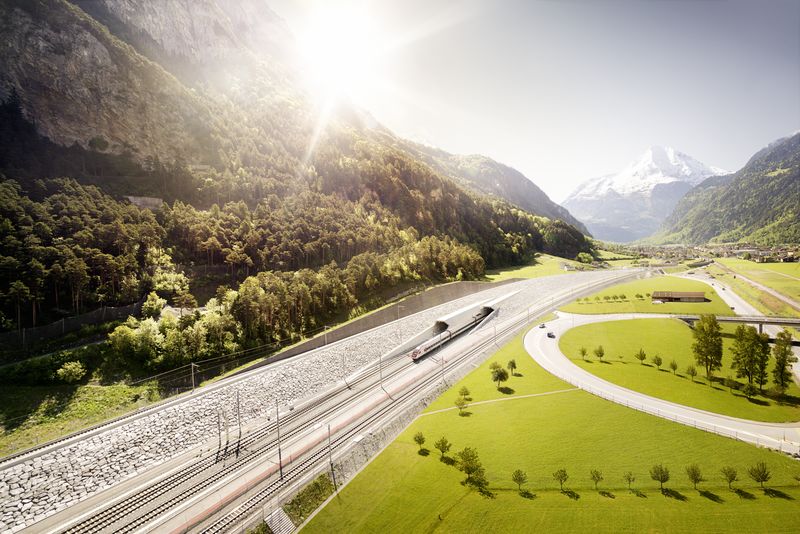
At 57 kilometres the Gotthard Base Tunnel is the world’s longest railroad tunnel, connecting northern and southern Switzerland. In addition to increasing freight capacity along the Rotterdam-Basel-Genoa corridor, the tunnel will include regular passenger services that significantly cut travel time from north to south.
During its construction, excavated gravel was transferred to either entrance and to a central portal. The central portal featured an elevator, which carried the material, some 850 meters (m) to the surface (see figure 1). During the 14 years of construction, the elevator carried out more than 84,000 lifts, removing 28,200,000 tons of gravel.
The elevator’s motor was speed controlled with an ABB medium voltage drive that used ABB’s IGCT (integrated gate-commutated thyristor) power semiconductor switches.
Image currently unavailable
Image currently unavailable
Image currently unavailable
Image currently unavailable
Image currently unavailable
Image currently unavailable
Image currently unavailable
Image currently unavailable
Image currently unavailable
Figure 1: The 57km long Gotthard railway tunnel showing the gravel elevator located at Sedrun. Foreground: Conveyor system with a roll diameter of 4.8m. Background: Service elevator. The conveyor’s 4,176 kW synchronous motor.
Following completion of the tunnel, the medium voltage drive was decommissioned. The IGCTs were returned to ABB’s semiconductor facility so that an analysis of their electrical performance could be compared with the original specification of 15 years earlier. No significant shift or degradation of the electrical parameters were found. The hermetic ceramic housing of the power semiconductor was still perfectly sealed.
The analysis focused on the turn-off circuit involving the gate unit and in particular the parallel connection of dozens of electrolytic capacitors and dozens of MOSFETs (metal-oxide-semiconductor field-effect transistor).
Original gate impedance measurements from the device qualification were compared against devices of different ages that were either in operation (including the ‘Gotthard devices’) or held in storage. Here, again, no significant degradation of the gate circuit impedance was found (see figure 2).
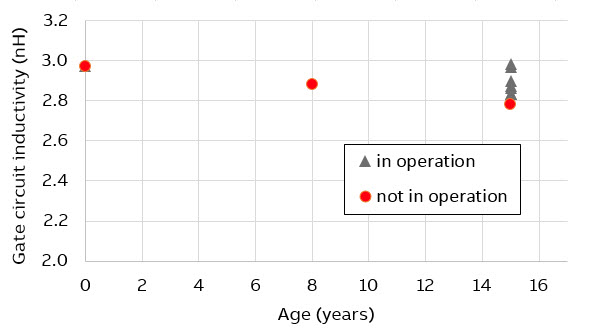
When the elevator was lifting gravel to the surface, the silicon chips would rapidly heat and cooling fast on stopping for loading or unloading. This exposed the IGCT devices to heavy load cycles during operation. A detailed examination of mechanical wear of the device’s construction was carried out. While there was evidence of wear, actual degradation was low. For instance, the degradation of the cathode metallization is shown in figure 3.

