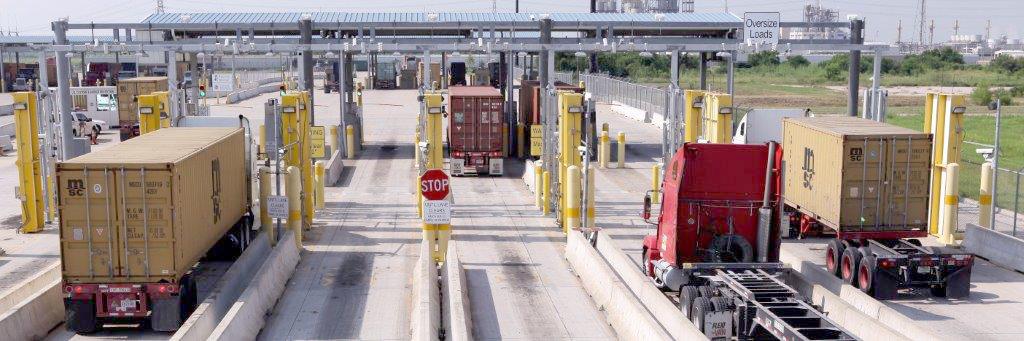
As in other industries, handling automation plays a key role in achieving such development in container handling. Automated systems enable remote operations, i.e., remote control of the ship-to-shore (STS) and stacking cranes as well as remote monitoring of automatic gates, where human intervention is the exception. The efficiency of operations can be further increased through the horizontal integration of these systems and equipment.
The container terminal arena is changing rapidly. More 16,000-19,000 twenty-foot unit (TEU) ships are introduced in the Asia-Europe trade every month. Within the next two years, the average ship size in this trade will reach 14,000 TEU. In addition, the cascading of ships together with a lot of new 9,000 TEU ships will result in a doubling of the average ship size used in all other major trades within a few years. Even if the trade volumes are expected to slowly increase, the number of loops and port calls will decrease due to the increased vessel size. There were 35 vessels coming from Asia to Northern Europe in 2007 every week – this number is now down to 22 and is anticipated to continue to decrease.
Now the challenge for container terminals is to handle fewer but very large calls. Handling 20,000 TEU calls in 48 hours realistically requires about 500 TEU/hour capacity, and shipping lines will not accept lower service levels or longer times at berths. The good news is that container terminals can meet the challenge by deploying advanced equipment and systems already available today.
Right design criteria crucial
Having the right design criteria and taking the correct decisions early in the project is crucial in order to meet the expected cost and performance targets. Thus, designing a greenfield container terminal is no longer just a matter of acquiring the right port equipment and integrating the equipment with an “off- the-shelf” terminal operating system (TOS). It is more a matter of designing and implementing an IT project with completely different capital expenditure (capex) and operating expenditure (opex), compared with designing a manually operated terminal.
One of the pioneers of automated container terminals was the HHLA Container Terminal Altenwerder (CTA) in Hamburg. CTA also automated horizontal transportation. After CTA’s foray into automation, it took some years before the next automated terminal began operation. By 2008, automated cranes had been installed at less than a handful of terminals. So, even though automated container terminals have been around for about two decades, the trend towards automation has only recently taken off. This also means that the competence and understanding of how to build a modern automated terminal is not widespread and there are associated pitfalls.
ABB has a long history of working with automated systems for cranes and terminals. The company has introduced more and more automation functions over the years, which have allowed cranes to be partly or fully automated. Intelligent automation now enables cranes to automatically adapt to changing circumstances, optimizing performance and output.
Considering the challenge of larger ships, taller cranes and bigger call sizes that the container terminals are facing, four success factors of an automated terminal can be identified:
– Efficient STS cranes
– Intelligent automatic stacking cranes (ASC)
– Integration of terminal equipment from ship to gate
– Remote operations from a control room
ABB has, over several years, worked with each of these success factors to develop solutions that meet specific customer requirements, for example, regarding land utilization, safety and environmental aspects.
