How will a variable speed drive (VSD) system respond to sudden changes in its operating conditions? What is the potential risk of damage to an asset if the source and or the load change? Until now, questions like these have bedeviled engineers and forced companies to build and test expensive models. Now, however, ABB’s medium voltage drive simulation twins (ST) can remove the uncertainty and risk associated with testing live hardware and ensure that nothing detrimental happens to a real-world system →01.
Peter Al-Hokayem, Ulrich Schlapbach, Federico Bertoldi, Pieder Joerg Innovation Team Motion Services, Turgi, Switzerland, peter.al-hokayem@ch.abb.com, ulrich.schlapbach@ch.abb.com, federico.bertoldi@ch.abb.com,
pieder.joerg@ch.abb.com
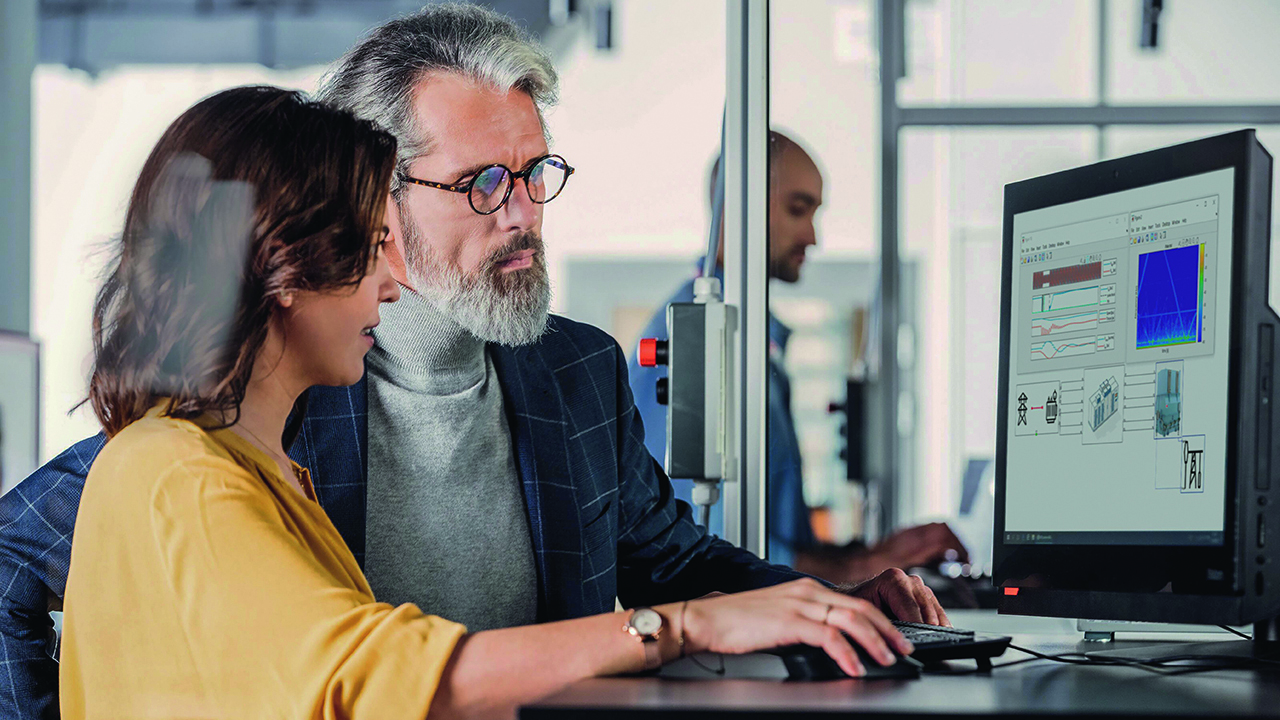
Variable speed drives are the backbone of industrial applications, transportation and energy infrastuctures – in short, most major mission critical applications →02. But with the focus generally being on the power conversion process (AC to DC and vice versa) it is easy to lose sight of complex system interactions →03 and concentrate on a single electric drive. In view of this, engineers are turning to simulation twins as the solution of choice to assess, validate and improve plant-wide performance.
