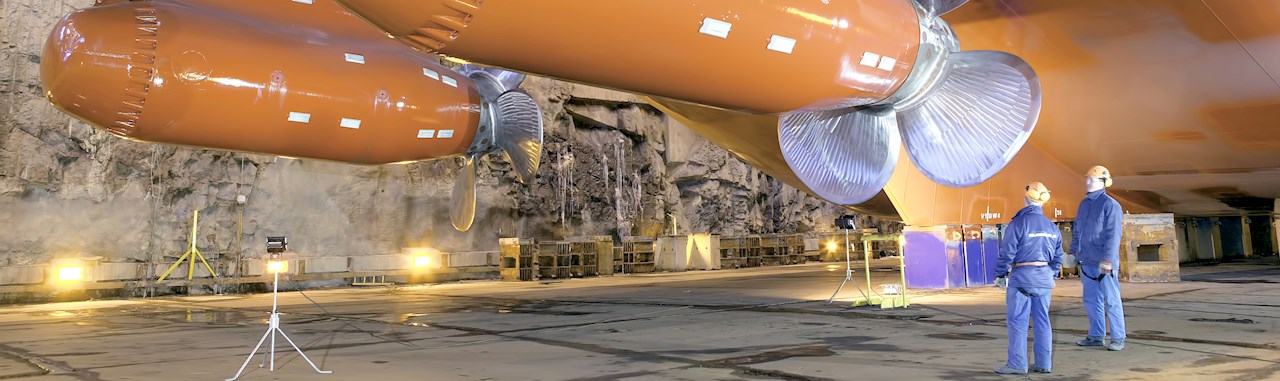
Year-round operations in ice covered areas result in increasing need for specially designed icebreaking offshore support vessels and tankers. An important characteristic of these vessels is their ice management capabilities.
Azimuth thrusters offer great flexibility in different ice management situations by using the thruster wake and propeller in close contact with the ice. Electric propulsion with Azipod propulsors has been successfully used with such vessels for many years, and the system itself has proved reliable when operating in ice. In the Sakhalin region, experience has accumulated from using seven icebreaking vessels with ABB electric propulsion, many equipped with Azipods. Recently, two new Azipod icebreaking vessels have been built for the Arkutun-Dagi field.
Electric Azipod propulsion systems have been playing an important part in making several demanding Arctic shipping projects technically and economically feasible. In this article we will be present the characteristics Azipod propulsion as well as some full-scale test results from the use of Azipod units in ice management operations. These results will show how Azimuth propulsion offers improved ice management performance and greater vessel design flexibility. They will also offer further insight into different possibilities; for example, selection of the most suitable azimuthing angles for various tasks.
Azipod propulsion in icebreakers
The Azipod propulsion system enables a vessel to break ice using the revolutionary Double Acting (DA) principle, [1] Heideman et al (1996). The DA principle means that the vessel can be designed with the stern optimized for icebreaking and the bow optimized for another condition such as a bulbous bow for open water or a heavily ice-strengthened bow for multi-year icebreaking by repeated ramming. It is well known that when going astern, the ice resistance of a ship will decrease as a result of the propeller flow around the aft part of the hull, which, among other factors, reduces friction. However, ships equipped with conventional rudders are difficult to steer when going astern. This problem does not affect ships equipped with an Azipod system, as the propeller thrust can be steered in any direction (see Figure 1).
The Azipod system greatly improves the maneuverability of ice-going vessels. The turning unit allows the propeller thrust and wake to be directed against the ice, meaning it can be effectively used in ice management tasks such as [2]:
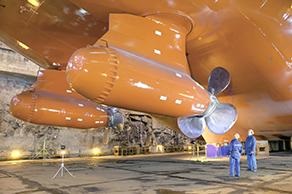
- Breaking the vessel through ice ridges
- Vessel operation in ice rubble
- Clearing a wide channel behind the vessel
- Clearing ice around the hull of the vessel or from a structure or platform
- Breaking level ice or pack ice to smaller pieces
- Clearing ice between the pier and the ship
This paper will explain how the correct operation of an azimuth thruster can further enhance each of these ice management tasks. Differences in ice management tasks in various ice-covered seas will be discussed.Full-scale ice management tests and measurements recently carried out onboard an icebreaker will also be summarized.
