The half-day event, staged at IMO headquarters in London, offered flag states and NGOs insights from leading developers of autonomous ship technology, with the voices of shoreside innovators also heard from Port of Antwerp-Bruges, Japan’s Ministry of Land, Infrastructure, Transport and Tourism, and Seafar NV.
In a stand-out presentation, Dr. Alina Colling, Product Manager at ABB Marine & Ports set out to bridge the gap between technologists and regulators by laying out an inclusive pathway for progress to satisfy regulatory, ship operating, sea-going and technical stakeholders. With a PhD from Delft University of Technology in the Netherlands, specializing in semi-autonomous navigation systems, and currently working as Product Manager for the ABB Ability™ Marine Pilot product family of autonomous ship technologies, few are better positioned to offer an overview of latest developments in the sector.
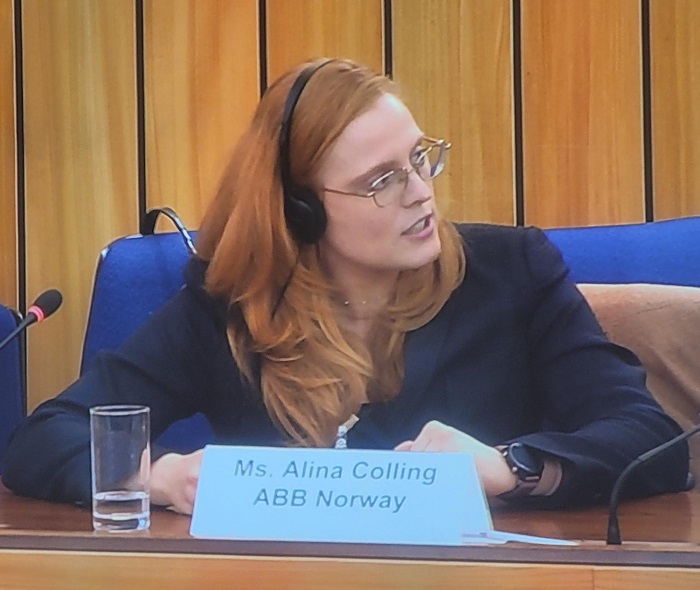
Colling said her purpose was to focus minds on redefining the ship as a “system of systems”, in order to fit together the puzzle of Maritime Autonomous Surface Ships (MASS) regulation. While regulatory work is at its formative stage, the approach aligns with the need to bring technologies to market on a step-by-step basis, she said.
She pointed out that ship operations go far beyond navigational functions, with a “system of systems” approach necessary to take account of operations where sub-systems work together but feature different tolerances and redundancies.
“Autonomous technology has come a long way, but the road ahead to reach large-scale commercial applications is also quite long,” said Colling. Just because a 10-meter boat can operate on an autonomous basis with I/Os* in the magnitude of tens, it does not follow that the approach is ready for a modern cruise ship with more than 20,000 I/Os.
The increasing complexity of interlinked systems requires a focus by system developers on user experience and the way humans interact with the technology, as well as more support from shore, in order to ensure safe and effective operations.
“Systems integration means the user is likely to have less immediate understanding of what each system is doing ‘inside the black box’,” Colling observed. “However, the user must still understand the system to ensure safety and compliance, and that troubleshooting can be done effectively.”