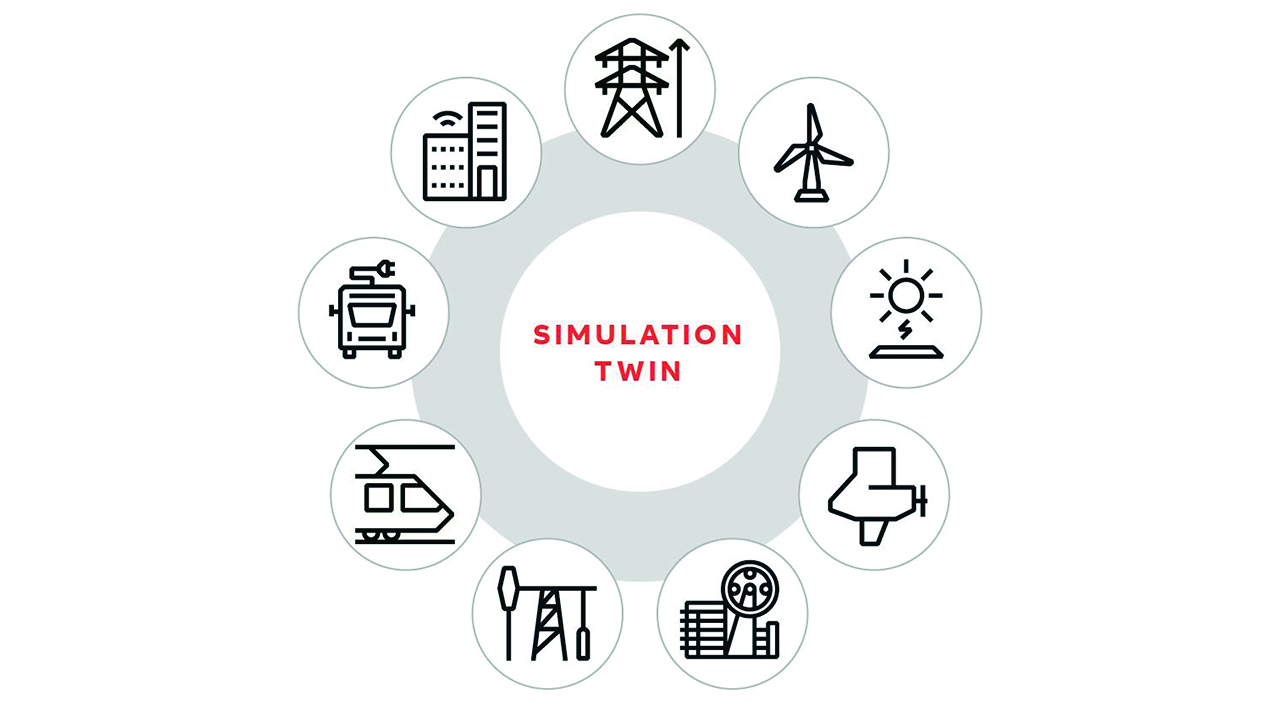
A simulation twin is a complete and operational virtual representation of an asset, subsystem, or system, that combines digital aspects of how equipment is built with real-time aspects of how it is operated and maintained. STs provide a safe environment to de-risk new drive system installations, expand existing plants and modernize installed equipment to the next level of performance. Be it for complex string testing, optimizing drive parameters, studying the interaction between drives and other electromechanical components, or performing power flow analyses, ABB has developed a wide spectrum of ST solutions that can match customer needs.
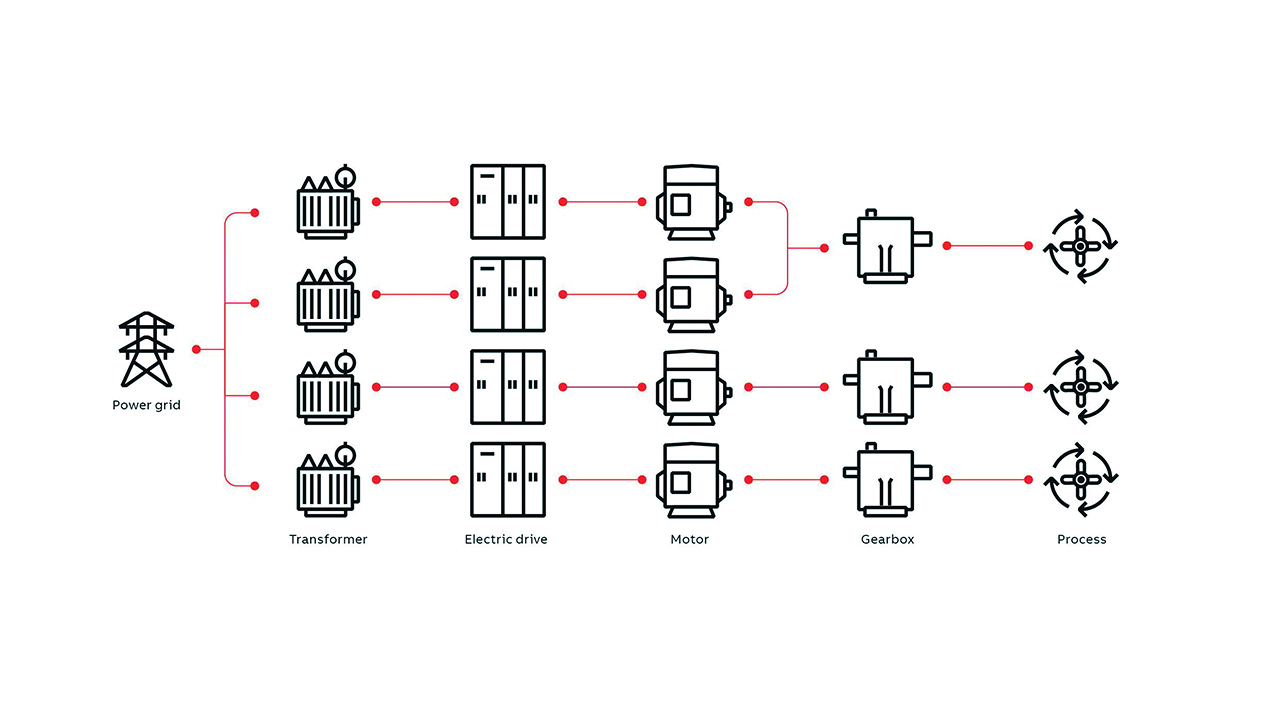
Comprehensive offering
Using a simulation twin in place of a real drivetrain system avoids excessive set-up and pre-tuning costs. It mitigates risk since any faults merely halt the simulation twin, thereby avoiding any damage that might otherwise have been inflicted if real equipment had been used. Furthermore, training of personnel to understand real hardware is simplified and less costly.
