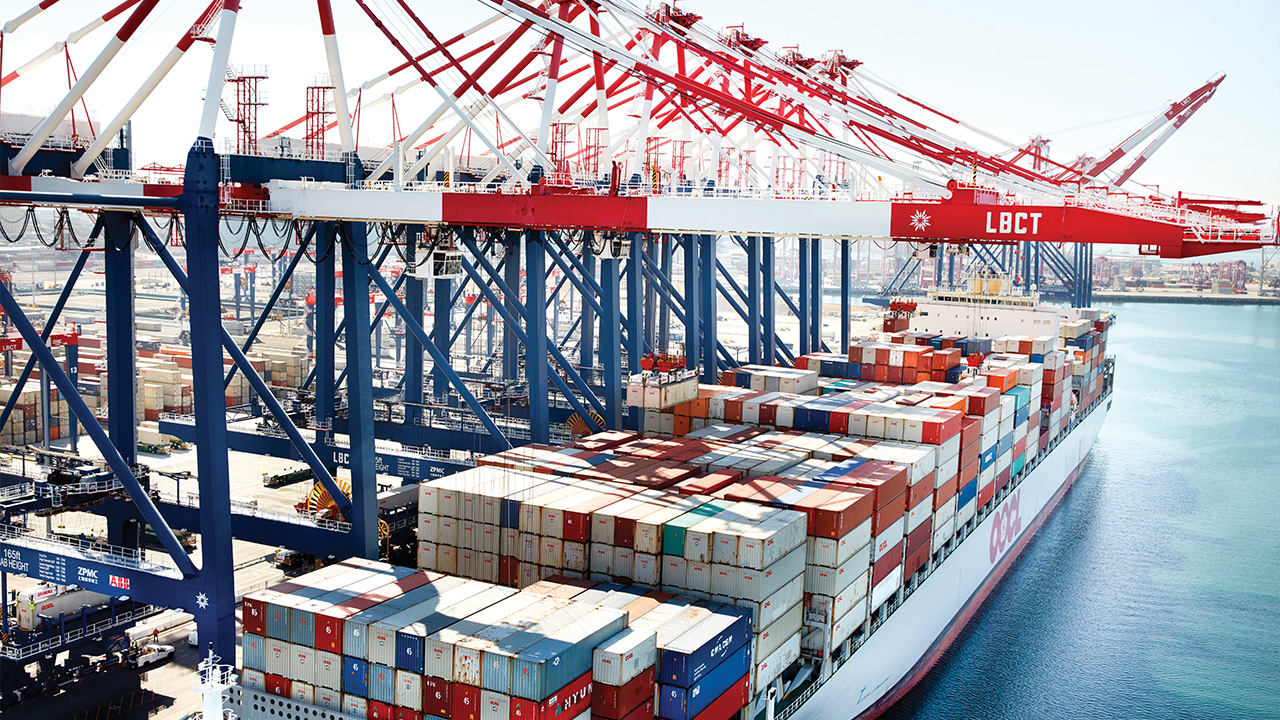
But at the end of the journey, when you are able to say you have achieved your goals, you most likely will feel it was all worth it. Long Beach Container Terminal (LBCT) is writing the future, together with ABB, by being the first fully automated container terminal in the United States.
Anthony Otto, President of LBCT, relates that he started on the project to develop and build the terminal about ten years ago. “When it all started, it took many different forms, and it did not look exactly like this,” he says, pointing out that his terminal has been in commercial operation for about one and half years now. But the vision was always clear: “What we have achieved here is a paradigm shift in our industry, here in Southern California and in the United States,” he says. The terminal is fully automated, and operated in a completely different way than the conventional terminals surrounding the new crown jewel of US container terminals.
What we have achieved here is a paradigm shift in our industry, here in Southern California and in the United States.
When meeting Mr. Otto and his crew at the new terminal, it is easy to see that everyone working at LBCT is proud of their workplace and the achievements they have accomplished. It seems that being part of a truly ground-breaking effort creates strong bonds between the people who share that experience. Perhaps they have formed the dream team that will ensure the success of the terminal for years to come?
