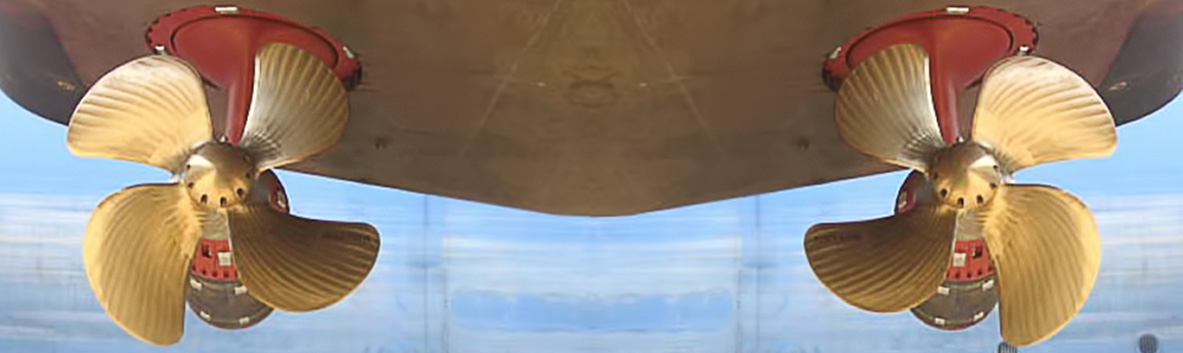
The “little sister” in the Azipod propulsor family is the Azipod C gearless propulsor series, which is gaining it’s foothold in the azimuthing propulsor market between 1 MW and 5 MW power – a market that has been dominated by geared mechanical propulsors.
The Azipod C gearless propulsor was first introduced to the market in the year 2000. It is available both as an open propeller version, Azipod CO, for typical ship applications and as a nozzled version, Azipod CZ (see Figure 1), mainly for dynamic positioning (DP) vessels. The power range of the Azipod C series varies from 1.0 to 4.7 MW. As of today, Azipod C propulsors have gained over two million cumulative operational hours. Deliveries include references from all major vessel segments: drilling, offshore supply, offshore construction, accommodation, heavy-lift, wind turbine installation, research, tanker, ferry and yacht segments.
The Azipod C gearless propulsor is a high-end product that improves three major aspects of operational profitability throughout the vessel’s lifetime: efficiency, reliability and cargo capacity. This article discusses how these aspects are improved as well as provides insight into excellent long-term operational experience.
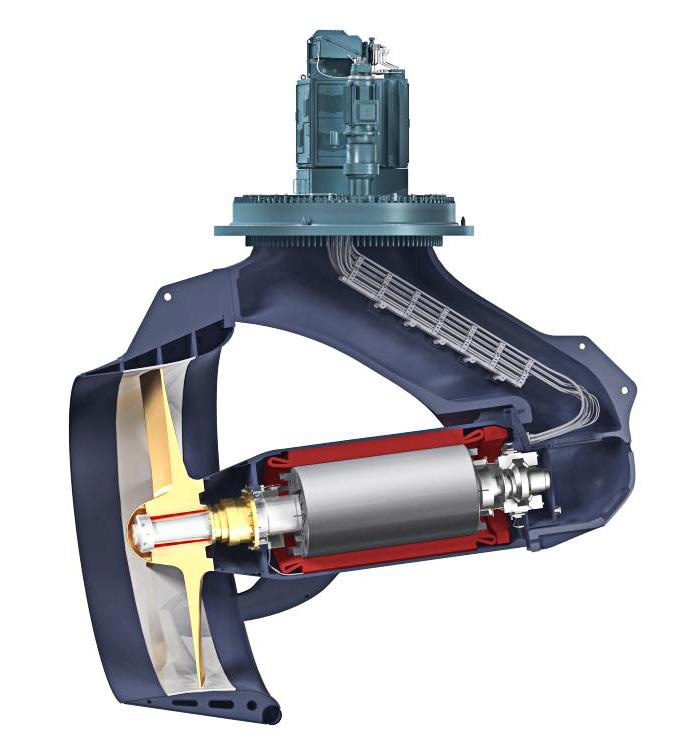
Efficiency
The most basic factor in the operational profitability of a thruster is the total efficiency of the propulsor affecting the vessel’s fuel consumption. Total efficiency can be divided into four subcategories:
- Hydrodynamic efficiency
- Mechanical efficiency
- Electrical efficiency
- Required auxiliary consumers
Hydrodynamic efficiency of the Azipod CO
The open propeller version, Azipod CO, is a pulling propulsor. The advantage of a pulling design becomes apparent with higher ship speeds – roughly from 10 knots onwards. In a pulling unit the water inflow to the propeller is more uniform (see Figure 2). There are no low-speed inflow areas in the propeller wakefield as there are in pushing units, where the propeller works closely behind a propulsor strut, as shown in Figure 3, or in an ordinary shaftline propeller that works behind the shaftline support structures.
