There is much value in combining the streams of data that flow from subsystems in a typical industrial process. ABB’s university collaborations address the challenges involved in exploiting this data and equip researchers with the knowledge needed to continue to deliver digital innovations.
Anna Stief, James Ottewill ABB Corporate Research, Krakow, Poland: anna.stief@pl.abb.com, james.ottewill@pl.abb.com; Nina Thornhill ABB Chair of Process Automation, Imperial College London, UK
Modern large-scale processes have become increasingly complicated over the decades and now often consist of many, complex process, mechanical and electrical subsystems. Automation schemes treat these subsystems as an integrated whole, so the need arises to close information loops between them. However, because such subsystems now generate a vast amount of data, the efficient and sustainable operation of assets over their, typically, 30- to 50-year lifetime requires sophisticated and holistic concepts to manage information and resources. ABB has been working closely with top universities over the last years to address the challenges involved in creating such concepts.
ABB and Imperial College London
ABB’s university collaborations address the digitalization challenges of the process industries at a fundamental level. For example, ABB and Imperial College London work together on a program of projects to manage industrial process information and resources so data insights can be converted into direct action in the physical world →1. The approach adopted by the program is characterized by its focus on improving efficiency in the huge installed base of process plants – chiefly by optimizing the operation of process equipment using techniques that include the prediction, detection, diagnosis and elimination of the root causes of process inefficiencies. The work has been undertaken by Imperial College researchers, ABB research engineers on secondment to the university and Ph.D. students sharing their time between Imperial College and industrial placements with ABB and other collaborating companies.
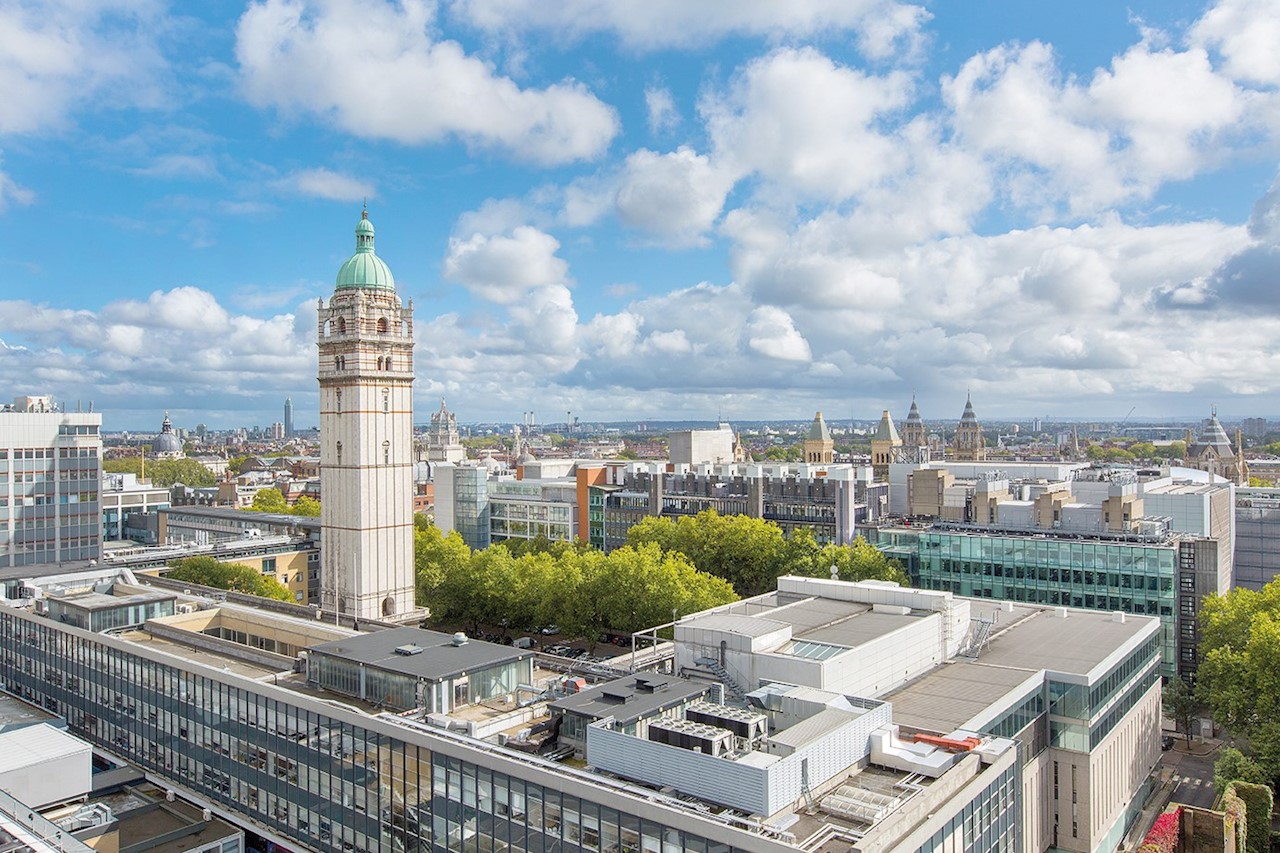
The fact that ABB has sponsored the Chair of Process Automation in the Department of Chemical Engineering at the university – where much of this work takes place – since 2007 shows how close the collaboration is.
