Beyond mass customization, "lot size one" production is the newest trend in discrete manufacturing. However, to be cost-efficient, such production systems must self-configure for any individual product design without human involvement and any individual product must be quality-perfect. How can this be achieved?
Dirk Schulz ABB Corporate Research Ladenburg, Germany, dirk.schulz@de.abb.com; Lars Simora Busch-Jaeger Elektro Lüdenscheid, Germany, lars.simora@de.abb.com
From automotive to commodity goods, mass customization is the state-of-the-art in discrete manufacturing. In Industry 4.0 (the current trend of automation and data exchange in manufacturing technologies), one of the drivers is to cost-efficiently manufacture highly customized consumer goods in small batch sizes – literally down to “lot size one”.
A good example of a product for which a lot size of one is desirable is the ABB-tacteo® KNX control element for smart buildings, where consumers can specify the functionality and look of each individual product [1]. To make such a perfectly individualized product, there are two main challenges: To be cost-efficient, the production system must self-configure for any individual product design without the need for human involvement; and, as essentially no spares are being produced, any individual product must be quality-perfect.
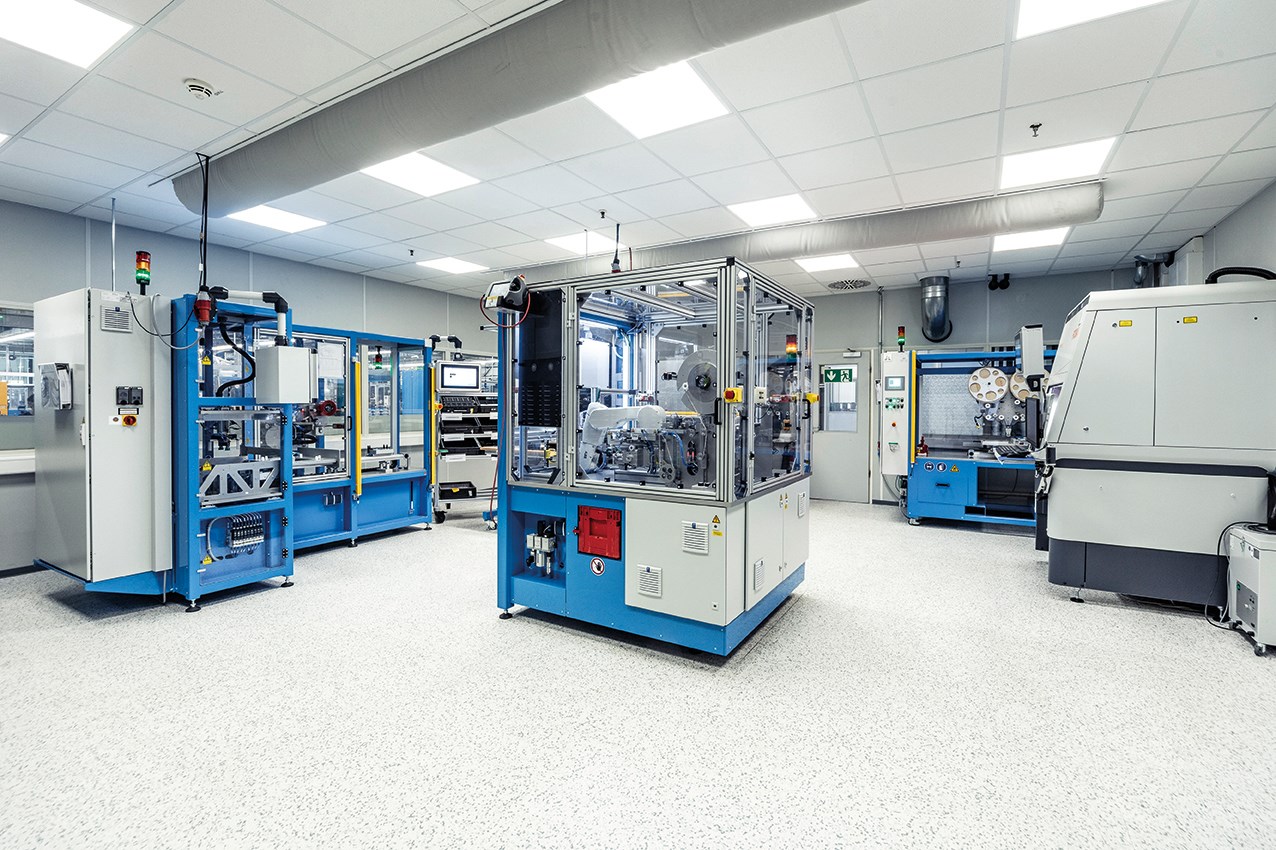
However, when designing the corresponding production line, it turned out that established integration concepts would not provide the flexibility or quality control needed. Achieving these goals turned out to be possible using concepts from Industry 4.0 such as the digital twin and M2M (machine-to-machine) protocols such as OPC UA1 →1. These concepts were successfully implemented by ABB-internal machine designers partnering with the system integrator, neogramm GmbH.
