Figure 1 Additional resistance from different external factors Figure 2 Draft histogram of a modern 30,000 DWT MPP operating over a year Figure 3 Speed histogram of a modern 30,000 DWT MPP operating over a year Figure 4 Main engine output histogram of a modern 30,000 DWT MPP operating over a year Figure 5 Relative cost of fuel of a Suezmax tanker
Along with cargo capacity (normally referred as deadweight), speed is one of the most important variables because it affects the transport capacity. The transport capacity of a fleet is a function of its cargo capacity and speed. Any change to these two variables has implications on the supply of that fleet, often measured in ton-mile, and potentially on the freight rates. This is probably why shipowners have always dedicated so much time to deciding on the right speed for their next vessel. On the surface this might sound awkward, but there is a big difference between 13 and 14 knots in power terms.
Once the speed – among the other design parameters – is defined, the designer runs a series of iterative calculations around the different elements of ship design: structure, stability, propulsion and so forth. When it comes to propulsion, the designer seeks optimization of the propulsion plant so that the vessel can achieve the design speed with the minimum amount of fuel, that is, maximization of the overall propulsion efficiency at a certain draft/deadweight.
Consequently, if the ship operates outside of the design point, the propulsion plant will not work to its full potential. In order to evaluate the impact of this insight, we need to evaluate how often ships operate outside their design point.
For this purpose, it is worth looking into three different types of operation:
A. Ships that operate consistently at their design speed and design draft
B. Ships that operate at a different draft from their design draft
C. Ships that operate at a different speed from their design speed
Ships that operate consistently at their design speed and draft
One of the key parameters for the design of the propulsion plant is the effective power (PE), which is the necessary power to move the ship with a certain draft at a certain speed (normally the design draft). Not long ago, estimating the effective power was a complex and non-exact affair, which required tank test validation if risk mitigation was sought. However, in today’s world of power computers, most designers have access to computer fluid dynamics (CFD), which adds considerable reliability to the power estimation process.
Nevertheless, power estimation techniques are not yet able to accurately calculate the effect of weather and waves, and even if they did, the weather conditions that a given ship faces over its lifetime is so diverse that such calculations would not add much precision to the end result. Consequently, the industry has tackled this effect by adding an empirical margin to the required power. This margin is known as the sea margin (SM) and is normally within 10 to 20 percent.
As a result, the installed propulsion power – usually referred to as break power (PB) – is calculated as follows:
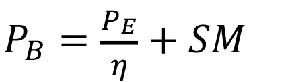
where η is the total propulsion efficiency
By adding the sea margin, it is possible to maintain the design speed up to a certain level of added resistance due to sea and wind. Consequently, when the added resistance from sea and wind is low or even negligible, the required power to maintain the design speed is much less and therefore the propulsion plant operates away from the design point.
There are, however, other factors that affect the overall resistance and thus the power demand. Examples of some of these factors, which are accounted for in the sea margin, are:
– Trim
– Fouling of the hull
– Roughness of the propeller blades
– Use of lifting devices such as rudders and stabilizers
Most ships face frequent variations of weather and sea conditions, and their hulls accumulate fouling and their propellers lose efficiency over time. Consequently, even a ship that operates at a constant speed does not operate at constant power and, therefore, operates most of its life outside of the design point, whatever that may be. This point is illustrated in Figure 1, where different external factors add to overall resistance in different combinations, depending on the operating condition.
Ships that operate at different drafts.
A tanker with a deadweight of 160,000 tons at a draft of 17 meters (the typical size of a Suezmax ), for example, will require power of about 15.6 MW at a speed of 14.5 knots (including a 15 percent sea margin). However, when sailing in ballast condition with a displacement of about 75,000 tons, the same vessel will only need about 8.6 MW to reach the same speed in the same sea and weather conditions. Even assuming the weather and sea effects – as well as the others listed above – are constant, the power requirement for the ballast leg is about half the power requirement for the laden leg. Traditionally, these vessels operate at a higher speed when sailing in ballast, but still at considerably lower power levels. Typically, the power requirement for the ballast leg is about 20 percent less than for the laden leg.
Thus, vessels that operate at different drafts, like tankers and bulkers, operate outside of their design point, not only because they are exposed to the same external effects described above – weather, sea, fouling, etc. – but also because they operate at a lower draft for half of the time.
Ships that operate at different speed
Container carriers are required to meet tight schedules so that the overall logistics chain runs smoothly and efficiently. This means that a ship might sail each leg at a different speed on a round voyage. A large container carrier typically has a top speed of 24+ knots and spends most of the time sailing between 14 and 22 knots. The histograms below show how often a modern 30,000 DWT multipurpose ship (MPP) operates outside its design point for draft, speed and power for a year. The vessel operated at a lower than design draft most of the time and below 40 percent of the design point engine power for more than 80 percent of the time.
In all three types categories of operations illustrated above, the propulsion power required to move the ship at a certain speed, with a certain draft under specific conditions, varies considerably. This means that the vessel operates more than often outside of its design point. However, the majority of ships are designed and built to meet a certain energy efficiency (normally measured in daily consumption) at the design point for draft and service speed.
When a vessel is built at design point, every system is designed to maximize the overall efficiency at that point. In other words, if a 160,000 DWT tanker is designed to operate at 15.5 knots, both the hull shape and propulsion plant are designed to minimize the fuel consumption at that speed and draft, taking into consideration a certain sea margin for the added resistance from sea and weather. That means the overall propulsion efficiency is maximized at that point leading to lower efficiencies when operating outside of it.
A new era of flexibility
Shipbuilding contracts specify what the consumption of the vessel at the service speed should be and thoroughly prescribe methodology to access such consumption. However, a shipbuilding contract rarely specifies consumption at a wide speed and draft range in a legally binding way. Even chartering contracts are very specific on the fuel consumption the vessel should attain at the service speed and design or maximum draft.
However, the industry has witnessed some changes in recent years that are making shipowners, charterers and shippers look at fuel efficiency in a new light. One such change is the development of the relative cost of fuel.
Figure 5 illustrates the development of the fuel cost for a Suezmax tanker over the last 24 years. From 2009 onwards, the cost of the fuel compared with the cost of the vessel increased dramatically. Such scenarios have, for the first time, put the topic of fuel efficiency on the agendas of senior executives leading the industry into a new age. Although most shipowners are now very sensitive about fuel efficiency, leading shipowners are already looking into how to spread fuel efficiency over a wider operational range. In other words, how to design and build ships that are more flexible.
Trends in ship design
The need for more flexible ships has led some shipowners to engage designers to come up with new solutions. One of the emerging trends is the optimization of the hull shape around more than one design point. In other words, the hull shape is designed to achieve a balanced efficiency based on a number of operating points rather than attain the least possible fuel consumption at a single draft and speed.
There are, however, other tools to achieve more energy efficiency at a wider operational range. By combining a two-stroke diesel, gas or dual-fuel engine with an electric motor, it is possible to improve fuel efficiency at a wider range of operating points.