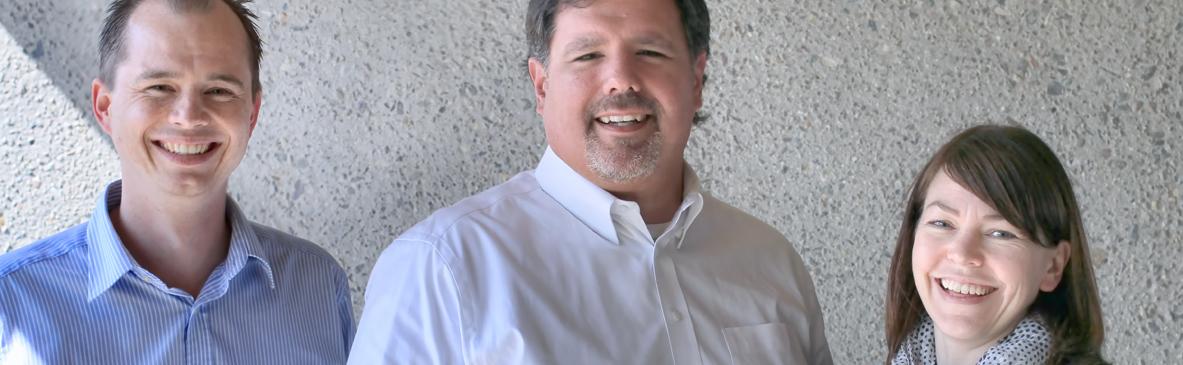
Patrick Vloemans, Allen Thomas and Clara Holmgren
Generations arranged a “brain trust” session with these specialists to envision solutions to this challenge. The group met in San Diego and comprised vice president of operations at APS Technology Group (member of the ABB Group) Allen Thomas, Clara Holmgren, product manager at ABB Crane Systems and Patrick Vloemans, global business development manager for ABB Port Solutions. Their mission was to come up with thought-provoking ideas that could bring the container industry to its next level of efficiency. That is not a modest ambition since the industry already is a low cost and highly efficient part of the container supply chain.
A standard with deep impact
The session began with a discussion about what the worldwide establishment of containerization has meant for cargo flow; i.e. allowing producers, buyers and retailers to adopt just-in-time principles and reduce warehousing and overproduction on a global scale. The revolution started with transport, but rolled on to change supply chains and enabled factories to reach a new level of efficiency, one that is dynamically changing as lower cost, higher quality sources become available. “But what if this revolution is just halfway into its potential?” the group asked.
Inaccurate and missing information
As they elaborated, the physical standardization of cargo flow was never followed up by a similar standardization of information flow. This poor state of affairs in information handling is illustrated by the fact that the misdeclaration of container weights has been an ongoing problem in the shipping industry. Following the accident involving structural failure of the container ship MSC Napoli in January 2007, the containers that were removed from the vessel were weighed. Of the containers that remained dry, 20 percent had a weight difference of more than three tons when compared with the shipper’s declaration. The largest difference for a single container was 20 tons.
Regulation kicks in
In May 2014 the Maritime Safety Committee of the International Maritime Organization (IMO) decided on, and approved for adoption in November, draft amendments to chapter VI of the international Safety of Life at Sea (SOLAS) treaty to require mandatory verification of the gross mass of containers. These requirements will come into force before May 2016 and will require a new type of information flow in the container industry.
No lack of technology
The weight of a container can be controlled every time a crane touches it, the team agrees. That crane can pair the weight data with the identity of the container by OCR (optical character recognition). The data can then be fed into the terminal operating system and forwarded to a stowage validation system to form an accurate loading plan that leverages the full capacity of each ship. In this way, a safety margin used to compensate for inaccurate weight data is eliminated and ballast water is no longer used to fill the gap between reality and declared weight. Our “brain trust” team sees this as the spark that could ignite a whole new concept around container information handling.
