Pioneer Foods Group is a leading South African food and beverage producer which exports its products all over the world. Its Shakaskraal bakery near Durban is its largest, and mainly serves a Portugal-sized province of KwaZulu-Natal.
Its cutting edge technology ensures the highest product quality, while also supporting sustainable operations. Reflective white roof sheets reduce the need for electrical lighting and internal cooling, while harvesting rain water for truck washing and irrigation. It relies on renewable resource-fired boilers and heat recovery on refrigeration equipment for the pre-heating of water.
Ultimately, its performance depends on the productivity of its workforce. So Pioneer Foods turned to ABB in 2016 to help ensure that its robots show up for work on time.
ABB supplied the company’s first robots in 2008 to the Olifantsfontein bakery in South Africa, and more robots were ordered on a steady basis during the following years. With the latest four ABB robots being commissioned last year, there were 27 robots doing everything from pan handling, bread de-panning, lidding, de-lidding and lidstorage.
This existing relationship served as the foundation for an expanded relationship with ABB. “They make sure we stay informed on current technology, new updates and upgrades and help us with critical spare parts onsite. We have high expectations on ABB’s service professionalism and ABB always delivers,” says Ivan Padayachee, Engineering Manager at Pioneer Foods’ Shakaskraal bakery.
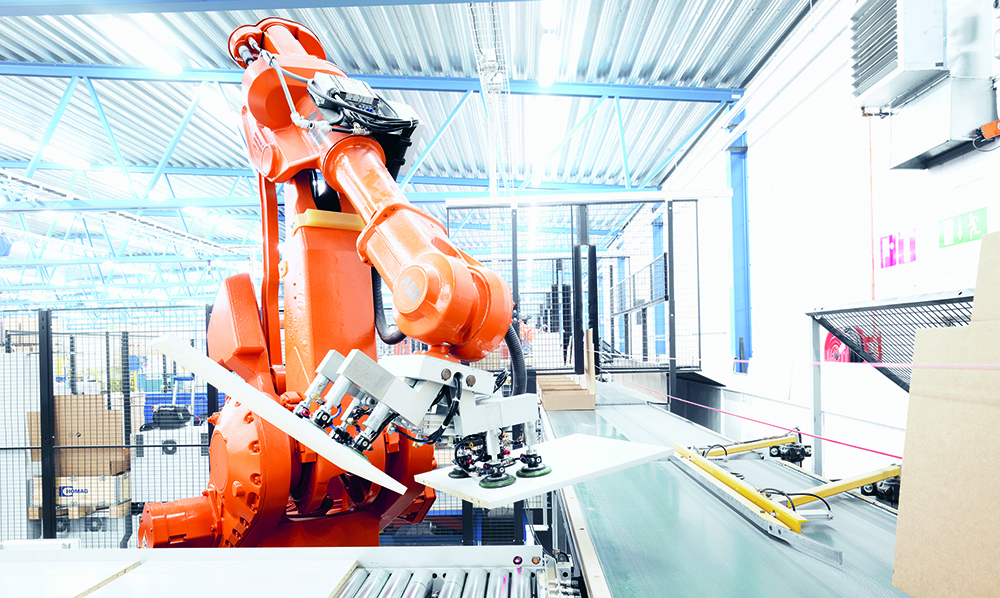
Condition Monitoring & Diagnostics
Keeping Pioneer Foods’ robot systems running at optimal performance relies on ensuring faster reaction time, higher efficiency, and better and quicker service and support.
Doing so means utilizing the connectivity capability built into every ABB robot, which allows for linking them via wireless or hardwire and leveraging actionable data. We implemented our Condition Monitoring & Diagnostics digital solution, which not only closes the loop between robots and operators, but operates securely and 24/7.
“ABB works closely with the Shakaskraal team to make sure preventive maintenance is done on the right robots and at the right times,” explained Padayachee.
The results can all be measured in time savings: More efficient service prep, faster incident notificationand reaction, and an iterative improvement anticipating the most frequent failures.
This success is also a demonstration of the benefits of ABB’s digital solutions.
Digital Solution Opportunities
Condition Monitoring & Diagnostics is one of five services that our Connected Services can tailor to meet a client’s unique needs; the others are Backup Management, Remote Access, Fleet Assessment, and Asset Optimization.
We also enable this connectivity not only via our robots. Our smart sensor solution can connect any low-voltage motor with the cloud, gather and analyze multiple parameters and call for action whenever needed.
With integrating each service come further improvements in facility productivity, delivering fewer incidents and reducing time, while increasing efficiency and extending equipment lifetime. The digitalization of vital processes also yields a learning relationship that makes system management more effective while informing it with new issues and opportunities that need to be addressed.
“Pioneer Foods believe in being proactive, not reactive,” says Trevin Chetty, Service Engineer, ABB Robotics, South Africa.
So does ABB.