Liza Chua, Associate R&D Engineer, Electric Solutions,ABB Marine & Ports
Ricky Chan, R&D Manager, Electric Solutions, ABB Marine & Ports
Tegoeh Tjahjowidodo, Associate Professor, NTU
Gerald Seet, Associate Professor, NTU
With the increasing focus on environmental conservation actions from all sectors, concerns have been raised over the expected increase in emissions from the shipping industry with the potential rise in international shipping. In response, the International Maritime Organization (IMO) set out to cut carbon emissions by half in 2050 [1] and implement stringent limits on SOx and NOx in Emission Control Areas (ECAs)[2].
With the new regulations, ship operators are faced with increasing pressure to find solutions for more energy efficient operations. Conventionally, ships have been designed using a single operating point as a reference where the energy sources can be tuned at the highest efficiency level. Such method has been proven optimal for ocean going vessels, such as container ships. However, such approach may not be ideal for other vessel types, such as tugboats and offshore supply vessels (OSVs), where the operational profile is dynamic, which means that energy-efficient operations cannot be guaranteed.
The so-called ‘tugboat dilemma’ is an example, where tugs are designed according to their maximum bollard pull, but they rarely operate in that range. The three main modes of a harbor tug operation can be broadly categorized as (i) transit, (ii) standby or idle, and (iii) ship assist operation. The power requirements and duration of each operation mode are vastly different, which can be seen from the tug’s load distribution as shown in Figure 1, represented by the solid black line. Specifically, tugs have been known to spend only a fraction of the operation time in the ship assist mode, while majority of the time (>80 percent) they are in the transit and standby mode where the power requirements are significantly lower. In comparison with the specific fuel oil consumption (SFOC) of the engine shown in dotted line shown in Figure 1, it can be clearly seen that the engine operates below the fuel-efficient range most of the time, leading to higher fuel consumption and greenhouse gas (GHG) emissions.
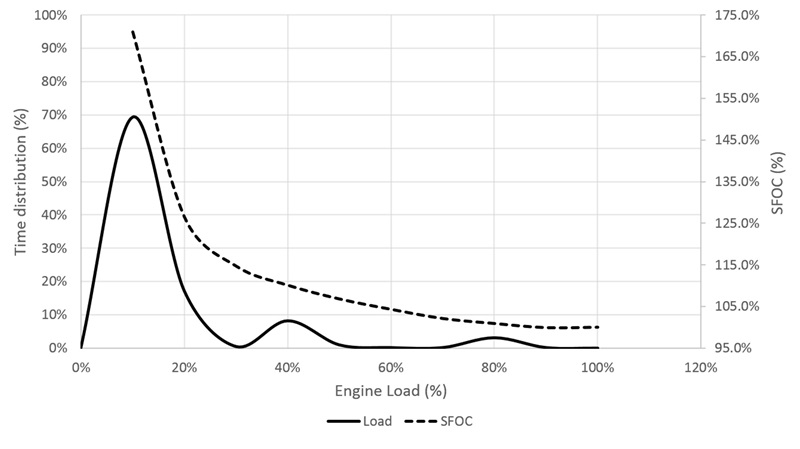
Electric propulsion can offer a solution to address the challenges of poor fuel efficiency for such vessels. In 2010, ABB introduced its Onboard DC GridTM power distribution system, which has since then demonstrated reduction of carbon footprint for a number of vessel types. The DC-based power system also offers the advantages of easy integration of energy storage devices such as batteries and fuel cells. An example of the hybrid electric power system based on the principle of modern DC distribution system, such as ABB’s Onboard DC GridTM is shown in Figure 2. In this system, the main power sources comprise of gensets and batteries. An AC-DC rectifier is used to convert AC power from the gensets to DC. Power from both genset units and energy storage are distributed through a DC distribution system to supply propulsion, service and hotel loads.
Such design allows flexibility to optimize the load allocation among multiple power sources, therefore offering large potential in reducing fuel consumption and possibilities to achieve low or zero-emission operation. For example, strategic loading can be implemented with energy storage system to maintain engine within its optimal operating range, and hence improving fuel efficiency. Additionally, batteries can be used as an alternative auxiliary power source, reducing the need for auxiliary engines, allowing the vessels to maintain its function while reducing their GHG emission and other pollutants.