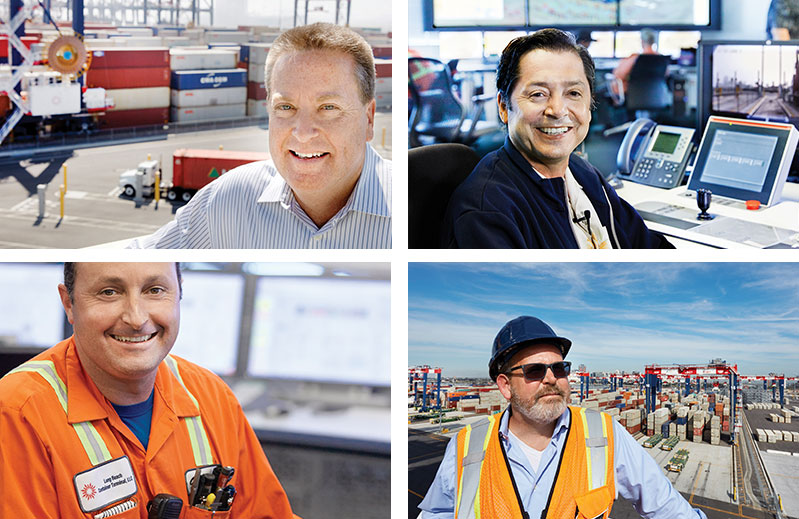
At the forefront of technology
Otto says his team searched for the best technologies and travelled the world to see different solutions in operation. The ultimate goal was to find the best possible solution for their new terminal, and to be able to build a terminal at the absolute forefront of technology.
It soon became evident that automation was the way to go, and as a result, LBCT became the first fully automated terminal in the US, employing automated cranes and automatic horizontal transportation.
When it comes to crane automation, the choice of partner to undertake this major development was clear early on – the partner would be ABB. “ABB has the necessary experience, and they are the leading supplier of container terminal automation,” Otto confirms.
As a result of that choice, all the cranes at the quay, the yard and the on-dock intermodal yard are equipped with ABB’s automation solutions. The quay cranes also have a crane OCR system from ABB for automated container identification and detection of door direction.
The first phase of the terminal with 1MTEU capacity went live in April 2016. LBCT is serving megaships and calls that many times require around 10 000 moves to be performed by the STS cranes alone. When the last phase of the terminal is completed in 2021, the designed capacity will have reached fully 3,3MTEU, making LBCT the largest container terminal in the United States in terms of capacity.
The first near-zero emission container terminal in the United States
Bucking a trend of most new major container terminals, LBCT is located very close to the city of Long Beach. So how is this possible? “To be allowed to proceed with this project we went through a very long, difficult EIR, an Environmental Impact Study to make sure that the impact of this facility on the rest of the city, downtown and the surrounding communities was kept to an absolute minimum,” Otto explains.
The new terminal, including all cranes and horizontal transportation, is electrically driven. Add to that all vessels calling LBCT are required to utilise a shore power connection for ships during berthing, and Otto concludes: “We are happy now to say that we are the first near-zero-emission container terminal in the United States.”
In top shape at all times
In an automated terminal, maintenance plays a key, even critical role, says Jim Jacobs, General Manager of Maintenance and Repair at LBCT. “In this environment any piece of equipment can be called on to service a customer anytime. For this reason, we rely on predictive maintenance rather than breakdown repairs. This requires maintenance activities to be communicated closely with the operations team at all times,” he says. “In a conventional terminal you can let a few things go, but in an automated terminal you have to keep the equipment running in top shape to reduce, or even eliminate, the interaction between man and machine. In an automated terminal the operations group needs predictability and reliability.”
Automation has greatly changed maintenance duties.
