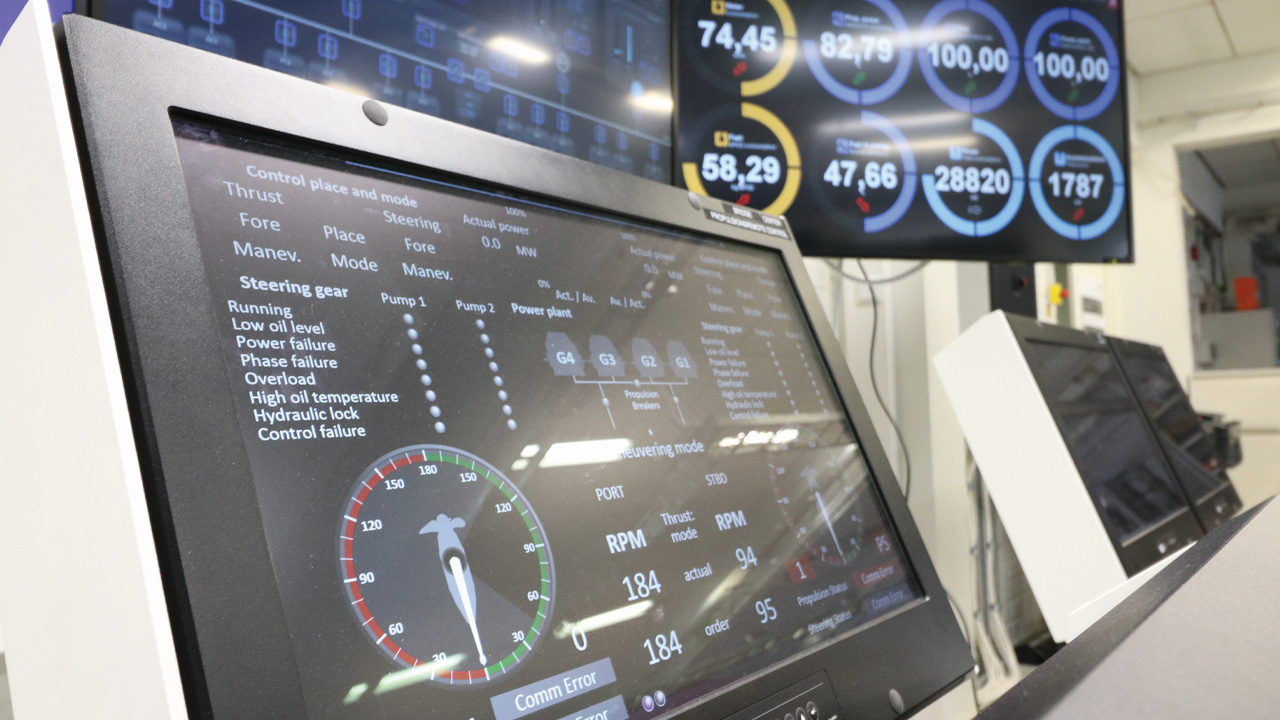
The systems are then connected together to operate as a single system on board a ship. This usually leads to a situation where these products or subsystems perform well independently, but when evaluated as a single complete system (with many interfaces between subsystems), the overall performance leaves room for a fair amount of improvement. Often, the first opportunity to fully test and evaluate a complete system is only after installation and commissioning on board a ship, during harbour trials and ultimately during sea trials. Should failures or quality issues occur during these late phases of ship building, they can have serious consequences and interruptions to prescheduled processes of ship builders. In the worst cases, this can result in significant delays in deliveries, thus causing major monetary losses to the ship builders.
To improve this traditional way of engineering automation systems on board a ship, ABB has previously opened a new high technology facility called the Integrated Marine Systems (IMS) laboratory. A part of this laboratory is shown in Figure 1, where an ABB remote control system (RCS), Vessel simulator, Remote Control Unit (RCU) and Azipod® Interface Unit (AIU) cabinets can be seen. In its entirety, the lab contains the key components of ABB’s marine technologies including automation, RCS, propulsion, integrated operations and waste heat recovery systems. The laboratory is designed to efficiently meet the needs of the customer and enables close working between ABB and customers already in the earlier phases of system design.