When alternative energy sources and energy storage system are considered, ship power management control strategy plays a crucial role to achieve the desired benefits of a hybrid electric power system. At present, majority of the ship power management strategies employed in the industry are using conventional rule-based/heuristic techniques, which depend largely on the experience of the system integrators and operators. However, due to the increase in the degree of freedom in power allocation, designing the control rules for a large number of combinations of power allocation and loading condition becomes a complex task, and more importantly, optimality is not guaranteed. In addition, the diverse operating profiles and control objectives make it difficult to optimize the hybrid power system performance over a single operating point during the design stage or apply common rules across all vessel types. These challenges of an advance power system demand an intelligent power management control strategy to effectively manage the multiple energy sources and their constraints to maximize the fuel savings and emission reduction benefits, while ensuring system stability and reliability.
Optimization-based methods themselves are not new and they have been well researched and proposed to improve power management strategies for hybrid electric vehicle (HEV). With technology advancements allowing greater connectivity on board ships, optimization-based methods can be applied to improve the power management of advanced power and propulsion architectures such as the hybrid electric vessel [3]. Digitalization allows real-time information of the power system to be obtained, which can be utilized to generate optimal decision on power split among the power sources through optimization-based methods. This article describes a real-time optimization-based power management strategy and control framework that has been proposed to optimize fuel efficiency and reduce emissions.
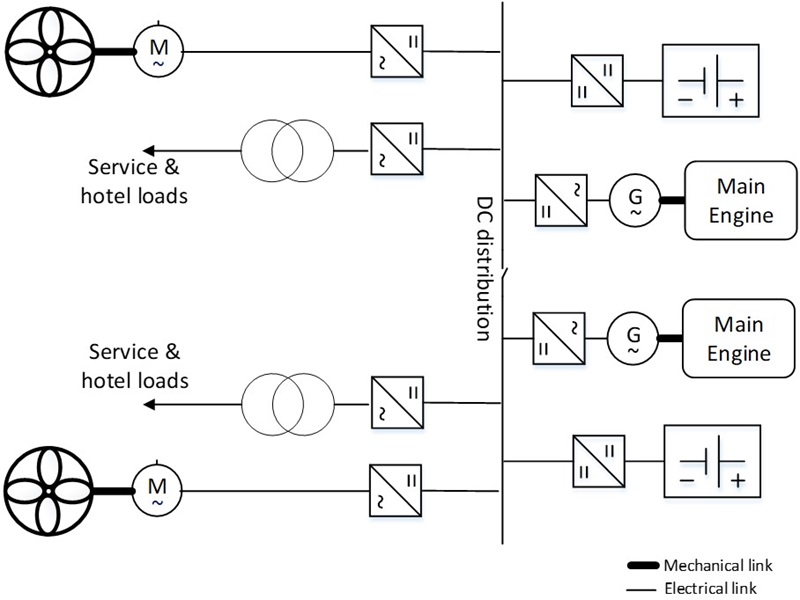
Power management optimization and control framework
The optimization-based power management strategy is developed for a hybrid electric power system considered in Figure 2. The system is simplified for the design of the optimization problem as shown in Figure 3. The formation of a power management problem into an optimization problem requires each decision variable to have an associated cost, and this cost determines if the control objective can be achieved while minimizing the cost function. However, in the case of a hybrid electric power system, the challenge of formulating the cost function is to associate the cost of battery energy to the energy cost of fuel.
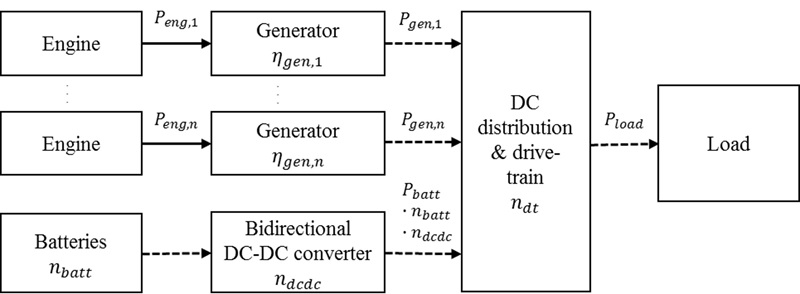
The equivalent consumption minimization strategy (ECMS) is one of the methods first proposed for applications in HEVs to associate the use of battery energy to an equivalent fuel cost. ECMS assumes a charge sustaining operation, where the amount of battery energy used will be recharged by the engines in the future. Under this assumption, the equivalent cost for the use of battery energy is a positive cost derived by considering the average fuel required to recharge the battery along the energy path from the engine to the battery. A negative cost is associated with charging of the battery, which is equivalent to the fuel consumption when engine is used to provide this amount of energy. ECMS considers only instantaneous equivalent fuel cost and does not require prior knowledge of future load demand, allowing it to be implemented in real-time. This is a great advantage in some marine applications as load predictions for vessels are not easily available, especially for vessel with multiple modes of operations that experience large load variations, for example tugs. Therefore, this work develops the power management strategy using this approach [4].
