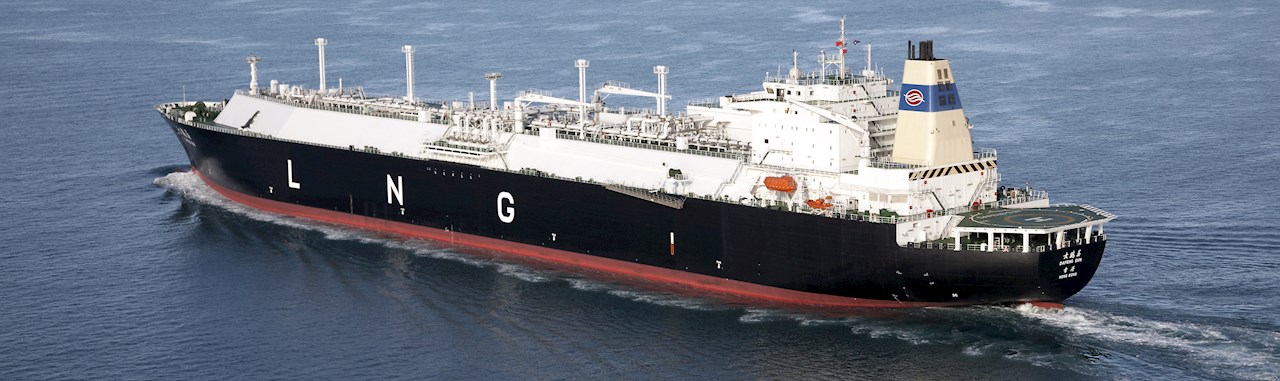
ABB technical experts explain the technology behind these advanced vessels that enable them to provide the world with a regular supply of gas.
The global consumption of natural gas has increased considerably in recent years. In 2012 it was 2,987 million tonnes of oil equivalent (mtoe) , compared with 1,768 mtoe in 1990. According to BP’s latest Energy Outlook, the consumption of natural gas is expected to reach 4,631 mtoe in 2035, as shown in Figure 1. By then, and for the first time ever, the consumption of natural gas will be as much as that of coal and oil – about 25 percent of global energy consumption.
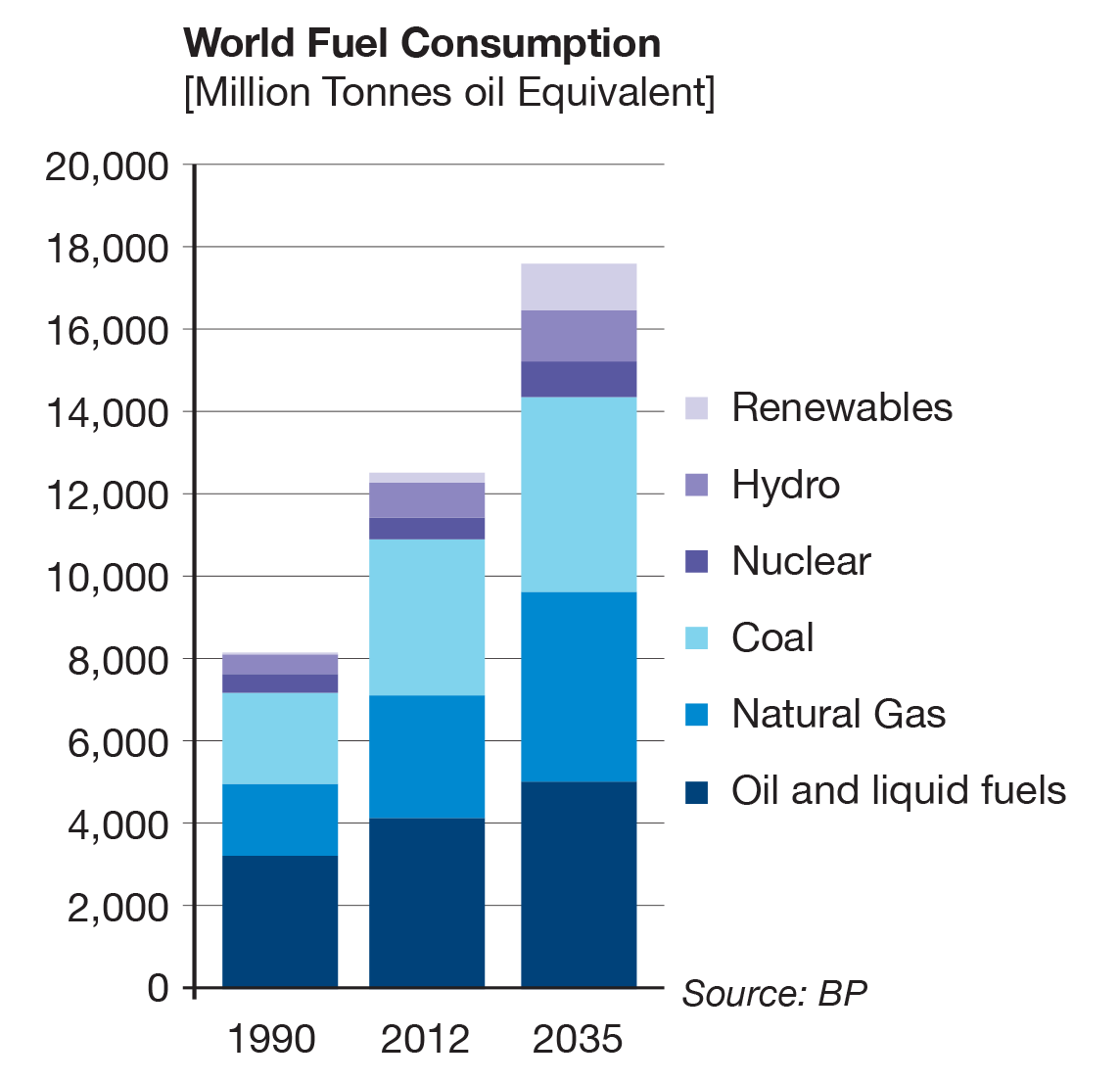
The increased consumption of natural gas is mainly driven by lower price, as compared with other fuels, but also by its environmental footprint – the combustion of natural gas releases much less CO2 per energy unit than other fossil fuels.
As of today, about 90% of the gas produced worldwide is transported by pipeline from the gas field directly into the consumers’ location. In 2012, world production of natural gas was 3,364 billion cubic meters (bcm), of which about 70 percent was consumed within the country of origin. The remaining 30 percent was exported to other countries both through pipelines – 706 bcm – and shipped by sea – 328 bcm. Although the amount of natural gas transported by sea only accounts for 10 percent of world consumption, this is significant share of the natural gas traded between countries –, about 32 per cent.
In order to make the sea transport of natural gas effective, and therefore economically feasible, it needs to be converted into liquid, known as Liquefied Natural Gas (LNG). The liquefaction of natural gas is possible by lowering the temperature of the gas to –163oC. The cooling process occurs at complex liquefaction plants located at deep sea ports and connected to the gas fields by pipeline. Once in liquid state, the LNG is then transferred into an LNG carrier. In order to safely transport 180,000 m3 of gas at –163C across the ocean, LNG carriers have complex and unique systems – for example, cargo containment, cargo cooling, regasification, electrical propulsion, etc – that comprise a technologically advanced vessel.