ABB in European projects
The Energy-SmartOps ITN (Innovative Training Network)1 ran from February 2011 to January 2015 and focused on integrated control and operation of processes, rotating machinery and electrical equipment →2.
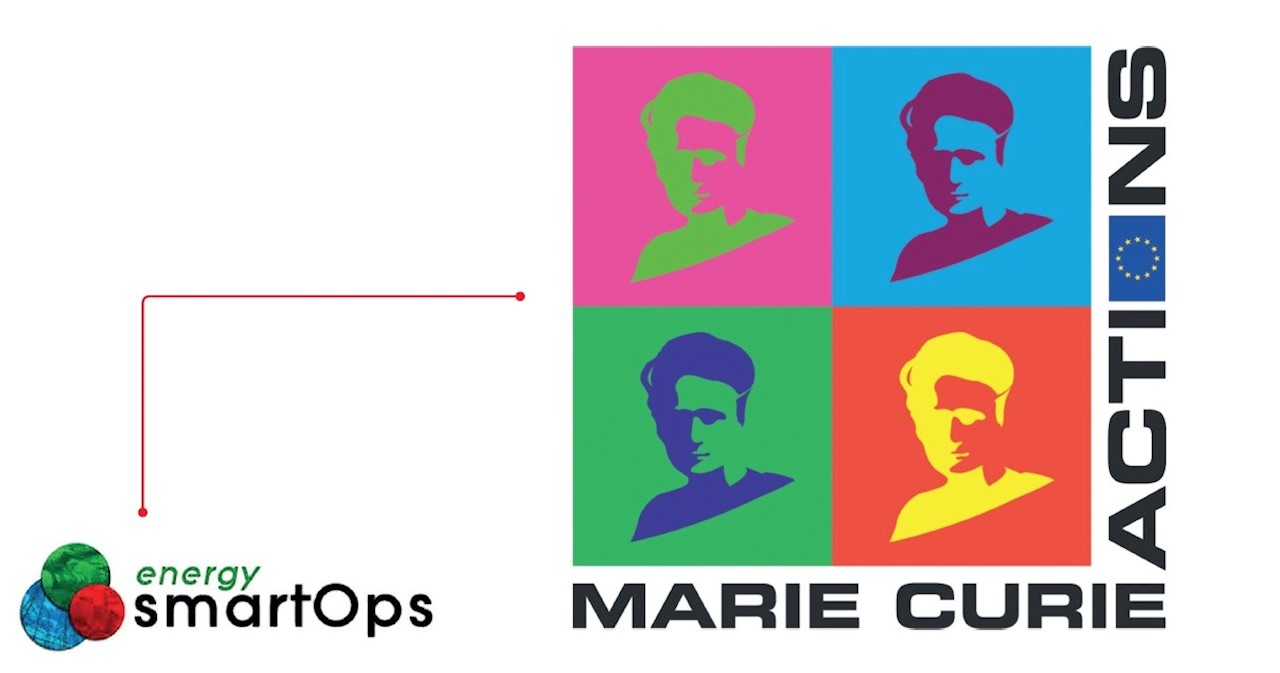
The project was coordinated from Imperial College and involved ABB, end-user companies such as BASF and Equinor, and several universities (Imperial College, Cranfield, ETH Zurich, Politechnika Krakowska, and Carnegie Mellon). Energy-SmartOps generated and tested monitoring systems that integrate multiple measurements from the process, mechanical and electrical subsystems. Energy-SmartOps closed the loop with performance monitoring and control by capturing information from all three subsystems and devising new algorithms that explicitly manage the interfaces and interactions between them. An ITN is a doctoral training program and Energy-SmartOps has launched a cohort of well-qualified researchers with PhDs – as well as industrial training – into the areas mentioned above.
