The ABB Belo Horizonte factory's progress in reducing energy consumption and CO2 emissions qualified it as an ABB Mission to Zero™ site, a scalable program to create more sustainable, energy-efficient operations.
The 8,000m2 facility produces 42,000 miniature circuit breakers each day to protect homes across the Americas. The challenge: making operations more sustainable without impacting production quality and delivery. Operations Manager Roni Silva shares how the Belo plant achieved this milestone while engaging the full team in their sustainability journey.
What was the catalyst for your sustainability efforts at the Belo plant?
About a year ago, I was excited to hear about ABB’s ambition to reach net zero by 2050 across all our sites. This business commitment and the rising market demand for sustainably produced products inspired us to take action. We needed help so I reached out to a colleague at our ABB Nogales Mission to Zero factory in Mexico, which had already started this journey. I learned how this plant reduced its emissions and applied technologies to improve efficiency from a new heating system to integrating the ABB AbilityTM Energy Management System.
I knew there had to be many energy-savings opportunities for our Belo plant, and we had the support and encouragement of our plant manager. Now that we’ve started our journey, it has been amazing and kind of addictive. Each energy savings has incentivized our team to seek more ways to be sustainable. This has also extended into my private life — I run my car on ethanol now, made from sugar cane, a sustainable gasoline alternative.
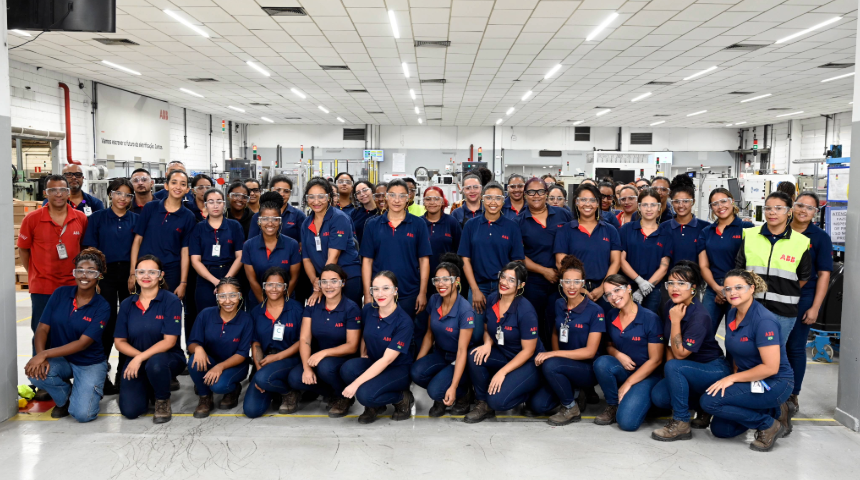
How did you kick off site efforts?
Without employee support, the goal of net zero would be unattainable. Our initial challenge was getting everyone onboard. It meant changing our traditional ways of operating. We ran training sessions and made weekly audits to show the impact of simple actions like turning off idle machines. We focused on continuous training and sharing information to build a strong culture of environmental care. This helped maintain high levels of engagement and ensured everyone understood their role in achieving our sustainability goals.
How has the plant applied today’s technologies to improve energy efficiency?
It has been a mix of investments in upgrading equipment and applying digital solutions. For example, we achieved major savings by adding frequency inverters in two main production areas. We also upgraded heating, ventilation and air conditioning (HVAC) equipment and installed LED lamps and skylights.
For me, a game changer was connecting everything to ABB AbilityTM Energy Management System (EMS) for metering, control and optimization of energy consumption. We now monitor all our electrical consumers across our facility. We compare energy consumption versus our production to ensure equipment is not running unnecessarily. The EMS also provides insights that help us identify new energy improvement opportunities.
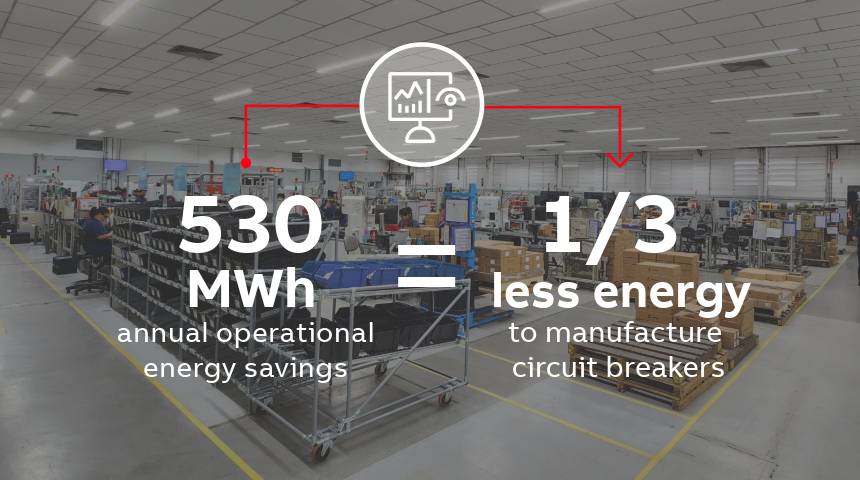
What results has the plant achieved in the past year?
Our plant has achieved annual operational energy savings of 530 MWh. To put this in perspective, we now manufacture each circuit breaker with 1/3 less energy than it took previously.
We also achieved a 128-ton reduction in CO2e emissions within the first year. We are only the second site in our local area with solar panels. It took a lot of coordination and problem solving, but we got the solar panels up and running and in full compliance with regulations. These panels contribute about 220 MWh of onsite generated renewable energy annually.
What’s next for the Belo plant?
Our journey is far from over. Our next ambition is to produce two circuit breakers with the same amount of energy previously required for one. We also have ongoing projects to upgrade systems, lighting and install more solar panels.
The biggest thing is that we have our employees’ enthusiasm to continue our Mission to Zero journey. Together, we have eliminated all energy waste tied to production – we no longer have any idling equipment. This is a huge reflection of our teamwork. Our employees also regularly volunteer ideas to improve our sustainability efforts.