Bruno Agostini, Daniele Torresin, Andrey Petrov ABB Corporate Research Baden, Switzerland, bruno.agostini@ch.abb.com, daniele.torresin@ch.abb.com, andrey.petrov@ch.abb.com; Jorma Manninen, Mika Silvennoinen, Joni Pakarinen ABB Motion, Drives Products Helsinki, Finland, jorma.manninen@fi.abb.com, mika.silvennoinen@fi.abb.com, joni.pakarinen@fi.abb.com
Advances in the ability to control electric voltages have enabled innovations in a plethora of products from electric motor drives to solar inverters. To manage this process efficiently, safely and reliably, not only are high-performance power electronics needed, their cooling is critical. This is especially true for the high-speed, LV drive market. In the past few years, vapor chambers have emerged as particularly interesting cooling devices for handling high heat flux in power electronics and for extending the applicability to air cooling. Ever poised for innovation, ABB set about exploring this possibility.
Missing offering
Having analyzed markets, ABB determined that customers’ power electronics needs converge toward a demand for higher power density and reliability; this hinges on the ability to cool these products efficiently. While such demands can be satisfied with water cooling systems, there is a conspicuous product offering gap for air cooling beyond a certain power density →01. Clearly, not every customer can accept the inconveniences and high cost of pumped water cooling systems as an alternative to air cooling. Thus, ABB decided to fill this unsatisfied demand. Relentless R&D efforts invested into thermal management spurred the development of ABB’s novel power electronics air cooling technology.
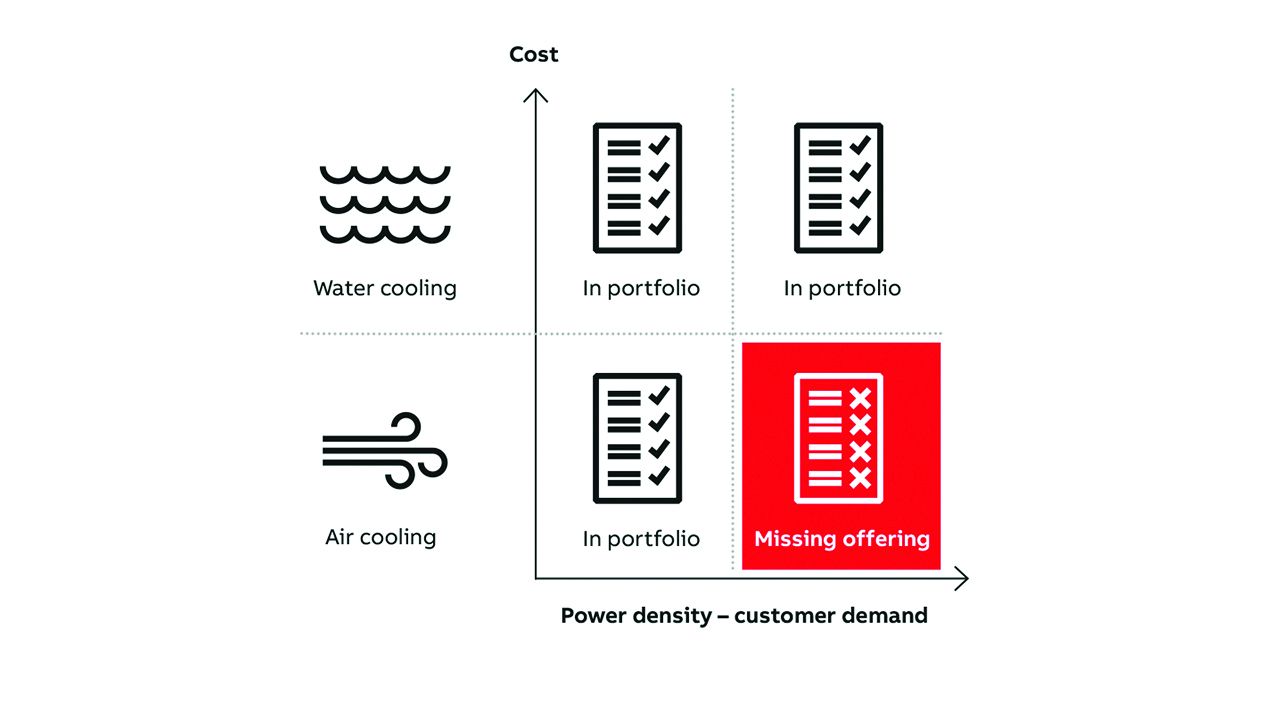
Two-phase cooling
Heat-pipes are ubiquitous heat spreading devices used to cool a variety of equipment, such as the central processing unit (CPU) of your laptop [1]. They can be shaped into a one-dimensional flow as in →02, or into two- or three-dimensional heat spreading forms known as vapor chambers. The working principle is based on the evaporation, circulation and condensation of a working fluid contained inside the heat-pipe – a two phase cooling process. The evaporation absorbs the heat from the component to be cooled, the circulation, achieved through capillary and/or gravity forces, spreads the heat and the condensation, transferring it to the cooling medium, which is usually ambient air. Such vapor chamber features caught ABB’s attention. The question became: Could vapor chamber technology be used to cool power electronics, which must dissipate kilowatts inside LV drives.