Simulation twins can also be offered as a service, whereby ABB carries out the drivetrain analysis and delivers a ready-to-use package to the customer. Alternatively, a simulation twin can be supplied to customers who wish to perform their own simulations. Whichever option is chosen, ABB experts can help determine the right solution.
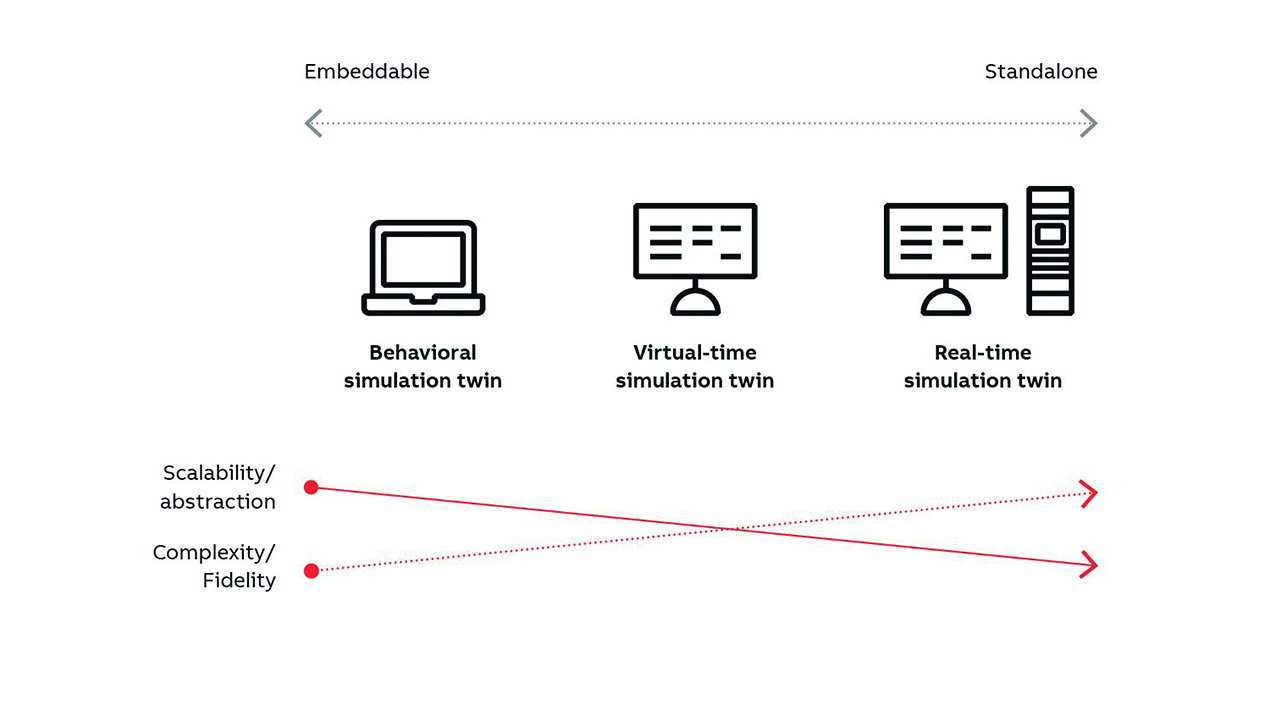
Three simulation twins are available for medium voltage drives →04, each of which can be scaled according to the complexity of the drivetrain application and the depth of the required testing:
• Real-time simulation twin
• Virtual-time simulation twin
• Behavioral simulation twin.
These solutions present the perfect tradeoff between modelling complexity, fidelity to the real systems they represent, and portability. In each case, ABB experts support customers in picking the solution that best meets their needs.
Real-time simulation twin
At the heart of ABB’s offering is the real-time simulation twin →05. This solution represents the closest physical and behavioral replica of the customer’s installed asset. It is typically used in high-risk environments such as oil and gas facilities and in testing facilities where safety and the time associated with trialing equipment could prove prohibitive. The real-time simulation twin comprises a modular cabinet that provides a live, one-to-one representation of the drivetrain control and protection hardware and software. It also provides a high-fidelity simulation of the physical system, including grid, transformer, drive, motor and process. Moreover, it can be interfaced to an overriding system emulation or another twin installation. By pre-testing and verifying a complete drivetrain system, the real-time simulation twin de-risks and speeds up the entire testing process, providing results that are the closest possible to those of its real system counterpart.