On the other hand, these vessels are no longer expensive machines used to transport small parcels of gas that cannot be transported by pipeline. They are becoming an important part of the natural gas logistics chain. Consequently, LNG carriers are required to perform to very high standards of reliability so that the gas is delivered on time without compromising safety of life, the environment and the cargo.
Some LNG carriers are built for a specific trade, and are therefore designed for a very specific mission. However, the increased dynamics of this market, and the tendency for the commoditization of these vessels, suggests that flexibility is likely to become the most appreciated feature.
The first LNG carrier with electrical propulsion was ordered in 2003 and delivered from 2005 and onwards. Since then, the use of electrical propulsion has increased rapidly, with about 17 percent of the existing fleet equipped with electrical propulsion. However, it appears that this is only the beginning of the story since 71 percent of the LNG carriers on order will be equipped with electrical propulsion, as shown in Figure 2.
Electric propulsion for LNG carriers

ABB is the largest supplier of electrical propulsion systems for LNG carriers. The advanced power solution developed by ABB Marine for LNG carriers is based on ABB’s highly reliable portfolio of generators, switchboards, transformers, variable speed propulsion drives and motors. These components are combined together with an advanced protection and power management system specifically developed for this type of vessels.
LNG carriers meet the most stringent requirements for regularity and reliability in delivering the gas to the destination on time. Electric propulsion and control systems are vital installations with built-in redundancy to minimize the risk of interruption of the transportation.