The REAL-SMART IAPP (Industry Academic Pathways and Partnerships)2 scheme started in September 2010 and ran for four years. Its contribution to digital innovation was in measurement-based monitoring and management of electrical grids and the industrial loads they supply.
It also was coordinated from Imperial College and involved transmission system operators (Fingrid, National Grid and Statnett), companies that supply technologies (ABB and GE) and universities (Aalto University, Imperial College London, Graz University of Technology). The interdisciplinary consortium had experts in electrical power systems, modeling, instrumentation, signal analysis, condition monitoring and the automation of oil, gas and chemical processes.
The IAPP scheme financed exchanges of researchers between industry and academia. REAL-SMART gave early-stage researchers from university partners a first taste of industrial research and development during their Ph.D.s and provided refreshers for experienced researchers with secondments in both directions between the industrial and academic partners.
The European Union supported these joint activities through the Marie Skłodowska-Curie schemes.
ABB demonstrators
Of particular note is the ABB control room at Imperial College →3.
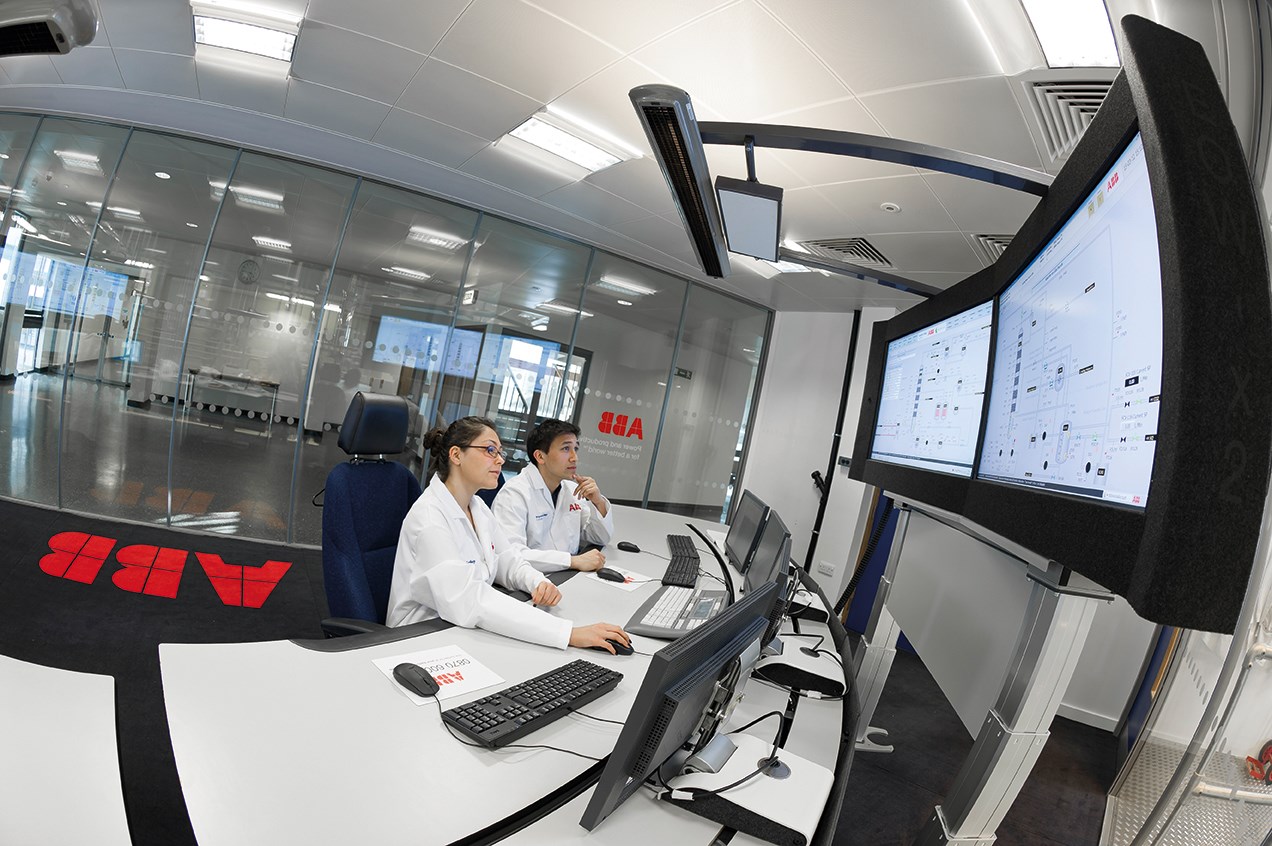
This comprehensive facility is housed in the Carbon Capture Pilot Plant in the Department of Chemical Engineering →4. An agreement between ABB and Imperial gives the university access to advanced control and instrumentation technology, as well as services and support for the installation. In return, ABB has access to the pilot plant for customer demonstrations and training, and trials of new technology – all in the center of London. A second demonstrator unit is in the making. Last year, ABB signed a memorandum of understanding to explore opportunities for the creation of a unique digital power network demonstrator unit incorporating ABB Ability™, ABB’s unified, cross-industry digital capability.
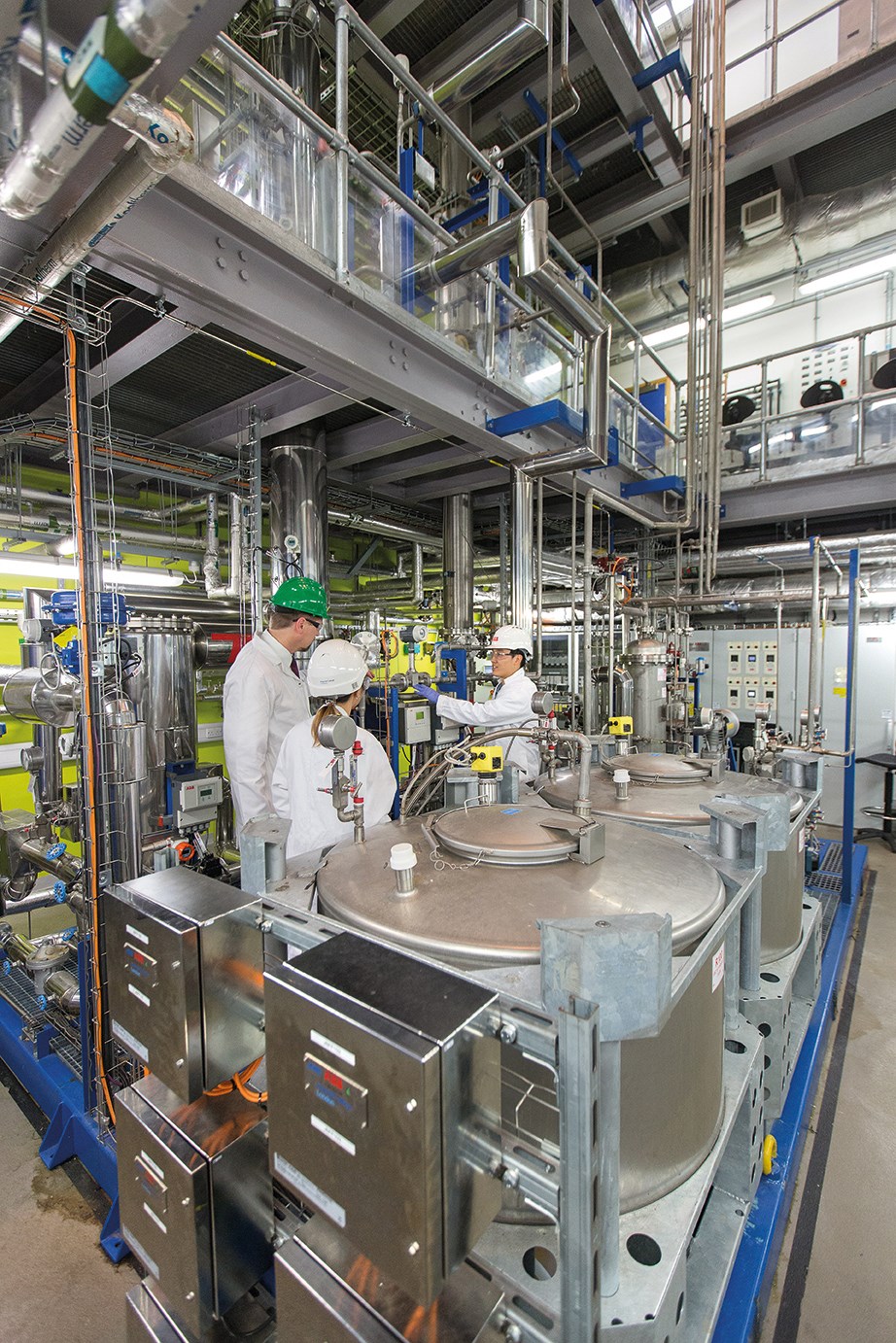