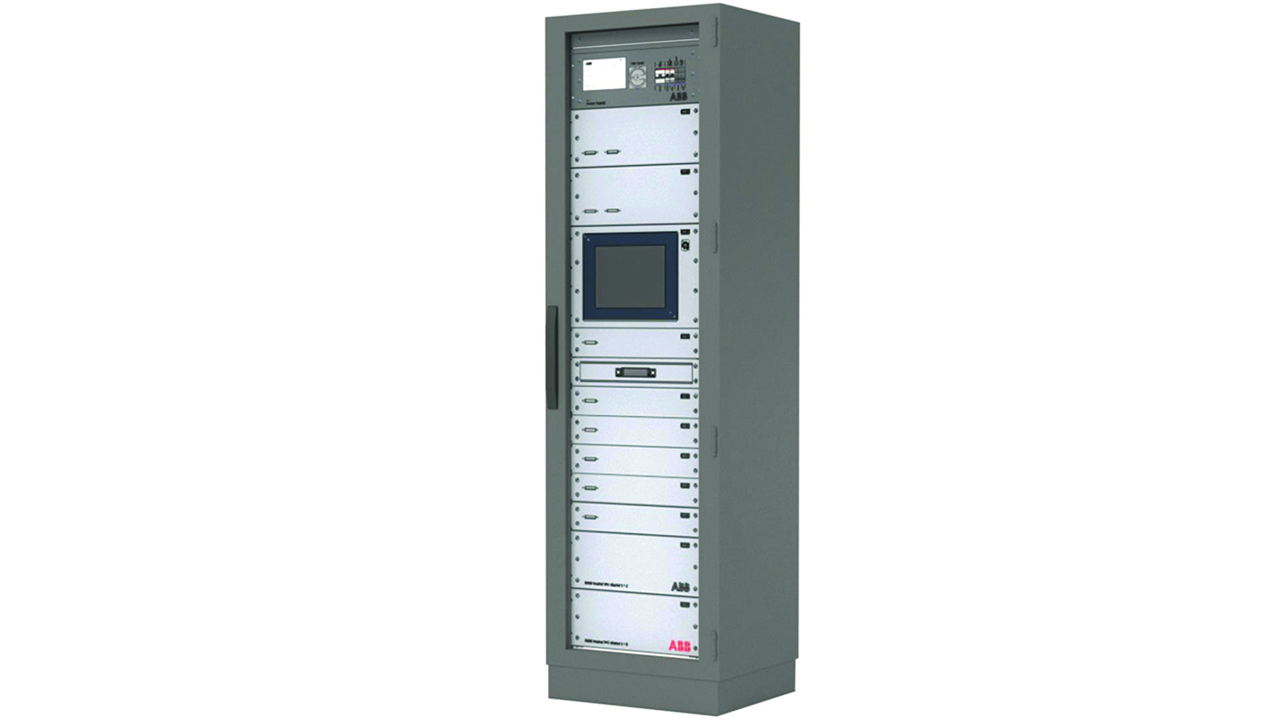
Virtual-time simulation twin
The virtual-time simulation twin is a PC-based equivalent of the real-time version. Here, the control hardware and software, as well as the physical drivetrain system, are fully simulated. This twin, therefore, operates in virtual time as opposed to the real-time response of a physical system. It is an ideal solution for customers in any industry that can benefit from a plant-wide analysis or assessment, especially when testing new concepts before a project is installed. It is also suitable for training personnel to understand the functionality of a real drive system and to operate equipment. The virtual-time simulation twin can be seamlessly scaled to multi-drivetrain system installations.
Behavioral simulation twin
The behavioral simulation twin provides a standalone software model that simulates any customer-defined abstraction of drivetrain functionalities, such as simplified system models and control layers. These models can be embedded into a larger simulation, for example, where power grid analysis is carried out, comprising several drives that are part of a complete network. This version can be scaled up to several hundred units and seamlessly embedded into a larger simulation environment, such as Matlab/Simulink or Power Factory, in the form of a functional mockup unit (FMU).
Assessing which twin to choose
The first step in determining which ST best suits a customer’s needs is a thorough assessment. As part of the solution development process, prior information regarding the installation is integrated into the solution. This information considers factors such as onsite operational experience, grid behavior, process requirements, and operational needs. Once the assessment has been completed, a decision is made as to which ST solution will be needed. Subsequent to this, ABB specialists model the solution, adapt the solution’s software to the customer’s setting, deliver the solution, and train the equipment’s users →06.