Electric propulsion technology has replaced the traditional steam turbine system. This was a well proven and reliable solution for LNG carriers, which used excess gas from the cargo tanks in boilers to produce steam. However, some years earlier, engine makers had launched power plant combustion engines able to use both diesel oil and gas as fuel – so-called dual-fuel engines. These engines are superior to the steam turbine system in terms of efficiency and, combined with electric propulsion, this system also developed the necessary reliability to meet the ship-owners’ and charterers’ most stringent requirements for the regularity of their fleet of LNG carriers. So when the first new propulsion system was ordered in 2003, others followed almost immediately with new orders. By 2005, almost all newbuild LNG carriers of standard size (140 000 cbm to 180 000 cbm) were ordered with the new propulsion system. A lot of effort was put into making the design as robust as possible and providing the required redundancy to meet the requirements. During the last 10 years of operational experience, the system has proved itself by the fact that today the majority of newbuild LNG carriers are still using the same system.
During the first years of development, the main focus was on the power and propulsion plant itself and, with small variations, the configuration has been the same for all vessels: two variable speed electric propulsion motors (total propulsion power in the range of between 20 and 30 MW), each fed by dedicated frequency converters. Figure 3 shows the typical layout. The power plant has been configured by four or five engines in the range between 5 and 12 MW, and using a system voltage of 6,6kV. Since electric propulsion in itself was not new, all components and configuration were available from other vessel types. Most effort was put into the control system and adapting it to this specific application. The main difference between this vessel type and others that use electric propulsion (for example, cruise liners) is, firstly, the use of gas as fuel. The power plant thus has different characteristics, particularly for handling load variations from the propulsion plant, as the engines have a slower response to transients in gas mode than in liquid fuel mode. Secondly, these vessel act as a long distance pipeline and end consumer expect them to provide a regular supply of gas. This means these vessels have very strict time slots on the way to the terminals, setting high requirements on the availability of the power and propulsion plant.
While the second challenge is mainly addressed by hardware, multiple configuration of components as motors, converters and generators, the first issue is basically addressed by the propulsion control system and its application software. This control system is designed to handle all kind of combinations of running generators and fuel usage. In the most complicated scenarios, we can imagine that one or two engines are running on gas, while others are running on liquid fuel, and this can change back and forth for several reasons. For example, ambient temperature determines the amount of boil-off available, and there may then be different scenarios of running the power plant either with mixed fuel or combinations.
All these scenarios have different characteristics and the challenge is to combine all this in an intelligent way in the control system in order to simplify the user interface into simple start/stop buttons and levers for speed and power control. A typical propulsion control configuration is shown in Figure 4.
Figure 3 LNGC typical electric power and propulsion configuration Figure 4 Propulsion Control System Figure 5 Records from blackout prevention test
Another task for the propulsion control system is the blackout prevention function. This is achieved by a combination of relatively simple power availability limitations to more advanced limitation based on various parameters from the stability of the power plant and quality of the gas fuel to the engines. However, the important thing here is having fast communication between the “brains” of the power plant (the protection relays) and the “brains” of the propulsion part (frequency converters/propulsion control). Having a proper interface here and using the best practices available, it is fully possible to obtain a good blackout prevention system. Figure 5 is an excellent example of this. The figure was recorded from a sea-trial for an LNG carrier with four generators, 3 x 11MW and 1 x 5.5MW. All three generators were tripped intentionally one by one in order to fully test the system and, even when the last one was tripped leaving only the smaller generator online (5.5MW), the propulsion system was fast enough to reduce the propulsion power and keep the power plant alive, while still having enough power for safe maneuvering.
In recent years, the power and propulsion plant has been supplemented with equipment enabling remote monitoring and diagnostics. This has been achieved by tailoring some special computer systems to communicate directly with the equipment on board, accessing all possible variables and parameters. This system started with the frequency converters, which are the most advanced components onboard, but also the easiest to repair if the fault can be located. This system enables an ABB engineer to address various issues remotely, and guide the crew to do corrective actions before the situation becomes critical in terms of keeping to the ship schedule, etc. The system was later expanded to also include monitoring of control systems and protection relays and is today under continuous development to handle the complete set of equipment defining the total power and propulsion plant for LNG carriers.
Figure 6 offers a closer look at the building blocks of an advanced monitoring and maintenance system and how the information is shared between different layers of the integrated system, taking all advantages of intelligent devices, protocols and condition monitoring techniques.