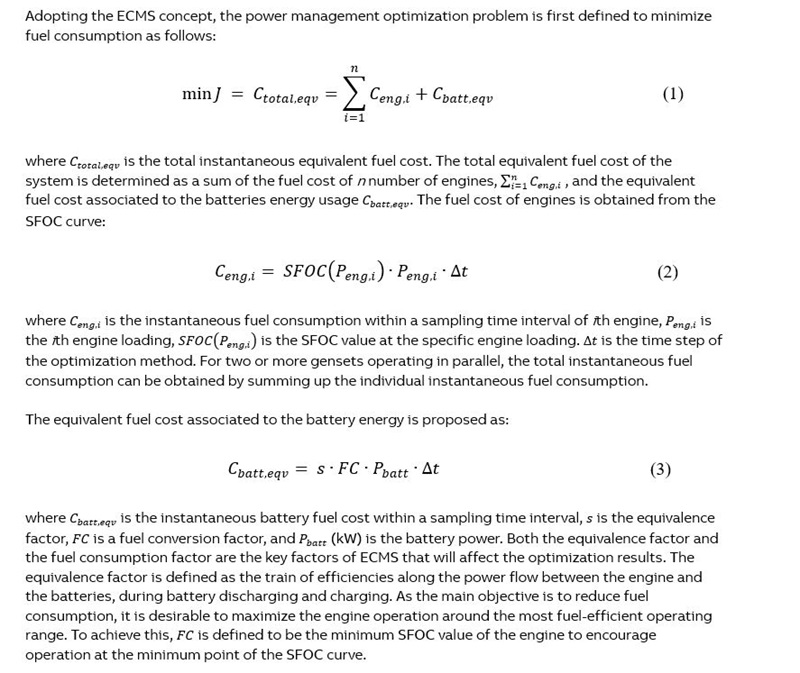
The optimization problem is subjected to equality constraints to ensure that the total load demand is met. In addition, boundary conditions such as range of state-of-charge to preserve the battery’s lifetime, charging and discharging limits of the batteries, as well as maximum rating of the engines are also considered in the constraints, ensuring that the solution generated is within the feasible working range of the power system. At every time step, the optimization problem is solved to determine the power split between the gensets and the battery to meet the load demand.
To implement the solution from the proposed ECMS to an existing power management system, a multi-level power management framework is proposed as shown in Figure 4. The proposed strategy takes the supervisory level, where power reference values generated at every time step are sent to the primary level control. The primary level represents the existing fundamental power management control in the system, where voltage droop functionalities, load dependent start/stop rules and protection controls are executed. The main controls for the gensets are start/stop signals, depending on the power references from the supervisory level. When power reference for the genset is greater than zero, the genset will be started. When more than one genset is operating, load sharing will be done through the existing voltage droop functionalities. To achieve the desired power split according to the power references from supervisory level, the bi-directional DC-DC converter will operate in power mode, implementing strategic loading when discharging in parallel with working gensets, since the voltage on the DC distribution line is maintained by the genset. When battery is the only source of power supply in the system, the bi-directional DC-DC converter will operate in voltage control mode to maintain the voltage stability on the DC distribution grid during load variations. The amount of discharging current will vary according to the amount drawn by the load demand, which should also coincide with battery power reference generated from the supervisory control.
