Jani Hakala, Janne Pohjalainen, Veli-Pekka Peljo ABB Marine and Ports, Helsinki, Finland, jani.hakala@fi.abb.com, janne.pohjalainen@fi.abb.com, veli-pekka.peljo@fi.abb.com
The International Maritime Organization (IMO) has issued resolutions to substantially cut greenhouse gases (GHG) emissions in the coming decades [1]. It will be challenging to achieve this target without major technological advances in fuel and propulsion technologies and the more widespread adoption of alternative energy sources such as batteries and fuel cells. ABB’s latest innovation that addresses this rapidly evolving environmental compliance landscape is the ABB Dynafin – a cycloidal-type propulsor that meets the urgent demand for higher efficiency and emissions reduction →01.
Image currently unavailable
Image currently unavailable
Image currently unavailable
Image currently unavailable
Image currently unavailable
Image currently unavailable
01a Two (shown here) or even four sets can be fitted to a vessel. 01b Each blade is individually controlled and can rotate, as can the main wheel onto which they are mounted.
01 The ABB Dynafin.
How the ABB Dynafin works
The ABB Dynafin concept is essentially a cycloidal propeller with individually controlled blades. The operating principle allows the unit to utilize a trochoidal blade path →02. (A trochoid is the curve generated by a point on the radius of a circle as the circle rolls on a fixed straight line.) Trochoidal propellers have been studied before, but until now, technology constraints have prevented them from being commercialized and introduced to the market.
Image currently unavailable
Image currently unavailable
Image currently unavailable
Image currently unavailable
Image currently unavailable
Image currently unavailable
02a Epicycloidal path of a blade with eccentricity and advance ratio λ<1 (cycloidal propeller). 02b Trochoidal path of a blade with eccentricity and advance ratio λ>1 (trochoidal propeller).
02 Trochoidal propeller behavior [2].
The ABB Dynafin generates thrust by means of profiled blades that project from the bottom of the ship. Each blade can rotate both around the global axis of a main wheel and around its own local axis, which acts as a pivot point for enforcing a prescribed pitch motion →01b. The thrusting blades’ trajectories resemble those of the tails of whales and dolphins. This sort of pitch motion leads to a very high propulsive efficiency. The propulsor can also change thrust direction almost instantaneously, increasing vessel maneuverability. In contrast, an azimuth thruster, where a conventional propeller is rotated around the vertical axis to direct its thrust, is slower and thus less effective in maneuvering the vessel.
Several key factors drive the high efficiency of the ABB Dynafin:
Larger propulsive area
The larger propulsive area covered by the ABB Dynafin lowers the loading of the propeller, giving the lowest thrust-loading coefficient. The lower this coefficient, the higher the ideal open-water efficiency of a propulsor. Further, the Dynafin’s geometry makes it ideal for shallow-water vessels as it does not protrude as much as an equivalent screw propeller.
High aspect ratio and no rotational component
The high blade aspect ratio (basically, blade length divided by width) significantly increases each blade’s lift/drag ratio so it is much higher than a conventional screw propeller. Further, screw propellers with rotation axes parallel to the inflow induce rotational losses in their wake; this is avoided in the cycloidal propulsor as there are no major rotational components in the wake flow.
Individual blade control
Each blade is individually controlled by an electric motor, a frequency converter (to control torque and rpm) and control logic. This enables the imitation of the highly efficient movements of a whale’s tail and adjustment of the blade movement (eccentricity, advance ratio and angle of attack) depending on different vessel operational situations, maximizing efficiency and thrust in both transit and dynamic positioning (DP) modes.
A major difference to a typical fixed pitch propeller, which is optimized to a single operational point, is that the ABB Dynafin can adjust the movement of the blades continuously to meet optimal performance over a wide speed range and different wake fields. The unit’s control and software technology opens up the possibility to continuously improve and optimize the vessel’s performance throughout its lifetime, creating the concept of a “digital propeller.” The ABB Dynafin can also be operated in “rudder mode,” meaning that all the blades are controlled as conventional rudders. This feature can not only bring benefits for double-enders and sail-assisted vessels but also increases redundancy in failure situations, providing partial steering capability.