ABB offers its customers analysis of failed devices. Some customers use this service extensively and return almost all failed devices. This presents ABB with the opportunity to improve the IGCT’s application conditions from the customer’s perspective, as well as improve the general IGCT design and manufacturing.
Furthermore, a reliable field failure can be calculated with a Pareto of main failure root causes. Such an evaluation shows an IGCT field failure rate of below 100 FIT (failed devices in 109 operating hours). The failure cause divides nearly 1:1 between power semiconductor and gate unit.
The overall field failure rate is state-of-the-art for power semiconductor devices. Additionally the failure ratio indicates no significant issue with the gate unit. This overall picture can be completed by a specific application with known load on the devices.
Impulse for this analysis
Since the first commercial IGCT device application in 1997, more than 250,000 units have been installed. The majority are still operating in demanding and reliability-critical applications like medium voltage drives, interties, breakers, FACTs and others.
One feature that generated much discussion is the full load current, which needs to be commutated to the gate path through the gate unit. While this allows the safe and rugged turn-off of the thyristor structure as a transistor, it also provides a powerful and reliable gate unit that takes the full phase current during turn-off for micro seconds (see also figure 4).
Often the massive need of parallel connected (several tenth) electrolytic capacitors and MOSFETs in the turn-off circuit were predicted as potential reliability issues in the technical community, although this aspect was thoroughly accounted during the development phase.
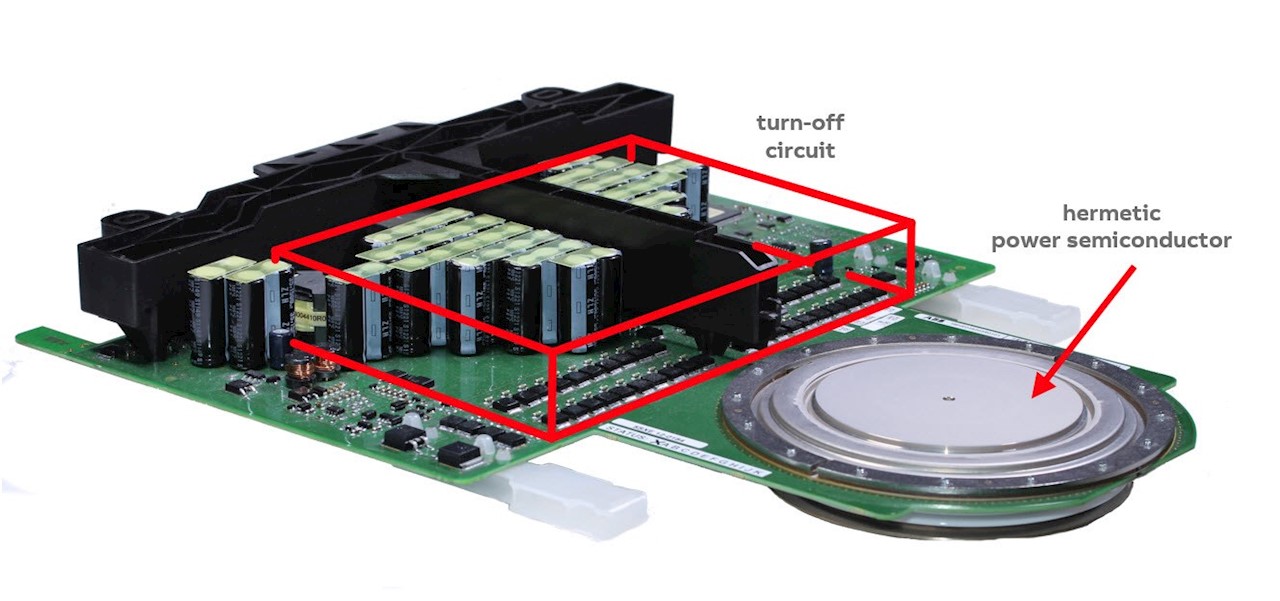