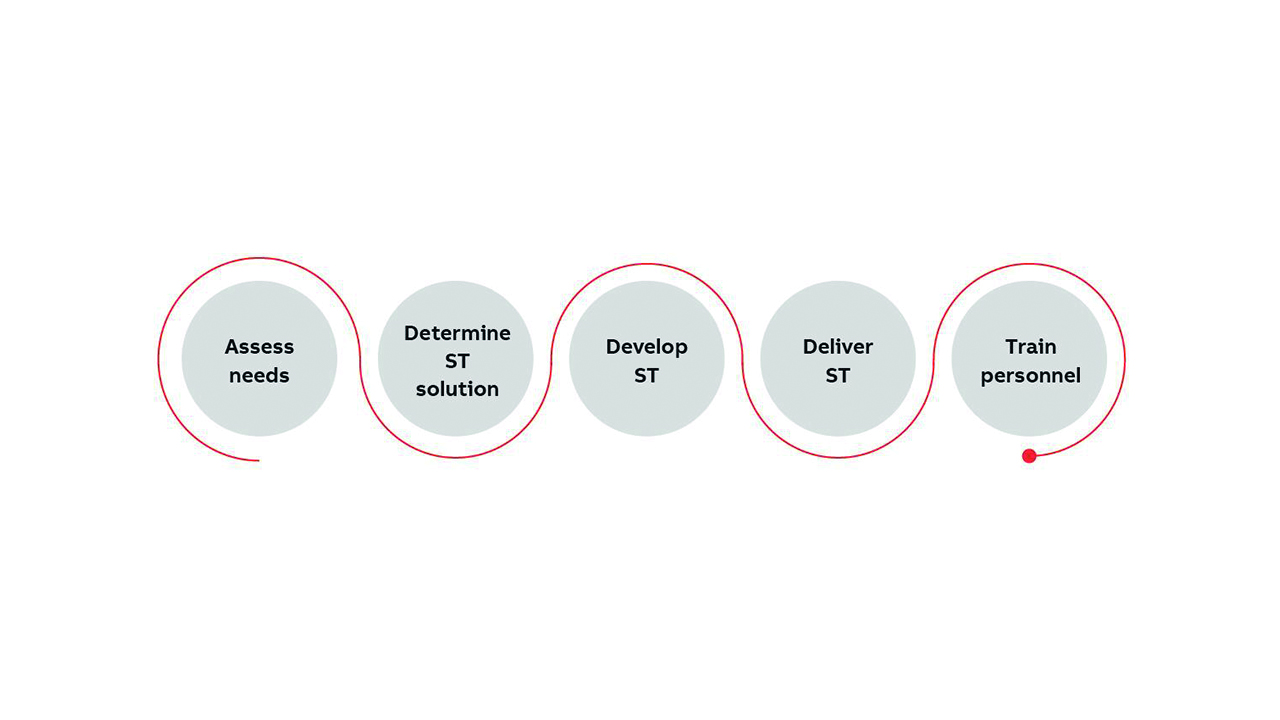
Application example 1: low grid-voltage ride-through
As mentioned above, simulation twins offer a range of advantages when planning and upgrading energy and power conversion infrastructures. With the growing complexity of grid requirements and the increasing demand for power quality on installation sites, operators are often interested in analyzing and optimizing the behavior of a drive system in terms of its transient grid behaviors. For example, low voltage ride-through (LVRT) →07 is a typical metric for which conditions cannot be readily generated onsite during commissioning. Here, STs can offer the perfect environment for safe investigation and tuning of system behavior to such events.
07a Line voltage 07b Delivered torque 07c Process speed
07 Example of a low voltage ride-through behavior on MEGADRIVE-LCI: After a drop in line voltage, delivered torque to the process is reduced, resulting in a process speed transient dip.
Application example 2: electromechanical system interaction
Variable speed drives are a key enabler of higher efficiency operations in processes based on rotating equipment – processes in which the interplay of electromechanical systems is usually so underplayed that it is lumped together as the inertia of the full drivetrain. In this case, STs can be used to simulate the drivetrain elements →08 to an extremely high degree of fidelity and hence provide detailed insights and understanding regarding various system interactions and effects on and from the grid. An example is the analysis of the torsional oscillations →09 resulting from a process speed ramp-up along any segment of a drivetrain. Once this has been achieved, STs can be used to optimize tuning of the associated controller parameters with a view to minimizing mechanical vibrations →10.