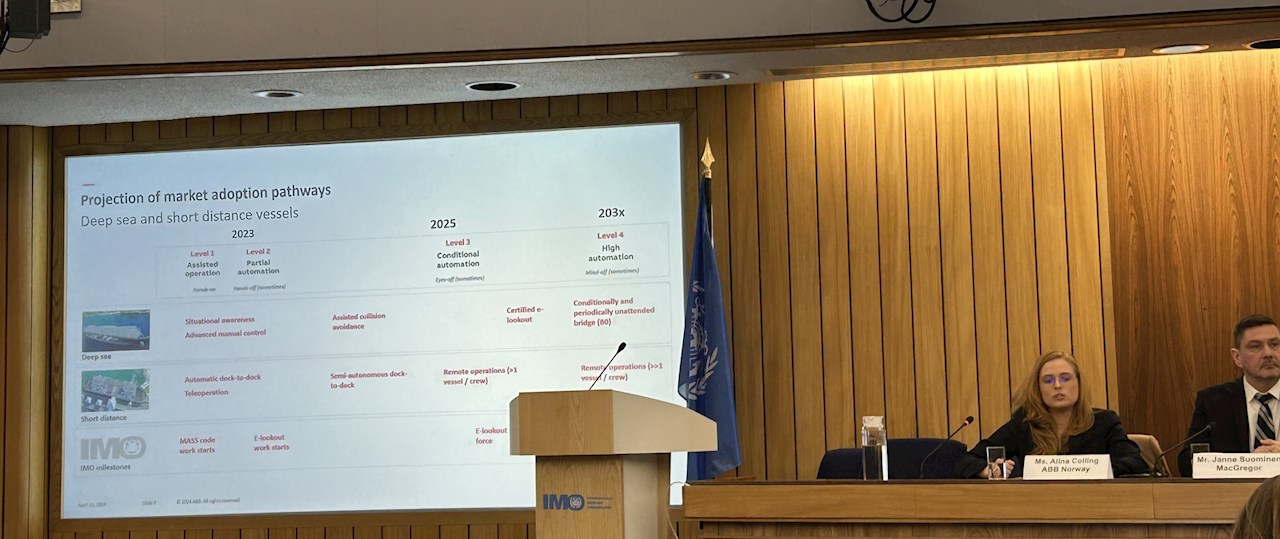
ABB’s approach towards autonomous ship technologies focuses on practical solutions which benefits operations, rather than on any conceptual voyage towards uncrewed ships, said Colling. ABB Ability™ Marine Remote Diagnostics Systems, advisory software, collision avoidance and the Marine Pilot solutions that are “building blocks for autonomy” all have a role in enhancing efficiency and safety.
ABB’s technologies are already finding smarter ways to help crew control ships. ABB Ability™ Marine Braking Assistance, for example, automates pod-way emergency stop procedures, enabling a full stop at the push of a button, helping reduce the stress of the situation. Marine Pilot Control unifies thrusters for maneuvering, piloting and dynamic positioning in one joystick. Meanwhile, ABB is working with Wallenius Marine on OVERSEA – a service integrating shore side fleet monitoring with operations on board.
As part of her presentation, Colling offered a projection for the adoption of autonomous ship technologies. She said there was potential for short sea operators to bring in conditional automation techniques where operations continue ‘eyes-off’ some of the time from 2025. On the 1-5 scale of autonomous operations that has become part of regulatory common speech, this is Level 3 automation where shore-based personnel can remotely control vessels.

On a different pathway, deep-sea operators use autonomous ship technology for situational awareness and advanced manual control today. The next step would involve uptake of assisted collision avoidance, with certified (automated) E-lookout solutions expected to filter into the market some time before 2030, Colling predicted. Regulators have separated work on E-lookout requirements out from MASS Code development, with expectations that deliberations this year may lead to a regulation on the E-lookout within a reasonable timeframe.
Where technologies exist to support conditionally and periodically unattended bridge operations onboard a deep-sea ship, Colling looked to an IMO horizon for such Level 4 autonomous ship operations on a commercial scale beyond 2030 and to restricted applicability dependent on the vessel types.
In deepening understanding of available technologies, ABB advocates for moving the debate forward so that MASS systems are understood in the context of goal-based standards based on operational concepts, said Colling. She stressed how developing rules in a stepwise manner goes hand in hand with preparing the market for autonomous technologies.
Only by working together to understand what is already possible and agreeing common definitions to integrate MASS into a ship as a “system of systems”, can the maritime industry hope to realize the full potential of autonomous ship technology.
*I/O stands for input/output and describes any program, device or operation that transfers data to or from a computing system.
Images credit: Hugh O’Mahony / JLA Media