![02 Heat pipe/vapor chamber thermal cycle is illustrated [1].](https://resources.news.e.abb.com/images/2023/7/18/0/Cooler_power_electronics_m2394-02-EN.jpg)
Historically, heat-pipes were developed to cool electronics, capable of dissipating some 150 W at 85°C and 6 W/cm². In contrast, ABB required a technology to dissipate some 4,800 W at temperatures between -15°C and 110°C and a heat density of 40 W/cm², a tremendous challenge. Working together with suppliers, ABB set out to upgrade the traditional heat pipe technology to meet this new challenge.
While the product gap could be filled, partly, for lower-end drives in terms of power density using a traditional heat-pipe technology, up-scaling such technology is limited to about 1,800 W. Thus, for higher-end LV drives, ABB decided to develop an original solution with the help of additive manufacturing.
Printed vapor chamber technology
Despite offering well-known advantages such as the ability to produce lightweight components and complex geometries, additive manufacturing has limitations, eg, the production of thick, dense (non-hollow) parts, post-processing, and surface finishing. And, yet one important benefit stands out: additive manufacturing supports ideation; it frees the imagination of product designers.
While vapor chambers are used to spread heat from a source to a sink, they are essentially thin walled containers filled with a fluid: from a construction point of view they are the perfect match for an additive manufactured solution. Traditional vapor chambers, manufactured with state-of-the-art methods such as stamping, machining, soldering and bonding, are necessarily a compromise between different constraints, while additive manufacturing allows each physical process to be optimized, eg, evaporation, internal fluid circulation, condensation and air-heat transfer, without impacting the other processes.
Often labelled as a high-cost production method for prototype-development exclusively, additive manufacturing is coming of age. Owing to the careful optimization of machine parameters eg, laser paths and focus, powder selection, supportless designs and post-processing elimination, vapor chambers can now be printed at a competitive cost. For instance, ABB chose to print the vapor chamber with an aluminum alloy, AlSi10Mg, a lightweight, solid and relatively low cost powder for metal 3D printers →03.
