Reports from the UN climate change conference (COP26) held in Glasgow made it clear that time is running out for implementing concrete actions, if we are to meet the Paris Agreement to stop global warming and keep the global temperature rise below 2° Celsius. In practice, this would mean cutting carbon dioxide (CO2) emissions to half, while it is forecast that electricity demand coming from heating and transportation will continue to increase 40-60 percent until 2050. From this perspective, it is evident that emission targets cannot be achieved without having smart Energy and Asset Management as the highest priority.
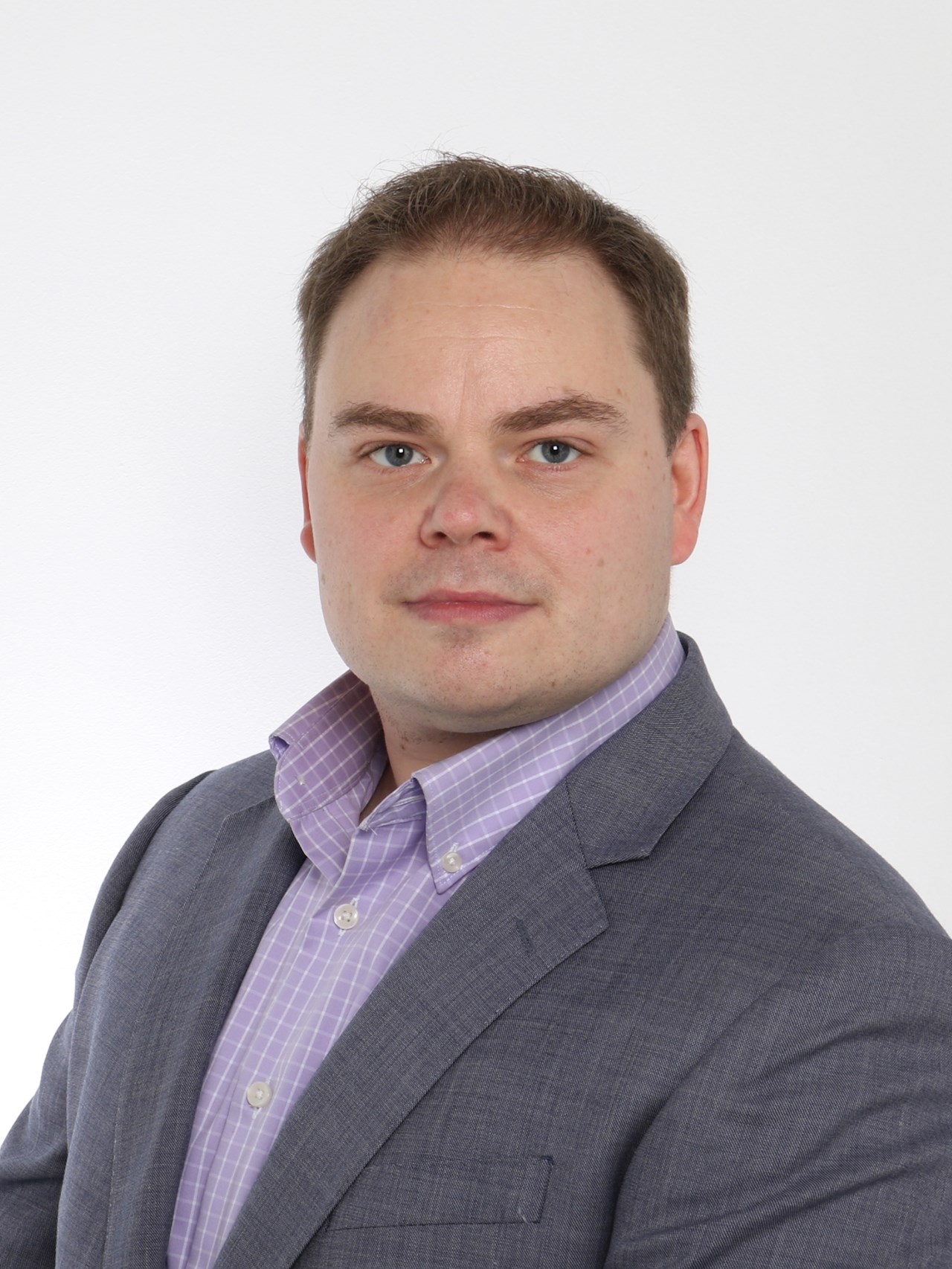
Clean Energy Management Ministerial and ISO 50001
One of the major communities that drive energy efficiency and a cleaner future topics is the Clean Energy Management Ministerial (CEM). The global forum promotes policies and programs that advance clean energy technology, to share lessons learned and best practices, and to encourage the transition to a global clean energy economy. The community has members from around the world, including the US, Canada, the UK, Australia, China, India, Saudi Arabia, Russia, Germany, Italy, Spain, Finland, and Sweden.
