The company leads the field in megawatt machines using innovative permanent magnet technology, pre-assembled at its impressive Large Drive Test Centre near the university city of Lappeenranta, Finland. ABB Generations met Vice President of Technology, Panu Kurronen, to discuss how exhaustive testing ensures reliability prior to delivery.
Generating the required electricity to power operations and amenities on ships is an issue that has haunted the industry for more than 150 years, since the dawn of the electrical era.
The challenge is even more pertinent today as shipowners hunt for new ways to increase energy efficiency and cut emissions amid ever-tightening climate regulations. “People are focusing on propulsion as the obvious area to look at for efficiency improvements, especially as new sustainable fuels become available. However, shaft generators also require scrutiny as they play a key role in modern propulsion systems,” says Kurronen.
How shaft generators can help reduce fuel consumption
“Let’s rewind a bit first. Electricity has traditionally been produced on ships using standalone synchronous excitation-based generator sets – or gensets. These require an external fuel source to produce the electricity, typically provided by an auxiliary diesel engine completely separate from the ship’s main engine,” he explains.
“The first shaft generators were developed in the 1960s and were a big step forward in reducing the historical reliance on gensets and thirsty auxiliary engines. By connecting directly to the propeller shaft, they make electricity using the energy already supplied by the main engine. The gensets can then be turned off, so reducing fuel burn. Shaft generators are also more effective when used in conjunction with the huge drive power of two-stroke main engines, versus less powerful four-stroke engines.”
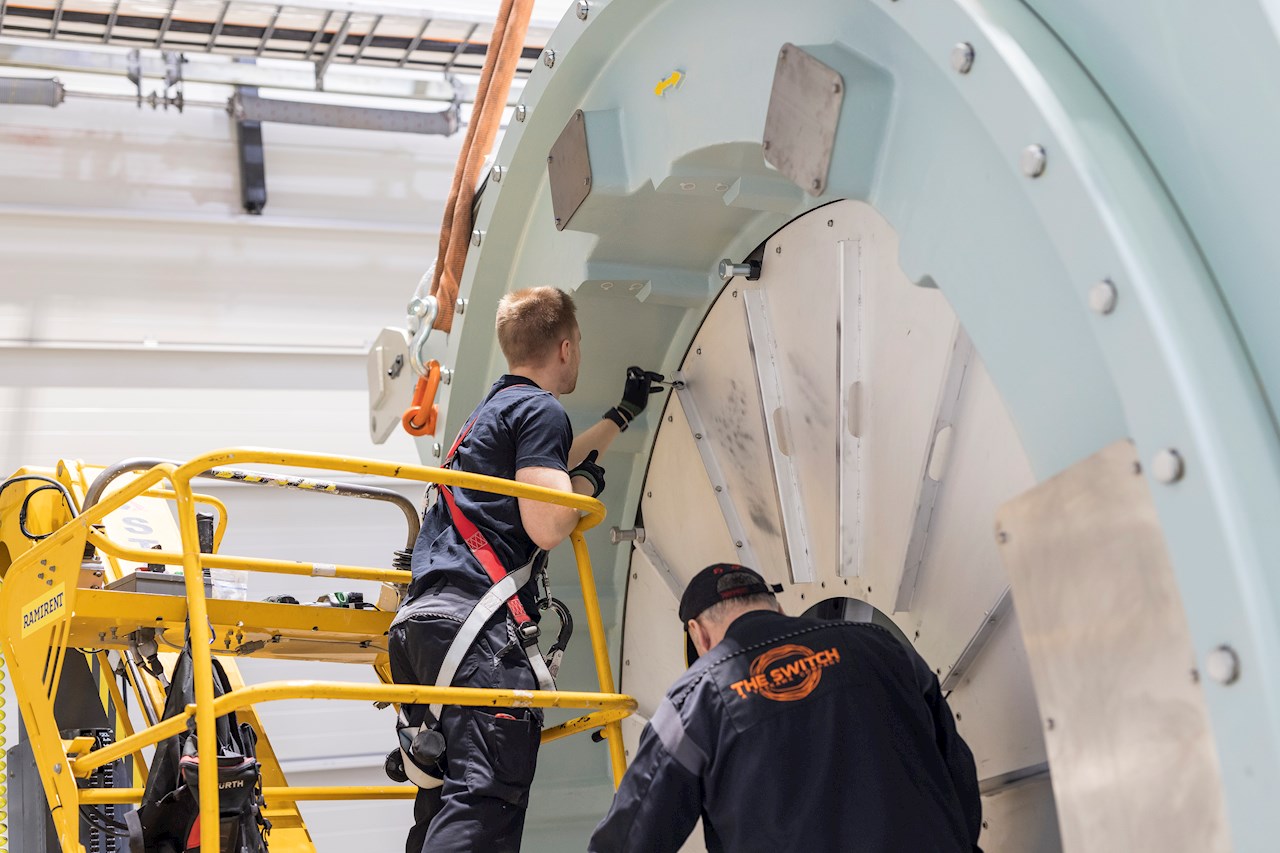
But there was still one major drawback – although shaft generators connect directly to both the ship’s propulsion shaft and the ship’s onboard grid, there was no frequency converter in between them.