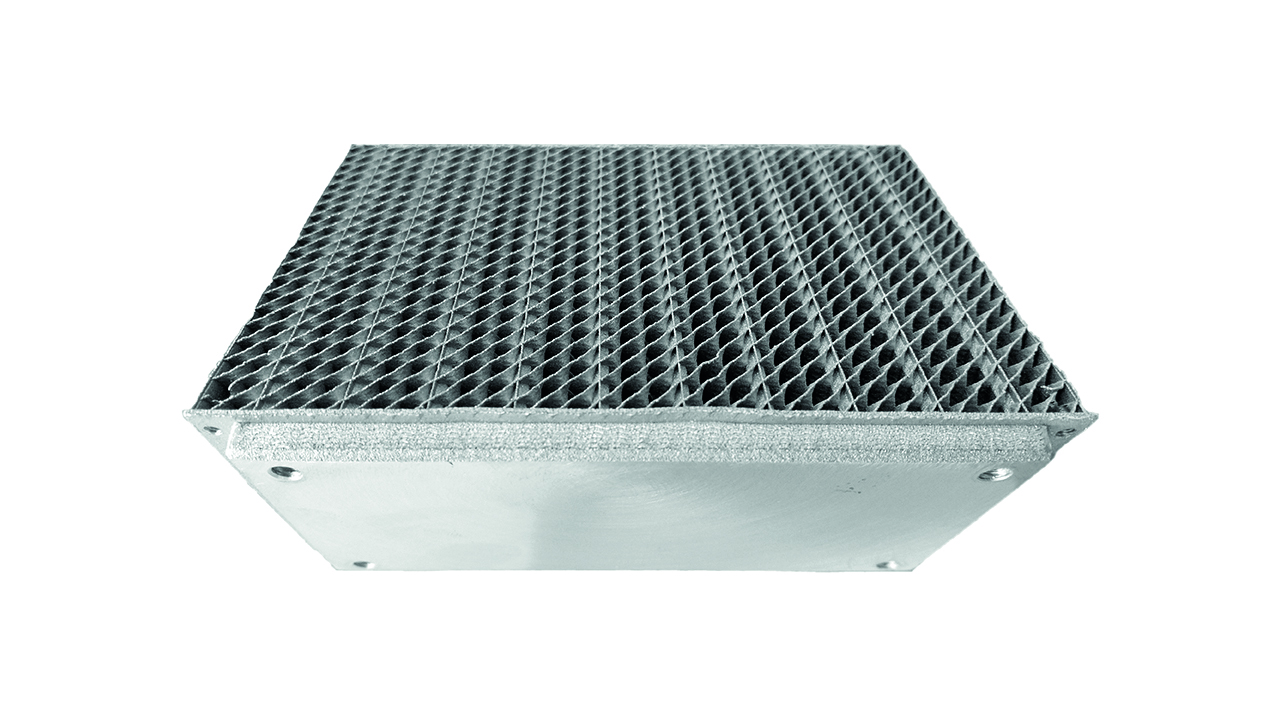
ABB also devoted attention to the geometry of the air fin design because this is where the heat transfer bottleneck usually occurs in traditional air coolers. Thanks to the design freedom that comes with additive manufacturing, ABB used triply periodic surfaces. Such fin geometry has been shown to significantly improve heat transfer within the range of air velocities that are used to cool ABB products [2,3]; this is accomplished by maximizing the air-heat transfer with a minimal drop in pressure.
Seeking superior cooling performance
To evaluate the cooling function of the printed vapor chamber, ABB compared the hotspot thermal resistance inside a LV drive for a standard heatsink, the best performing vapor chamber manufactured by state-of-the-art technology, and ABB’s new technology →04. ABB’s 3D printed vapor chamber yields a thermal resistance that is 30 percent lower than the standard heat sink, and 17 percent lower than the best performing traditional vapor chamber.
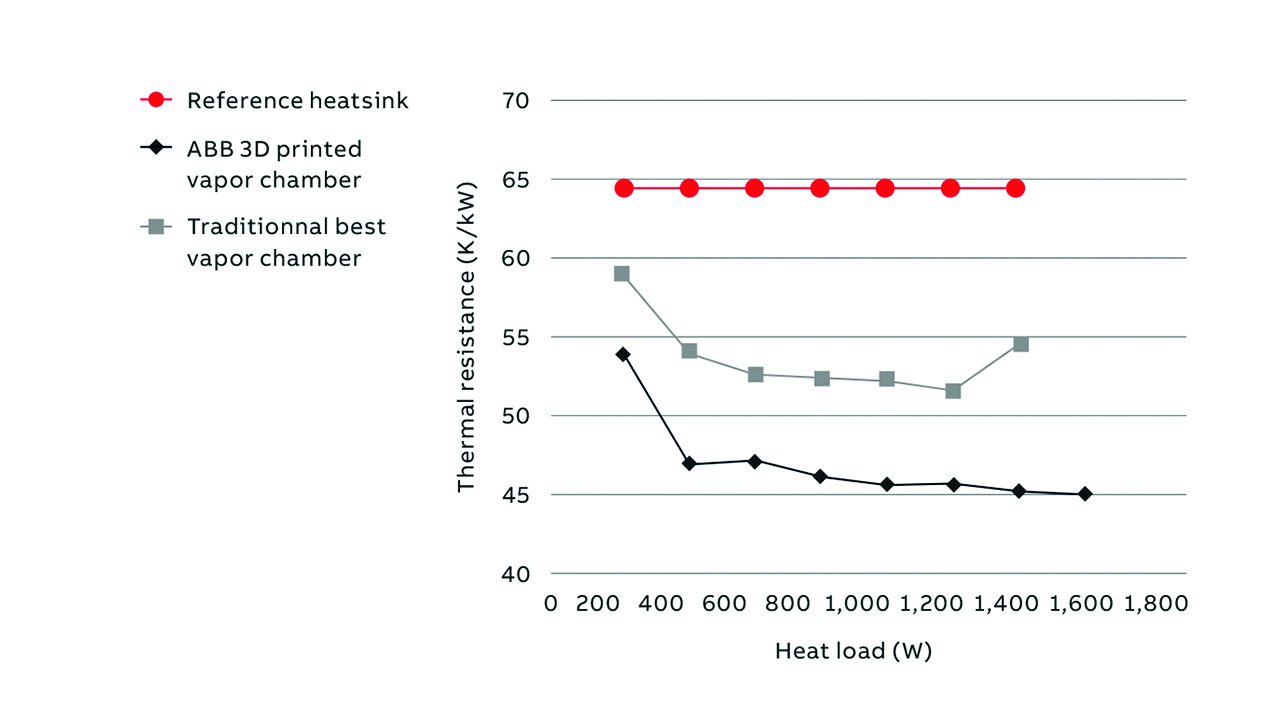
Defined as the temperature increase of the heating component relative to the cooling air divided by the heat losses, thermal resistance does not depend on heat losses for a standard heat sink, but it does for vapor chambers. A typical U-shaped curve is produced due to the variation of the working fluid’s thermo-physical properties with temperature. Initially, the internal circulation of the fluid improves as the heat losses increase, then a broad plateau is reached, which represents the heat load variation, until a condition called dry-out is established. At this level, the circulation of the liquid phase can no longer cope with the vapor production rate. Importantly, ABB’s vapor chamber technology did not reach the so-called dry-out condition →04. In contrast, dry-out did occur above 1,200 W for the traditional market-best vapor chamber tested →04. The superior performance of ABB’s technology is noteworthy as it could lead to significantly longer product life since power modules could operate at lower temperatures, higher current or switching frequency, due to the higher heat load handling capability.
Availability of alternative working fluids
Because the working fluid impacts vapor chamber performance, ABB evaluated how four different fluids impact thermal resistance →05. Acetone, a commonly used working fluid, was initially tested and found to be the best performing fluid. However, acetone is flammable, so ABB also investigated nonflammable alternative fluids, prioritizing those that are nontoxic and characterized by an acceptable Global Warming Potential¹ (GWP); Fluor-based refrigerant fluids (HFC, HFO) are nonflammable and nontoxic, and can also help maintain a low working pressure; this should be minimized to lower the mechanical resistance requirements. Therefore, two fluor-based fluids with GWPs equal to that of CO₂ (the reference gas) were evaluated: R1233zd and R1336.
