MPS Egg Farms (MPS) is a family-owned shell egg business operating seven farms in the United States. As one of the top ten egg producers in the USA, MPS Egg Farms aims to be the premier supplier of shell eggs by meeting the highest standards of customer service, quality, food safety, and animal husbandry. With 14 million laying hens, MPS produces 9 million eggs and delivers an average of 24 truckloads of eggs every day to customers which include grocers, food distributors, and food service companies across the country. Food safety standards and sustainable processes have a very high priority at MPS, with the objective of ensuring the best balance of quality, cost, environmental impact and secure supply.
Kipster concept from Holland being used
MPS has been inspired by the Kipster concept for sustainable production of eggs which originated in the Netherlands and focuses on achieving better animal welfare, reducing food waste and cutting carbon emissions to achieve carbon-neutral egg production. Therefore, MPS decided to partner with Kipster to build four of their innovative hen houses in North Manchester, Indiana, USA. The aim was to take further tangible steps towards reaching full carbon neutrality and circularity at its farm, while also making sure the chickens have a good life producing eggs.
To help achieve these aims, MPS worked with the Dutch system integrator Hotraco which has its headquarters in Horst, Netherlands and is a leader in implementing the Kipster concept. Hotraco specializes in designing, building and delivering motor-drive control solutions that manage and run ventilation, manure drying, feeding and egg conveyor operations on egg and broiler farms. For the MPS expansion at North Manchester, Hotraco installed advanced motor-drive control systems to run the 56 ventilator fans that move air and the 40 conveyor belts that are used to transport the eggs, chicken feed and manure waste.
