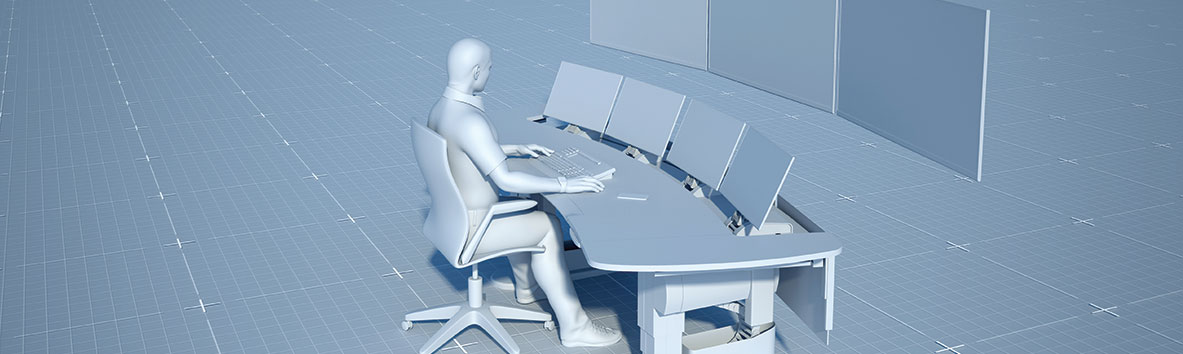
The concept
The previously conservative maritime industry is now tapping into the possibilities of connectivity and digitalisation, taking advantage of improved satellite coverage and cloud computing. Owners and operators are increasingly looking for suppliers that offer remote troubleshooting, performance monitoring, and condition-based maintenance. This allows operating the fleet at lower fuel and maintenance cost, while improving crew, passenger, and cargo safety and productivity. In order to facilitate the change, ABB is adding sensors and software to system deliveries on board vessels, improving data transfer storage, and analysis of the data. Our service centers now utilise the information to support customers in emergency situations, in maintenance planning, and in helping to optimise ship operations. The future fleet will be better connected to the owner’s shore side technical department, and to ABB’s technical departments, by having access to the same information and monitoring systems. We call this way of operating Integrated Operations. Combining the new technologies with our traditional on-call and maintenance services will enable us to be part of our customers’ daily operations and make better decisions together. Because vessels will become more complex, ship owners will want to simplify how they manage their fleet. ABB will offer customers a package that is integrated from office to propeller - provided by a partner with strong domain knowledge. This way of operating will enable suppliers and customers to take the first steps towards autonomous shipping.
A conservative industry is changing
Shipping has come under scrutiny by regulatory and environmental bodies for its environmental and safety record. Speculation in shipbuilding and slow economic growth have put the industry under significant economic pressure. The maritime industry needs to become more modern, efficient, and safe. In fact, we are witnessing how this industry is turning from being one of the most conservative industries to being open for new ways of operating.
Life at sea as we know it, is going to change profoundly. And so will the life at the office. Digitalisation will affect everything, ‘from office to propeller’. Planning, operational tasks, and decision-making will be carried out by involving more people and information, and by creating virtual teams whose members are located on board, on shore at the owners’ offices, and at the suppliers’.
One of the biggest operational improvements lies in the integration of the operations taking place on board the vessel and on the shore side, from anywhere, and with anyone who is critical to the value chain, such as original equipment manufacturers (OEM) like ABB.
Any company that aims to supply to the maritime industry will have to master the following four megatrends:
- Digitalisation and connectivity
- Automation and electrification of systems
- Emissions reduction and electrification
- Automation of work
The era we are dealing with here is the 4th Industrial Revolution. Work will be revolutionalised, as will the production and use of energy. Even if these changes still seem far away for many of us, some shipbuilding tenders include exactly the kinds of features laid out in this paper.
Operators and their suppliers will integrate and automate their processes
We believe that only a vertical integration of the entire product and activity chain, from the machine, sensors, historian on board, the cloud platform, applications, and dispatch of service engineers, design, and R&D is going to provide ship owners and their fleet with a next-level standard in safety, productivity, and low carbon footprint. Or as one of our major customers put it, “our ambition is to operate by aviation industry safety and productivity standards by 2020”.
Large amounts of data will be collected by using professional IT architectures and technologies, but a meaningful analysis and interpretation of the collected data is only possible through the application of domain knowledge. Much of the technology we are developing now aims at integrating ABB with its customer, for the purpose of sharing knowledge and making better decisions on both sides of the table.
Today a hundred highly skilled service engineers are able to support 500 vessels with phone and on-call technical support, but in the future, the same number of engineers and technical experts will be able to support a significantly higher number of vessels at sea, if a remote connection exists. The amount of on-call visits would be reduced dramatically as well which means safety and reliability goes up. Already today, we reduced the on board visits by service engineers to those ships with remote condition monitoring on propulsion drives by 70%, and with improving predictive monitoring we are able to inform the crew before damage occurs.
The most progressive ship owners and operators have already implemented advanced operational models and tools, and they look for partners who are on a similar technology level, in order to integrate with them, and run the business at next level safety, and productivity. The automation of work will affect every company, and every department inside the company.