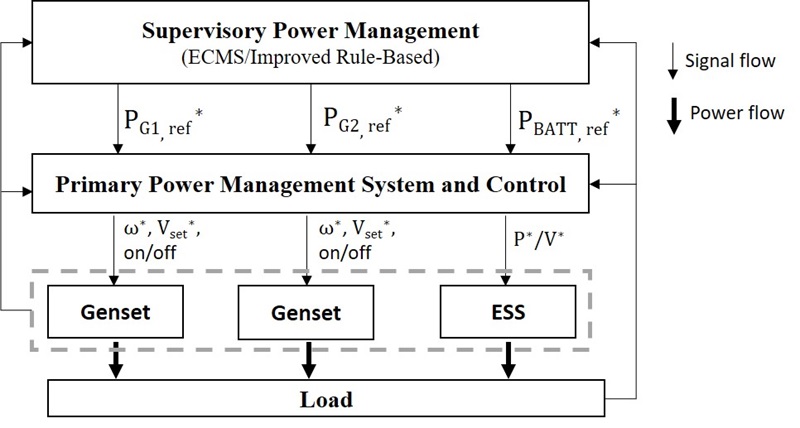
Case study
The feasibility of the proposed ECMS and the multi-level power management framework is investigated over the operation of an hybrid electric harbor tugboat consisting of two gensets and batteries. A representative time-domain load profile of the harbor tugs derived based on field engine data and experiences of tug owners is shown in Figure 5.
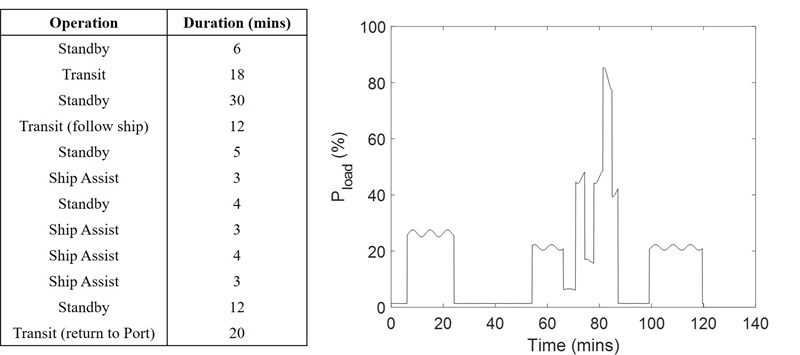
The case study is conducted in the laboratory facility in MARINTEK, Trondheim. The facility consists of a full-scale system that can be configured to mimic a hybrid all-electric vessel general system layout with Onboard DC GridTM and ABB Power and Energy Management System (PEMS). The system parameters for this case study is indicated in Table 1. As it is not practical to run such a long experiment, the duration of the load profile is scaled downed proportionally to a total cycle time of 35 minutes for this purpose, while still capturing sufficient dynamics to show the effectiveness of the optimization method. The operation cycle is executed separately in three segments - segment 1 consisting of transit and standby operations for the first 12 minutes; segment 2 consisting of transit, short standby and ship assist operations for the next 11 minutes; and segment 3 consisting of mainly transit operations in the last 12 minutes. The performance of the proposed ECMS in terms of fuel savings is also evaluated against an improved rule-based strategy that is designed with the understanding and knowledge gained from the solutions of optimization-based strategies.
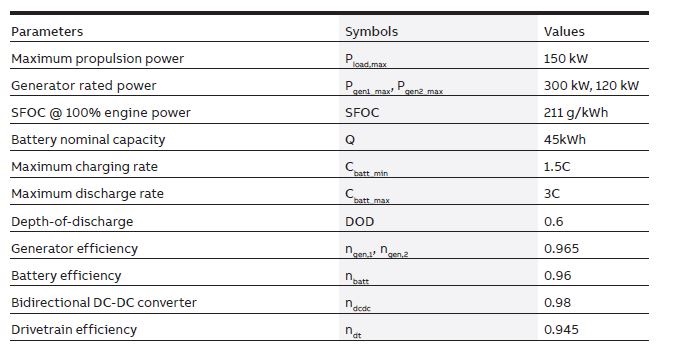
The experimental results shown in Figures 6 and 7 demonstrate the feasibility of the control framework, and performance of the proposed strategy. Voltage stability of the system is observed where the voltage on the DC grid is well maintained between 540-580Vdc, within 6 percent of voltage droop. The control framework is well executed where the power references from the proposed ECMS are achieved in the actual power split between the power sources as shown in Figure 7. The load demand is met with SOC of the battery is well kept within the lower and upper SOC limit of 30 percent to 90 percent as set in the constraints. Although the total power delivered to the load is observed to be slightly lesser than the total power delivered by the power sources, this is due to power transmission losses in the system.
