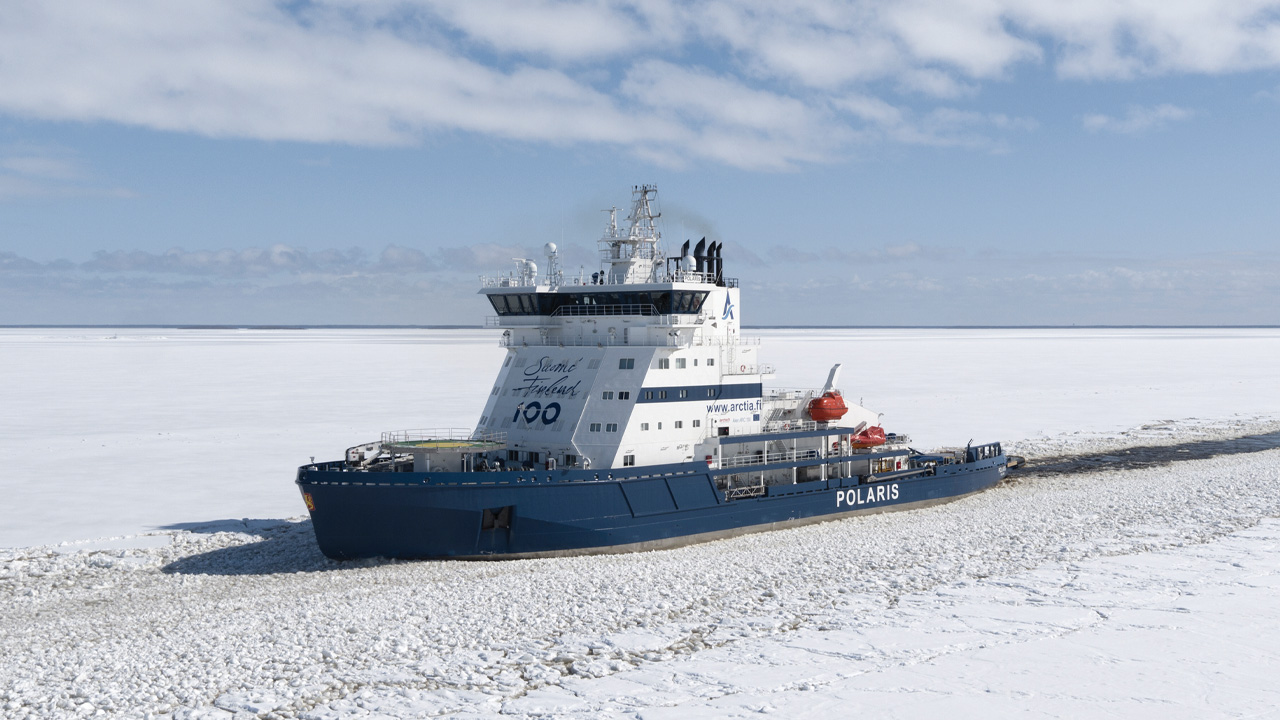
Aker Arctic Technology was contracted by FTA, the Finnish Transport Agency, to design the new craft, dubbed the Polaris. Mika Hovilainen was in charge of concept development on the Polaris project.
The target was to develop icebreakers for the most difficult conditions in the Baltic.
“The target was to develop icebreakers for the most difficult conditions in the Baltic,” Hovilainen says. In the northern Baltic, the Bay of Bothnia, ice typically reaches a maximum thickness of one metre, relatively light compared to the Arctic. The challenge, Mika relates, comes from prevailing winds that push ice flows against the Finnish coast, creating what are known as ice ridges. Despite the fact that Arctic ice is typically twice as thick, ridge ice fields are every bit as daunting in their own right.
Polaris’ predecessors were the workhorses built in the 1970s for the Swedish and Finnish governments, the now-legendary Urho class ships. The Finnish icebreakers Urho and Sisu are familiar fixtures on the Helsinki waterfront, while the Swedish giants Atle, Ymer and Frej now operate out of Luleå in the northern Baltic. “These were the most powerful and best performing icebreakers in heavy ridge conditions,” Mika relates. “Now Polaris is meant to replace these, with even better performance.”
As with most icebreaking projects in Finland, the development of Polaris was a national effort. Aker Arctic teamed up with ILS Ship Design & Engineering out of Turku to evaluate concept alternatives, and the vessel was built at Archtech Helsinki Shipyard.