Figure 2 Pulling Azipod CO propulsors receive undisturbed water inflow, which increases propeller efficiency. Figure 3 The Inflow to the pulling propeller is more uniform, compared with a propeller working behind a propulsor structure.
In addition, the Azipod CO motor module tube behind the propeller works as a “costa bulb” streamlining the propeller slipstream onto the motor module. This avoids flow separation immediately after the propeller hub, which creates additional drag in ordinary pushing propellers and further improves the efficiency and thrust of the Azipod CO propeller.
The more uniform wakefield enables optimization of the propeller blade design, offering higher efficiency and a higher margin against undesired cavitation. In addition, the costa bulb effect of the motor module further increases propeller efficiency. Thanks to a pulling design, the efficiency improvement in transit speeds can even be as much as 10 percent, compared with a pushing propulsor or shaftline.
Hydrodynamic efficiency of the Azipod CZ
Propulsors equipped with a nozzle, also known as a duct, are normally installed on vessels where DP operation is a major part of the operational profile. The effective thrust per power, i.e. newtons per kilowatt, at zero ship speed or close to zero ship speed, is essential for the hydrodynamic design of a nozzle propulsor such as the Azipod CZ.
In contrast to transit speeds optimized propulsors, a pushing propulsor is able to reach high thrust efficiency at low ship speeds. As the inflow speed is very low due to low vessel speed, it is more beneficial to keep propulsor structures away from the propeller-induced slipstream.
The Azipod CZ is a pushing unit with a nozzle profile tailored and optimized specifically for the Azipod CZ structure. The strut is located further from the propeller, compared with a conventional nozzle propulsor, providing better inflow and a more uniform wakefield for the propeller also in the bollard condition.
The Azipod CZ was the first nozzle propulsor on the market that featured the significantly tilted (7°) shaftline and nozzle arrangement. The tilted shaftline improves effective thrust significantly as interaction with the ship’s hull or other thrusters can be avoided, especially during DP operation. In addition, the effective thrust of forward thrusters during the transit operation is improved; for example, in the case of drillships.
The effective thrust improvement from a tilted shaftline and nozzle is 10 to 30 percent during DP operation, compared with a non-tilted design.
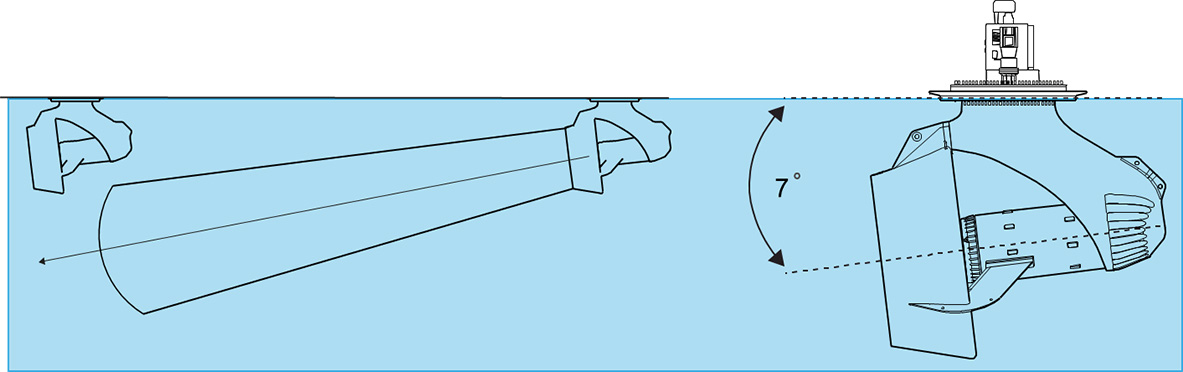
Mechanical efficiency
The mechanical efficiency of the Azipod C propulsion drivetrain is the best in its class. The robust gearless design has only two bearings on the drivetrain providing close to 100 percent mechanical efficiency.
The gearless design of the Azipod C propulsor improves mechanical efficiency by about five percent, compared with a conventional geared mechanical propulsor.