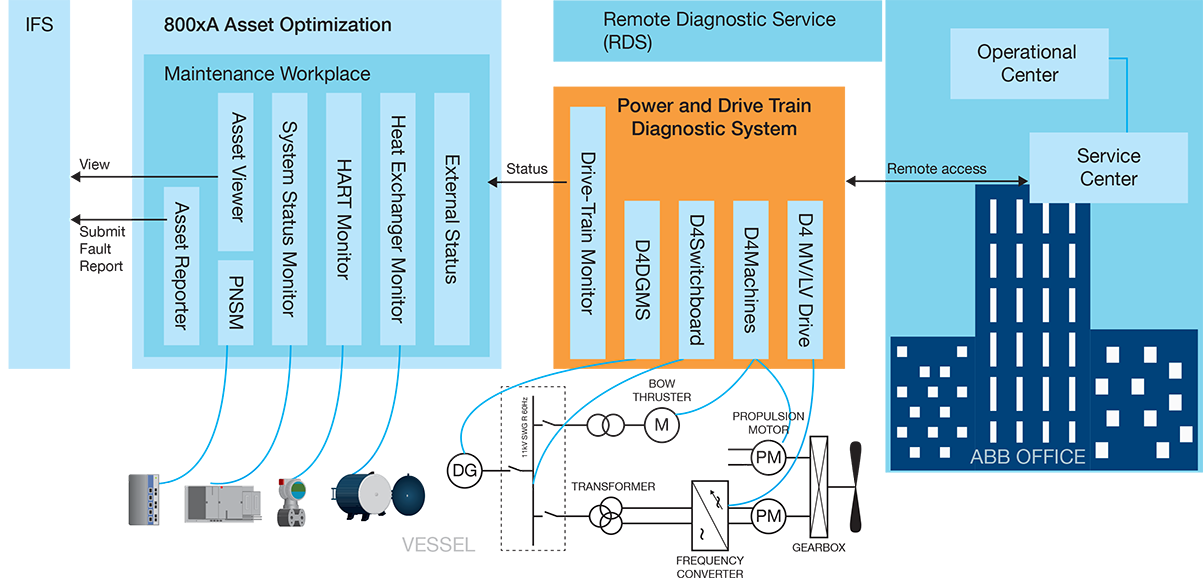
Examples of diagnostic solutions are related to the monitoring of the electric power-drive train system on its component and subsystem level. In practice, the monitoring system for electric propulsion can be delivered with or without integration to upper automation system.
When a case is under discussion, it is natural for the operator is to navigate to the maintenance workplace screen and read the exact fault message generated by the intelligent device itself (frequency converter), together with all the troubleshooting hints associated with it.
If the crew onboard is familiar with the equipment and, based on the information received from the maintenance workplace, is able to fix a faulty component, the rectification process ends at this point and the system is put back to operation. This may not, however, be the case if the reason for the trip is unknown. Calling service specialists from the original equipment vendor may be required in this case and will undoubtedly lead to even longer downtime and additional expenses.
This can, however, be avoided. Modern, advanced integrated automation systems can be equipped with a secure, satellite link to the onshore support center that can be used by the same service specialist within minutes of a request. The support engineer would, in this case, look into another layer of the automation system – a diagnostic and monitoring system specifically designed to continuously collect all necessary, high resolution measurements from critical components.
The principle of data logging and analysis that takes place at the diagnostic level of the system involves taking all the advantages of intelligent devices (such as protection relays, frequency converters and PLC controllers) and using them exclusively for troubleshooting and condition monitoring. The successful introduction of advanced diagnostic techniques depends on the availability of good quality, high-resolution measurement data that typically cannot be provided from the legacy control systems. On the other hand, since physical wiring and cabling is usually limited to interfaces defined for control and protection purposes, the scope and quality of available signals is quite limited at the upper level of the control and automation system that can be effectively used by a diagnostic system for detailed troubleshooting and advanced condition monitoring.
The solution is the use of communication protocols such as IEC 61850, together with all the additional means of connectivity that modern intelligent devices offer. In the fault rectification scenario presented earlier, the same support engineer would access high-resolution data loggers (sampled with, for example, 10kHz) that were recorded by the device at the moment it was tripped and stored for further fault tracing analysis by the diagnostic system. Such an analysis, remotely performed, would identify the root cause of the problem and lead to rectification and restarting of the system in the shortest possible time.
Events and transient recorders from each individual protection relay are uploaded to the diagnostic system and presented on the same chart having a common time axis. Since protection relays implement SNTP time synchronization and are synchronized to the same master clock, the analysis of electrical fault propagation across the MV switchboard can be done at the system level with the time span manipulated from single milliseconds to several seconds.