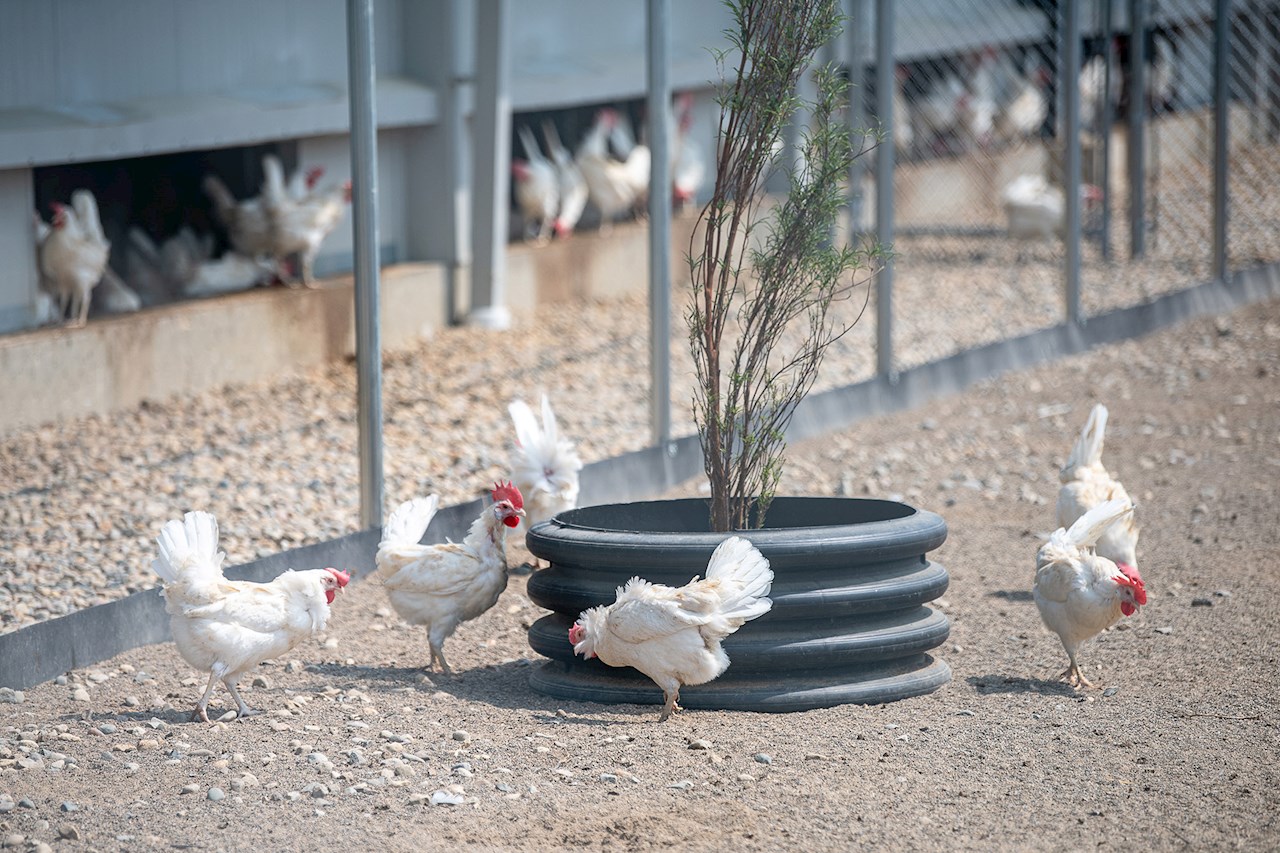
84 ABB drives control the key processes
To achieve the precise and safe motor control needed to run these operations at the optimal speeds, Hotraco installed 84 units of ABB’s general purpose ACS580 variable frequency drives. The ACS580 drives give very accurate and energy efficient control of the speed and torque of the motors that run the fans and conveyors in the egg farm facilities of MPS.
Luca Coniglio, the Global Marketing Manager at Hotraco Agri, explains some of the company and project background. “For 50 years Hotraco has helped customers worldwide to better control their livestock farming, horticulture and storage processes by using our innovative automation systems. For the MPS project with Kipster concept implementation, the ABB control systems were a key requirement that was specified by the end customer. This fact led to an efficient and fruitful collaboration between Hotraco and ABB which allowed us to create an optimal control solution for MPS for ventilation, egg collection and material conveying.”
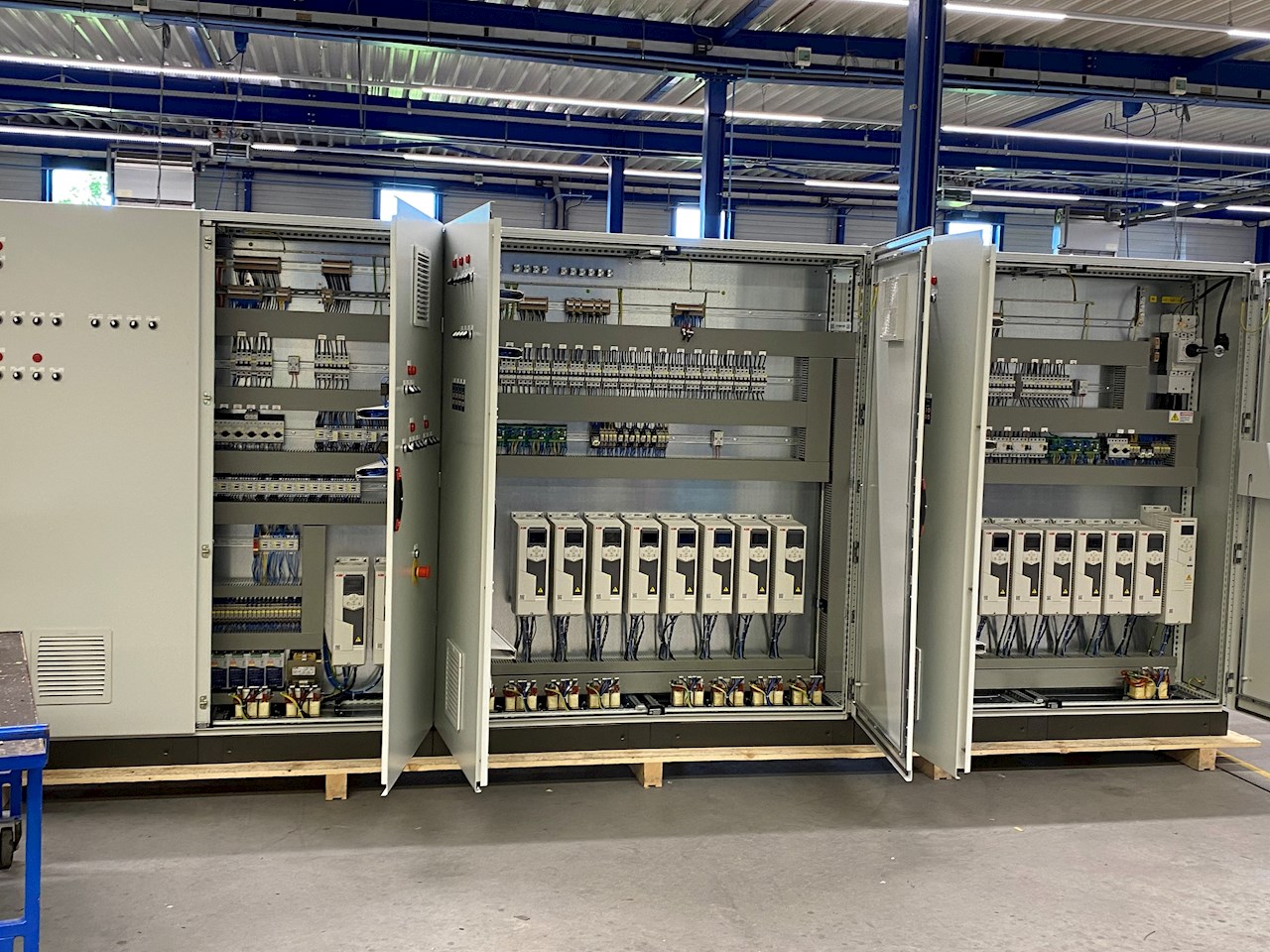
Sustainability and animal welfare have always been a priority
MPS’s Director of Sustainability Rachel Sanborn says that for MPS Egg Farms, sustainability and animal welfare have always been of the utmost importance. And today they see interest in this topic rapidly growing as consumers seek to learn more about where their food comes from and how it is produced.