Next-level process network optimization – PRONTO
ABB participates in the PRONTO (PROcess NeTwork Optimization) project3. PRONTO is a European Industrial Doctorate program funded by the Marie Skłodowska-Curie Actions scheme under EU Horizon 2020→5. The consortium partners include leading universities such as Imperial College London, TU Dortmund, the Norwegian University of Science and Technology, AGH University of Science and Technology, Cranfield University, the University of Valladolid and Carnegie Mellon University, as well as companies with good reputations for innovation such as BASF, Petronor, Equinor, Acciai Speciali Terni and INEOS.
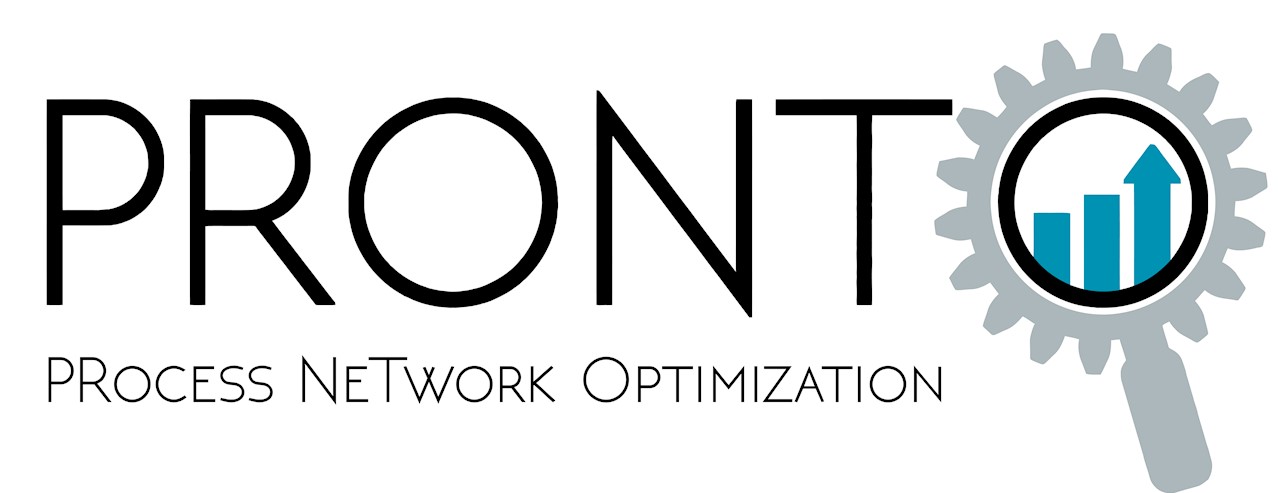
PRONTO focuses on process network optimization for the efficient and sustainable operation of Europe’s process industries, taking machinery condition and process performance into account. The research topics in the project are:
• Data analytics for assessment of the condition and performance of networks of process industry production equipment.