Ice management (IM)
What do we mean by ice management? How can we define it? Players in the industry have different perceptions of what it is depending on their own experience. We will briefly go through IM in different areas in the world and highlight what is required from the vessels that operate in those areas.
Sakhalin
In the Sakhalin area, IM used to be closely connected to the Sakhalin II project and the Molikpaq platform in the 1990s. Offloading from Molikpaq was via a SALM (single anchor leg mooring) buoy and a floating storage and offloading unit (FSO) named Okha. Both the SALM and the FSO were moderately ice strengthened and the operating window was very dependent on effective IM. The area consists of drifting sea ice of varying thickness with occasional stamukhas or parts of them. A stamukha is an ice feature that has been grounded and grown in size due to rafting. Storms and high tides can push it back into the sea, where it starts to drift with the pack ice. In this area ice concentration is normally well below 1 (10/10).
The supply vessels expanded the operating window for the SALM, Okha and the offloading tanker by positioning themselves upstream in the ice flow and creating an ice-free path by turning the thrusters more or less transversely and then pushing the ice to the sides using the propeller wash. In this kind of operation the force and the direction of the propeller wash stream are important and this should be reflected in the design of the propulsion arrangement.
Nowadays, this mode of operation is no longer needed since offloading from the Molikpaq platform is by pipeline to the shore. IM tasks are now mostly to clear ice away from loading and manifold areas and to keep the rescue area, where the emergency escape capsules descend, clear of ice. These tasks are better performed by milling the ice with the propellers. It is important to understand that the gravity-based platforms do not need IM to survive because they are designed to withstand all ice loads.
Baltic Sea
IM is quite different in the Baltic and other sub-Arctic areas. Here we generally speak about assisting and convoying merchant vessels. When an icebreaker frees a vessel in compressed ice, the ice milling effect of the azimuthing thrusters can be fully utilized. On the other hand, during vessel convoying, the flushing effect from the transverse thrusterwash can be used to clear the channel and reduce the required power outtake of the vessels that follow, thereby saving fuel and reducing emissions. These are design points for assisting icebreakers.
Caspian Sea
The ice conditions in the Caspian Sea are highly dynamic. Outside of the landfast ice, the ice is constantly moving, rafting and ridging. This, in combination with very shallow water in the northeastern part of the Caspian, produces grounded ridges that reach high above the water level. In these conditions, the only way to operate is to mill the ridges with propellers and remove the milled ice with the propeller wash. This is how the supply vessels manage the ice at the Kashagan site when they clear the loading and escape areas.
Arctic waters, North America
IM performed in North America is, again, completely different from that described above. On the east coast, in the Labrador Sea between Newfoundland and Greenland, IM means mainly iceberg towing in more or less open water during the summer season. This kind of operation requires different capabilities from vessels. Azimuthing thrusters offer excellent maneuverability and are able to manage growlers and bergy bits using the directed propeller wash effect. If the thrusters are equipped with nozzles, they protect the propellers against towing wires in the sea to a certain extent. It is a common misperception that iceberg towing requires very high bollard pull force. As a matter of fact, iceberg towing is normally performed using low speeds and pull forces – normally less than 100 tons – to prevent the iceberg from tumbling over.
IM on the North Slope in the Beaufort Sea is more violent than anywhere else in the world. Here the focus is on protecting exploration vessels from drifting pack ice that contains multi-year (MY) ice. There are several IM techniques, some involving several vessels with different roles. However, all the vessels used for IM have a high ice class in common and they are usually equipped with very strong bows intended for breaking the MY floes by repeated ramming. When operating in MY ice conditions, great care should be taken when rudders and propellers or azimuthing thrusters come into contact with the ice. With MY ice, the main mode of operation is bow first.
Russian Arctic
There are also different kinds of IM in the Russian Arctic. In the waters to the west of Kara Gate there is an established shuttle tanker service system and another ready to start up any day. Here the IM vessels are supposed to prepare the offloading site before the tankers arrive and help them maintain the correct position with respect to the ice drift direction during offloading. During operations, both flushing, milling and breaking bow-first have been used. In the high Russian Arctic to the east of Kara Gates, IM mostly involves convoying vessels through the ice. Nuclear icebreakers normally break a lead through the ice ahead of the convoy. The reason for the large distance between the icebreaker and the convoy is safety related. The ships following the icebreaker need a proper stopping distance in case the icebreaker is stopped by severe ice. If the vessel(s) cannot follow, the icebreaker returns to free the vessel by maneuvering close to the stuck vessel, thereby releasing the ice pressure on the hull.