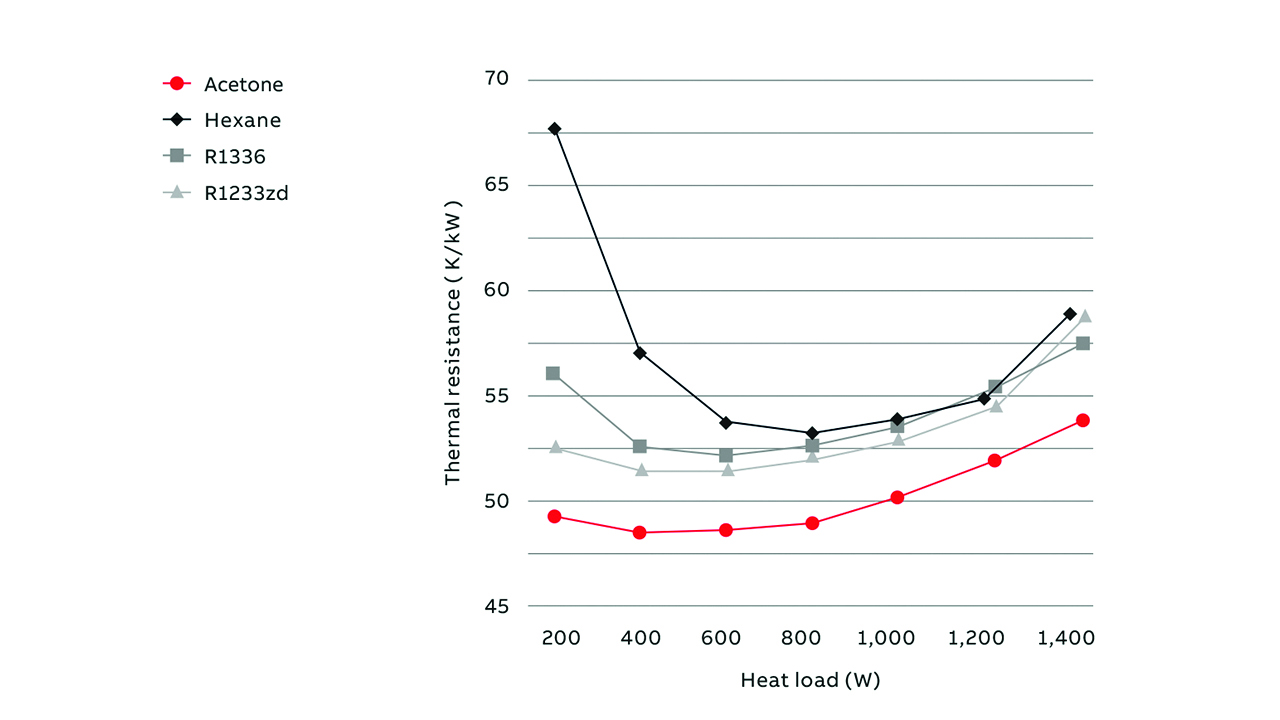
Moreover, another flammable fluid was tested: Hexane, to determine if an even lower pressure fluid could achieve a better performances than that of acetone. A comparison shows that R1336 is the best-performing alternative fluid, for applications that require a nonflammable cooling fluid, even though it displays a 7 percent increase in the thermal resistance compared to acetone →05.
Temperature and pressure cycling resistant
In contrast to CPUs of computers, most of ABB’s power electronic products, such as LV drives, must be able to operate flawlessly in extremely harsh environments, eg, in ambient temperatures ranging from -40°C to 50°C and experience large temperature cycles, which can negatively influence product life. Thus, ABB investigated the influence of temperature cycling on the thermal resistance →06 to establish the reliability of the newly printed product for use in ABB’s product LV drives. By dipping the vapor chamber 500 times, alternatingly between two liquid baths; one maintained at -15°C and the other at +110°C, and measuring the thermal resistance of the uppermost and lowermost base plate before and after each of the cycles, ABB ascertained the impact of temperature cycling on their product. Because no significant differences were observed, these results support the use of the printed vapor chamber in LV drives.