The LNG breakthrough
So why LNG? “LNG is the cleanest fossil fuel, and the government was interested in building a ship with a greener profile,” Mika says. “There was already one government vessel, the Finnish Coast Guard Offshore Patrol Vessel Turva, in operation using LNG fuel. There were also several LNG terminal projects under discussion, and it became clear that we would have sufficient bunkering opportunities. In general, logistics for LNG are steadily improving.”
LNG also made it possible to meet ECA, or Emissions Control Area requirements, due to take effect for the whole Baltic, and applicable to all new ships trafficking the region. But innovation seldom comes easy. “LNG adds both costs and complicating issues to design,” says Mika. “Like how to accommodate larger tanks on the ship.” LNG requires more volume for the same amount of energy as fuel oils, and the pressurised tanks required to contain it take up more space. “The rule of thumb is four times the volume of fuel oils.”
Still the design team was able to accommodate the major increase in tank size with only minor increases in vessel size. The solution: “Build up, not out,” says Mika. “These are the biggest vertical tanks ever built, at 17.6 metres high. That gives the ship 10 days of autonomous operation in the most demanding conditions of a normal winter.” Mika says.
“The design is tailored to allow bunkering and crew change cycles to coincide, and that was the target,” Mika reports. The Polaris also has dual fuel capacity using fuel oil for extended autonomy if needed. “But a section of the fuel tanks is reserved for recovered oil in the event of a spill, so they are not always full.”
Oil recovery, even in ice, is just one of Polaris’ many capabilities, including emergency towing, rescue, and salvage. “But ice breaking is of course paramount, and Polaris has proven to be excellent at this.”
Hovilainen points out one performance enhancing innovation in particular: the arrangement of two Azipod thrusters in the stern, and one in the bow. This selection was made to optimise icebreaking and towing performance, especially in contact towing, where the towed ship is winched up against the towing notch in Polaris’ stern.
“The forward Azipod unit has proven to have a great impact on manoeuvrability. Placing a thruster 100 metres forward of the pivot point gives tremendous steering leverage when towing.” A bow-mounted azimuthing thruster was previously tested on the Baltika, a smaller Russian breaker, but has proven to be every bit as effective on a larger scale.
The forward Azipod® unit has proven to have a great impact on manoeuvrability.
Full-scale ice trials were performed at end of March 2017, and official trials confirm feedback from the crew, that the vessel is over-performing in all aspects. New high marks for Baltic icebreaking have been set in level icebreaking, ridge penetration and manoeuvring capability. (See testimony from a Polaris master on the next page).
Mika Hovilainen acknowledges the breakthrough that LNG represents on the Polaris, but as an engineer, he feels compelled to communicate all the factors that go into making Polaris special:
“Polaris is commonly referred to as the most environmentally friendly icebreaker because of LNG fuel, but in fact that is just the icing on the cake.” Before considering how to produce the energy, energy consumption was minimised, he points out. That meant refining many aspects of design, including hull form, propulsion arrangements, system design, heat recovery, and more. “Our goal was to design the most efficient icebreaker ever,” Mika Hovilainen states, “and we have definitely achieved that goal.”