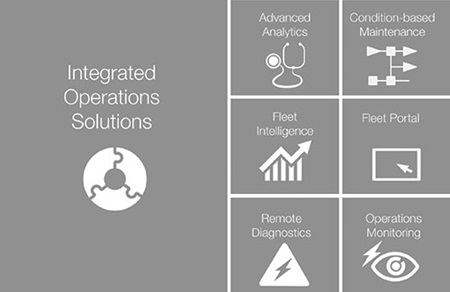
Five steps to autonomous operations
The first steps towards autonomous shipping involve combining new digital services with our existing technical services. We call this phase Integrated Operations’ because it speaks to a new way of operating, not intended to replace the crew, but to support them. We also believe that new technologies will help to improve efficiency to a similar level where best-in-class industries (such as the aviation industry) operate.
Through the Integrated Operations concept, critical equipment and control systems on board a vessel can be monitored, and are used at ABB on shore service center and the customer’s on shore fleet operational center, for optimising the vessel and fleet operations.
Some of the data provided by these systems is analysed on board the vessel, by automated algorithms, which allows immediate and fast reaction from the crew to act on anomalies, performance issues and emergency situations. In addition, we can send some of that data to shore and make it accessible to the customer wherever they need it, whether that is in an operational center or just on a laptop or a smart phone. This data transfer takes place either through a cloud server or within their own IT network. This gives the customer’s technical department on shore better visibility of each vessel and the total fleet, and enables it to react in a more efficient way in emergency situations and to plan better for maintenance and operations. In addition, we are using this information ourselves, in our own service centers, from where we can remotely access key equipment in order to troubleshoot, or to analyse losses and support our customer in maintenance planning and making improvements to systems during operation.
We can also run a virtual copy of the system on a server and make it ‘age’ according to the vessel that is operating at sea. This concept, also often described as ‘Digital Twin’ will soon be a commercial reality and it will be a key to provide condition-based maintenance.
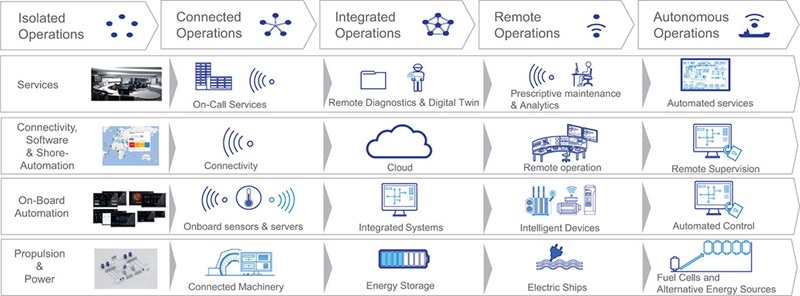
The modular offering
Our service offering is modular and customers can start with whatever service addresses the issues they have at that given moment. Because we are performing the services ‘with’ our customers, we need to be able to integrate with the tools and providers they are using as well.
The Internet of Things, Services, and People is an emerging industry megatrend that will change the way the maritime industry and many other industries operate.
The key is to know which new solutions and services to combine with the existing core of our business, in order to provide the customer with enhanced productivity of their assets, and investments – whether that is a productivity improvement in the production process, in safety, quality, or in cash.
Working closely with our customers and using the same tools means there will be more interdependencies between our work processes and value chains. The work we perform in engineering, service, and supply chain will become more performance-driven and customer focused because Integrated Operations improves our ability to provide our knowledge and services to the users.
The more all parties in the value chain are connected, the higher Operational Excellence will move on the agenda. Improvement initiatives will be joint efforts between the owner, operator, and supplier, for example in supply chain and spare part management, handling emergency procedures, and asset lifecycle management.
Integrated Operations is also a good example of ABB’s Internet of Things, Services, and People (IoTSP). We have taken action to accelerate the digitalisation, by improving our competencies in new areas and integrating them with the existing organisation. Our new Integrated Operations Centers are proof of that. We consider this the beginning of the next Industrial Revolution and a wave of shipbuilding activity that will see more connected, integrated, electrical, and autonomous vessels and maritime operations.
We believe the next step-change in productivity and safety in shipping comes from integrating ships better with shore side operations. Integrated Operations is the concept that will drive this change in the coming years.
Customer benefits
- Full transparency of critical systems down to detailed level
- Visibility of critical processes and alarms
- Detection of failures and analyse together with the OEM
- Ability to reduce voyage speed of ships and the whole fleet
- Higher availability of systems and vessels by accepting known, low risks
- Incident management combining onshore, OEM, and vessel crew
- Plan, manage and increase maintenance during operations
- Save man years in technical planning department, by better OEM cooperation
- Comply with classification in extended and reduced maintenance
- Help plan fuel efficiency during voyage and operation
- Develop new solutions that solve challenges based on data
- History of systems performance, condition, and intervention
- Attract and retain a new generation of professionals
- Improved exploitation of staff and OEM expertise through improved cooperation
- Manage documentation globally, easy to update and locate files
- Manage software installed base, and upgrades, globally and reliably
- Leaner global footprint due to better access to OEM and internal resources
Authors:
Richard Windischhofer, Ph.D.
Senior Vice President, Business Development and Integrated Operations, ABB Marine & Ports, Norway
Mikko Lepistö
Senior Vice President, Vessel Information and Control, ABB Marine & Ports, Finland