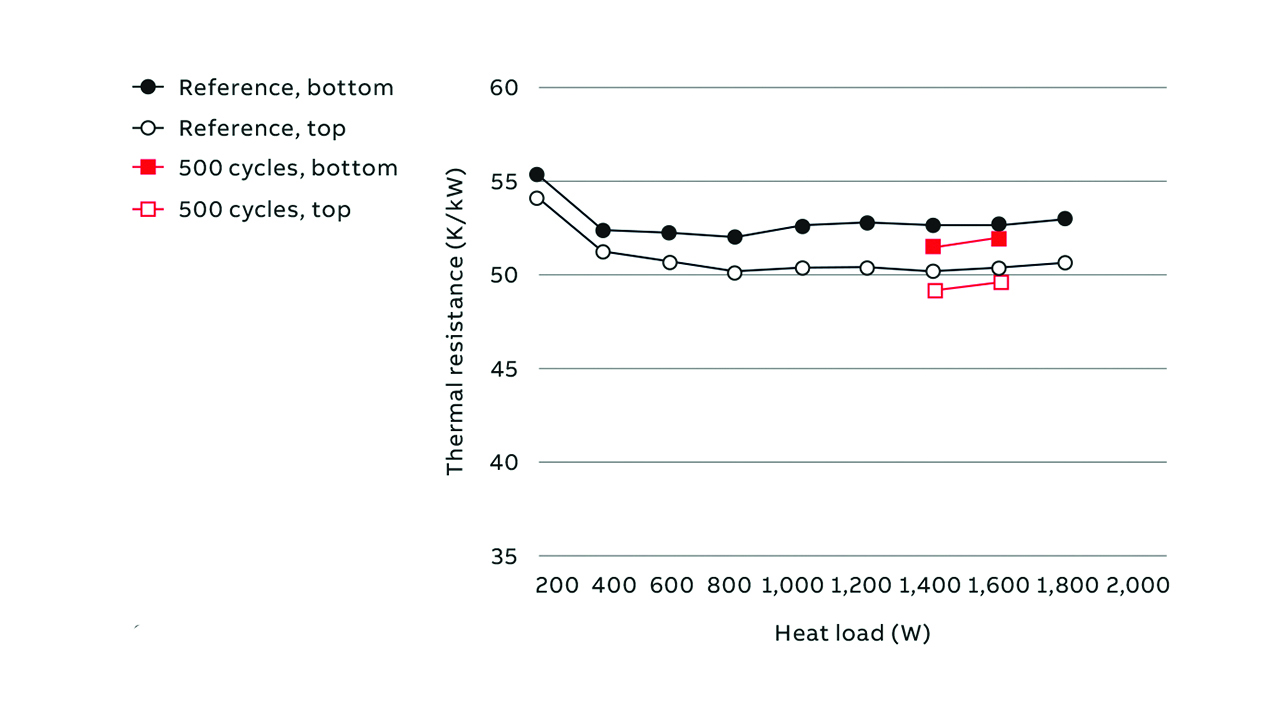
Another noticeable advantage of ABB’s cooling device is that the working fluid: acetone, does not freeze at the extremely low temperatures (down to -40°C) typically encountered in power electronics applications. Conversely, standard market vapor chambers made of copper use water as a working fluid; such a construction can lead to ice formation, bulging and mechanical damage to the vapor chamber.
Meeting clogging requirements
In industrial applications, ambient air is often loaded with dust particles that can reduce the cooling performance of vapor chambers due to the clogging of fins. To test clogging’s impact, ABB evaluated the effect of dust-filled air on chamber performance →07, specifically, the influence of dust clogged fins (for vapor chambers printed with triply periodic fins) on the cooling air pressure drop. Using ASHRAE standard dust, typically used in filter fouling tests in accordance with ANSI/ASHRAE standard 52.2 – 2012 6.2, particulate concentrations of 100 mg/m³ were injected inside a closed-loop air tunnel and circulated through a standard heatsink and four different 3D printed vapor chambers. After 150 g of dust had been circulated, amounting to six hours of air circulation, representing several years of use, the pressure drop for all prototypes remained essentially unchanged. These results indicate that the ABB vapor chamber is no more prone to clogging than the standard heatsink – a meaningful result.