An automated terminal differs significantly from a manually operated one and requires an evaluation of areas such as:
– Maintenance and service
– Staff and competence
– IT infrastructure
– Risk assessment and safety
– Environmental impact
– Land utilization
Efficient ship-to-shore cranes
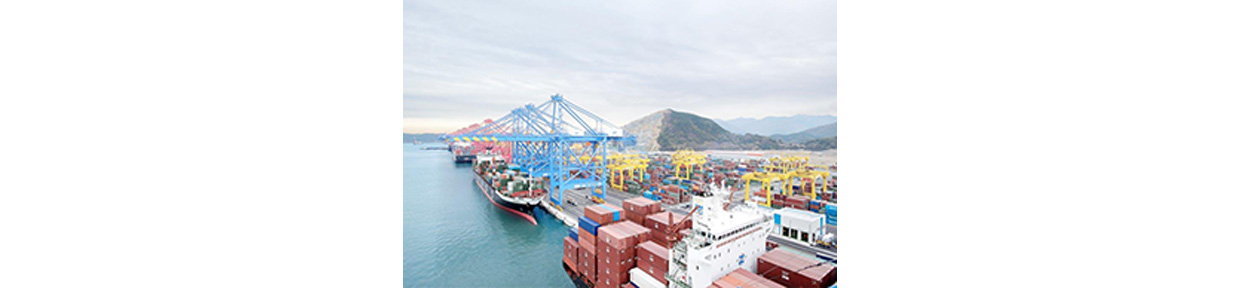
The STS cranes set the pace for the whole terminal. This means that the productivity of the fleet of STS cranes is extremely important for the commercial success of a container terminal. STS crane automation and the remote control of STS cranes are currently major trends that are profoundly reshaping crane operations. The main driver behind these trends is the need for cranes that have a lifting height of more than 50 meters. The need for such lifting heights is due to the larger ships such as the 18,000 TEU Triple-E class ships being put into service. With ships of this size, the travel distance of the trolley also increases and this requires the cranes to be run faster to maintain the productivity level. Moving human operators from the crane cabin and having them operate cranes by remote control and automation allows the full capacity of the cranes to be continuously utilized. It also opens up the possibility for the use of cranes with even higher speeds and accelerations yet to be built.
Today, these functions are available for all types of STS cranes, including double trolley and/or double hoist/tandem spreader cranes. There is a clear market trend towards cranes that can handle multiple containers. For instance, between 2013 and 2015, ABB has and will deliver automation systems, including automatic landing on the quayside, for 33 cranes with double trolley and 46 cranes with double hoist or tandem operation. To date, the largest cranes have double trolley and double hoist and a lifting capacity of 130 tons under the spreader. Automation makes these complex giant machines manageable for operators and terminal logistics systems, ensuring uninterrupted production with high productivity.
Production records verify that automation improves productivity and is also “machine-friendly” since it runs the operation more smoothly than a human operator and leads to less damage to the equipment. This also reduces maintenance costs for, for instance, spreaders. Simulations verify that an inexperienced operator using automation is more productive than an experienced operator working manually.
Automation for STS cranes has the following features:
– Continuous control of the load sway and skew
– Ship profiling and optimum path control
– Optical character recognition (OCR) identification of containers and vehicles enabling automatic handoff
– Measurement of vehicle position and guidance of vehicles
– Automatic container landing on platforms, ground and vehicles
– Single interfacing with TOS for work orders, bay layouts, container and vehicle information
Intelligent automatic stacking cranes
When productivity speeds up at the quay, a fleet of coordinated ASCs becomes a necessity because it is crucial to have a high container through-put to and from the vessels. The yard must be able to fully support the quay operation and deliver good service to landside transportation. During the last decade, many terminals have implemented highly automated stacking cranes. In fact, the number of ASCs delivered and equipped with ABB’s automation system will exceed 500 this year.
Also, stacking cranes are continuously becoming larger and more advanced. Today, end-loading cranes are able to stack five to six tiers high and 10 wide, while the cantilever cranes typically stack six high and 10 to 14 wide.
The handover to all types of vehicles can be automated when proper safety arrangements are implemented. To save time, the cranes operate using an optimum path overlapping horizontal and vertical motion, and multiple cranes in a block are coordinated to avoid waiting times.
Stacking cranes equipped with intelligent automation are able to respond to varying seaside and landside volumes and ensure timely delivery of containers for quay and rail terminal processes. The scheduling function allows the cranes to optimize the use of the cranes within the block based on all known work orders and time constraints. This improves productivity and reduces empty travel and, consequently, energy consumption.
Integration of terminal equipment from ship to gate
The large cargo quantities to be handled in a short period of time are a challenge for the whole chain from ship to gate. Advanced on-dock rail and intermodal facilities can be used to strengthen the chain.Intermodal cranes can be automated to the same level as stacking and STS cranes. Using automated cranes and automated guided vehicles (AGVs), it is possible to move a container from the ship via the stack to a rail wagon without using any manned machine in the process.
In a fully automated terminal, accurate information about container identity and location is of the utmost importance. It is important to eliminate inefficient and risky processes throughout the chain; for example, manual handling of truck, container and driver information at the gate. Also, for STS cranes, manual handling of container and vehicle identification creates unsafe and inefficient handoff processes.