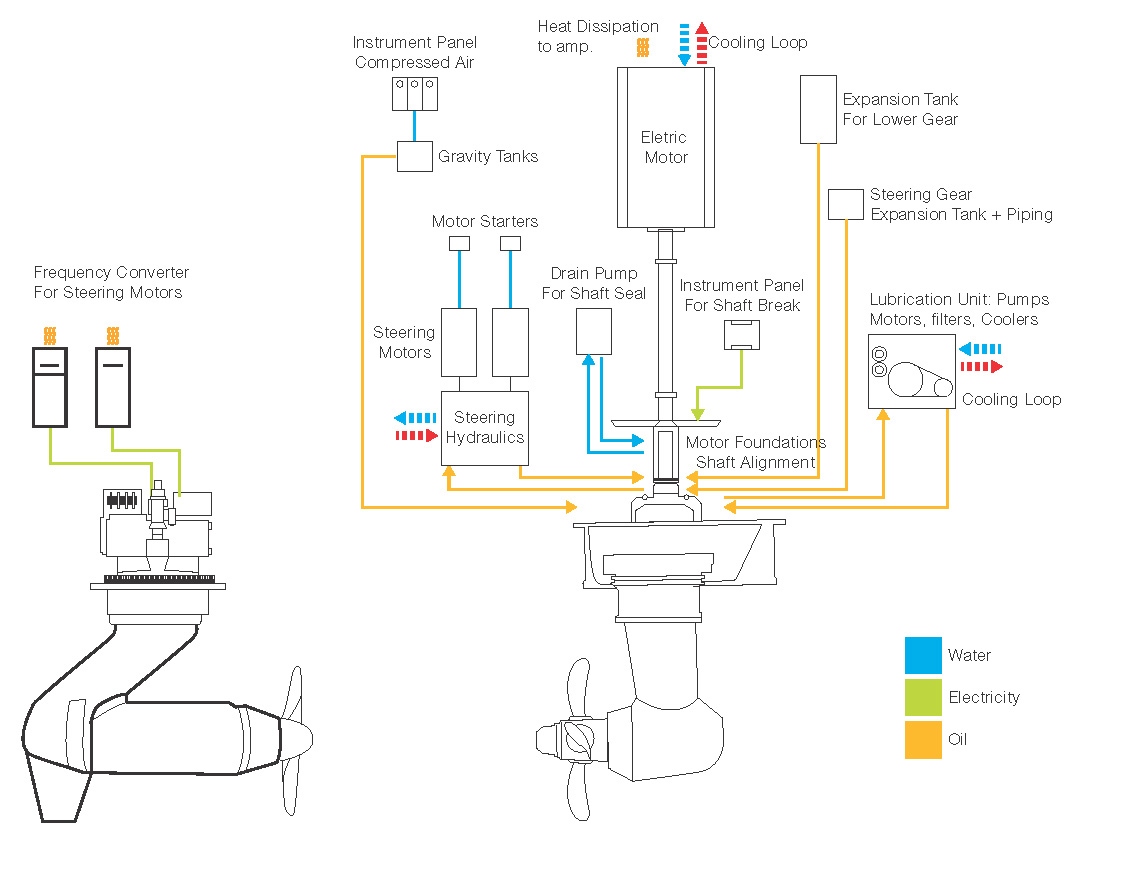
Electrical efficiency
As conventional geared propulsors are powered with an inboard induction motor, one unique and advanced feature of the Azipod C gearless propulsor is the permanent magnet propulsion motor. Unlike normal electric motor types, the rotor of a permanent magnet motor is naturally magnetized. Thus, the additional power consumption for magnetizing the rotor is saved.
The electrical efficiency of the Azipod C permanent magnet motor is about 98 percent, while typical induction motors have about 96 percent efficiency at a rated point. The efficiency difference increases further with partial loading. In typical DP loading – for example, at 10 percent of rated motor power – the efficiency difference can be 5 percent between induction and permanent magnet motors.Compared with a typical induction motor, an Azipod C permanent magnet motor improves electrical efficiency from 2 to 5 percent, depending on the vessel’s operational profile.
Auxiliary consumers
No comparison of total efficiency can be made without taking into account the auxiliary consumers of the propulsor. Auxiliary consumers that are needed in conventional geared propulsors include, for example, the lubrication system for bevel gear(s) and cooling system for the inboard propulsion motor. These systems require power for lubrication and cooling water pumps, and cooling fans.