The regulatory requirement to share one piece of information could pave the way for a cloud-based, unified handling of information objects reflecting not only the weight, current and previous location and other events or tracing, cargo category, destination and priority. In addition to the benefit it could have within container terminals around the world, the data could be shared in as much detail as the business interest of the stakeholders allow.
A common interface
Our ABB brain trust sees no problem in delivering the crane automation system that updates the container information object, wherever it is, with accurate data on mass according to the upcoming IMO regulations. Terminal operating systems could share event data, and shippers, fleet managers, insurers, cargo owners and analysts would make use of that data as required. All the industry needs is to agree on an interface. What web developers call a REST-based API (application programming interface) is the common solution that allows any system to talk to any other system in our time and age. One such approach to standardization of interfaces that may hold promise has been drafted and is being evaluated by the leading container port industry organization, PEMA, the Ports Equipment Manufacturing Association.
What the data can do
Why should each container have an information object “in the cloud” from the moment a shipper places his order and the supplier attaches a number of SKUs (stock keeping units) to this reservation? According to our team, the point is not the availability of real-time data itself. It is what you can do with the data in terms of pre-planning and pre-processing:
- The logistics company will be able to organize its cargo flow earlier.
- Accurate information ahead of time would drive automation and result in cost reductions as well as higher precision and predictability at terminals.
- Once event data is added, each link in the transport chain will enjoy a new level of predictability, further reducing storage and warehousing, from shipment of materials to the factory to the arrival of finished goods on store shelves.
- Customs can pre-process shipments and no longer delay the cargo flow.
- Checking the weight at every handling point and additional data from e.g. x-ray systems could reveal tampering and possibly customs fraud.
- Bottlenecks can be eliminated through simulation and modeling of workload, days and weeks ahead of time, allowing for better resource allocation and use of electricity required to complete the day’s container movements.
- A vast number of agents and intermediate players, who are necessary due to the lack of information transparency, would no longer be needed in the transport chain.
- Shipping lines can copy the practice of the express package industry to create new products for priority freight that escape fierce price competition and focus on customer value.
A coordinated approach needed
One shipping line or one terminal operator alone cannot establish a new standard for information sharing in the container industry. Our team concluded that a complete cargo information loop would have to be created. The new solution would not be a new network. The ships and the operators are already there. Rather than a new technology or system, the quest is for an improved working method.
The big hubs are already highly automated gateways and the potential is in better connecting smaller terminals – “spokes” – to the highly optimized intercontinental cargo flows. This could allow shipping lines to create new products to reach the market and then trickle down to the multimodal handling, maybe even to automated warehousing connected to the ports.
Eventually, the return on investments in information systems and terminal automation needs to come from the freight customer, while satisfying every player along the chain with a better margin than before. A coordinated approach would be needed between partners, which could demonstrate a new level of performance to the industry at large.
The group of world shakers
Our team’s beachhead project would involve partners who could work together to establish at least two new marine or hinterland terminals linked to an existing major gateway. The partners and their roles would be:
- A shipping line with ambitions to create a new, faster freight product with higher predictability and value – a product that would be differentiated from the low-priority cargo.
- Terminal systems providers that can facilitate control and automation that better secures high-priority cargo a fast track through the system.
- A software vendor with a leading market position that would provide an interface between a new and the conventional working method.
- Government partners with a growth agenda and ambitions to pre-process customs in an all-electronic information flow.
- A port operator that sees the project as the start of a new network of smaller terminals.
- A financier with a vision of pushing for new technologies that improve efficiency and sustainability
At the outset of the workshop, the team set 2020 as a relevant time horizon for implementing a new information flow. “A bold, but not unrealistic vision,” they concluded.
APS Technology Group (APS)
APS Technology Group (APS), a member of the ABB Group, is a leading provider of optical character recognition (OCR) and process automation solutions for marine and intermodal container terminals. ABB acquired APS in February 2013 in order to strengthen its long-term growth strategy in container handling and terminal automation markets.
Each container should have an information object “in the cloud” from the moment a shipper places his order. Weight, cargo category, priority, destination as well as updated event data should be accessible. Traceability, predictability and pre-processing could optimize every part of the logistics chain.