Our machines use modern neodymium magnets that create the magnetic field much more efficiently.
The frequency bottleneck
“This limited their efficacy as they could only cope with a constant speed from the ship’s propulsion drive. When the ship’s speed changed, the frequency of the electric current produced fluctuated, rendering the shaft generator unusable. It would then have to be disconnected, and the genset(s) would take over,” Kurronen explains.
This issue was resolved in the 1980s when frequency converters were introduced. “The shaft generator then came into its own as it could cope with any speed from zero up to the ship’s design-rated speed and feed a constant frequency to the ship’s electrical grid.”
Conventional shaft generators combined with frequency converters can be used as the sole generating source of electricity onboard a vessel or as a supplement to the gensets, reducing the need to burn fuel. “They can also be used as a source of power to drive the propeller at very low speeds, which is useful for saving emissions when moving around in port. The system can also be used for occasional propulsion power boosts of up to 15 percent if needed to break through ice, for example, or when sailing in strong headwinds.”
However, despite these benefits, there are some key areas where conventional shaft generators fall short. “Conventional systems still require a current to flow in a rotor winding to create the magnetic field, so there is always energy loss through heat. Heat loss means lower power conversion efficiency, resulting in higher fuel consumption in the main engine. They, of course, generate savings versus gensets, but more advanced units go further,” says Kurronen.
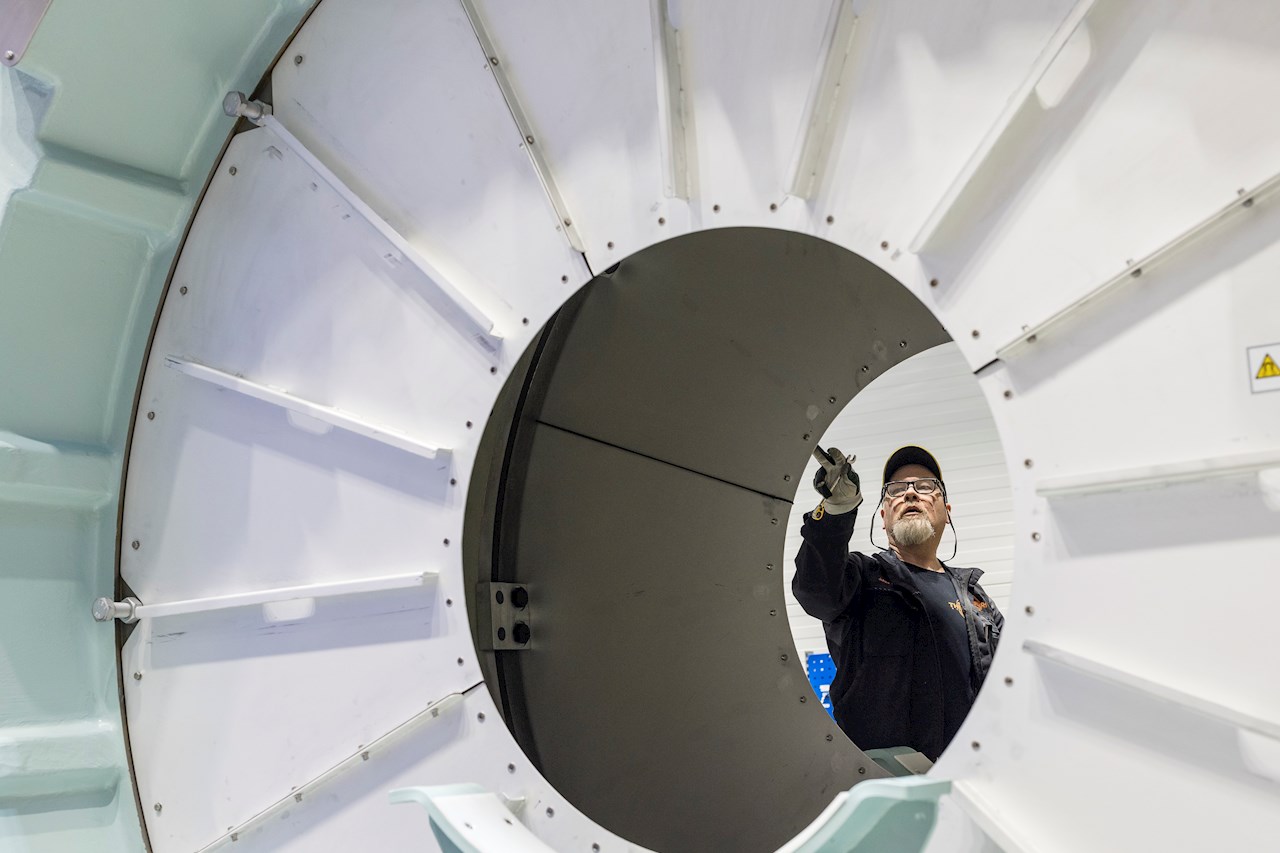
The PMs are so strong that the whole unit can be reduced in size, typically weighing 30–50 percent less than conventional machines.
