- Optimize maintenance schedules by using digital data to assess individual robot performance
- Quickly identify the most stressed robots in a production line
- Real operational data enables fast fault diagnosis and improved planning and budgeting of spares
It is becoming increasingly important for industrial companies to connect their robots digitally and to gain insights into the state of health of their mechanical workforce through targeted data analysis. Conventional maintenance follows a rigid schedule, where all robots are serviced once a year or after 20,000 operating hours, regardless of their workload or how much or how little they were used.
ABB's way is smarter: data collected through condition-based maintenance provides an individual health record for each individual robot. By showing exactly which axes are overloaded or stressed, the data can reveal whether a particular robot’s gearboxes are susceptible to faster-than-normal wear and will need to be replaced. By using this data, tailored maintenance schedules can be created for the robots that need the most attention, saving costs and reducing production downtime.
Data collection
ABB is one of the pioneers in the field of data-based analysis. Since 2002, long before the general wave of digitization, ABB has been collecting data on the performance of its installed base of robots. As a comprehensive record of a robot’s performance, the data provides an accurate indication of a unit’s health status, including the wear of certain mechanical components such as gears and balancing units. Technically, the analysis works as follows: The robot controller processes and stores data in real time.
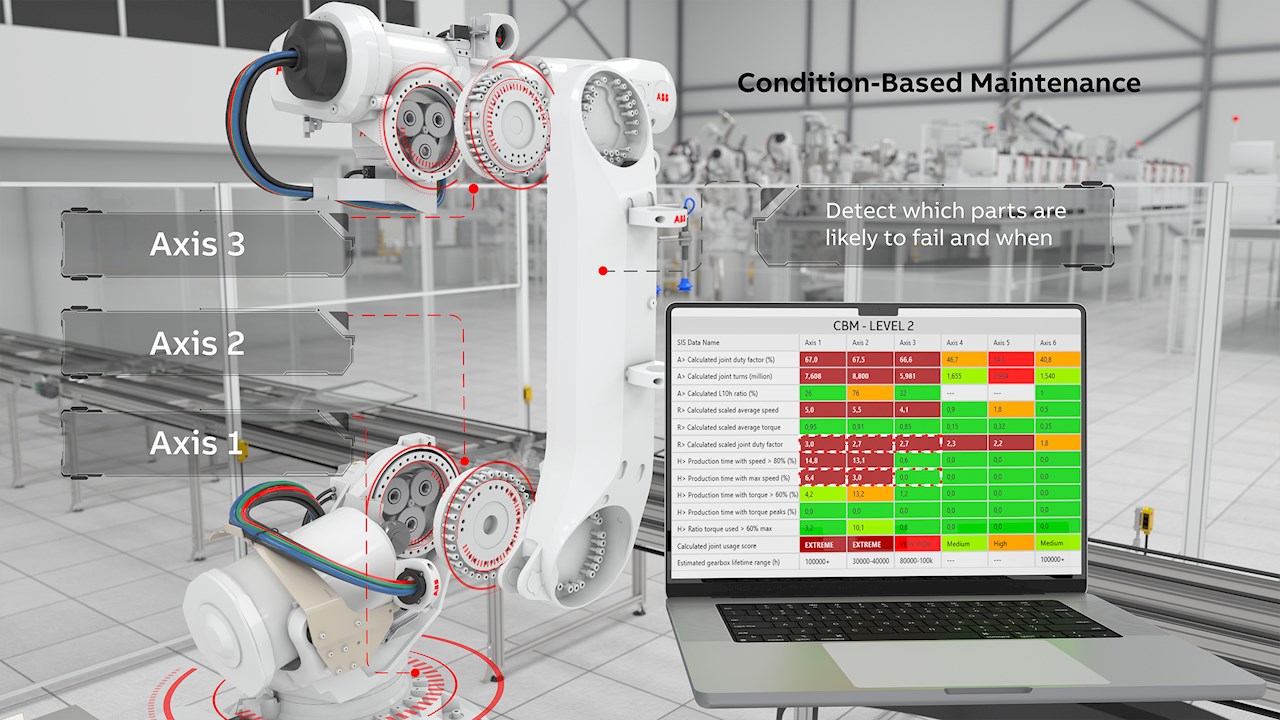
This is exclusively movement-related data, covering a compilation of the movements of the robot joints such as torque, acceleration, or the ratio of idle time to movement time. No sensitive data such as information on part variants or cycle times is recorded. The protection of production privacy has top priority.