• Optimization of resource use in process networks, taking account of real-time information about the condition and performance of the process equipment.
• New concepts for process operation identified as having high potential for impact by industrial partners.
The consortium offers early-stage researchers training under the European Industrial Doctorate scheme by involving the non-academic sector extensively in joint supervision of the doctoral training. There is a strong emphasis on industrially relevant Ph.D. projects that lead to practical demonstrations. Collaboration manifests itself in a wide range of forms: from knowledge transfer and shared case studies to joint publications and face-to-face brainstorming sessions during project meetings.
The PRONTO project continuously delivers innovations in process optimization and analytics technology. One such development aims to combine quantitative and qualitative data from diverse sources for process monitoring to enable more reliable and robust condition assessment→6. The motivation for this research is that industrial processes and machinery generate a variety of data from disparate sources, each of which may potentially be a valuable source for process monitoring. Different sources of information may be used to monitor the state of health of systems with each source or sensor typically being better suited to diagnosing different faults. Monitoring approaches that fuse data from multiple sources have the potential to diagnose a greater number of faults with greater accuracy and reliability.
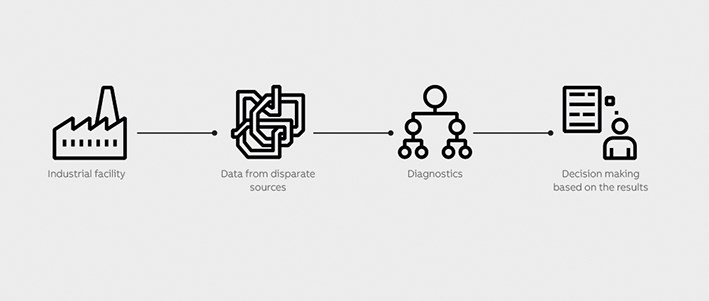
Another development recognizes that new condition monitoring techniques are needed to tackle the new challenges of big and heterogeneous data. One such solution brings together probabilistic approaches, such as Bayesian inference and multivariate statistical analyses, such as principal component analysis, into an innovative analytics structure to provide a transparent, flexible, modular and scalable condition monitoring framework. As well as fusing data from multiple data sources to achieve accurate fault diagnosis, the method allows the end user to trace the decision-making process back to the root cause and identify which signal types contributed to the decision [1]. This solution is just one of many currently being developed in the project.
Digitalization and collaboration
Digitalization will dictate the specifications of the next generation of products, systems and services. It also has the potential to revolutionize and reinvigorate already-existing and well-established applications. Next-level digital solutions will allow the performance of existing plants to be monitored more accurately, more reliably and holistically, allowing assets and resources to be managed in a more informed manner.
However, there are some challenges: Growing volumes of data from process subsystems demand better ways of combining information from disparate sources. Further, as more systems produce more data, the traditional boundaries between different process, mechanical and electrical subsystems are less meaningful, necessitating a multidisciplinary domain understanding of the interactions between different elements.
To address many of these challenges, ABB continues to engage in various collaborative projects with leading universities and innovative companies. The knowledge and experience shared during such collaborations allow industry-relevant challenges to be solved with cutting-edge digital technologies. Furthermore, and perhaps of even greater value, such academic-industrial collaborations are providing the next generation of talented researchers with the training and experience needed to continue to deliver such digital innovations in the longer-term future.
Footnote
1) This project has received funding from the European Union’s FP7-ITN research and innovation program under the Marie Curie grant agreement contract number PITN-GA-2010-264940.
2) This work was supported by the Marie Curie FP7-IAPP project, “Using real-time measurements for monitoring and management of power transmission dynamics for Smart Grid REAL-SMART,” contract number PIAP-GA-2009-251304.
3) This project has received funding from the European Union’s Horizon 2020 research and innovation program under the Marie Skłodowska-Curie grant agreement number 675215.
Reference
[1] A. Stief et al., “Two stage data fusion of acoustic, electric and vibration signals for diagnosing faults in induction motors,” Elektronika ir Elektrotechnika, vol. 23, no. 6, pp. 19–24, 2017.