Magnetic innovation
This is where PM shaft generators are a game-changer. “Our machines use modern neodymium magnets that create the magnetic field much more efficiently, without the need for external power supplying a current to the rotor. This immediately decreases the amount of fuel required. The PMs are also so strong that the whole unit can be reduced in size, typically weighing up to 30–50 percent less than conventional machines,” says Kurronen.
The system can cut fuel consumption by a further 2–4 percent compared to conventional units, generating savings that are becoming ever more potent as emissions regulations get stricter. “This reduction applies to emissions as well. Over a typical 20–25-year lifespan of a large vessel, these savings can bring an estimated $2 million reduction in fuel costs and help avoid 5,000 tons of CO2 emissions.”
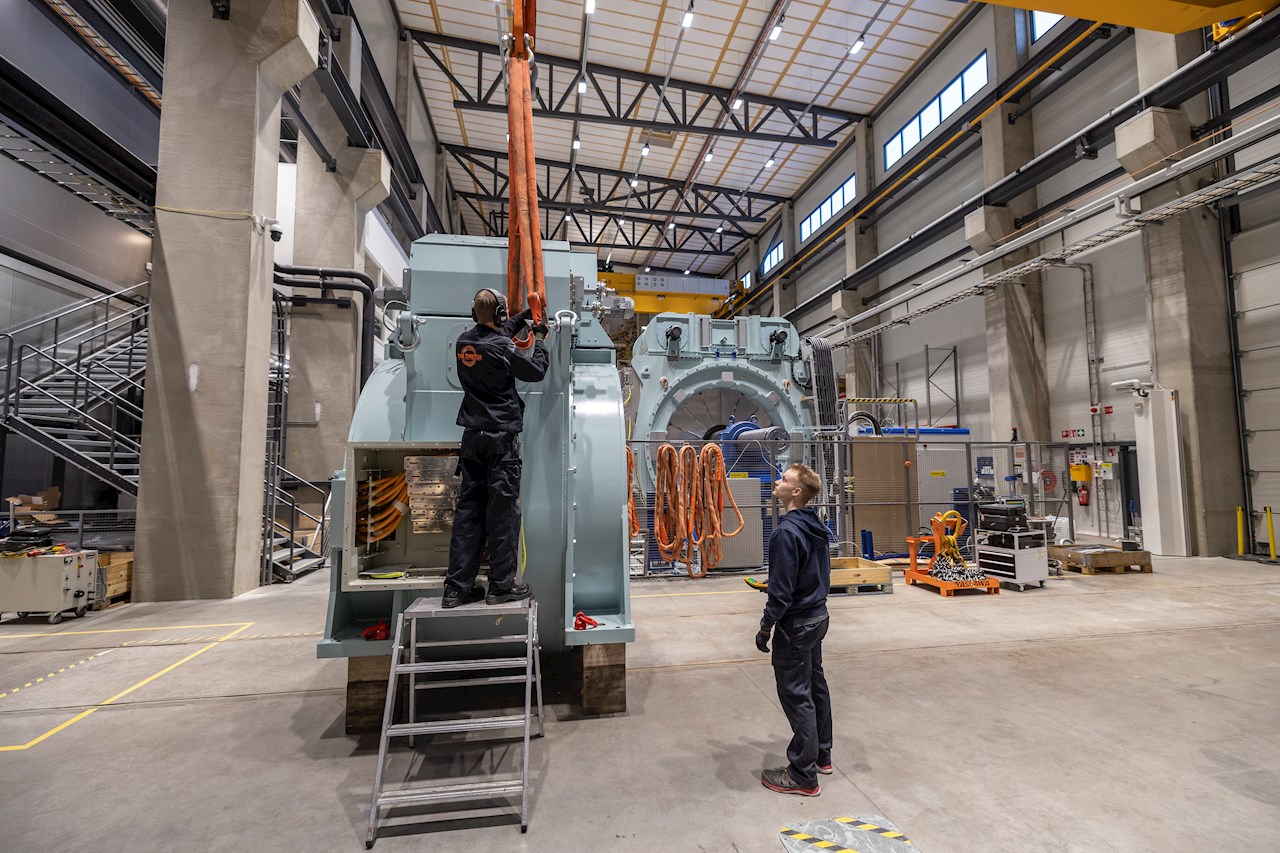
Easy installation, lower maintenance
This added efficiency can also help a vessel gain a better Carbon Intensity Indicator (CII) rating. Plus, the solution eliminates genset wear and tear or failures that could require disruptive and expensive repairs. “The simple mechanism also means there are almost no wearing parts, dramatically increasing reliability and simplifying installation. With more than 100 of our units in operation today, not a single failure has occurred,” Kurronen says.
