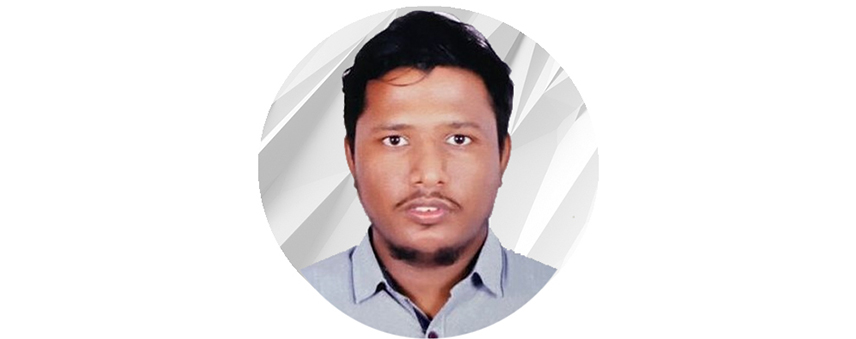
It is my 5th year in ABB, working as an Advanced Process Control (APC) engineer implementing ABB Ability™ Expert Optimizer. I am mainly focused on projects in the cement Industry, but this is starting to change as I continue to broaden my industry expertise.
I have a chemical & process engineering background, which sets a good foundation for the typical challenges faced in implementing APC in the industry. My routine tasks involve first understanding unique customer processes' and then looking to exploit control opportunities. However, my first job after graduation was in industry gas manufacturing, where I learnt the importance of process optimization with different control strategies.
In 2018, I joined ABB, a completely new environment from what I was used to. I received a warm welcome as I was familiar with some team members through an earlier internship in 2016.
During my initial days of joining ABB, I was trained and mentored by my seniors on the APC team, which included primary DCS interfacing and general process control. Here, I learnt about system architecture, plant operations, and the core of my work, model predictive control, and fuzzy logic.
Though the initial days were challenging, I gained a lot of confidence in the products and technology, thanks to the management for believing in me and giving me back-to-back commissioning opportunities. During my journey, the team supported me in improving my technical skills, sometimes during non-office hours when I was remotely away at a customer site in a different time zone.
Throughout the initial commissioning, I learnt the complete scope of project execution, which includes functional design, project engineering, OPC configuration, step testing, model identification and simulation, fine-tuning of the application, operator training, and remote maintenance. There is no substitute for "getting your hands dirty," this initial on-job training helped me understand the complete workflow of taking a plant from sub-optimized to optimized.
Today I can proudly call myself an APC engineer, which has the simple goal of improving process performance for the customer. This includes improving process stability, increasing productivity and yield, and reducing consumables (energy, chemicals, etc.).
Implementing an APC program is typically faced with many obstacles, for example, sensors needing to be fixed, missing instrumentation, poorly tuned base level PIDs, equipment-related bottlenecks, unrealistic constraints, and management of change (MOC). One of the skill sets I developed as an APC engineer, which systematically handles these challenges, is performing plant audits, otherwise known as Fingerprints.
Here, we define a base level of performance and identify the delta between the current plant and best in class through mainly statistical data analysis. This includes equipment, instrumentation, control strategies, PID health, and overall potential performance increase. Fingerprints are one of the significant recommended steps for a successful APC implementation.
During the APC execution, I learned it is essential to constantly clarify the customer's needs, targets, and objectives and gain as much insight from as many sources as possible, from upper management to operators. We must stay agile and flexible as goals can change during the middle of a project. This helps us build a control strategy unique to their plant conditions. One primary example is a site in India with an operational concern in their cement mill, where it frequently tripped, affecting the power plant for balancing the power requirement. As a team (ABB and customer), with everyone's input, we built a control strategy that helped stabilize milling operations and reduced load fluctuations, significantly reducing mill trips.
A unique Project I am proud of:
During Covid times, we had an opportunity to execute a project for one of the largest cement conglomerates in Indonesia, which included the commissioning of four cement mills, one raw mill, and one kiln line. As onsite implementation is critical for APC success, especially handling the MOC, this project was very challenging due to the travel restrictions and limited flight options at the time. With the necessary safety measures, I had an opportunity to execute this project with continuous support from my manager, who was remote. I am super proud of this project because overall, it was a very successful implementation of APC under trying circumstances where we achieved a 4 % increase in production and between 2 – 5 % reduction of specific power consumption in the mills, and a 2 % reduction of specific heat consumption in the kiln line.
For me, as a junior engineer, this is a project that will always stand out and one that I will never forget. Another reason I will always remember this project is that there was a challenging task as a young engineer to convince the customer to adopt technologies such as APC, especially when dealing with MOC. What I find (and found) works as a junior engineer is the constant involvement of all personnel from the start, explaining the step by step the project, with a significant emphasis on listening to them rather than dictating from “years of experience,” focusing on understanding their requirements, and ensuring their inputs make it into the optimization strategy. I believe this ensures buy-in and helps increase the visibility and responsibility of the project, as the customer is now more involved and invested in making it a success.
Overall, I believe APC provides a strong foundation for my and anyone’s career who is interested in overall plant economics, driving efficiency, optimization, and even sustainability. I want to continue growing and contributing more to projects across multiple industries over the coming years, not only cement! As ABB is involved in all major industries, I have the opportunity and support to do so. I want to thank all my colleagues who have helped me in this journey and for their continued support and guidance.