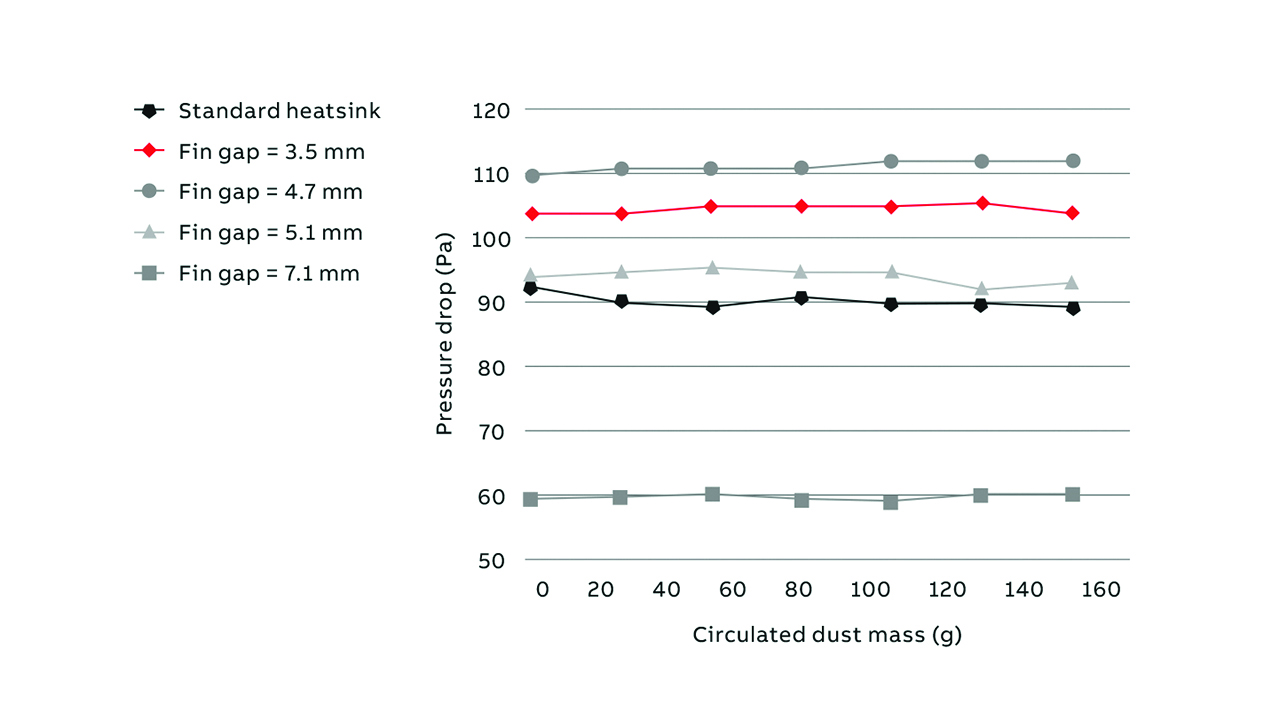
Economic considerations
The aforementioned test results rigorously support the use of ABB’s printed vapor chamber to cool power electronics, efficiently and reliably. But what about cost – additive manufacturing is expensive and mainly applicable for low-volume production, right? Well, yes and no. Thanks to the specifics of vapor chamber geometry, ABB was able to develop special parameters that increased the printer productivity and decreased the part production cost. Additionally, ABB reduced post-processing to a minimum by designing the part without the need for supports, minimum roughness and with maximum flatness; this obviates the necessity of using expensive wire-EDM and CNC milling machines.
Higher production volumes give the printshop higher negotiation power with raw material suppliers too, resulting in lower raw material prices compared to small volume “retail” prices. With the state-of-the-art process, a 4-laser machine is capable of printing about 3 to 4 tons of heatsink product per year, or 10 to 50 thousand pieces, depending on size. By using an AlSi10Mg alloy and fast parameters for additive manufacturing, costs per kilogram are generated that are an order of magnitude higher than for extrusion, laser welding or skiving depending on the production region and part geometry. However, weight impacts cost too; 3D printed parts are lightweight – weighing 7 to 10 times less than parts manufactured conventionally.
Moreover, additive manufacturing is a rapidly developing field where production efficiency and cost are continuously improving. New, so called “area printing” additive manufacturing machines allow a 10 times faster printing speed. Together with further design advancements aimed at reducing part weight, such modifications will cause a dramatic shift in the air cooling industry. For the first time, printed heatsinks will not only be smaller, lighter, and better performing, they will be able to price-match existing extruded heatsinks; this transition is anticipated to occur within the next two to four years.