Unlocking optimum robot performance with Condition-Based-Maintenance If a robot were a human, ABB’s Condition-Based Maintenance (CBM) service would be equivalent to a comprehensive blood count analysis. Data is gathered and evaluated, and the findings provided to customers as a two-level analysis. At the first level, the entire robot fleet is considered, and the most heavily used robots are identified. At the second level, the most heavily used robots are checked even more closely. ABB experts will then make further analysis to find the causes of the overload and recommend a tailor-made maintenance strategy.
The advantages of condition-based maintenance for the customer are obvious: they receive an exact health report for some mechanical components that is individualized for the type of robot used and recognizes where there is a statistical risk that a robot might fail. This type of data-based maintenance is much smarter than general preventive hours or time-based maintenance of all robots.
The ability to devise Condition-Based Maintenance plans for individual robots means that servicing is always performed at exactly the right time. By preventing excessive mechanical stress that can cause premature failures, these tailored plans can save companies money and time through reduced maintenance and disruption to production.
In addition to the optimal maintenance cycles, Condition-Based Maintenance has other advantages for customers. Equipped with real-time operational data, they can better plan spare parts stocks, budget precisely, and increase the service life of their robots. And for suppliers, there is another decisive advantage when it comes to quality management, with Condition-Based Maintenance being included as part of the quality management audit required by the customer to prove the increased production reliability.
A complete diagnosis
As well as showing which robot needs maintenance, the precise analysis used by ABB also allows conclusions to be drawn about which specific axes of the robot are the most stressed. This enables the issue to be precisely located, and concrete recommendations given by ABB experts about the most suitable services.
The benefit this can bring can be highlighted by the example of an incorrect configuration or poor implementation of the robot program. If left unresolved, these can have an impact on stress and wear. Without identifying the cause, another replacement of the replaced part is just a matter of time and a ticking bomb. By using the analysis data to identify both the problem and its cause, stable production can resume, with an attendant reduction in costs by eliminating unnecessary downtime and parts replacement.
A critical aspect of a robot’s design is its use of compact gears, which have been used in robots on various axes since the 1990s. While they allow for a slim design, they are also the most expensive mechanical parts of a robot. As such, any failure of the gears can be costly. Intelligent maintenance saves money here. During operation, the bearings can shed metal which collects in the oil. To avoid permanent damage, the oil must be changed after 20,000-24,000 hours of operation to reduce the level of iron debris in the oil. If the analysis can prevent a failure of a compact gear, the analysis pays off due to the high costs for a new compact transmission.
The importance of the duty factor
The duty factor reflects the overall activity of the robot. The impact of the duty factor varies depending on the robot application – see chart below.
Typical duty factor impact by application:
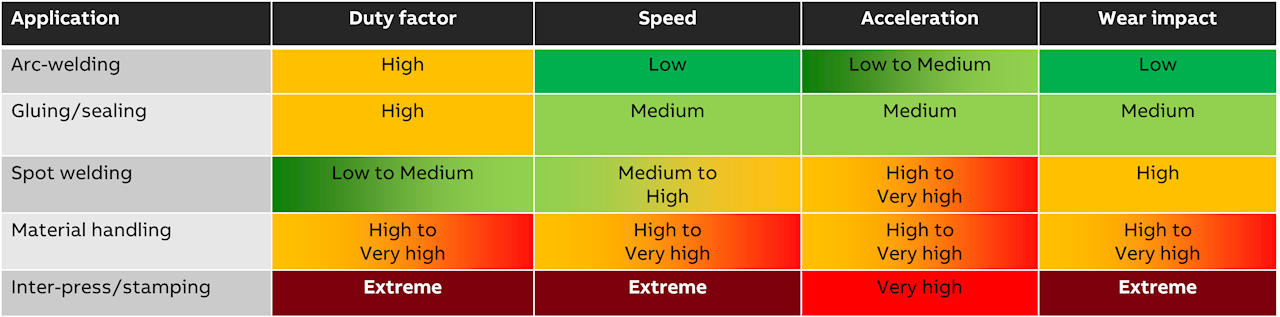
The customer receives the result of the analysis in clear reports that help them to justify the maintenance costs internally. As a rule, with such an analysis, less than five percent of the robots are under pressure to act.
The report shows exactly which axes have been particularly stressed and require maintenance, enabling the customer to take the appropriate actions.
Summary
As more factory floors introduce robotic automation, the ability to perform tailored maintenance based on accurate individualized condition monitoring and fault diagnosis is key to optimizing production performance and ensuring maximum availability of robots. Truly unique in the industry, ABB’s data-based analysis achieves this by enabling optimal robot maintenance planning and maximum production reliability. ORIGINAL ARTICLE IN GERMAN: Datenbasierte Roboter-Wartung: Mit optimalen Wartungszyklen Produktions-Stillstände vermeiden - Destination Zukunft (abb.com)