The fuel consumption in each segment is shown in Table 2. Comparing the performance of proposed ECMS against the improved RB strategy, the advantage of proposed ECMS over the improved RB is mostly shown in segment 2 and 3. Based on the improved RB strategy, genset 2 is used to provide the required power for the load and charge the battery in the transiting period in attempt to increase the load on the engine in segment 2. However, due to the charging rate limit of the battery, the total load on the engine remains around 30 percent, which is relatively low and less fuel efficient. The proposed ECMS in this case, utilizes available battery power during this transiting period, hence preventing the engine to operate at low engine loading. In segment 3, similarly, the improved rule-based utilizes both genset 2 and battery to provide power for the load, while ECMS utilizes the available battery power to avoid operating the engine in less fuel-efficient range. This resulted in a substantial amount of fuel savings in ECMS as compared to the rule-based strategy, as shown in Table 2. As the combined installed power of genset 2 and the battery is sufficient for 100 percent of the maximum propulsion power in this case, genset 1 is started during the operation.
Overall, it is shown that the proposed ECMS demonstrates better fuel efficiency as compared to improved rule-based strategy. The battery seems to be more well-utilized in the case of ECMS in segment 2 and 3, contributing to the overall fuel savings. In the case where shore charging is possible, this amount of battery energy used can be charged from shore power, which further saves on fuel consumption. The fuel savings achieved from ECMS in this case, can be up to 24.4 percent with the availability of shore charging.
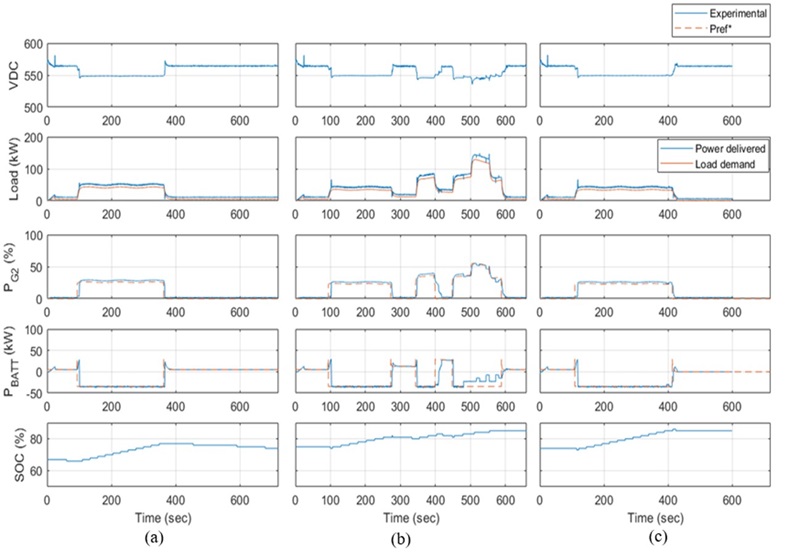
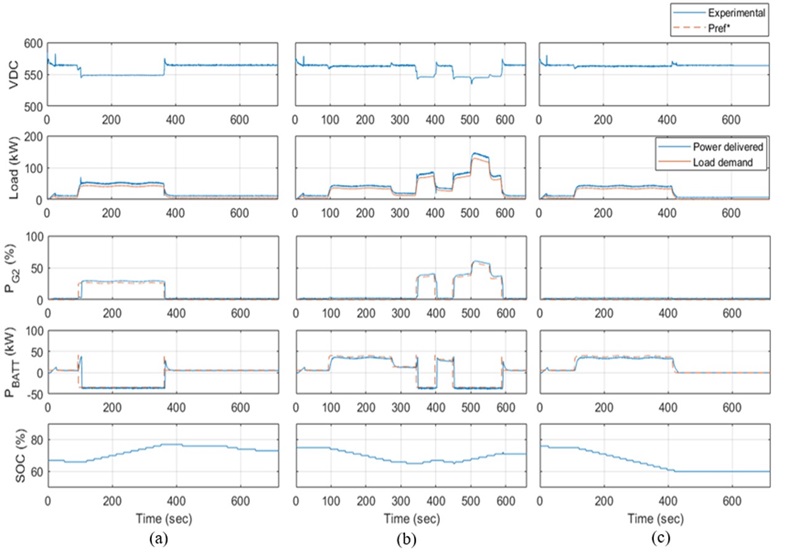

Dealing with emissions – managing the trade-off between NOx emission and fuel consumption
A minimization of fuel consumption will lead to a reduction in emission only if the emission and fuel consumption are proportional. However, among the major composition of ship emissions (CO2, NOx, SO2, HC, CO, PM), a possible trade-off between NOx emission and fuel consumption has been highlighted. An example is the specific NOx emission (SNOX) and SFOC curve as shown in Figure 8 [5], where it can be observed that there is an increase in NOx emission when fuel consumption is low in certain operating range. Although there are existing technologies in the market such as exhaust gas recirculation (EGR) and selective catalytic reduction (SCR) to reduce NOx emissions, such devices may have their constraints such as requiring addition operating power or space limitations on smaller vessels. Therefore, the possibility to optimize NOx emission reduction and fuel consumption during engine operation, through the power management control approach, is investigated.
