Hoists perform a range of critical functions in a mining operation, playing an essential role in their pair and maintenance of plant and mobile assets. Simply put, hoists lift what people cannot, which makes them potentially hazardous to operators. For that reason, mining companies want a trusted name in hoists, and few are more respected than ABB.
A trusted name
More than 130 years of experience has refined ABB’s approach to mine hoist technology. It is the only original equipment manufacturer (OEM) delivering complete systems based on customised designs for electrical products and mechanical equipment. ABB provides low lifecycle cost solutions with high reliability and system availability. Customers can expect short project execution time and a single source of supply for the complete system, including service and spare parts. Over its lifespan, ABB has delivered more than 1000 hoisting solutions around the globe.
Elevating safety
With well over a century in the industry, ABB has helped to drive the evolution of hoist safety to what it is today. ABB technical product manager for its Safety Plus for hoists portfolio Alonso Morey discussed the development of hoist safety in themining industry. “ABB has been a global leader in the development of mechanical and electrical equipment for hoists for 130years. We have been always at the forefront of hoist safety,” Morey told Safe to Work.
“Hoists are complex machines. Historically, hoist safety meant having an independent system monitoring the movement, speed and position of the hoist. “This included high reliance on the skill of the operators for other manually-controlled protective functions, such as not starting the hoist if a gate is open. These systems would then be able to activate emergency braking if necessary.
”Hoist safety, according to Morey, really began to evolve with the idea of functional safety standards– an objective, quantitative measure of safety. Unlike subjective measures and manual inputs from an operator, functional safety standards include expanded automatic responses from the machine itself. Automatic prevention of cagemovement while the doors are open is one application of functional safety. In 2005, Australia became the first country in the world to mandate functional safety standards for hoists, defining what protections a hoist required and with which safety integrity level (SIL).
“Soon after, the IEC [InternationalElectrotechnical Commission] standard 62061 was released, which provides requirements to manufacturers of machines for the integration of functional safety standards,” Morey said. “This is now standard in Australia. Since then, the Australian guidelines were updated in theTechnical Reference Guide for Powered Winding Systems by the New South Wales Resource Regulator in 2020.
“Regulations became more specificabout the different safety functions necessary for different types of hoists and applications.
Functional safety at heart
When it comes to regulations, “Australia led the way for functional safety”, according to Morey. “That of course led customers and end users to adopt a view that functional safety for hoisting is the right way to go,” he said. “ABB has always been known for its safe hoisting systems, so with the shift to the more objective functional safety principles we redesigned our systems to meet and exceed the latest standards.
“These are built into the machines, automatically detecting danger and engaging safety mechanisms. That way risk is transferred from the operator to the automated control system.
Hoist safety has had a long history in Australia but has reached its zenith with ABB’s Safety Plus for hoists,the first SIL 3 (Safety Integrity Level) certified suite of solutions for hoists. A SIL measures the probability of failure of functional safety features ondemand. There are four levels of SIL, up to SIL 4 (SIL 3 for machinery). As the rating increases, the higher the safety level of the machine and the lower the probability of failure.
ABB goes one step further, having its Safety Plus products independently SIL 3 certified by the Research Institutes of Sweden.The Safety Plus suite is composedof three solutions: the hoist monitor, the brake system, and the hoist protector. These have been rigorously examined and certified, and strictly developed in accordance with the ‘safety of machinery’ standard IEC62061. The Safety Plus hoist monitor comes fitted as standard to new ABB hoists but can also be easily retrofitted to existing mine hoists, sending acommand to apply safety brakes and remove motor torque in the event of a position, speed or movement-related safety hazard.
The hoist monitor can detect a vastrange of hazards, including critical overspeed, overwind/underwind, encoder drive failure, protection by pass, worn friction linings, rope slip, rope miscoiling, slack rope, unclutcheddrum movement, roll-back andincorrect direction.
The Safety Plus brake system can guarantee SIL 3 protectionfunctions such as:
- bringing the hoist to a safe state after a safety circuit trip
- holding the hoist unbalancewhen stopped
- preventing unexpected brakerelease when mine personnelare embarking or disembarking the cage
- holding the unclutcheddrum unbalance
- controlling hazardous energyduring maintenance
- lowering the hoist unbalanceunder gravity force in case ofextended power outage or failure of the drive system.