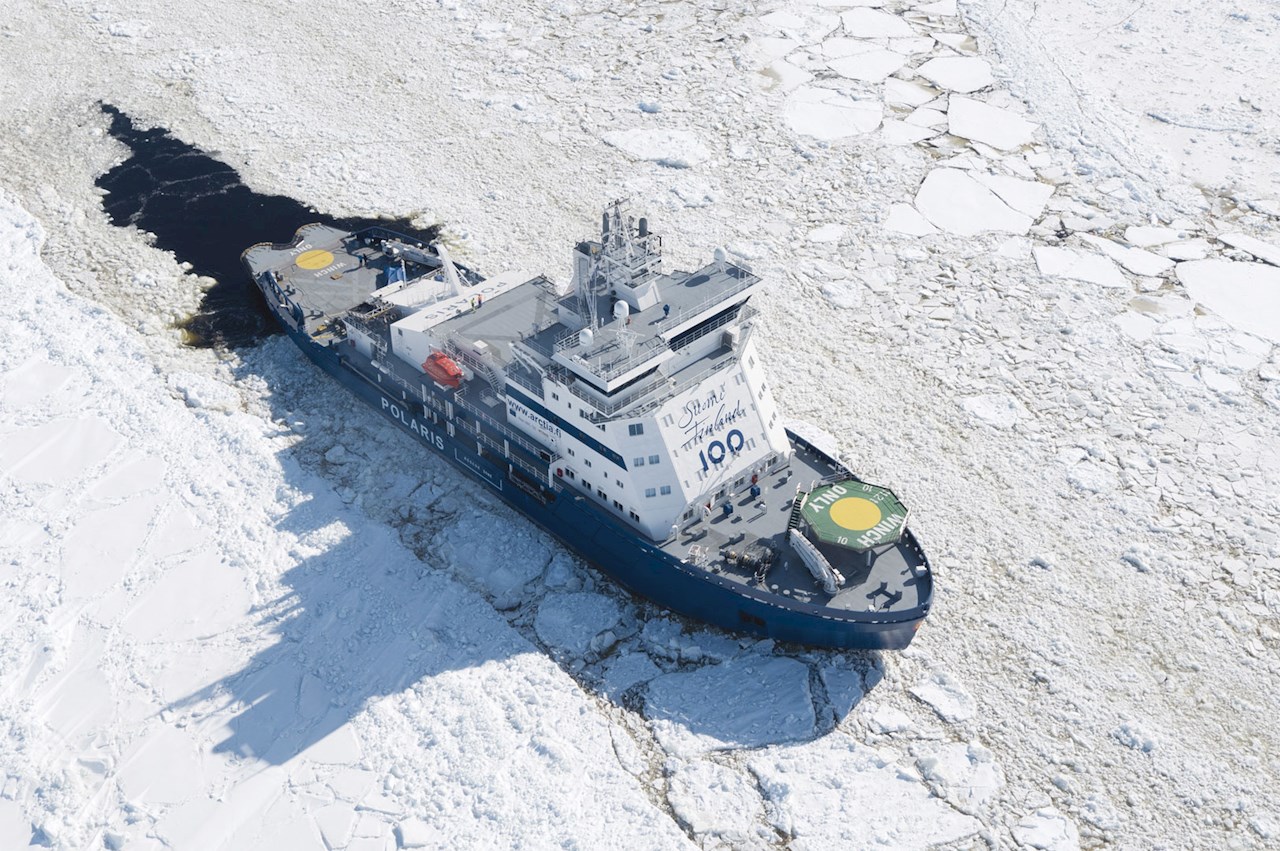
A master’s praise
Polaris Master Pasi Järvelin was asked to report from the bridge on the performance of the Polaris in its first months at sea, including the official ice trials in the Bay of Bothnia, completed on 25 March 2017.
How have the ice trials gone this winter?
In normal winters, ice conditions are worst at the end of March, so these dates were chosen beforehand. The thickest ridge ice during the sea trials was measured to be 12 metres (9½ m below and 2½ m over sea level). We didn’t have any difficulties steaming through those ridges at good speed, and without any stops.
Did Polaris distinguish itself in any way in particular?
Polaris is much more agile than any other icebreaker. This is not only due to the dual aft Azipod thrusters, but also the bow-mounted Azipod, which has proven to be an excellent aid for manoeuvring in ice.
What is it about LNG as a fuel that makes the biggest difference compared to MFO?
LNG is more environment friendly compared to Marine Fuel Oil, though we can also use Ultra Low Sulphur Fuel Oil as needed. More importantly, LNG hasn’t forced any restrictions on manoeuvring.
The height of the LNG tanks has also raised the bridge height above water. Is this an advantage or a disadvantage?
The height difference compared to other Finnish icebreakers is just under two metres. In extreme foggy weather it might be better to be lower in order to keep direct sight of the assisted vessel, but normally height is an advantage, allowing a better view of the ice field ahead.
The bow-mounted Azipod is said to have improved performance considerably, especially when towing. Can you elaborate on these improvements?
The bow-mounted Azipod unit gives much better performance, especially when going around the assisted vessels in order to ease ice pressure. When towing I myself prefer to steer with the bow Azipod, but some officers have chosen to stick to their old style.
The Urho-class breakers are now legendary. Will the Polaris someday become a legend too?
Urho-class vessels are still very useful and capable, but they are more than 40 years old. The engineers have devised so many improvements during these decades, that for me, Polaris already represents a legendary innovation.