This scenario of changing times in maintenance is confirmed by Maintenance Engineer Giuseppe Giannola who works with maintenance and repair of all the stacking and STS-cranes: “Automation has greatly changed maintenance duties. It includes new challenges and requires new skills as the duties are now more technical, computerised and software related. We also have much more coordination with other departments regarding access to the equipment. But the goal remains the same – keeping the cargo moving and minimising downtime.”
To support the maintenance of an automated terminal, ABB has delivered some new tools to LBCT. “One example is the overview table that shows all the lifting equipment in the terminal. That allows us to proactively spot problems as they arise, and centrally dispatch the maintenance,” Jim Jacobs says. “We can use the overview table to take care of many warnings, faults and problems that come up, and many of them can be solved efficiently from the control room, which helps keep things moving,” Giannola adds.
“This is real teamwork”
In the heart of an automated container terminal, the control room, we meet a happy crew of crane operators. Here the team from ILWU Local 13 is remotely handling confirmations and exceptions for LBCT’s fleet of fully automated stacking cranes, a relatively new phenomenon in the US.
The stacking crane operators at LBCT are experienced crane drivers and have worked in traditional yards driving the cranes from a crane cabin, so they know what they are talking about. With 20 years of crane driving experience, Eric Gonzalez says his work at LBCT is completely different compared to his previous jobs. “I describe my duties as babysitting the cranes, because we are sitting up here in the control room overseeing the whole fleet of cranes out in the field.”
The operators appreciate the technical capabilities and responsiveness of the ABB systems, but they also emphasise the benefits of the new working environment, and how it allows them to become a real team.
It’s easy to understand that the new working environment is a big change. In conventional terminals, crane drivers work under harsh conditions, which in turn presents a challenge when recruiting future port professionals.
The crane operators at LBCT say that simple things really do matter; things that office workers take for granted. Like working in a clean environment, being able to take a short break to get a cup of coffee, or just getting up to move around. The flexible and ergonomic Remote Control Station also allows working sitting and standing up. “Now I can rest my back, and basically live a healthier life,” Gonzalez says.
But there is more to the control room at LBCT. More than being the “crane operators’ office”, it is the focal point in keeping the containers moving. At LBCT, the clerks and part of the maintenance crew are also stationed in the control room with the operators. In talking about the benefits of working in such environment, another very human aspect quickly pops up: communication.
Communication between people is not always easy, and using radios or sending your message via a third person does not make it easier. According to people working with operations and maintenance at LBCT, the shared control room makes communication much easier, more efficient and more direct, reducing the risk of misunderstandings.
When it comes to communication, it is not only the task at hand that needs to be addressed. Communication is also the key element in building relationship and teams. Having the possibility to work in a shared control room helps crane operators, maintenance engineers, clerks and supervisors get to know each other. The person “at the other end” is no longer just a voice on the radio. They are a colleague you get to know, maybe even a little about their family or the names of their kids. Before, you might never even have met.
All this facilitates collaboration between people, and that has a positive impact on productivity. “This is real teamwork,” says Giannola.
The future of LBCT has begun. The terminal is on course to combine two aging terminals into a new terminal that is safer, greener and more productive than its predecessors. There may be no better way to put it than Giuseppe Giannola does: “This is a great place to be.”
ABB has made two videos about LBCT. To see them, please click the video tiles below.
FACTS ABOUT THE CRANES AT LBCT
STS cranes with world leading lifting power
Lifting capacity up to 130 tonnes
Automation enables efficient utilisation of various dual and single hoist configurations
Lifting height up to 50,3 meters
Main trolley speed 240 m/minute and hoist speed up to 180 m/minute
Fully automated container handoff and detection of door direction with Crane OCR
Fast and efficient automatic stacking cranes
Stacking 6 high, 9 or 10 wide for optimised utilisation of yard space
Gantry speed up to 240m/minute and hoist speed up to 120 m/minute
High precision stacking
Automatic landing and pick up of containers on AGVs, terminal chassis and road chassis
On-dock intermodal yard cranes
Automation functions similar to automatic stacking cranes
Designed to operate over eight tracks
In operation 24/7