IM is thus not a clearly defined function but various tasks involving milling or flushing with the propellers or managing the ice by breaking it with the bow. Different IM tasks require different capabilities from the IM vessels. Elegant vessel designs can produce compromises that work reasonably well for several IM tasks.
Full-scale IM tests on board the icebreaking PSV Aleksey Chirikov
Aleksey Chirikov is an icebreaking platform supply vessel built by Arctech Helsinki Shipyard for Sovcomflot. The vessel’s main features are summarized in the table below. Figure 2 is a photograph of the vessel taken during sea trials.
Sea trials were conducted with the Aleksey Chirikov in March 2013 in the Gulf of Finland. In between the standard sea trial program, tests were conducted to study the propulsion system’s response to various combinations of propulsion power and azimuth angles.
Tests were conducted by measuring vibrations from Azipods while constant power and azimuth angle was maintained. Increasing the azimuth angle with high power increases vibrations and, at a certain angular zone, it is advisable to avoid continuous high power to prevent unnecessary loading of the machinery. It is worth noting that the Azipod system, being simple and robust, has considerable tolerance against vibration, especially when compared with systems with a more complex mechanical power train. However, it is only prudent to take means to lessen vibrations, if this can be done while performing all tasks.
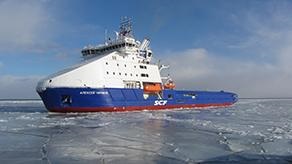
Full-scale IM tests on board the icebreaking PSV Aleksey Chirikov
Aleksey Chirikov is an icebreaking platform supply vessel built by Arctech Helsinki Shipyard for Sovcomflot. The vessel’s main features are summarized in the table below. Figure 2 is a photograph of the vessel taken during sea trials.
Sea trials were conducted with the Aleksey Chirikov in March 2013 in the Gulf of Finland. In between the standard sea trial program, tests were conducted to study the propulsion system’s response to various combinations of propulsion power and azimuth angles.
Tests were conducted by measuring vibrations from Azipods while constant power and azimuth angle was maintained. Increasing the azimuth angle with high power increases vibrations and, at a certain angular zone, it is advisable to avoid continuous high power to prevent unnecessary loading of the machinery. It is worth noting that the Azipod system, being simple and robust, has considerable tolerance against vibration, especially when compared with systems with a more complex mechanical power train. However, it is only prudent to take means to lessen vibrations, if this can be done while performing all tasks.
Vibration levels depend not only on power, but also on the speed and direction of motion as well as the geometry of the ship’s hull and propulsion system. All possible combinations were not tested due to limited time allocated to the test. Hence, all tests were carried out only in ahead motion (positive rpm in “pulling mode”), in light ice and sea conditions.
In the first test Azipods were gradually turned to toe-in position (see Figure 4) while maintaining high power. In second test, Azipods were turned 90 ° outward, producing no net thrust (Figure 5 and Figure 6). Power was increased step by step, up to maximum power. In the third test, the azimuth angle was gradually lessened.
During the last tests (see Figure 5), with a reverse direction of rotation of the propellers (“pushing mode”), the behavior was somewhat different because the propeller geometry was different. Also, during this last test the propellers started to cavitate slightly before full power was reached. This was due to the fact that propellers were optimized for forward speed bollard pull.
Table 1. IBPSV Aleksey Chirikov main parameters
LOA | 99.9 m |
DWT | 3950 t |
Breadth |
21.7 m |
Propulsion |
2 x ABB Azipod VI1600 total 13 MW |
Figure 3 Propeller wake with 45 ° azimuth Figure 4 Azipod toe-in position (“pulling mode”) Figure 5 Propeller wake with 90° azimuth Figure 6 Azipods turned 90° in reverse rpm rotation (“pushing mode”)
Generally, the vibration levels during the tests remained moderate. While the tests were conducted only in the vessel’s ahead motion, the author’s impression is that an astern operation would make such IM operations even smoother. The Azipod’s mechanical design allows the reverse propeller rotation “pushing mode” (Figure 6) without power or torque limitations. Therefore, if needed for vessel operations, the propellers can be designed to absorb full power without limitation in both “pulling” and “pushing” mode during IM duties.