To go one step further and include the transient and dynamic characteristics of the electrical power systems into the IMS test environment, ABB has now expanded the laboratory with low level power electronics controllers and protection devices (i.e. protection relays) together with real-time simulation devices. In this new setup, all electrical and automation subsystems of a ship are integrated into a complete system that exists in a controlled environment in an ABB laboratory. Such an environment allows testing of full systems even more effectively, and ensures that the delivery processes, quality of the deliveries, and safety of the system are maximised.
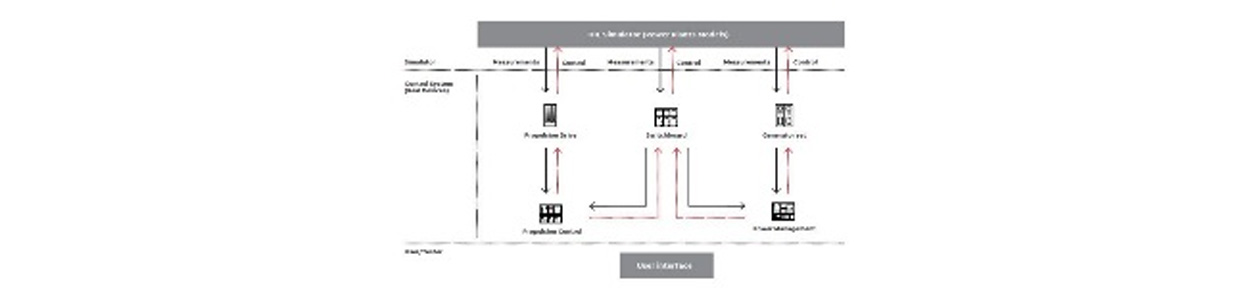
This article describes how ABB’s integrated system testing methods can improve the overall system efficiency and quality of ABB Marine solutions. The IMS electrical system platform is further described and its benefits are shown. Also, a short introduction to real-time hardware in the loop simulation technique, which is used in the IMS electrical system platform, will be given.
Benefits of full system testing with IMS Testbed
Rapidly evolving technologies and increasing amount of intelligence on ships demand new methods to effectively verify the operation of complete systems. Testing of complete marine electrical and automation systems is often very expensive due to their size and complexity, and therefore the possibility to do so before the actual commissioning is extremely limited. This often leads to a situation where the interfaces between different subsystems are properly tested for the first time only after the equipment is already installed on board vessels. Therefore, it is often the case that bugs and incompatibilities are discovered at this point, leaving little time for trouble shooting without causing serious damages to other processes related to delivery. Since the IMS test laboratory already contains the same critical equipment and connections as in the actual vessel, long before delivery on board, testing and improving of these systems is possible with little effect on other delivery processes. This ensures the optimum quality of ABB deliveries and that the installed systems are safe and fully operational.
By having all critical interfaces of the low level protection and control devices connected to the upper level power management system (PMS) and the propulsion control unit (PCU) in a laboratory, the complete system can be fully tested and evaluated together with the customer already during the earlier sales and engineering phases. This enables the customer to better take part in the system design, further reducing the learning curves of both the customer and ABB. By working together with the customer on the IMS test platform, ABB and the customer can together iteratively identify customer needs and the optimum solutions that exceed requirements for these needs. This way, with ABB’s help, the customer can truly understand the problems at hand, and with the customer’s help, ABB can provide the best solutions.
In addition to testing delivery projects, the IMS test platform will be consistently used for developing new technologies. Novel technologies, e.g. variable speed engine operation, energy storage and fuel cells on board an all electric ship are both developed and fully verified on the test platform, which further increases quality by enabling more standardised product interfaces. This makes ship building processes even faster than before and shortens the time-to-market of both ABB products and customer’s final system.
