Mathematical Modeling, 2014, pp. 3467 – 3484.
[2] Z. Lihong, “CFD modeling of methane distribution at a continuous miner face with various curtain setback distances”, Journal of Mining Science and Technology, 2015, pp. 635 – 640.
Photo fig. 01: ©agnormark/stock.adobe.com
Photo fig. 05: ©Michael Evans/stock.adobe.com