By automating these transfer points with gate, rail and crane OCR solutions, the time spent on handling the containers is significantly reduced, greater inventory transaction accuracy is achieved, truck turn times within the terminal are reduced, and the safety is increased. At the Group Maritim TCB terminal in Buenaventura Columbia (TCBuen), where such a solution was delivered by APS Technology Group, a member of the ABB group, STS crane productivity also increased by three moves per hour thanks to faster handoff of the containers.
Recently, Yilport also selected gate automation and operating solutions delivered by APS Technology Group for its four multipurpose ports in Turkey. Yilport will also implement APS Technology Group automated container identification and handoff solutions at the quay using crane OCR at its facilities in Gebze, as well as at its new terminal, Gemport, under construction in Gemlik. With these solutions, Yilport will be the first terminal operator in Europe and the Middle East to manage exceptions across all gates and cranes at multiple terminals from one central and remote location in real time. The solution also provides full support for Yilport’s enterprise reporting.
Remote operations from a control room
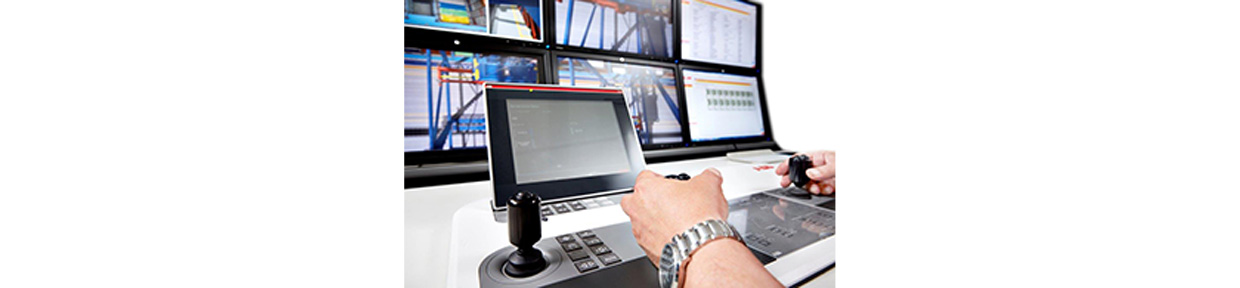
Today, remote operation and exception handling are an integral part of automation that enables people to be separated from machines and moved from a dangerous and harsh working environment to the safety and comfort of a control room. The remote operation also creates an attractive working environment for the next generation of port staff and reduces absence.
Due to the increasing height and capacity of the cranes, the working environment of STS crane operators has been deteriorating over time in spite of investments made in better cabins, etc. This undesirable development needs to be turned around if operators are to work until the steadily increasing retirement age for this occupation without developing health problems caused by poor working conditions.
ABB has developed new ergonomically designed remote control stations for operators monitoring and supervising automatic cranes and for handling exceptions. The layout of the joysticks and controls in the remote control station is the result of careful ergonomic analysis of operators’ workflow and cooperation with crane operators. The controls are positioned in a way that supports the operator’s natural workflow.
There is one additional benefit with operations from a control room that deserves to be highlighted. Remote operation means that the team comes together in one location. The terminals are run by a team of motion, logistics and maintenance specialists who handle the planning and manage exceptions together. This results in a new level of collaboration and team spirit because everyone easily interacts and shares the same view.
Systems like the ABB Terminal View provide an overview of the entire terminal. This enables a multidisciplinary group to identify bottlenecks, which optimizes processes and sets priorities to increase productivity.
The recent orders for cranes and other equipment show that the industry is moving towards more advanced equipment, integrated systems and automation, involving the whole chain from ship to gate. Automated horizontal transport is being delivered to several terminals.
ASCs are the forerunners of automation and are now moving the automation frontier to new regions like Central America with projects in Mexico and Panama. For example, the Manzanillo Terminal (MIT) in Panama is strengthening its yard crane fleet with six automated cantilever stacking cranes, which will operate alongside the existing rubber tyred gantry cranes (RTGs). This is a good example of how automation can also be deployed in an existing terminal to significantly increase the terminal’s container handling capacity.
The changes that we now see in the industry are based on urgent needs and the availability of suitable technologies. This means that we will see a fast transformation of our industry within the next few years.
In addition to a clearly improved working environment, remote operation increases productivity, improves safety and reduces energy consumption in the following ways:
– Supports seamless operation without any loss of time at shift changes/breaks, etc.
– Eliminates time and cost needed for transportation of staff to cranes.
– All cranes are immediately available; for example, moving four containers from a feeder vessel takes a few minutes instead of up to an hour when you do not have to move the operator to/from/between crane(s).
– Onboard cameras provide better views than is possible from the cabin in situations like landing containers on a ship/vehicle or handling hatch covers close to ground.
– No need to change into special clothes and gear.