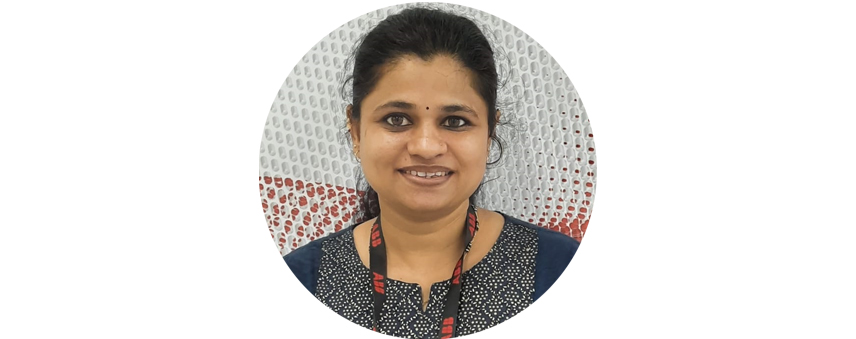
About me
As an Advanced Process Control (APC) engineer, my 15 professional years of experience have been both challenging and rewarding. My role involves implementing control strategies to optimize and enhance the performance of industrial processes. Over the 15 years in the industry, I have had the privilege of meeting different people worldwide and being exposed to understanding their challenges, which has made me a better individual. My name is Ashwini Ujja, and I studied chemical engineering. I started my career as a trainee in the cement industry as an operation and maintenance engineer before moving to the optimization side through advanced process control and related technology. My experience as an APC engineer implementing ABB's Expert Optimizer has married my passion for engineering with economic optimization. It is a dynamic and challenging field that offers many opportunities for growth and innovation.
A recent project I was involved in:
My last project was with a leading cement manufacturing company in Turkey, one of the significant global cement-producing countries. Over the years, the customer has grown from a small cement plant to a conglomerate of companies with a diverse portfolio. Today, it operates in various countries and exports its products worldwide.
My project involved the Pyro area (Calciner + Kiln + Cooler) of the Grey clinker production line. ABB received the order post covid period, however, travel restrictions were not completely lifted. This meant that the project involved remote commissioning, where my remote work started with securely transferring the software installation files to the site server, installation of ABB's Expert Optimizer software, establishing the OPC connectivity between the Expert Optimizer system and OPC server for communication to the plant's control system.
To understand the optimization challenge, I thoroughly analyzed the existing process with multiple inputs from the plant team. I collaborated with the plant operators, management, and engineers to gather data to understand the process dynamics.
Using this information, I developed a control strategy incorporating traditional control techniques and Model Predictive Control. I implemented the APC system by integrating it with the plant's distributed control system (DCS, communicating via OPC). I conducted extensive testing in different scenarios to ensure its effectiveness and robustness. I guided the customer's automation team in building safe switching logic, allowing the operator to turn APC on with the correct modes. Then, multiple setpoint transfer tests were performed to ensure bump-less transfer of the APC setpoint to the DCS when APC mode was turned on and off.
Calciner Control was the first focus of implementation. During the initial plant analysis study, I observed that the existing control had high variation in the temperature, as it involved feeding alternative fuels (a non-conventional fuel that is substantially non-coal based), e. g, municipal waste, car tires etc. Control of alternative fuels is always a challenge with traditional control methodologies.
I conducted multiple-step tests on coal, stand-by coal, and alternative fuels to understand the process response and system dynamics. Further, these step test results are used to develop the models in the APC modeling tool. ABB's Model Builder develops these models’ using techniques like state space, graphical, and sub-space models for linear and non-linear processes. The tool can validate the model with the step test data. The validated model is then loaded into the control strategy. The calciner model was built to accommodate both the temperature control and the disturbance created due to the uneven flow of the alternative fuel.
Calciner control model structure:
Manipulated Variables (MV)
- Calciner Coal
- Stand -By Coal
- Alternative Fuel
Control Variables (CV)
- Calciner temperature
- 5th cyclone bottom temperature
- Calciner O2
- Calciner CO
Temperature variation decreased within 3-4 hours of running the plant in Expert Optimizer mode. It was closely monitored, and necessary adjustments were made to improve efficiency further. Next, we started testing the control for different scenarios, for example, maximization of alternative fuel feeding, limiting coal feeding, stand-by coal reduction, alternative fuel failure, temperature control during alternative fuel flow disturbance, high CO condition, Low O2 condition, etc. The significant stabilization of the process was one of the first observed benefits.
Upstream stabilization always positively affects downstream units, such as the kiln. Also, operator buy-in is now much easier due to the initial benefits observed from the calciner application. Kiln and Cooler implementation also started with a step test campaign, modeling, data validation, and loading the model and strategy to the online engine. The following control loops were considered for kiln control:
Manipulated Variables (MV)
- Kiln Feed
- Kiln Fuel
- Kiln Speed
- ID Fan Speed
Control Variables (CV)
- Kiln Torque
- Pyrometer Temperature
- Kiln Inlet analyzer NOx, O2 and CO
- Preheater Exit O2 and CO
- Clinker Free lime and Liter weight
Regular operation of Expert Optimizer control is supported by interrupt actions that ensure abnormal operating conditions are controlled, and the process returns to normal—for example, High CO, Analyzer Cleaning, and Ring Action. Expert Optimizer is smart enough to detect these abnormal operating conditions and automatically make corrective control moves, preventing the process from drifting to unstable conditions.
One common challenge is the management of change and buy-in from operators. One way to counter this is getting plant personnel involved early and imparting as much knowledge as time allows. During the project, I provided training and documentation to the plant operation and automation team, ensuring they understood the Expert Optimizer control loops and could effectively operate them.
Though many challenges were faced during the implementation, like frequent plant breakdowns, maintenance shutdown, and availability of the remote connection, I am proud to say that the project was completed on time with collaborative support from both teams.
The project aimed to achieve the below KPIs:
- Reduce process variability
- Increase throughput and yield
- Reduce specific energy consumption.
- Expert Optimizer utilization above 90%
The customer conducted multiple tests in batches post-commissioning to evaluate the project's benefits. The results of the test were positive. The plant achieved significant energy savings with high utilization time. Expert Optimizer also enhanced process stability, resulting in lower product quality variation. The overall test results were consolidated as follows:
- Reduction in the free lime variation by 60%CO Calciner 1 (ppm)
- Increase in throughput by 1.2%
- Reduction in energy consumption by 1.6%
- Utilization time > 95% during the test period
The project has paved the way for winning repetitive order of both (White and Grey) clinker lines, expanding to other geographical locations outside of Turkey and increasing the scope to include grinding mills.
Being an APC engineer requires a strong foundation in process engineering, control theory, and plant economics. It also demands excellent problem-solving skills, attention to detail, and collaboration with multidisciplinary teams. It is also gratifying, as the benefits achieved are frequently quantifiable and often link to the sustainability objectives of the plant and organization!