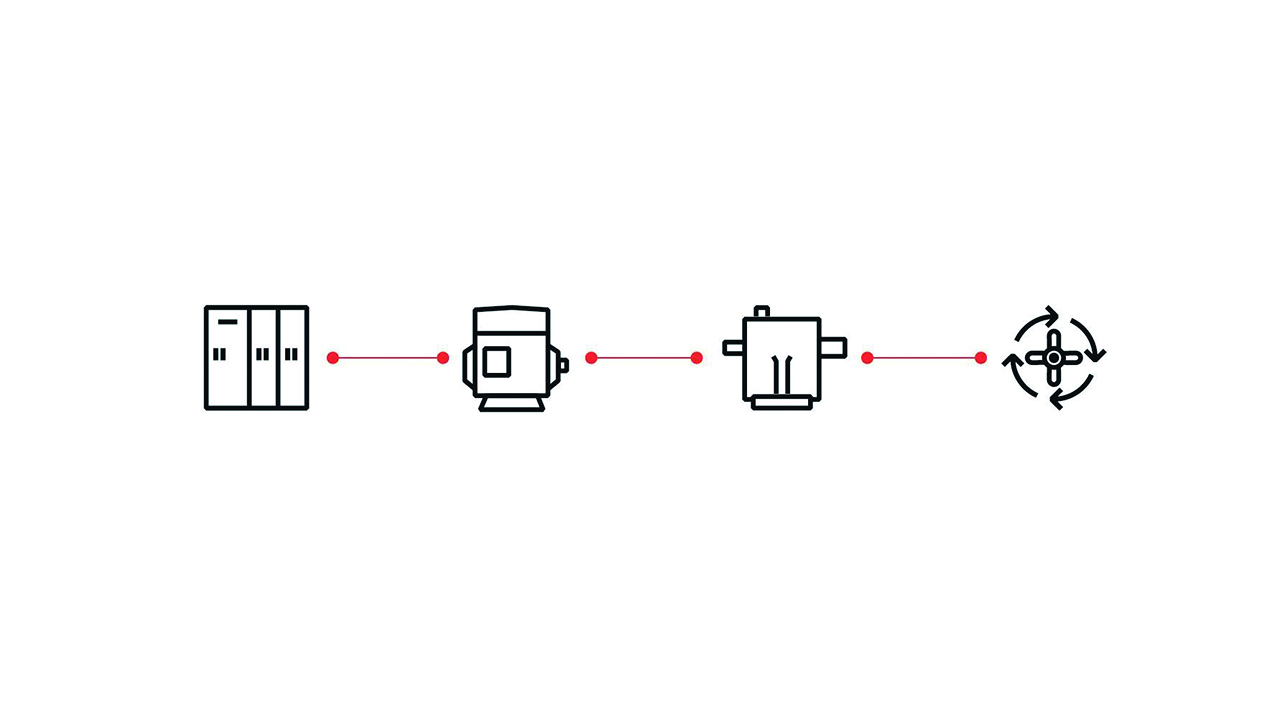
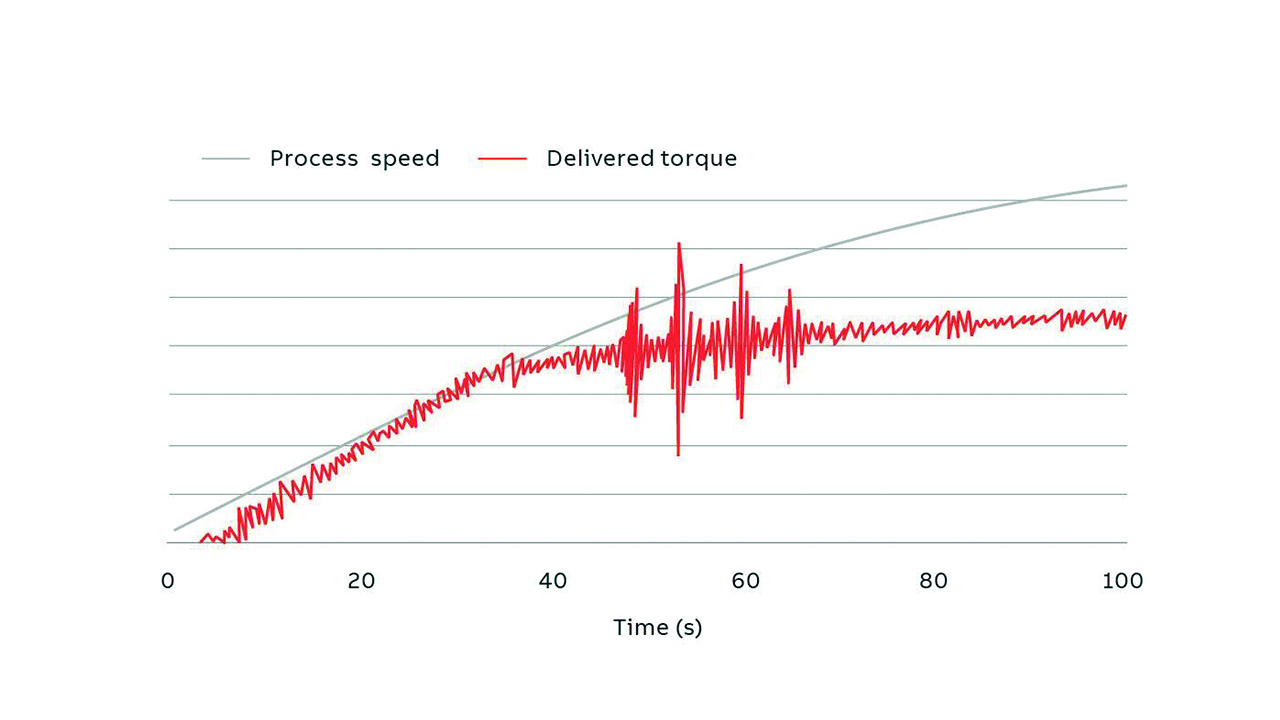
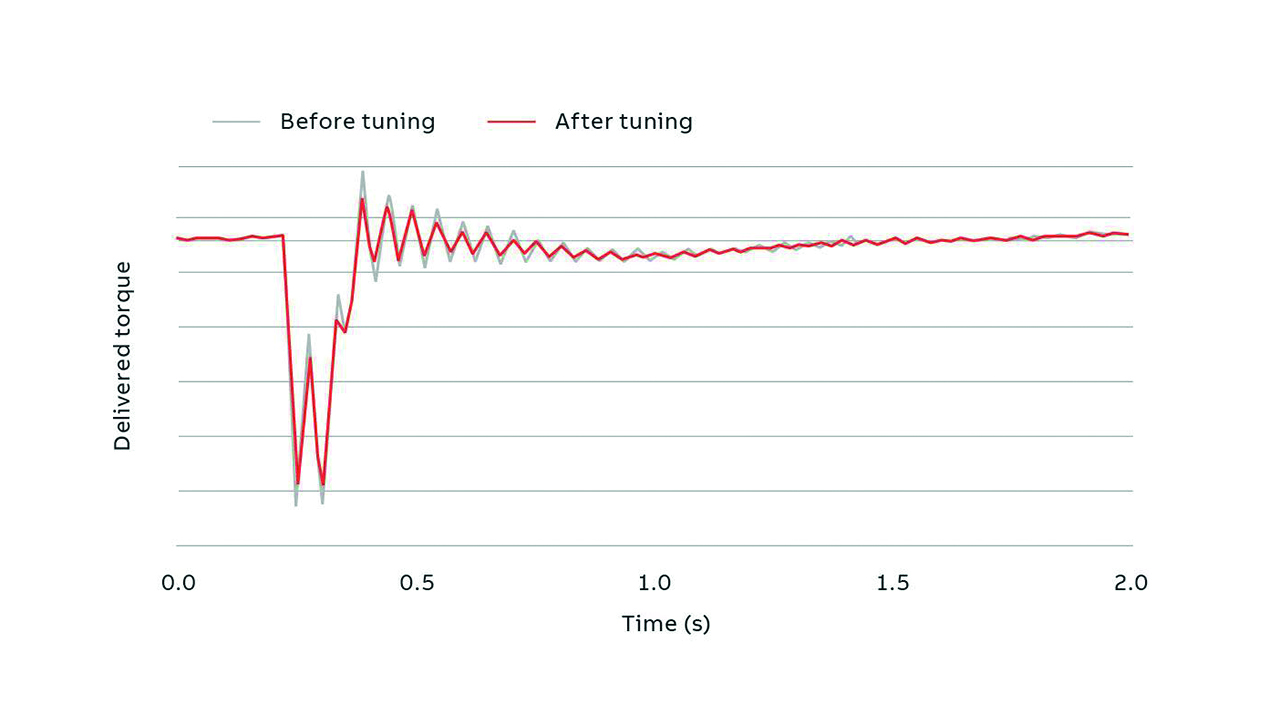
Advantage 1: Rapid anomaly identification and resolution
Maximizing uptime is a key requirement for mission-critical applications. STs can play a major role in this regard by resolving onsite issues in an efficient way. For instance, given data logger information on an issue →11, a scenario can be replicated in a one-to-one fashion using an ST, thus providing a high level of insight into the time-series signals from the twin model and the twin software. Experts can then evaluate the information and recommend the fastest path to resolving the issue.