The company supplies shaft generators to OEMs and systems integrators, including ABB Marine & Ports, looking for market-ready solutions that enhance performance and reliability for their customers. “We are currently involved in a major ABB Marine & Ports delivery of permanent magnet shaft generator systems to a series of very large containerships under construction in China and South Korea. They are expected to yield up to 17 percent greater efficiency during voyages versus diesel gensets,” he adds.
Michael Christensen, Vice President, Segment Manager, Dry Cargo Global Sales at ABB, comments: “We have a great relationship with Yaskawa Environmental Energy / The Switch and applaud the innovations they have made in the demanding field of shaft generators for marine use. Like ABB, they are equally committed to helping customers convert, store and consume energy more efficiently and reducing CO2 emissions per capacity mile.”
Yaskawa Environmental Energy / The Switch has been at the forefront of exploring and expanding permanent magnet machine technology for two decades, first for wind power applications and since 2013 for marine. “The technology has the potential to reduce emissions beyond simply improving operational efficiency. As an investment, it has a very short payback time, especially in view of the expected high cost of new sustainable fuels. Vessels equipped with a shaft generator system may also require lower installed gensetpower; and with running hours reduced, the gensets require less maintenance. This means a reduction in both Capex and Opex,” Christensen adds.
The technology has the potential to reduce emissions beyond simply improving operational efficiency.
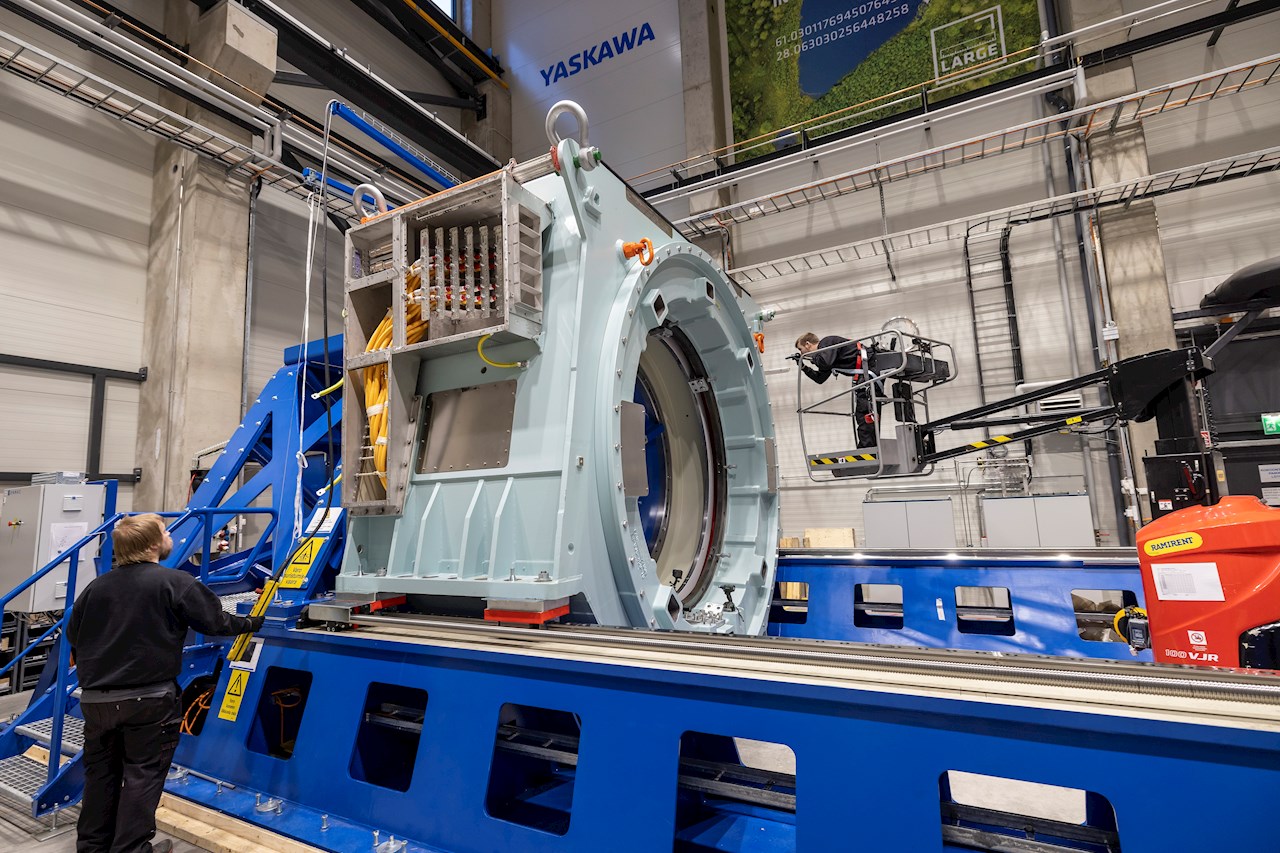
Enter the Large Drive Test Centre
Kurronen explains that, prior to delivery, all permanent magnet shaft generators are exhaustively tested at the Yaskawa Environmental Energy / The Switch’s purpose-built Large Drive Test Centre (LDTC) next door to its factory in Lappeenranta. “The LDTC is one of the world’s largest facilities to test large electric machines and converters for marine and renewable energy configurations, and we can now push the boundaries for the biggest machines in the business. We performed our first factory acceptance test (FAT) for three PMM1000 shaft generators in August 2021, and today we regularly test 12-MW back-to-back electrical drive systems.”
This year, capacity has been extended to test systems up to 18 MW. “That beats almost anything else available globally – and it’s all happening out here in the middle of the Finnish countryside,” says Kurronen.