Minimal hull appendages
Propellers with a traditional shaft line require a rudder and struts for the shaft, which induce additional drag. For a cycloidal propulsor, there is no need for a rudder and the only parts protruding from the hull are the blades. Thus, there is minimal added drag, improving the vessel’s hydrodynamic performance.
Moreover, the high efficiency of the ABB Dynafin means smaller power plants can be used, leading to a more flexible general arrangement, more room for cargo and passengers and lower maintenance costs. Additionally, maneuverability is enhanced by combining the propulsion with an intelligent control system, which also results in more efficient and safer ship operations.
Precise propulsion control
Rotational movement of the main wheel is produced by an electric direct-drive motor. The main wheel rotates at a relatively low 40 to 80 rpm and has four to six identical blade modules. Rotation direction is kept the same under all operational situations and thrust amount and direction are determined by a combination of main wheel rpm and blade adjustment.
Models and modeling
The development of the ABB Dynafin was greatly aided by using computational fluid dynamics (CFD) simulations (to evaluate hydrodynamic performance) and scale-model open-water testing →03-04. Propulsors were retrofitted to a platform support vessel (PSV) hull to obtain a direct comparison against existing Azipod® units in the same power range. Following the successful simulations and model-scale tests, ABB engaged in productive discussions with several ship design offices, shipyards and ship owners and operators to validate the feasibility of the concept. The ABB Dynafin concept was unveiled to the market in mid-2023.
Image currently unavailable
Image currently unavailable
Image currently unavailable
Image currently unavailable
Image currently unavailable
Image currently unavailable
03a Fluid flow around individual blades. 03b Twin-set simulation.
03 With almost limitless possibilities, CFD simulations provided the fastest and most cost-efficient way to investigate hydrodynamic phenomena and to improve the concept. These two low-resolution screenshots illustrate how simulations can be performed of different aspects of the design.
Reducing underwater noise pollution
In addition to GHG emissions, underwater radiated noise (URN) is increasingly recognized as a major issue due to its potential effect on aquatic ecosystems. Limits on URN are expected in the near future. The ABB Dynafin minimizes electromagnetic noise by having the electric motors inside the vessel’s hull. Low-pressure pulses and blade-tip speeds create less cavitation and turbulence, resulting in low hydrodynamic noise. In addition, individual blade control enables optimized trajectories to minimize hydrodynamic noise in different operational situations.
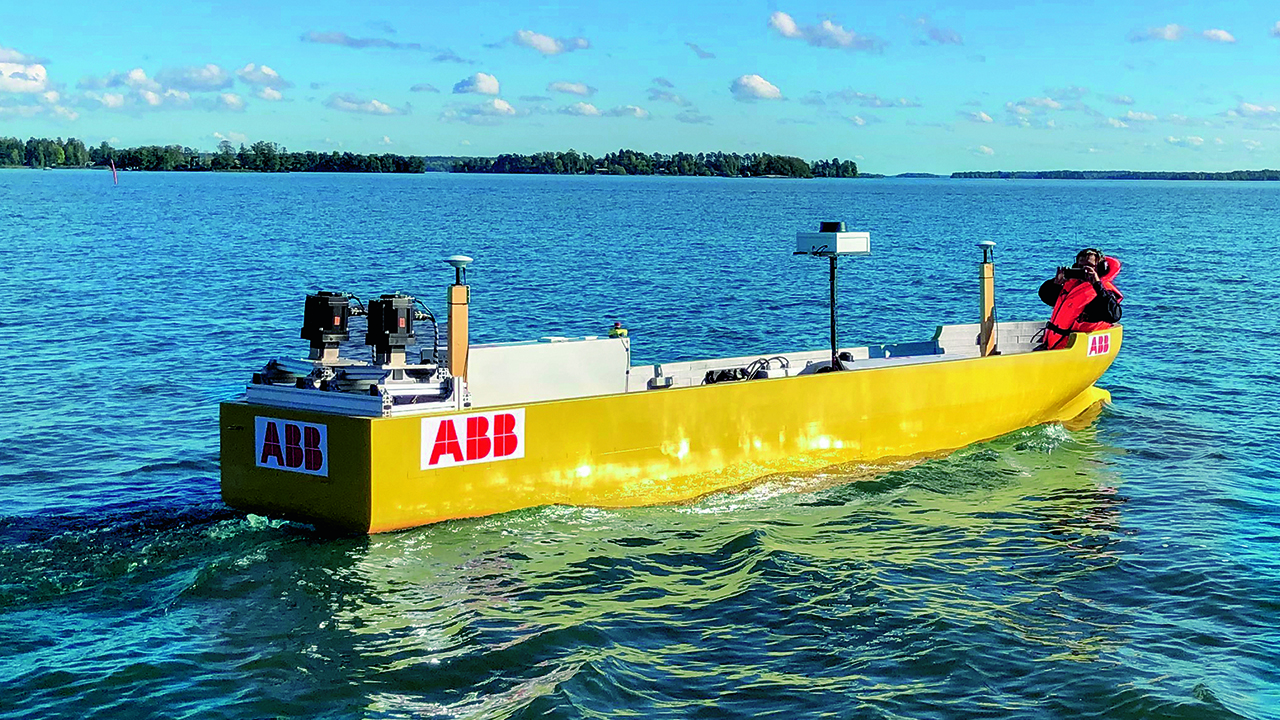
Wide-ranging application
Initially, ABB is concentrating on developing the ABB Dynafin units in the power range of 1 to 4 MW per propulsor. With four units installed, up to 16 MW applications can be covered. In addition to having a direct electrical power train for both the main wheel and the blade modules, a mechanical bevel gear may be used, allowing connection to the main engine and extending the benefits to vessel segments where electrical power trains are typically not used.