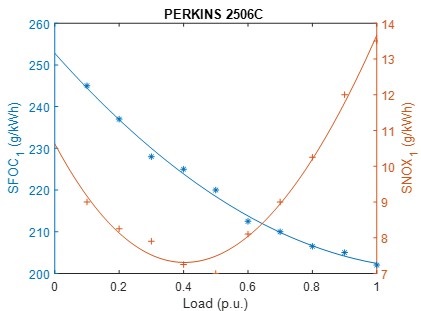
With the validated performance of the proposed ECMS, the optimization strategy is extended to further consider the minimization of ship emission. To manage the increase in fuel consumption due to the effects of NOx emissions, a method is proposed to include a control weighting KNOX that defines the amount of priority given to NOx emission reduction. The proposed cost function formulation is expressed as:

where Ctotal,eqv represents the total equivalent fuel consumption defined in Equation (1)-(3), and Etotal,eqv is the total equivalent NOx emission that can be obtained by replacing the SFOC terms in Equation (1)-(3) to the engine’s SNOX values. The value of KNOX is in the range of 0 to 1, where a value of 0 omits the NOx emission and considers only fuel consumption in the optimization problem, while a value of 1 considers only NOx emission. In this way, the ship operators are given the flexibility to prioritize between fuel efficient and emission efficient operation depending on the operation needs. For example, when a vessel is operating near the harbor or in ECAs where the limit for NOx emission is more stringent, a pure NOx emission reduction control can be adopted. In cases when there are lesser requirements on the emission reduction, fuel consumption can be improved by adjusting the KNOX to a lower value. The effectiveness of the proposed method in managing the trade-off between fuel consumption and NOx emission is demonstrated through simulations over the harbor tug operations shown in Figure 5.
Performance of the proposed approach is investigated over the range of KNOX at regular intervals of 0 to 1. The results for KNOX at 0 and 0.6 are presented in Figure 9(a) and (b) respectively to show the effects of KNOX. In Figure 9(a) where NOx emission is not considered (KNOX = 0), it is observed that the engine operation is maximize around 100 percent loading, which is the most fuel-efficient point as observed from the SFOC curve in Figure 8. As weighting factor increases, the emphasis to reduce NOx emission increases. Therefore, it is seen in Figure 9 (b) that there is a shift in the engine operating point to around 40 percent loading when switched on, in attempt to maximize the engine operation around the lowest point of the SNOX curve in Figure 8 to reduce NOx emission.