“MPS Egg Farms is committed to a sustainable future, which is why we continue to take progressive measures such as implementing the Kipster concept to further reduce our environmental footprint. By partnering with Kipster, we have become one of the first organizations in the world to produce a carbon neutral egg while maintaining superior animal welfare standards.”
Furthermore, explains Rachel Sanborn, “The egg industry understands that over 60% of the greenhouse gas emissions from egg production are attributed to the feed that chickens consume over their lifetimes. To reduce these emissions, the Kipster process uses upcycled feed which is formulated by nutritionists and consists of food waste like broken pasta or out of spec flour from bakers and other food producers.”
Small steps add up to big progress towards circularity
Upcycled feed can reduce greenhouse gas emissions by up to 50% compared to conventional feed. In addition, the use of upcycled feed also means less land is needed to grow feed crops for the birds, allowing the land to be used for other purposes. Furthermore, the barns themselves are solar powered, and like most egg farms, MPS dries the mixture of manure, spilled feed and feathers and turns it into fertilizer used by nearby farmers to grow their crops. Thus, by deploying these numerous sustainability steps, MPS goes a long way towards achieving full circularity in egg farming.
Another important point is the security of fresh air supply and exhaust air handling, which can be critical both for animal welfare and for the safety of personnel. The high reliability of ABB drives is therefore appreciated for keeping the facilities well ventilated and ensuring fresh, clean air circulation. For additional animal safety, the ABB drives offer automatic adaptation to a power mains failure. This means that if the power fails, the single phase feature in the ABB drive still keeps fans and pumps in motion, reducing the risk of mortality.