Energy Management Working is a priority initiative at CEM, promoting ISO 50001 as a “proven framework to manage energy use.” Part of the promotion involves giving Energy Management Leadership awards to organizations that have implemented the standard – to recognize their efforts in transforming their organizations and the ways in which they have found ways to save energy and reduce costs. With this practice, CEM shares experiences to inspire others to follow suit.
According to the Energy Management Working Group, energy management systems have the potential to save up to 30 percent of the total energy use in industry and up to 40 percent in commercial buildings. Thus, implementing ISO 50001 globally could cumulatively cut energy use by 62 exajoules by 2030 – saving more than $600 billion in energy costs and avoiding 6,500 megatons of CO2 emissions, which is equal to taking 215 million passenger vehicles off the road.
One impressive example is from Canada, where industrial companies that have implemented ISO 50001 have achieved an average cumulative energy performance improvement of nearly 10 percent within the first two years. This has resulted in up to $2 million in annual energy cost savings for large Canadian companies.
In some countries, like in Finland, commercial and industrial buildings are required to do energy audits regularly. Also, in this case, becoming ISO 50001-certified is an advantage. With an ISO 50001-certified monitoring system, building owners are exempted from doing manual checks and costly audits on site. These kinds of regular manual checks can be replaced by certified, automated monitoring and measurement systems, that can be either running on premise or in the cloud.
Asset management’s role in energy efficiency
How can then asset management contribute to an energy efficiency standard such as ISO 50001? ISO 50001 promotes usage of the continuous improvement circle: Plan – Do – Check – Act and repeat. One of the key points is the evolution from checking to acting. To be able to identify the points of the distribution network where the power losses are happening, one needs to have energy measurements in multiple parts of the network. However, this provides only the information that you need to act, not necessarily how to act.
How do we move from the collected data that provides information of the need to the knowledge of what to do? Let’s take one example: Based on past experience, we know that if there are loose connection joints inside switchgear or panels, it results in heating of the joints. This means that part of the energy is consumed in order to pass through the loose joints. With correctly placed temperature sensors and asset monitoring features this can be easily detected, without having to visit the site. This also means we can plan to carry out maintenance work at the site more accurately and thus reduce the time needed on site. These are great both from both cost and safety perspective; better planning leads to a safer working environment and reduced time on site means cost savings.
As you can see, I clearly distinguish between data, information, and knowledge. The reason to create these borderlines is that I strongly believe that it is not always necessary to collect the data in a central location. The key thing is that information that can be processed and automatically converted into actionable knowledge is available in the central location; processing the data to information can be done on the edge or in the cloud. Or as it’s sometimes called ‘in the fog’, which in meteorological terms would refer to ‘a cloud close to the ground’.
Let’s take a practical example from a switchgear installation; we can have a protection relay and other monitoring and diagnostic devices that gather data from the sensors and utilizes the communication network to pass that data onto the central location, i.e., the asset monitoring system. From the asset monitoring system, the operator gets the knowledge to act upon. With such fully digitalized and correctly maintained medium-voltage switchgear with 14 feeders, you can save energy losses equal to 150 tons of CO2 during 30 years of service. That’s equivalent to the emissions produced by a mid-sized European car driven for 1.250.000 km.
In summary:
- To be able to get information about energy efficiency, you need an energy monitoring system
- To be able to transfer the information to actionable knowledge, you need an asset management system
- For knowledge creation, data processing can happen in multiple places and the actionable insights need to be collected in the central location
Conclusions
Examples have shown that organizations that have implemented ISO 50001 have reduced energy costs and increased competitiveness, while minimizing greenhouse gas emissions.
Also asset management plays a pivotal role in maximizing energy efficiency. By applying both approaches real gains in both sustainability and competitiveness are possible. The benefit of combining asset and energy management is that you can
- Identify where the power losses are
- Identify equipment that possibly contribute to the energy losses (e.g. switchgear power loss analysis, measurements before and after the transformer)
- Track the service record of the equipment
- Better plan when to do maintenance or replace equipment
About the author
Ville Luoma was the Common Platform Manager and chief product owner for the ABB Ability™ Energy and Asset Manager platform in ABB’s Electrification Business Area. Ville joined ABB in 2005 and he has held several positions in global product and software development management. Ville now works for ABB Large Motors and Generators as Digital Lead.