The average specific fuel consumption and NOx emission over the range of KNOX at regular intervals of 0 to 1 for one operation cycle is shown in Figure 10. The increase in KNOX causes a shift in the engine operating point towards the emission efficient point that brings a reduction in NOx emission, while compromising on the fuel efficiency. Overall, the proposed approach performs as expected where the increase in the weighting factor KNOX reflects a reduction in NOx emission. Using this method, the emphasis on NOx emission reduction can be controlled by adjusting the weighting factor, hence managing the compromise on the fuel efficiencies
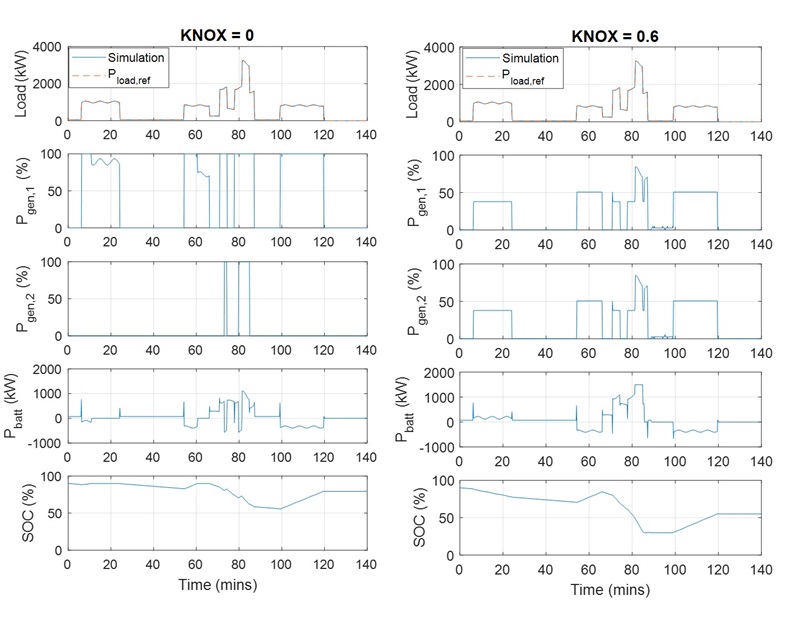
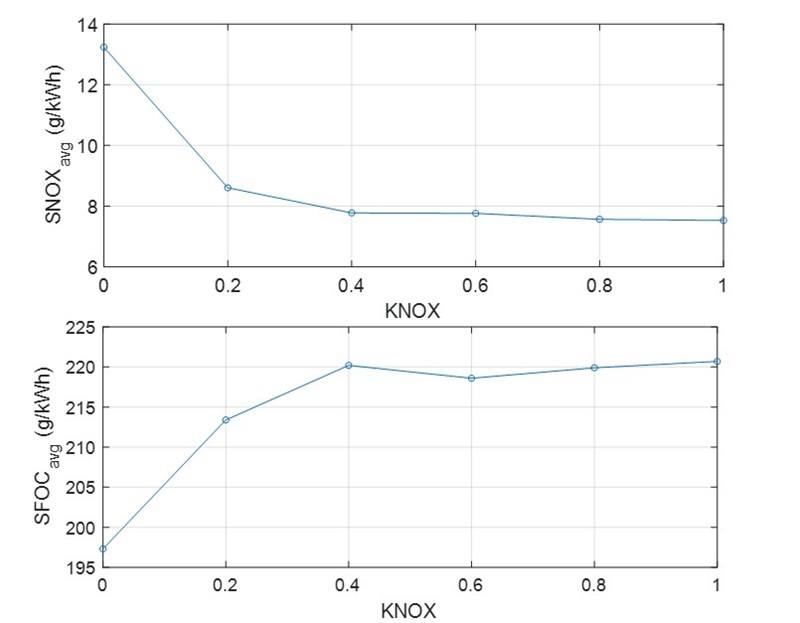
Moving forward
While technologies are rapidly evolving for new system configurations and alternative power sources to achieve more energy efficient operations, advanced control technologies are necessary to achieve the desired benefits of these systems. The proposed strategies in this work have shown the potential of optimization-based power management control strategies for advanced marine power systems to improve fuel efficiency and reduce emission. The proposed strategies are not limited to a hybrid electric vessel and can be easily extended for different combination of power sources, as well as different applications such as offshore rigs. Moving forward, with digitalization bringing greater connectivity and faster communication on ships, there are greater opportunities to be explored in optimization-based methods to improve control strategies, enabling ships to operate more efficiently and environmentally friendly.
References
[1] International Chamber of Shipping, “Reducing CO2 Emissions to Zero: The ‘Paris Agreement for Shipping’”[Online]. Available: http://www.ics-shipping.org/
[2] IMO,“Marpol annex VI prevention of air pollution from ships.”[Online]. Available: http://www.imo.org
[3] Geertsma, R. D., Negenborn, R. R., Visser, K., & Hopman, J. J. “Design and control of hybrid power and propulsion systems for smart ships: A review of developments, “Applied Energy, vol. 194, pp. 30-54., 2017.
[4] Chua, L.W.Y., Tjahjowidodo, T., Seet, G.L.S. and Chan, R. “Implementation of Optimization-Based Power Management for All-Electric Hybrid Vessels”, IEEE Access, vol. 6, pp. 74339-74354, 2018. DOI: 10.1109/ACCESS.2018.2883324.
[5] H. O. Kristensen, "Energy demand and exhaust gas emissions of marine engines," Clean Shipping Currents, vol. 1, no. 6, pp. 18-26, 2012.