The Catch-22 of battery manufacturing
Battery manufacturers today bear the brunt of societal responsibility. The climate crisis demands that humanity decarbonizes as fast as possible, and with the incredible projected growth of electric vehicles and renewable energy, batteries are the key to the clean energy transition [1][2]. Battery manufacturers' ability to keep up with the production demands of the energy transition is not only in the interest of those manufacturers, but the entire world.
Battery manufacturers today are feeling pressure from all sides. The successful deployment of cleantech is tightly tied to the cost of batteries: battery energy storage must be at least cost-neutral compared to fossil fuel alternatives in order to justify wide adoption. Batteries are also notoriously challenging to make. Uniformity and consistency is a must for any manufacturer, but for batteries, the effects of variability can even be lethal [3]. So, not only are they expected to meet increasing volume and quality demands while lowering price requirements (thus, thinning margins), but the field is also rapidly changing around them. There are constantly new developments in battery chemistry and best practices for production, which means processes are often changing.
And on top of all of this, battery manufacturers find themselves in an existential crisis: Since batteries are ushering in the age of clean energy, they are under scrutiny to be sustainable themselves in order to not contradict their very existence, but how can manufacturers afford to implement the highest level of sustainability when there is such great pressure to create as many batteries as possible as quickly as possible? In fact, manufacturers cannot afford to not invest in sustainability. They are in the unique position of needing to achieve growth profitably while also being good stewards of the earth, lest they weaken their own value proposition as a fossil fuel alternative.
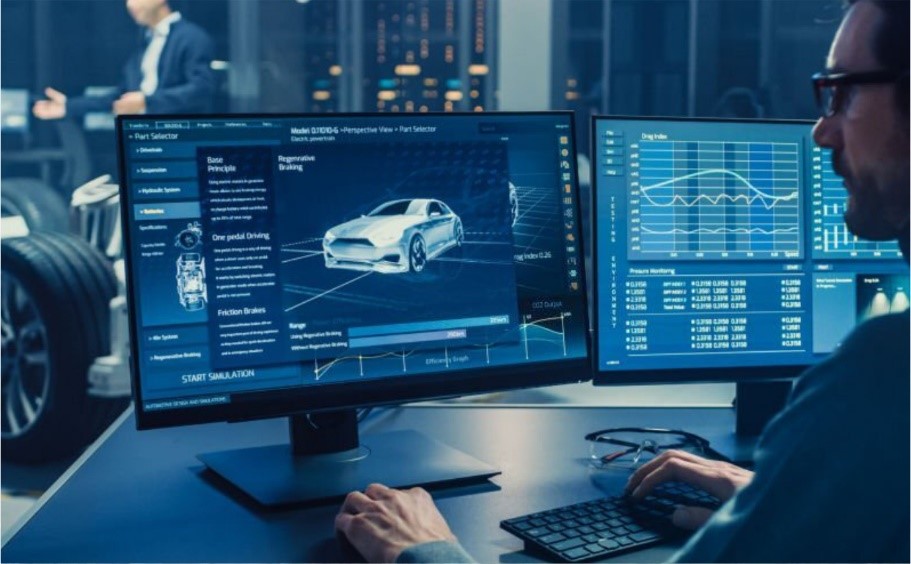
The sustainability-innovation nexus
To be sustainable is to use resources responsibly, to foster a healthy environment, to take care of people, and to ensure transparent, responsible supply chains. There are unlimited combinations of technologies and policies that can be implemented today to improve a battery manufacturer's sustainability: building cells from renewable materials (e.g., organic, aqueous, etc.), improving production processes to use less material, powering manufacturing operations with renewable energy, and sourcing raw material from companies that adhere to the highest human rights standards, to name a few.
Lucky for battery manufacturers (and all of us), focusing on sustainability can accomplish all other production, quality, and cost-reduction goals. When we aim to reduce energy use, emissions, and water use, we reduce cost. When we aim to reduce resource waste via lower scrap rates, we improve quality. When we aim to provide a safer, more inclusive environment for our workers, we improve productivity. And key to enabling each of these outcomes is digital.

Digital as the key to unlocking sustainability
“Digital” is thrown around as a futuristic buzzword, but plainly speaking, a digital solution collects information as data (through means such as sensors) and then does something useful with that data, like automating a process or providing intelligence that allows a person to make an informed decision. Advanced process controls improve yield and quality while reducing energy and resource use. Asset performance management promotes the longevity and energy efficiency of equipment. In addition to reducing scrap and improving logistics (and therefore, energy efficiency), manufacturing operations management systems facilitate production transparency and traceability, which has become essential due to the high environmental (e.g., scrape rates, energy consumption) and economic/political (costs, regulations) impact of the battery production process [4]. Energy management systems predict factory energy use and orchestrate that demand with the grid and/or on-site generation to reduce emissions and utility costs. Connected workforce management tools can provide training and work instructions to the multitude of new workers that will be needed to shoulder the battery revolution (900,000 new jobs are expected in the US alone [4]), thus ramping them up to productivity as fast and as safely as possible.
Amidst the complexity and demands of the modern era, we must have clarity of vision to see the forest through the trees. For battery manufacturers, sustainability provides that vision. Sustainability is both the raison d'être and the means to solve other business challenges. Through sustainability-focused digitalization, battery manufacturers stand to meet environmental requirements, improve product quality and yield, and achieve overall cost-efficiencies – thus bringing all of us into our sustainable future.
References
[1] International Energy Agency, "Demand for electric cars is booming, with sales expected to leap 35% this year after a record-breaking 2022," April 26 2023. [Online]. Available: https://www.iea.org/news/demand-for-electric-cars-is-booming-with-sales-expected-to-leap-35-this-year-after-a-record-breaking-2022.
[2] World Economic Forum, "IEA: More than a third of the world’s electricity will come from renewables in 2025," 16 March 2023. [Online]. Available: https://www.weforum.org/agenda/2023/03/electricity-generation-renewables-power-iea
[3] M. Wayland, "Ford recalling 18 electric F-150 Lightning pickup trucks after battery fire," CNBC, 10 March 2023. [Online]. Available: https://www.cnbc.com/2023/03/10/ford-recalls-electric-f-150-lightning-pickups.html. [Accessed 30 June 2023].
[4] F. M. Zanotto, D. Z. Dominguez, E. Ayerbe, I. Boyano, C. Burmeister, M. Duquesnoy, M. Eisentraeger, J. F. Montano, A. Gallo-Bueno, L. Gold, F. Hall, N. Kaden, B. Muerkens, L. Otaegui, Y. Reynier, S. Stier, M. Thomitzek, A. Turetskyy, N. Vallin, J. Wessel, X. Xu, J. Abbasov and A. A. Franco, "Data Specifications for Battery Manufacturing Digitalization: C," Batteries & Supercaps, 2022.
[5] F. Takemura, "This Georgia program is training a huge cleantech manufacturing workforce," Canary Media, 9 June 2023. [Online]. Available: https://www.canarymedia.com/articles/clean-energy-jobs/this-georgia-program-is-training-a-huge-cleantech-manufacturing-workforce. [Accessed 30 June 2023].