The Safety Plus hoist protector extends safety functions beyond themine hoist itself to the rest of the hoist infrastructure.The hoist protector is capable ofmonitoring maintenance lock-outsand emergency stops in areas such as the hoist house, headframe and shaft locations, as well as shaft accesslevel gates, boarding and maintenance platforms, and tail rope wander. These solutions come together with ABB’s long history in the mining industry, as well as its vast network ofinternational experts, to create a titan of mine hoisting safety.
“Independent SIL 3 certificationmeans that you don’t have to takemy word that we take safety veryseriously,” Morey said.“We are proud to offer hoistingsolutions that are safer than what mostapplications would require.”
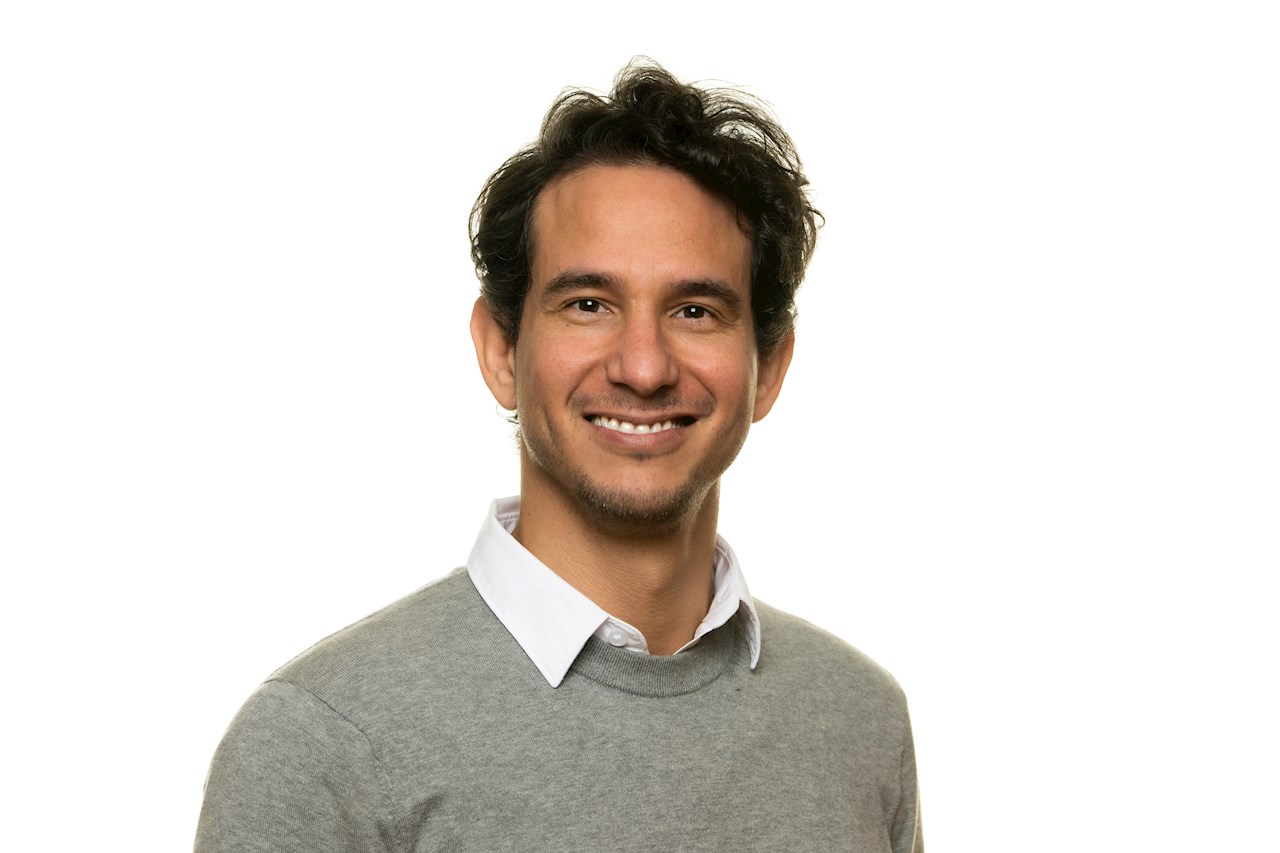
Alonso Morey pictured left, is the Technical Product Manager - ABB Ability™ Safety Plus for mine hoists.
This article was first published in the Jan/Feb 2024 edition of Australian Mining | Safe to Work.