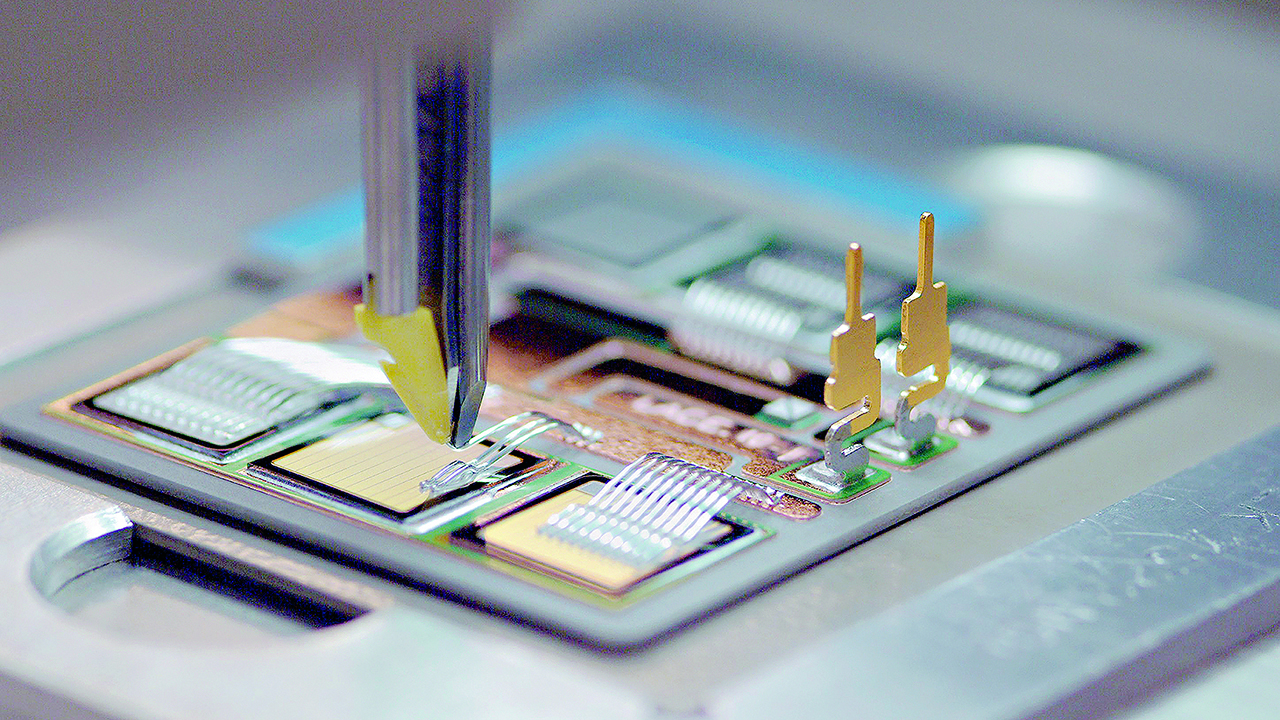
To unleash the full potential of power electronic semi-conductors →08, more efficient and reliable cooling is essential. Despite having conquered the CPU and graphic processing unit (GPU) markets over the past two decades, two-phase heat transfer via the use of copper-water vapor chambers is limited. Scaling-up such technology (by increasing the volume and heat load) for use in LV drives is possible only up to a point: A level exists beyond which power and reliability requirements cannot be satisfied simultaneously. Taking-up this challenge, ABB developed an original vapor chamber solution with the help of additive manufacturing. Not only is this new technology more affordable than ever, it demonstrates superior performance compared to standard technologies, thereby meeting power electronic customers’ cooling needs today and tomorrow.
References
[1] Zootalures and Offnfopt, CC BY-SA 3.0: https://creativecommons.org/licenses/by-sa/3.0, via Wikimedia Commons, https://commons.wikimedia.org/wiki/File:Heat_Pipe_Mechanism.svg [Accessed Sept. 22, 2022.]
[2] M. Khalil, et al., “Forced convection heat transfer in heat sinks with topologies based on triply periodic minimal surfaces”, Case Studies in Thermal Engineering, Volume 38, 2022, pp. 102313.
[3] J. Iyer, etal., “Heat transfer and pressure drop characteristics of heat exchangers based on triply periodic minimal and periodic nodal surfaces”, Applied Thermal Engineering, Volume 209, 2022, pp. 118192.
Footnote
¹ GWP refers to the total contribution to global warming resulting from the emission of one unit of a gas relative to one unit of the reference gas, CO₂.