Real-Time Hardware in the Loop simulation in IMS Platform
The IMS electrical system test platform is a testbed based on Hardware-in-loop (HIL) simulation technology. HIL simulation is a real-time simulation technique which can be used to develop and test complex power systems. In this technique, a real-time HIL simulator is used to build a virtual model of the power state in which real power electronic controllers and electronic protection devices can be connected for interaction. The virtual power state consists of power producing and consuming components (e.g. engines, generators, motors, converters, etc.) since the electrical and mechanical dynamics of these components can be fairly accurately modelled. On the other hand, the real equipment connected to the simulator are logic-containing controllers (e.g. protective relays and power electronic controllers). Analysing both hardware and software aspects in different situations (e.g. grid faults) is highly interesting for optimal system development regarding performance, reliability, safety and efficiency. This equipment is connected to the simulator through hardwired I/O and fieldbus communication (e.g. Modbus TCP or IEC61850 GOOSE and MMS) as they would be in a real system on board a ship. Together, the simulator and the real equipment form a simulation loop that can be used to test the operation of a complex system in both normal and fault situations.
The data obtained from the test platform is regularly compared to that obtained from real ships. This makes it possible to ensure that the results obtained from the test platform are valid and comparable to the ones obtained from the systems on board a ship. This provides ABB and their customers an efficient and valuable testing environment from which they can have access to the hardware features that would not otherwise be available in a completely software based simulation model.
IMS Electrical Systems Test Platform
The IMS electrical systems testbed contains all critical components of ABB Marine power plant deliveries. The objective of the testbed is to provide the means to test and verify all control and protection functions of different intelligent devices in ABB Marine deliveries. Compared to conventional, purely simulation based testing methods, this testbed provides the user access to both software and hardware features of the system performance.
The laboratory contains equipment as required in both conventional AC system and Onboard DC Grid deliveries. The equipment consists of ABB’s newest generation protection relays (Relion615, Relion620 and Relion630), AC800M control units, ACS880 control units, UNIREC control units, Unitrol1020 automatic voltage regulators and HIL simulation equipment. The general idea of HIL testing with ABB equipment, as used in AC systems, is illustrated in Figure 2. By combining this equipment in different configurations, different delivery systems can be tested.
A general configuration of an ABB Marine AC distribution system in IMS electrical system testbed is illustrated in Figure 2. In this configuration, starting from the top, is a real PMS which controls the virtual diesel engines in the simulation model. The PMS communicates with the main switchboard components (protective relays) using IEC61850 GOOSE protocol. Real Unitrol1020 AVRs are used to regulate the voltage of the virtual generators. The main switchboard is completely modelled using a combination of real and virtual relays. Up to seven real protective relays can be simultaneously connected to the test platform, enough to test most different system configurations. The addition of virtual relays is often interesting, e.g. in fault situations, to see how the rest of the system reacts to the fault. Continuing further, the testbed contains real ACS880 drive controllers that control the virtual frequency converters and propulsion motors. The real PCU gives references to the drive controllers. Both the PCU and the PMS are directly connected to the rest of the IMS lab equipment, e.g. RCS and automation, as they would be in a real ship.
To give a concrete example on how the testbed works, consider a situation where a critical fault happens on one side of the grid which forces the whole grid section out of operation. Once the protection relays detect the fault, they will attempt to isolate the fault by opening the surrounding breakers. Through IEC61850 GOOSE, they inform PMS and PCU to reduce both power production and consumption respectively. Once the affected grid section is de-energised, it will not go back to operation until the fault is cleared and the protection relays are informed of the clearance. Once this is done, the generators can be re-started and the previously faulty grid section can be synchronised and connected back to the rest of the healthy grid. The second propulsion motor can also be turned on again and the whole system is again fully operational. In this scenario, the functionality of the PMS, PCU, and protection are fully tested and validated using the same controller and communication protocol as in the real vessel, giving the customer higher degree of confidence in the system.
Using the same setup, the ABB team also has the opportunity to test a variety of scenarios and sea conditions, allowing verification of the seamless operation of ABB Marine systems long before building the real system on board a ship. Some of the test scenarios include grid faults and fault recovery sequences, testing of communication network performance and stability on high traffic, optimal tuning of grid components and designing and testing of novel technologies. By performing all these various tests in the earlier phases of system design, ABB can ensure the optimum quality of system deliveries by improving the reliability, safety and efficiency of the systems.