Results of these full-scale tests can be used to draw up new guidelines for the design of Azipod-propelled vessels, that are to have IM duties, to maximize their IM effect while maintaining long and reliable service life of the relevant machinery.
Azipod ice load measurements on board the FESCO Sakhalin
The measuring system for ice loads on the propulsor for this icebreaker was installed in 2005 during the building stage and the long-term measurements were carried out until 2008. The system measures ice loads on the body of the Azipod propulsor on the shaft bearings. Today the vessel operates under the name SCF Sakhalin.
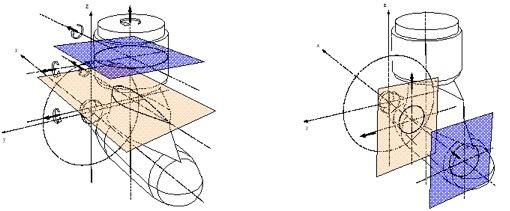
Azipod instrumentation
The loads on the thruster body were measured by strain gauges attached in two different cross sections to the inner structures of the upper part of Azipod. These locations were defined based on stress distribution on the Azipod structure for load cases where longitudinal, transverse and torsion loads were applied at the potential locations of ice loads. The instrumented areas inside the Azipod are shown in Figure 7.
The propeller-bearing loads and the thrust were also measured by strains at the lower part of the Azipod. The propeller bearing loads were measured with strain gauges attached at the supporting structure near the bearing. Strain gauges for the thrust were located at the longitudinal stiffener near the thrust bearing. The instrumented areas in the Azipod shaft line structure are also shown in Figure 7.
The relative shaft line movements were measured with displacement transducers attached close to the bearing housings. The dynamic behavior of the lower body was measured by tri-axial accelerometers located in both bearing housings. Some accelerometers were also attached outside the Azipod in the Azipod room. The hydraulic pressures of the steering motors were measured in order to determine the torque of the steering motors. The ship’s status and environmental conditions were ascertained directly from data in digital format provided by ABB’s and ship’s systems. The measuring signals were transmitted from the turning part of the Azipod by a wireless data link. In total, 53 different signals were recorded, Nieminen (2005) [3].
Azipod ice-load measurement results
Azipod ice load data was collected during normal ship operations over four years. The operations consisted mainly of stand-by and IM close to the Orlan platform (Figure 8a) as well as transit voyages from the platform to the port of Khlomsk.
The measured and analyzed data provides insight into loads in different operational modes and it has been very useful in verifying dimensioning criteria as well as developing Azipod systems for the new type of icebreakers. Some of the major classification societies have been very interested in the results when developing and upgrading their ice rules.
Figure 8b shows global ice loads as a function of the azimuth angle.
To sum up, different IM tasks require different capabilities from the icebreaker. However, elegant vessel designs and the correct selection of propulsion system can produce solutions that work reasonably well for several IM tasks.
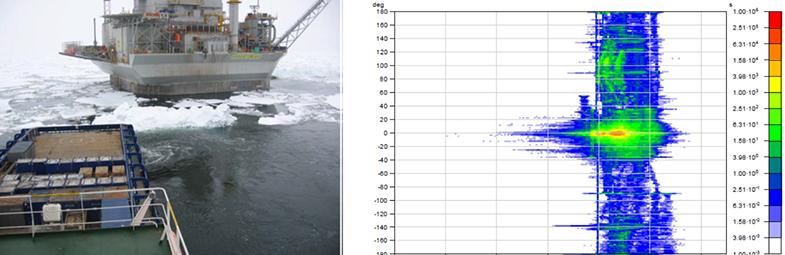
Notes
- Heideman, T. et al (1996). Full-scale ice trials in ridges with the Azipod Tanker Lunni in Bay of Bothnia in 1996. Polartech’96.
- Keinonen, A. (2008). Ice Management for Ice Offshore. Arctic Passion Seminar, March 6, 2008, Helsinki, Finland.
- Nieminen, V. (2005). Ice Load Measuring System of Azipod Propulsion Unit of IB FESCO Sakhalin; Instrumentation and Calibration. VTT research report TU57-055933 (Confidential).
References
Hanninen, S., Heideman T., Toivanen, O. (2014). Results Using Azipod Propulsion in Ice Management Operations. OTC24631, Houston,.Nieminen, V. (2008). Ice Loads on the Azipod Propulsion unit of IBSV FESCO Sakhalin. VTT research report VTT-R-07784-07 (Confidential).