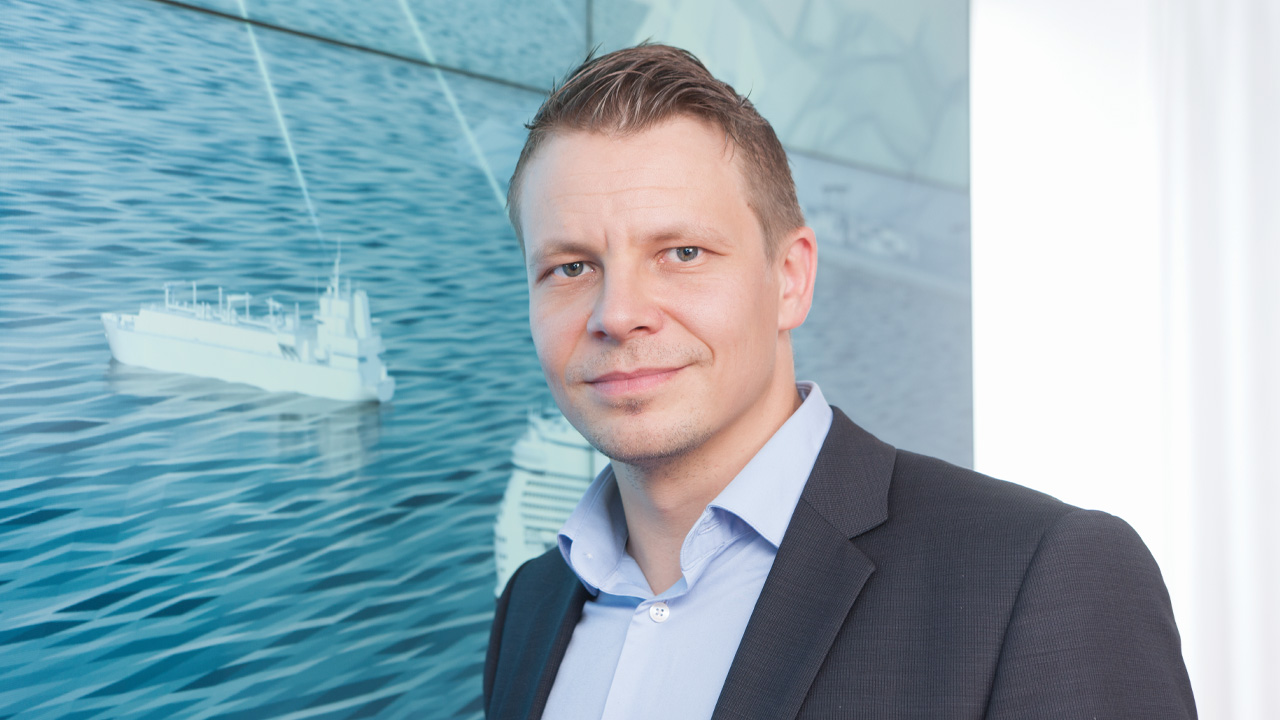
It is a vision fuelled by relentless and rapid developments in technology, but tempered by human nature. “Technology will appear in and invade every link in the value chain,” Tervo says, “from developing and making, to experiencing. The flow of information will transform the ability of systems.”
But for this to be realised requires open platforms and sharing, and that demands the most human of elements: trust. “Shipping 4.0 embraces open systems, but it can only happen on a broad scale if all the players in the picture are willing to trust what their data is telling them.”
While binary data may be absolute, Tervo observes that trust is intangible. “Some achievements come only through experience. In many ways it’s the same as with self-parking cars. At first you might not trust the technology, but once it has proven itself, you trust it more than you do your own abilities.”
For ships, the “self-parking” system utilises data from multiple sensors to create a dynamic picture of the vessel and the surroundings. The ship’s state of motion is visualised in relation to the static and dynamic objects around the vessel to help the operator in controlling the ship.
“At the moment there are people on land as well as on deck who shout instructions in a walkie-talkie for the captain who does not have full visibility of the ship.” Once the crew learns to trust the assisting solutions, Kalevi says, those can be utilised as part of closed-loop control to perform automatic operations. “But it requires trust that the machine can see better than a human can see – and without human error and fatigue.”
We can make a ship react optimally.
He relates back to the early days of computers in shipping: “It was the same when we introduced digital technology in the marine business. Our clients only trusted the naval architect. They didn’t believe in the computer. But once they experienced the benefits, they came around.” There will always be someone willing to take those first risks, he says. “Then the rest will follow with smaller risks in order to reap a larger benefit.”
In data we trust?
But trusting data-driven performance also requires trust in the quality of the data. There are ways to cultivate this trust, Tervo says: “The first is to evaluate the quality of the data and make sure it is reliable, or take steps to make it reliable. Then there are redundant data sources to avoid having to rely on a single source. Continual diagnostics can also be run to ensure an uninterrupted supply of healthy data.”
When all this is done, data can often give a more reliable view of a situation than humans. “Through machine learning and artificial intelligence, machines can recognise objects and situations that they have never actually encountered,” he says.
Empowered by this technology, Tervo points out that ABB has the ability to control all the ship’s systems, from autonomous control to new digital services, to engine and control room design, to power train efficiency systems. “We have progressed in all these areas, to the point where we can build entire integrated ships systems, from bridge to propeller.”
ABB is currently developing a novel control system for dynamic positioning, manoeuvring and open sea operation to help the crew to control the ship more intuitively, safely and with higher efficiency. “The solution enables the user to focus on controlling the ship, while the system takes care of which assets are used to perform the control.” He notes that current solutions do not fully utilise the manoeuvring potential of ABB’s Azipod propulsion system. “But we know how Azipods work, we know how the ship reacts to changing impulses from the unit, so we believe that we can create a unique product for controlling a ship with Azipod propulsion.”
Technology is helping us understand what the user’s role will be in the future.
“We can make a ship react optimally, telling it how and when to generate and consume power, where to navigate, and how fast to steam. We are ready to take this from the planning stage to reality, but ABB does not expect to do everything alone.”
Better together
Working from a holistic perspective, Tervo says that ABB sees the need to understand the customer’s value proposition, acknowledging that each client has specific needs, and working with them to fulfil those needs. “There is still room for considerable improvement. Our next move will be from advisory services to closing the loop of decision making, and this will require even better customer insight. With this, we can help them calculate predictions, optimise resources, and connect this knowledge to actions.”
Data from operations can also be used to make decisions at higher levels, he says. “We can enable strategic changes in operations. This gives connectivity more added value. We are learning to use our experience to connect the dots, to complete the picture of overall benefit.”
“Technology is also helping us understand what the user’s role will be in the future.” This, he maintains, is necessary in order to respond to changing roles in the value chain: “Retailers like Amazon already have their own logistics services down the entire supply chain,” he observes. That in turn moves the supplier’s products and services down in the value hierarchy, and increases the importance of the retailer.
Regardless of how disruptive this may seem to original equipment suppliers like ABB, Kalevi Tervo assures that the move toward intelligent shipping will be sustained by the same basic principles that have always driven quality OEMs like ABB: “Our goal will always be to increase customer value, to provide maximum benefit from the application of technologies.”