Made to order: ABB-tacteo KNX – the perfectly individualized product
The ABB-tacteo KNX sensor is a capacitive control element for intelligent building automation in high-end luxury hotels, offices and public and residential buildings →2.
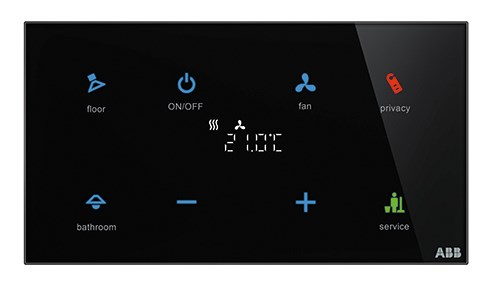
Constructed from glass, ABB-tacteo KNX meets all the requirements of modern design, the highest levels of quality and, above all, convenience for residents. From blinds, lighting and heating to media playback and room access, with ABB-tacteo KNX everything is easy to control.
The number of functions provided by the control element is variable and is determined by the customer’s specific needs and wishes. Individually configured according to the customer's desire with an easy-to-use online configurator, each sensor is unique in design and function.
This means that the consumer is given direct control over the design of the end product, while the strengths of the traditional value network →3 – in which wholesalers take care of distribution and expert installers integrate building automation products according to the consumers’ needs – are maintained.
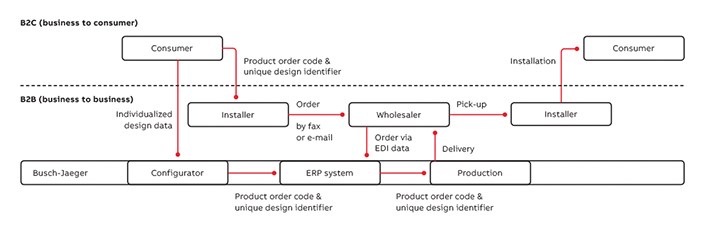
A control element consists of high-quality glass, bearing the designed icons over an opaque background coating, behind which the KNX electronics reside. The manufacturing steps are as follows →4: After placing the panels on a tray, a near-infrared (NIR) laser removes the coating according to the shape of the designed icons.
04a Glass panels in tray. 04b Laser processing. 04c Trays in drying rack. 04d Manual electronics assembly. 04e Mounting the electronics onto the panel. 04f Glass with electronics mounted.
Then, the transparent areas are coated again by a digital printer to give them the level of translucency needed for each icon. Once the ink has dried, the electronics are attached and the finished product undergoes testing before it is shipped to the wholesaler. All physical, electro-mechanical and software features of the product are individualized according to customer design.
Quality – perfection in every step
Nummerous innovations are possibe in the context of Industry 4.0, such as autonomous machines that negotiate the production schedule with each other, or smart products that steer themselves through the production process. The first challenge, then, is to decide which concepts are useful for a particular production environment.
Considering the design freedom the consumer has, every control element is potentially a unique product. Quality becomes both a top priority and a top challenge because a quality issue requires the complete element to be manufactured again and thus might delay the entire customer order.
Today, lack of digitalization is a main contributory factor to quality issues: Material is procured and transported manually, guided by order data on paper slips. Mix-ups happen easily but are hard to detect. While design data are available in digital form, they are manually transmitted to the machines on removable media. Quality-relevant data such as calibration settings for machines are not captured and cannot be audited should quality inspection of the finished product reveal any flaws.