In an Azipod C propulsor, the minimum electrical losses of submerged permanent magnet motor are cooled directly to the surrounding seawater passively through the motor’s casing. Thus, a cooling water pump and cooling air fans are not needed in the Azipod C system. In addition, savings are gained due to the absence of other auxiliary systems that are present in a conventional propulsor, including a bevel gear lubrication system and possible steering hydraulics. See Figure 3 for a comparison of auxiliary systems.
The absence of both gear lubrication and propulsion motor cooling systems improves the propulsor’s total efficiency, typically by 1 to 2 percent, depending on the loading profile.
Reliability and maintenance
Reliability of the propulsor is vital or shipowners. Failure in propulsion may decrease the safety of the operation, especially in rough seas. It may also lead to discontinuation of the vessel operation and significant reduction of the income provided by the vessel.
Normally, propulsors on ships are maintained during dry-docking of the vessel every five years. However, there is some push from owners and operators to increase dry-docking periods from five to seven years or even more.
In the offshore business, semi-submersible drilling rigs, for example, are not dry-docked at all and their many propulsors, usually eight per rig, are overhauled by demounting a few propulsors at a time. The change-out of propulsor is carried out underwater with the help of divers. The extra replacement unit is changed-in and the demounted propulsor is overhauled (critical components inspected) and put in service rotation.The Azipod C design has some major advantages to ensure safe and reliable operation over the overhaul period:
- The gearless and simple drivetrain has a minimum of mechanical parts that wear, making overall reliability superior.
- The multistage shaft seal has a primary seal and two backup seals. The leakage from the primary seal can be monitored, giving sufficient planning and preparation time for maintenance in the case of a damaged primary seal.
- The Azipod C motor module is pressurised to avoid any water ingress into the propulsor.
Long-term experience with the Azipod C propulsor is well documented. So far, the longest continuously serving propulsors have been in operation for close to nine years in a rig before an overhaul. Several guests at an offshore oil and gas industry seminar, held in February 2014 at ABB’s Houston Ship Channel workshop facility, were able to see the condition of the critical parts taken out from one of the long-serving Azipod C propulsors. The Azipod CZ propulsor was disassembled one week before the seminar and it came fresh out of operation after a swap-out at the end of 2013. The components showed hardly any wear and tear and most of them could be reused after a thorough inspection and partial reconditioning. See Figure 6 for an example of the critical component condition.
The seminar included a hands-on session where the audience could touch and inspect components such as the thrust, slewing and propeller-end bearing, shaft and slewing seals and the service brake. The strut of the unit and the stator and rotor of the propulsion motor where exhibited for inspection as well. The event was very well received by guests from the oil and gas and offshore industry, including visitors from drilling companies, shipyards, operators, classification societies and designers (see Figure 7).
Figure 6 Azipod C thrust bearing condition after close to nine years of DP operation. The original grinding texture (right) could still be seen on the raceway. Figure 7 A seminar at the ABB Houston Ship Channel workshop included presentations and a hands-on session to examine the condition of used Azipod C components. Figure The number of critical components on the Azipod C drivetrain, such as bearings (upper) and gear wheels (lower schematics), is significantly lower, compared with a typical Z-drive type geared propulsor. Figure 9 The Azipod propulsor saves the footprint and space as the conventional onboard propulsion motor (marked with red arrow) is not needed. Figure 10 Three Azipod CO propulsors in a pulling arrangement
More payload
A smaller footprint is an advantage for any onboard equipment, especially with small compact vessels such as anchor handlers, offshore supply and construction vessels and, even more so, in ferries and yachts. The beauty of the Azipod propulsor is that the large propulsion motor is placed underwater, next to the propeller, saving valuable onboard space.
The saved onboard space is typically used to:
- Get more payload
- Change machinery layout to reduce the vessel’s overall length
- Optimize hull lines to reduce hull resistance
The above possibilities improve the operational profitability of the vessels by improving payload and lowering fuel consumption.
Conclusion
Since 2000, experience has verified the inherent benefits of the gearless podded design with regards to efficiency, reliability and space savings. Further advantages of the Azipod C propulsor include, for example, a permanent magnet motor and simple auxiliary systems.
The combined annual fuel cost savings, including improvements in hydrodynamic, mechanical and electrical efficiencies, can be realistically estimated to be from 10 to 30 percent, compared with conventional geared azimuthing propulsor.
The excellent reliability of the gearless design has been demonstrated by over 2 million accumulated running hours with Azipod C propulsors. Long service intervals and excellent reliability improve savings from maintenance and out-of-operation costs for operators and owners.