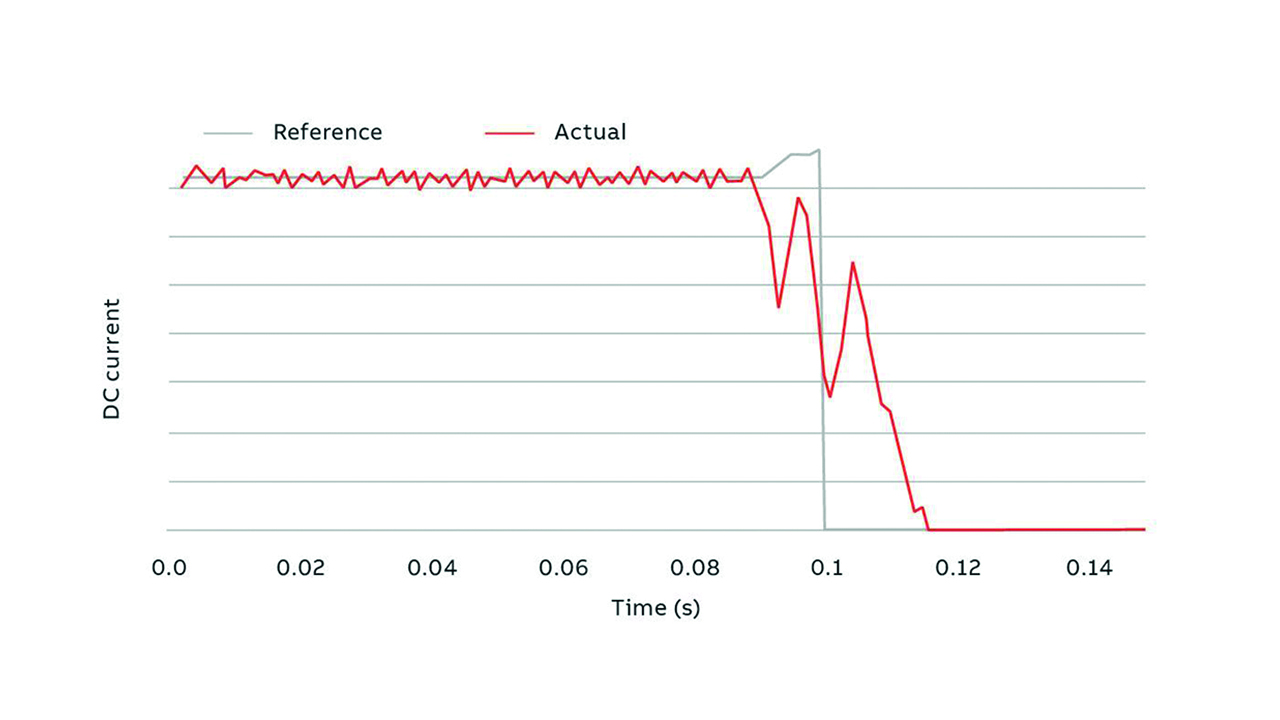
Advantage 2: Integration into larger simulations
Behavioral or virtual-time STs are ideal for investigating power grid behavior in connection with disturbances, particularly because large 10 – 100 MW VSD loads can be a key player in overall grid behavior. For example, several versions of STs in the form of functional mock-up units (FMUs) can be integrated into larger simulations in order to investigate events such as load flow anomalies, short circuits and harmonic network behavior.