Construction of the LDTC started in the summer of 2019 and was completed in 2020. “We went ahead with the investment simply because equipment is getting bigger all the time, and drives are getting more powerful. It was essential to have a place where we can verify the reliability of the units alongside customers as they move towards a greener future.”
Prototypes are given a back-to-back full-load FAT to test them to full capacity. “In practice, each marine project has different speed, power and torque requirements. So typically, a new machine type is developed for each new project, and the first machine always undergoes back-to-back FAT. In addition, each individual machine we produce is given a no-load FAT before being shipped,” says Kurronen.

Tailored testing
The LDTC can also combine testing with individual customers’ own components, such as their own shaft, bearings, beds or converters. “And we can design and manufacture any other tooling customers might require, providing as close to real-life validation as possible,” Kurronen adds.
The centre can undertake around 50 test sets per year, depending on test complexity and the size of the machines, which are typically of at least several megawatts capacity and weigh in at 20 to 80 tons. “We have space to run two parallel test sets simultaneously, or one running and another in preparation, which shortens throughput time. We can also perform certification tests for classification societies.”
Kurronen adds that there are clear benefits for customers in that they can have complete confidence in the thermal, electro-magnetic and mechanical behaviour of each machine. “Finished units that have been tested to full capacity, with certification carried out on site, also save time and money during the commissioning phase. Customers can also request special tests, including using a third-party converter and/or the actual components to be installed in the vessel. These include no-load string tests and back-to-back string tests at full power.”
In conclusion, he quotes the company’s mission to electrify the world with game-changing green technologies. “But we are very careful to ensure everything works reliably before we sell it to others. Customers can rest easy knowing that the shaft generator they have bought has already been through an ultramarathon at the LDTC.”
Large Drive Test Centre
The 1,155-square-metre factory expansion features:
- Advanced liquid cooling system
- Electrical distribution centre
- Two overhead cranes with a total maximum capacity of 100 tons
- Concrete floor more than two meters thick and weighing around one million kilograms
- Heavy-duty steel construction that can withstand back-to-back tests up to 80 tons, as well as all associated forces and machine vibrations
Images: Mikko Nikkinen