Propelling shipping into the future
ABB Dynafin’s higher total efficiency compared to existing propulsion systems leads to direct savings in fuel costs and makes it possible to reduce the size of the vessel’s power plant. This latter aspect is particularly beneficial to hybrid or fully battery-powered vessels, as the size of costly battery banks can be minimized. Lower fuel consumption, enabling smaller fuel tanks, and a smaller footprint of the power train, provides more flexibility in general arrangements and more space for passengers and cargo. These indirect savings can have a significant positive financial impact. In addition to high efficiency, the ABB Dynafin enables superior vessel maneuverability, lowering costs and increasing safety.
ABB’s expertise in hydrodynamics, mechanical systems, ship electrification, automation and control put the company in a unique position to further improve the ingenious ABB Dynafin. The ABB Dynafin will add a new level of adaptability and intelligence at the heart of propulsion performance and change how the shipping industry thinks about propulsion systems.
The ABB Dynafin improves many aspects of a vessel’s performance, from efficiency through reliability to crew and passenger comfort:
CUSTOMER BENEFITS
High efficiency
• Open-water efficiency up to 85 percent.
• Significant fuel savings, resulting in emissions avoidance.
• Less installed power, supporting the electrification of vessels and utilization of greener fuels.
Excellent maneuverability
• Instant control of thrust and its direction, supporting operational safety, flexibility and DP capability.
• Suitability for demanding operations and sea conditions.
High reliability and easy maintenance
• Combined propulsor and steering and a direct electrical power train for the main wheel and the blade modules result in fewer components.
• The absence of wear-sensitive gears and the main wheel’s moderate 40 to 80 rpm minimizes component wear.
• Easy access to the main wheel, enabling inspection and replacement of many components from inside the vessel, improving the ability to monitor components, increasing vessel availability and shortening dry-dock stays.
• The unit’s modular structure and higher degree of standardization simplify spare-part management.
High onboard comfort level and sustainable operations
• Low rotational speed minimizes cavitation, pressure pulses, noise and vibration.
• Low underwater noise, enabling operation in sensitive marine areas.
Video explaining Dynafin “Introducing the revolutionary ABB Dynafin™ – the latest propulsion innovation by ABB” (hosted on Youtube)
References
[1] International Maritime Organization, “Revised GHG reduction strategy for global shipping adopted.” Available: https://www.imo.org/en/MediaCentre/PressBriefings/pages/Revised-GHG-reduction-strategy-for-global-shipping-adopted-.aspx#:~:text=The%20revised%20IMO%20GHG%20Strategy,points%20for%202030%20and%202040. [Accessed December 10, 2023.]
[2] Fasse, G. et al., “An experimental blade-controlled platform for the design of smart cross-flow propeller.” Available: https://www.sciencedirect.com/science/ article/abs/pii/ S0029801822003547. [Accessed October 12, 2023.]