In individualized production, it is imperative to detect flaws in the product as early as possible; preferably, they should be avoided altogether. Individualized production must not only be highly adaptive but also resilient, and human operators and machines need to collaborate seamlessly to close the quality loop.
Complete digitalization using digital twins
Individualized production has two key enablers: adaptive material transformation within, and digital interoperability between such machines. While material technologies like NIR lasers or digital printers already exist, machines still need to be taught how to work together naturally to achieve the needed efficiency and quality.
Today, machines are hardwired or coupled through PLC software. While this arrangement achieves a tight integration, it comes at significant effort and does not yield much flexibility for new product variants except that which is designed in from the start. For truly adaptive production, machine integration must be achieved with a much looser coupling, so the entire line can be flexibly reconfigured with minimal effort.
This is achieved by providing digital twins [2] that represent the specific skills of each machine in a common format on the network, independently of any wired or programmed connection. To avoid “media breaks,” product design along with order and quality data are represented in the same manner. The idea is that by orchestrating the machine digital twins based on the ordered product design, any reconfiguration in software seamlessly translates to production steps in the physical world and quality information is mirrored back into the software domain.
Using the digital twin concept, the ABB-tacteo KNX control element now passes each production station as follows: Upon arrival, the glass is scanned and its identity is used to get the approval, the design data and the process parameters for the next production step. To this end, the machine contacts an orchestration service provided by ABB Ability™ Operations Data Management zenon →5, which automatically replicates the product recipe from the ERP and holds the production history of the particular glass.
Once the glass has been processed, this is reported back to the orchestration service along with machine data used for quality tracking. The glass now departs for the next station as indicated by operations management and as shown on the HMI (human-machine interface) to direct the worker. For normal operating steps, station operators interact with the machine using a standardized ABB B&R2 Automation Panel 900 →5. Manual steps, such as material transport, are electronically guided and supervised.
05 ABB Products and solutions used for the ABB-tacteo Industry 4.0 production line. 05 ABB Products and solutions used for the ABB-tacteo Industry 4.0 production line. 05 ABB Products and solutions used for the ABB-tacteo Industry 4.0 production line.
For example, if a glass is inserted into the printer before it has been lasered, it is rejected and the human operator is instructed to take it to the laser station instead. If glasses are transported from laser to printer out of order, the printer still is guaranteed to receive the correct raster data matching the lasered icons on the glass. Before leaving the printer, the current calibration data are captured for the particular glass. The same holds when calibrating the icon brightness on the product itself during automated testing. In this manner, a quality issue with the product can be traced to the potential root causes such as problems with the machines or suboptimal process parameters. Above all, quality issues are raised right when they occur, any flawed product is automatically removed and production of the corresponding design is restarted.
To support the way machines, services and human operators work together as described, machines and their digital twins are derived from a common design template →6. Machines following this template are also easier to add or replace because they naturally plug into the existing production system.
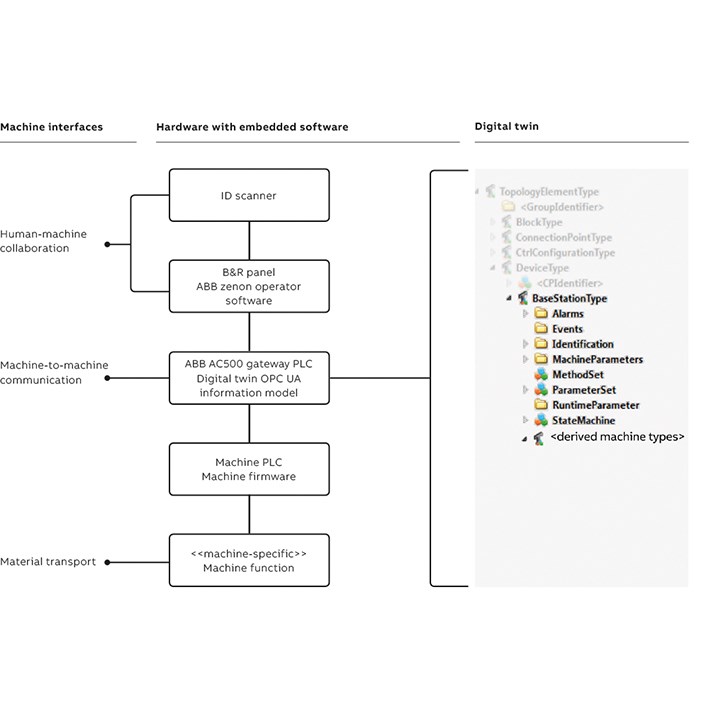
In this production concept, the ABB-tacteo KNX control element qualifies as a smart product: The identity of each glass actively drives its own production and the outlined process steps allow the quality loop to be closed based on the global product memory.
