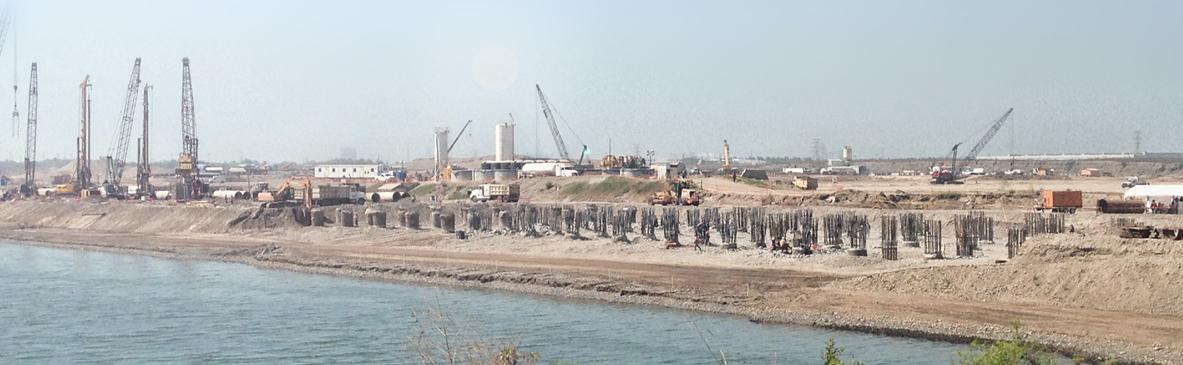
Lázaro Cárdenas Container Terminal
By the second quarter of 2015, phase one of the APM Terminals’ Lázaro Cárdenas Terminal 2 (TEC 2), located at the port of Lázaro Cárdenas on the Mexican Pacific coast, is set to begin operations. The facility is being developed in three phases, the first with an annual throughput capacity of 1.3 million TEU.
"With Lázaro Cárdenas we had the opportunity to say ‘Why don’t we automate?’ and ‘Why don’t we try to automate more?’" says Tiemen Meester, Vice President for Business Implementation at APM Terminals, headquartered in The Hague.
The foundation for the first phase of TEC 2 was officially laid at the end of 2012. This stage involves constructing a 750-meter quay, installing state-of-the-art cargo handling equipment, creating an intermodal rail facility and developing an automated 45-hectare container yard and gate facility.
Automation underestimated
"The driver behind our decision to automate was simple," explains Meester. "If you look at our large portfolio of terminals, you could say the automated terminals are underestimated. But we considered the fact that while they don’t move at the highest speed, they are highly predictable. So we said it’s time to bring back automation in our company – because of the stability it brings."
Meester says the management created several business cases for TEC2, "basically deploying more capital expenditure (capex) on equipment. But we were surprised at how much more efficiently and how many more containers we could put through the same footprint. So the higher equipment capex was off set by lower construction cost, meaning for the same money we could automate the yard."
TEC 2 represents an investment of almost $900 million. The International Finance Corporation and partner banks provided a $300 million loan for its phase 1 construction. With so much money at stake, it’s not surprising that Meester counts the commercial gamble as the biggest risk his company takes when building a new terminal.
"It’s an enormous undertaking. You put hundreds of millions of dollars into your civil works, buying cranes, equipment and technology.
Opex a major factor
"This is shareholder money and we need to provide a return. How much money you need to mobilize up front to buy what is a very important consideration. If you can build a terminal for $500 million or $450, we all want the $450. But making sure we get the most efficient terminal built for the lowest cost is in our interest."
Meester says the operating expenditure (opex) number is also a major factor behind how APM Terminals designs and makes business cases. "It’s sometimes complicated to put a terminal together, but, at the end of the day, we’re in a simple business. We lift boxes out of a ship, onto the quay, then out of the yard – and vice versa. It’s about what’s the least costly and most efficient way to lift those boxes."
"It’s not just that automation costs more. I think that’s misunderstood sometimes. The business case was pretty straightforward at Lázaro Cárdenas: We could get a more efficient and stable operation for the same money that we would have spent on a non-automated terminal.
While the decision to opt for automation at Lázaro Cárdenas was seen by some in the industry as last-minute, Meester says it was really the result of having time to optimize the design after winning the tender.
"If you want a perfect business case, you can work for a year. But usually there is a deadline imposed, especially with tenders. I’ve seen situations where we’ve had to respond in six weeks. Then you aren’t going to get a fantastic product. At other times, we’ve been able to work on a tender for four or five months.
"When there’s more time, that’s when creativity really comes into play. I think Lázaro Cárdenas is a good example of that. We had more time so we made some changes to improve the facility."
Most of the play was around the layout of the footprint. When fully completed, TEC 2 will provide shipping companies with 1,485 meters of berth, 16 ship-to-shore cranes, and an annual throughput capacity of 4.1 million TEU.
But APM Terminals’ latest decision to automate is not just the result of a passing trend. Of that Meester is convinced. He bears this out in his answer to what the terminal of the future will look like: "A quiet dark place."
As he explains, "The trend towards electrification is undeniable. More and more new terminals will be electrified and thus pretty quiet. As for the dark place, that’s down to automation, which is here to stay. It’s going to be more important as we move forward. I’m not saying everything is going to be 100 percent automated. There will be modules. In some places the gates will go quicker. Yard automation is already here, with crane automation and automated stack profiling – it’s all being integrated over time.
"The fact that there are no longer people walking between the machines is a fantastic safety feature. People are operating the machinery from other places. Hence I make the joke that the lights can go out."
At APM Terminals it seems the lights are on full beam and directed firmly at the automated future.
Photos: APM Terminals
Lázaro Cárdenas Container Terminal
Lázaro Cárdenas Container Terminal (LCT) is a transshipment hub at Lázaro Cárdenas, Mexico’s second busiest port in the state of Michoacán. The first phase of the new terminal will give LCT a land area of 63 hectares, three berths and a total quay length of 930 meters. Phase 2 will be built on 85 hectares of land adjacent to the new terminal.
The TEC 2 project will improve efficiency for shipping lines as well as exporters and importers, alleviating bottlenecks and improving cost efficiencies in the transportation of containers through Lázaro Cárdenas.
APM Terminals
APM Terminals is one of the world’s leading port operators with a global terminal network of more than 70 facilities in 68 countries and on five continents.
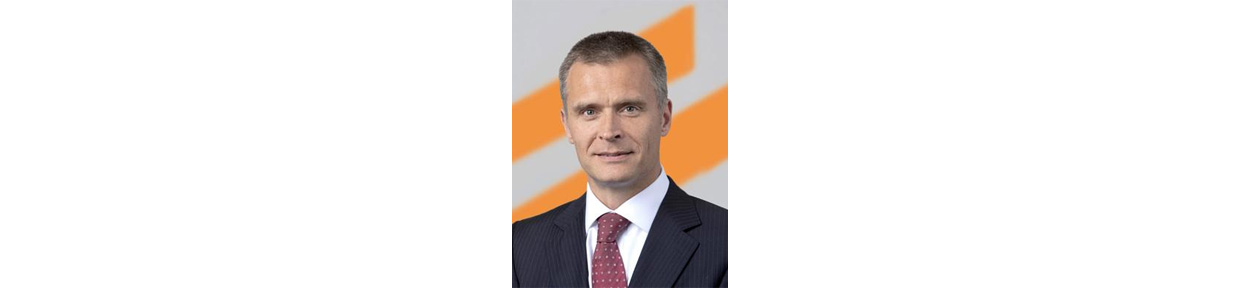