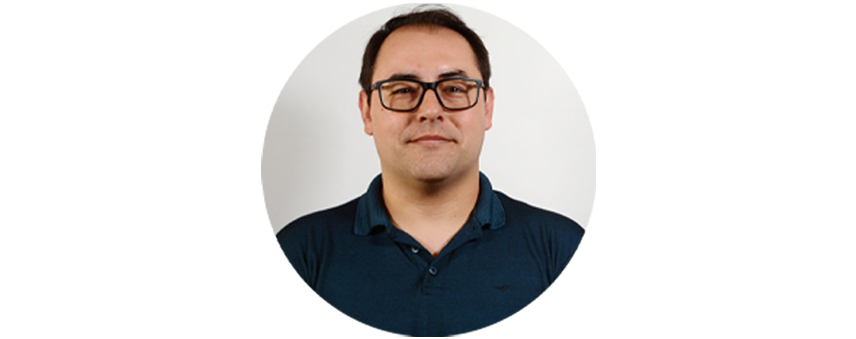
About me and why advanced process control?
My journey into advanced process control (APC) has been a natural progression. Over the past 14 years, I’ve worked in project engineering, focusing on industrial automation and commissioning in the mining and cement sectors across the Americas region. My work has taken me to places like Brazil, Bolivia, and North America.
During my time in industrial automation, I gained exposure to solutions that build upon the base-level automation system, optimizing underlying processes. This involved various APC technologies, and I had the opportunity to contribute to several projects where my work supported the implementation and interfacing of APC systems. Through these experiences, I confirmed the efficiency and indispensable nature of these tools for process optimization and control, in addition to what human operators were able to achieve.
These solutions not only enhance operational efficiency but also contribute significantly to achieving KPI results.
Given my involvement in such projects, I seized the opportunity to join the ABB team. As a Digital Applications Engineer, I’m excited to deepen my knowledge and contribute to the ongoing development and implementation of these essential technologies in the automation realm.
What are the challenges and highlights of working with APC in the industry?
As the advancement of new tools, updates and improvements in the industry are constant, our challenge is to always keep up to date and be able to meet all the needs and challenges of the projects in which we are involved and to know when certain technologies are appropriate to solve certain customer challenges.
While the rewards of working with advanced process control are substantial, the journey is not without its challenges. The dynamic nature of industrial processes, coupled with the complexities of APC system integration, requires resilience, adaptability, and troubleshooting skills.
From overcoming data acquisition limitations to developing robust models and addressing real-time optimization constraints, each project presents unique hurdles that need innovative solutions and involvement of multiple teams.
Aligning the goals and expectations of process engineers, operators, and management play a crucial role in overcoming resistance to change and ensuring organizational buy-in to APC initiatives.
Additionally, effective communication and collaboration with teams are indispensable to ensure the successful implementation of the project.
Together with my team I am sure that we can further develop new techniques and ways to perform our work effectively and that can generate positive results in the implementation of new projects.
A recent project I have been involved in
Recently, I have been working on several projects for plants in Europe. One example is of a cement plant looking to improve quality of cement by reducing variability in the raw feed. This involves setting up and testing strategies developed by ABB for quality control in cement production. This system receives analysis values performed in the laboratory and with instruments through a lab information management system, otherwise known as LIMS. With these values, the logic analyzes the quantity and acts on the dosage of the materials in the process to ensure uniform production quality defined by operations while minimizing any overdosing scenarios of expensive additives. This module is referred to as RMP or Raw Material Proportioning and uses Advanced Process Control within the Expert Optimizer system to deal with the multivariable and dynamic complexities of additive dosing.

What are the challenges of this project?
For these types of projects, some of the sample types of materials use an automated sampling system. In this case, the control is done without difficulty by the APC after it has been sampled. However, the challenge of these projects occurs when the sampling system is still done manually and with a long-time delay between samples being tested and the values made available. In this case, it requires additional manual work and time to check the tests before corrective actions. There are several possible software technologies that could be applied to this type of a challenge, such as inferential estimation using AI and machine learning.
Potential future work and expansion
Due to the effectiveness and flexibility of advanced process control, it is common to implement optimization programs in stages, covering various production units in the plant, based on readiness and ROI. Maintaining a relationship with the operations team is essential for ongoing success, where in the above case, an expansion to downstream units such as pyro and milling sections of the plant would be a natural progression.