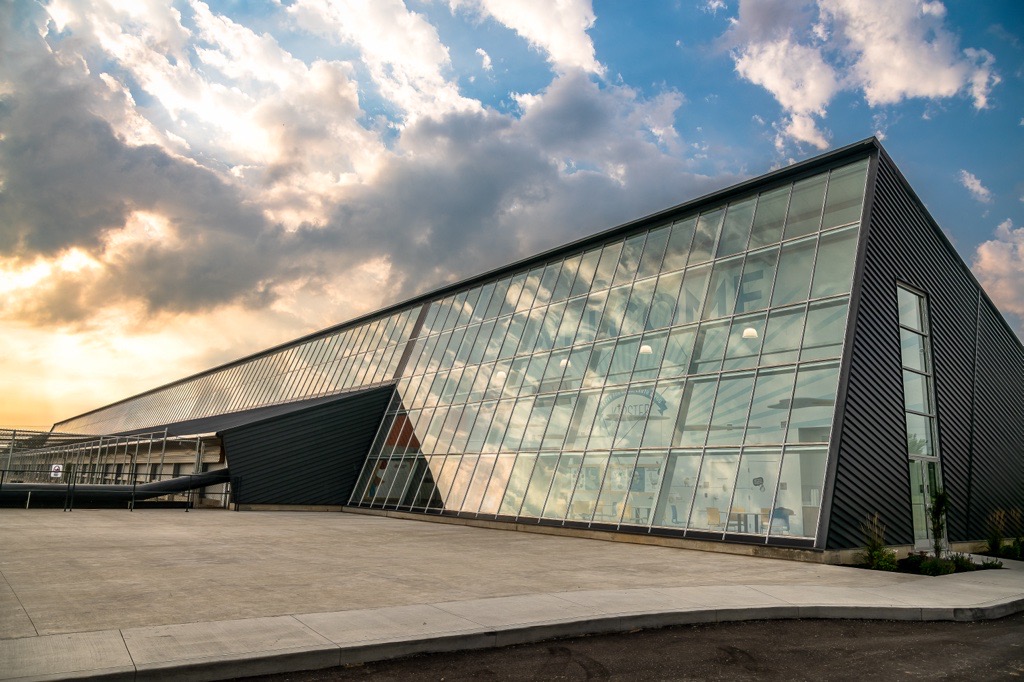
ABB drives ensure energy savings and increase operational reliability
Alex Bradford, who is Lead Electrician at MPS, says he can see that big savings have resulted since the ABB drives were installed. “Our first Kipster-type chicken house, which uses Hotraco controls and ABB ACS580 variable frequency drives, has just reached its one year milestone,” he says. “By using the energy efficiency calculators that are built into the ABB drives, we can see that over the last year we have saved nearly 400,000kW. This equates to roughly US$9,000 in annual savings. Although these numbers may be overstated, even if our actual savings are only half of those figures, it still adds up to several thousand kW and several thousand dollars saved per year.”
“Another, and potentially higher, cost saving benefit we believe we get from the variable frequency drives is lower wear and tear on the equipment and reduced maintenance labor costs,” continues Alex Bradford. “The drive’s slow start function is gentle on the motors and the associated equipment they are driving, allowing them to progressively ramp up to full running speeds. This procedure is almost always better for the longevity of any equipment.”
An associated advantage of the soft start/stop function in the ACS580 drive concerns the fragile eggs on the conveyor lines. The gentle control avoids sudden and rushed movements that could damage the shells of the eggs, which would then have to be thrown away, causing production and monetary losses.
Lei Gommers, who is the Global Business Development Manager for ABB Drives, explains a bit more about the capabilities they offer. “ABB drives that control machinery used in poultry farms are easy to program and set-up to manage many critical factors in poultry farming, including ensuring that fans used for ventilation always run properly. Any risk of them not doing so can result in health problems or even mortality among the chickens inside the farmhouses. As an example, ABB drives have auto derate functionalities built-in which slightly reduce the fan speed to keep it running during critical situations. This conserves energy, in a safe way. The drive also handles harsh and corrosive environments like farmhouses thanks to the coating of the sensitive components. This helps ensure both reliable operation and equipment longevity which reduces costs. ABB drives can also mitigate harmonics which can be a nuisance, especially in poultry farms that may be connected to a weak power network.”
Invaluable support from ABB’s channel partner
Regarding support and high process reliability, Alex Braford says that the ABB local channel partner is an invaluable asset when using ABB drives. “They assist us with product selection, project design, programming, and technical support, and also organize additional educational opportunities to help us get the most out of the drive features and how we use them.”
Throughout this project, it is clear that ABB and its channel partner have played a key behind-the-scenes role in supporting the MPS initiatives. The result is that by taking the progressive decision to adopt the Kipster concept, and clearly specifying ABB drives as a requirement for the operations, the goal of achieving full circularity in egg farming has now come a big step closer for MPS Egg Farms.