Advantage 3: Training
STs can significantly accelerate the hands-on experience and operational knowledge of technical personnel →12. Employees can gain vast knowledge and explore a range of operational scenarios using STs, all in a safe environment. For example, it is possible to extract and visualize many signals from a system model and/or control software to gain better understanding of the various modes of steady-state or transient behavior of a drive system or fleets thereof.
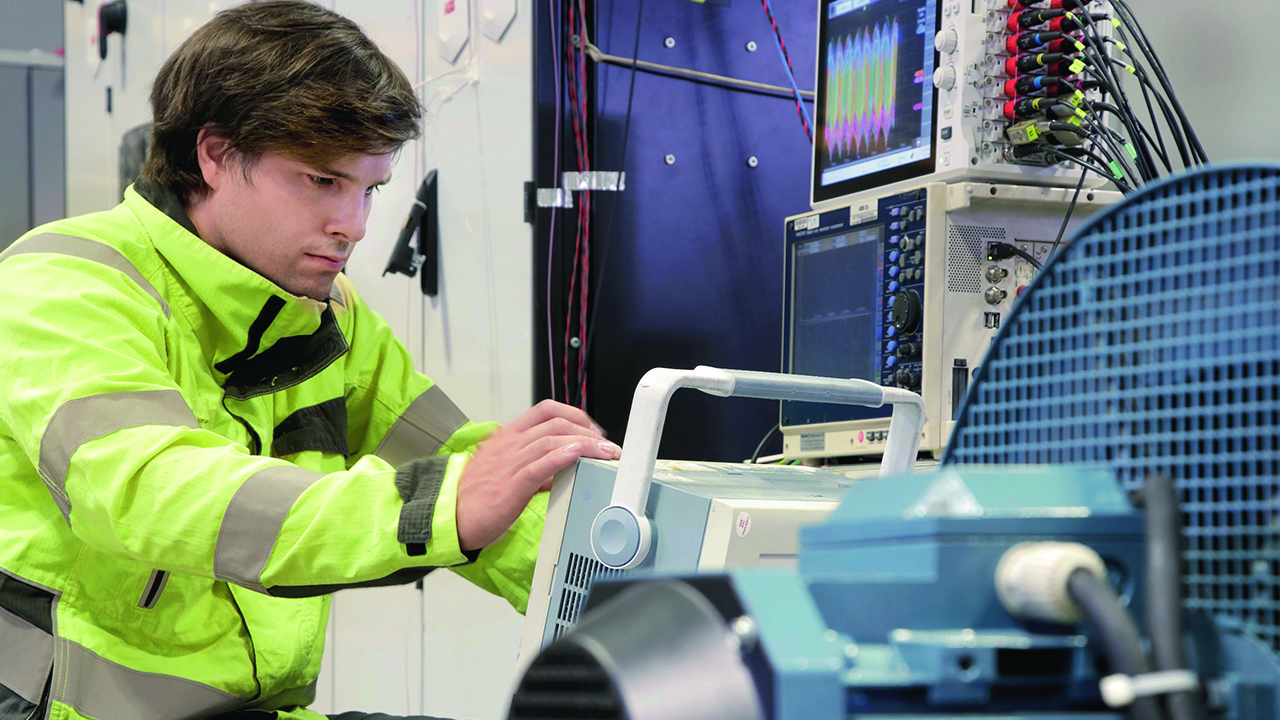
Conclusion
As variable speed drive systems and their associated processes become increasingly complex and as grid standards become more and more demanding, simulation twins can become the solution for assessing and improving their performance. Furthermore, as their underlying models are refined over time to provide a perfect replica of installed equipment, simulation twins can become the building blocks of each new installation.
Looking ahead, simulation twins will be trained online using streaming data and used to detect anomalies or impending plant failures. This will open the door to better planning and much higher levels of plant availability.