Designing the digital twins
The production process described depends on a mix of very different data: some relate to the product design, some to the manufactured product, some to a specific machine and some describe information common to all products or machines. For example, for each product design, there are machine-independent characteristics such as the layout of the control icons; there are generic machine properties such as the current operating state; and there are properties like the printer calibration data, which are machine-specific but do not depend on the product. Product design is translated into machine-specific artifacts like rasterized icons and there are test results for each manufactured product.
To create these digital twins, the best practice was to first create a top-down OPC UA information model from the perspective of the overall production steps, as shown in the center of →7. Only in a next step was the model split and parts allocated to the individual machines and software services. To upgrade existing machines with this model, the best method was to wrap them using an ABB AC500 PLC →5 as an embedded OPC UA gateway. To this end, close collaboration between information designers, the integrator and the various machine builders was required to ensure the real machines could simply be plugged together in the factory to form the desired production system.
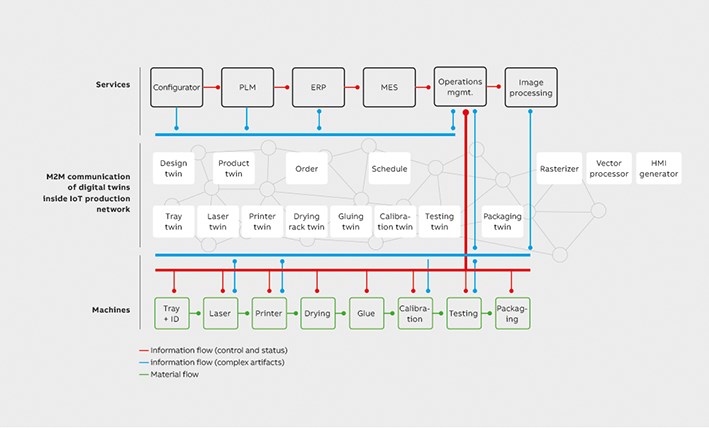
Industry 4.0 for all
Designing the ABB-tacteo production line provided first-hand insight into the needs of machine- builders and production designers on the road to Industry 4.0. Particularly for individualized production, perfect quality control and automated reconfiguration are the key challenges to be addressed by an automation solution. These challenges can be met based on Industry 4.0 concepts such as digital twins, smart products and M2M technologies like OPC UA.
While today, individualized production requires significant up-front investment, future solutions must be covered by established annual investment budgets to be broadly competitive.
To this end, specialist machines need to be taught how to work together out of the box. This requires automation vendors to supply processes, tools and standards that make it easy for production designers, machine builders and integrators to build their digital twins independently and then run virtual integration testing before physical machines are actually built and commissioned in the factory. Currently, premium products such as the ABB-tacteo KNX control element are welcome catalysts to drive this type of innovation. The vision, however, is to offer Industry 4.0 not as a premium product but as an off-the-shelf solution that can be applied to any type of production, from large factories to small and medium-sized enterprises.
Footnotes
1) The OPC Unified Architecture (UA) is a communication protocol for industrial automation developed by the OPC Foundation. What sets it apart from other M2M communication protocols is the versatility of communication patterns (from polling to event-based, from point-to-point sessions to publish/subscribe) and the extent to which the structure and semantics of data can be described.
2) B&R denotes Bernecker + Rainer Industry- Elektronik GmbH, the largest independent provider focused on product- and software- based, open-architecture solutions for machine and factory automation worldwide. ABB acquired B&R in July 2017. The strategic significance of the acquisition is that it made ABB the only industrial automation provider offering customers in process and discrete industries the entire spectrum of technology and software solutions around measurement, control, actuation, robotics, digitalization and electrification.
Reference
[1] “ABB-tacteo KNX sensor.” Available: https://new.abb.com/ buildings/tacteo
[2] “Digital twin – the software component of Industry 4.0”, in this edition of ABB Review, pp 27-33.